Owing to the fact that, in contrast to electricity generation, companies generate the indispensable „energy of compressed air“ themselves, they are also responsible for its long-term and reliable availability. Inevitably, due to the digitalisation of the production processes, a fundamental change was made in the field of maintenance tasks. With iConn, Gardner Denver has developed a cloud-based platform which allows the user to look at the compressor and its performance data virtually, from a computer or an iPad. iConn forms part of the standard equipment in new CompAir compressors, but it can also be integrated into existing compressor systems, and even equipment by other manufacturers, as a retrofit solution.
Marius Breusers, Aftermarket Product Manager at Gardner Denver: „Today, we look at the compressed air supply in producing companies using a holistic approach, regardless of their size. At a very early stage of our activities in countries with a low density of industrial infrastructure, we learned the crucial importance of the predictive maintenance approach. This led to us developing iConn – a digital platform for IoT and Industry 4.0 solutions, for proactive monitoring of information from compressed air systems in real time – very early on.“
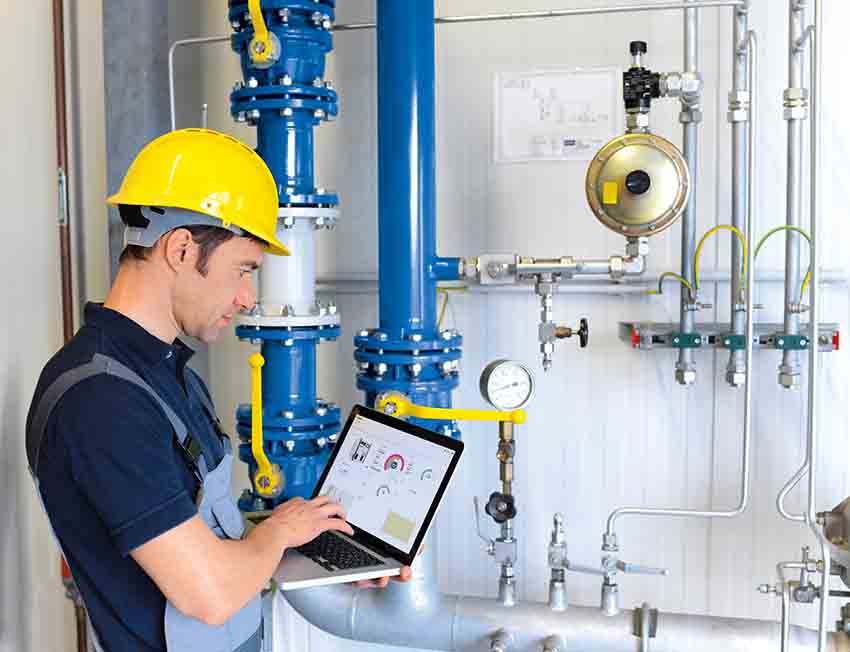
Preventive maintenance
Those dealing with the maintenance of compressors should be aware that the maintenance costs – calculated over the product life cycle – are similar to the acquisition costs. For these reasons, in the past, many compressed air users switched their service strategy from “parts replacement when needed” to “preventive maintenance” and now replace wearing parts before they fail. Undoubtedly, this means they increase the availability of the compressed air station, but are always left facing a dilemma: too little maintenance can lead to costly failures, production standstills and higher energy costs. Alternatively servicing too early drives up costs unnecessarily, among other things due to the need to stock supplies of expensive parts.
The question is therefore: how do you find the right level of service – according to the principle of “as much as necessary, as little as possible”?
Smart maintenance: configuring iConn according to your needs
iConn is the entry-level solution that provides a detailed and regular overview of the operating hours. Irregularities and maintenance instructions are automatically reported to the user in real time. With iConn Universal, it can be retrofitted to monitor any unit from other manufacturers. You can choose whether the messages are sent in the form of an email to the computer in the maintenance centre or to the smartphone of the current person in charge. In either case, the fault message is sent immediately as the situation arises. In this way, it is possible to take preemptive steps before events, such as a drop in pressure, have negative consequences for production. If the authorised persons access the stored data via the web-based iConn page, they can effectively track the life cycle of each compressor.
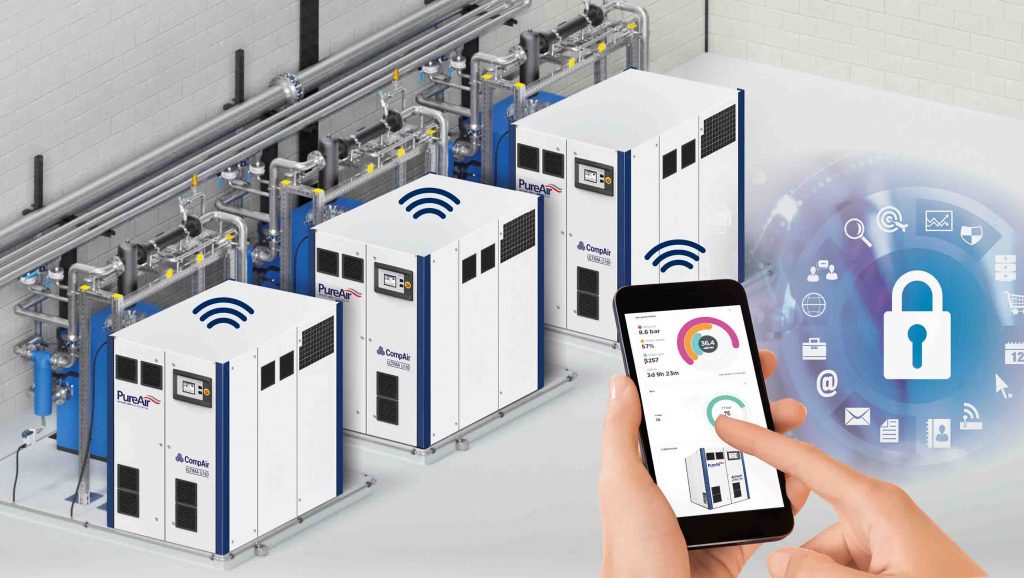
Smart maintenance with the monitoring of compressors is possible without any investment costs using the basic version of iConn. Even when the additional functions are activated, it is not a luxury, but rather an economically sensible investment, which can be used to ensure smooth production processes.
With these additional features added, the system becomes iConn HD and enables predictive maintenance planning with an “early warning system“ for machine faults. This enables the user to conduct forward-looking, demand-oriented maintenance (predictive maintenance), which is perfectly aligned with the motto of “maintenance if and only if the probability of failure is rising“. Web-based remote monitoring with dashboard control is also available. This digitised service includes both predictive maintenance planning as well as maintenance and periodic energy analysis in order to relieve the burden on compressed air users entirely; energy savings and thus a sustainable use of the compressed air as a means of production are also included.