SIBA System Integration stands for customized system solutions in the field of intralogistics. Their services cover the entire system engineering process – from planning, manufacturing, installation and commissioning to after-sales service. As an independent system partner, SIBA develops efficient, environmentally friendly and durable solutions for automated storage and transport systems.
The company employs more than 50 qualified staff members at our site and export around 80 % of their systems. Technological leadership, high level expertise, and precise manufacturing are always the centre of SIBA’s operations.
Interview with Ing. Alfred Altmann, CEO of SIBA System Integration GmbH.
What are the main areas of activity of the company?
Alfred Altmann: Our core competence lies in the implementation of customized, automated storage systems – with focus on stacker cranes for pallets, containers and special loading equipment. We are specialists in the implementation of automated mini-load systems (AKL) tailored to customer-specific requirements. Our portfolio is complemented by load handling devices, vertical lifts, and intelligent picking solutions.
The focus is on efficient space utilization, reduced energy consumption and increased in-house productivity for our customers. Our expertise covers everything from unit load logistics to the handling of heavy loads and special load carriers.
What’s the news about new products/services?
A.A: A key area of innovation at SIBA is the combination of proven mechanical engineering with intelligent control systems. Our trolley systems (multi-level transfer cars with shuttle) enable exceptionally high storage performance in a compact space – while drastically reducing energy consumption. In particular, our trolley with multi-deep storage ensures extremely high storage density and minimizes CO₂ emissions.
At the same time, we are continuously developing our load handling devices, such as the “Spicker,” which allows mixed storage of differently packaged products without loading aids. Flexibility and sustainability are at the core of these innovations.
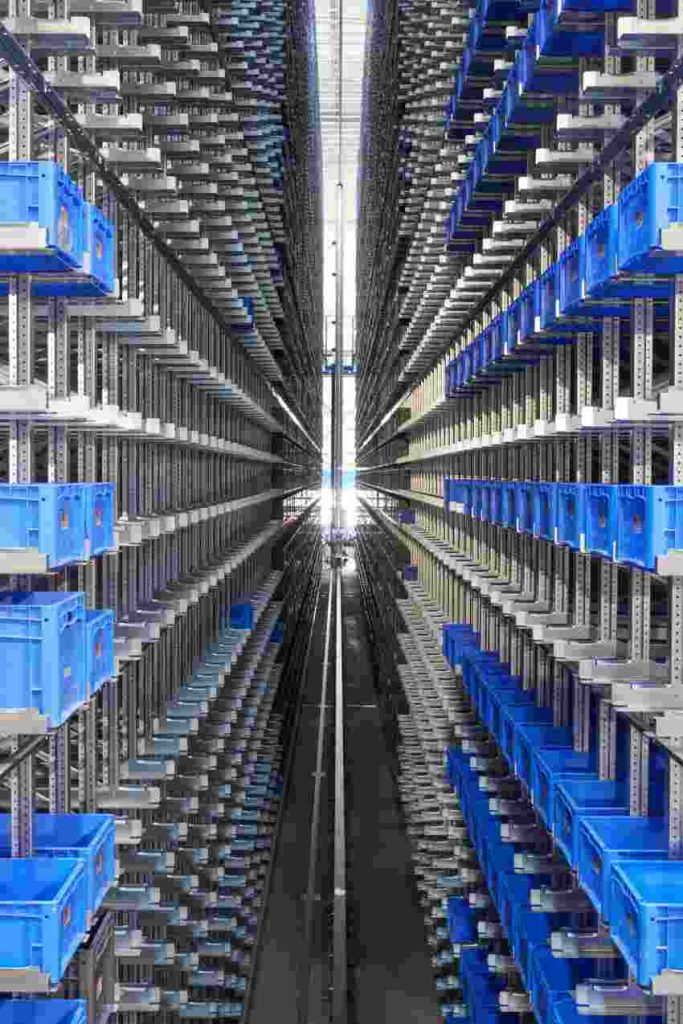
What are the ranges of products/services?
A.A: Our product portfolio is broadly based – and designed for maximum customization. At the center is our core product: the storage and retrieval machine (SRM) – also known as stacker crane. SIBA SRMs impresses with minimal approach dimensions, maximum space utilization and high throughput. At the same time, their low energy consumption makes them particularly resource-efficient and environmentally friendly.
Our SRMs can be used for a wide range of applications – from small parts warehouses to multi-deep pallet warehouses. With a wide range of load handling devices, we implement single-, double-, and multi-deep storage solutions – tailored to the warehouse type, available space, and throughput requirements.
In addition, we offer:
- Trolley solutions for high storage performance with low energy consumption
- Floor-based transport systems such as our SIBA ETB – an electric railbound system
- Shuttle systems: AKF L-Line, Q-Line, and B-Line (battery-powered satellites for multi deep storing in rack channels)
- Complementary conveyor technology
- Production is carried out in-house – using CNC machines, robotic welding systems and a high level of vertical integration.
What is the state of the market where you are currently active?
A.A: The market for automated storage solutions is still in the early stages of development, despite the emergence of many new technologies. Many companies are now realizing the full potential of efficient intralogistics – especially when it comes to sustainable production and supply chains.
Europe is proving to be a highly dynamic market with a growing demand for automation. In North America, we are currently observing a slight hesitation regarding large-scale investments; however, the overall potential remains high. Across all industries, we see clear growth prospects – particularly driven by e-commerce, the pharmaceutical sector and the food industry.
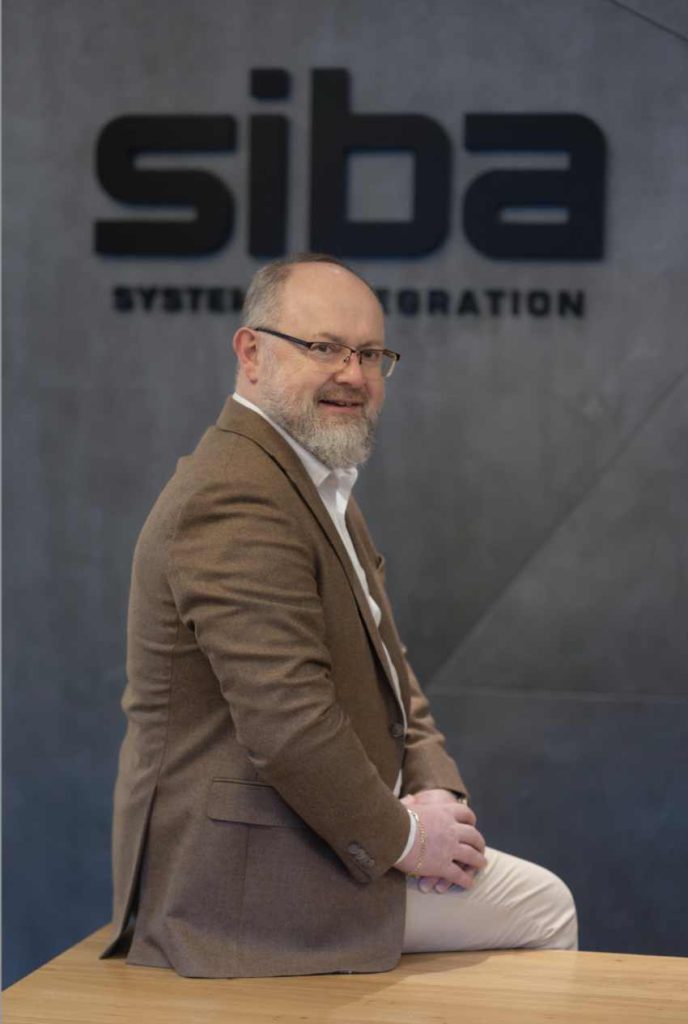
What can you tell us about market trends?
A.A: Current market trends are heavily focused on autonomous systems such as AMRs (Autonomous Mobile Robots), AGVs (Automated Guided Vehicles), and 3D shuttle systems. These solutions offer flexibility in certain applications – but they are not always the most efficient solution. At SIBA, we take a differentiated approach: rather than following short-term trends, we focus on sustainable, needs-based system solutions that combine technology, AI, ergonomics, and cost-effectiveness in an optimal way.
Our experience shows that efficient mini-load systems with high-performance SRMs are superior in many cases – especially when it comes to durability, ease of maintenance, and energy efficiency. An additional advantage: SRMs require neither heating nor lighting – significantly lowering energy consumption and sustainably reducing operating costs.
What are the most innovative products/services marketed?
A.A: A technical highlight remains our AKF, which received the “Best Product” award at LogiMAT in Stuttgart back in 2005. While IT limitations set boundaries at the time, today’s advances in automation and AI now enable such systems to operate reliably and autonomously in 3D environments. High-precision steel construction is a key factor in making this new generation of systems possible.
Our trolley systems are also among the most innovative solutions on the market – capable of delivering high performance with minimal energy consumption.
Another standout is the SIBA ETB – a floor-based, rail-guided transport system that is ideally suited for linking warehouses with production areas. It is especially low-maintenance, reliable, and cost-efficient.
However, our true innovation lies not only in individual products – but in our ability to combine these systems in a modular, application-specific, and customer-oriented way.
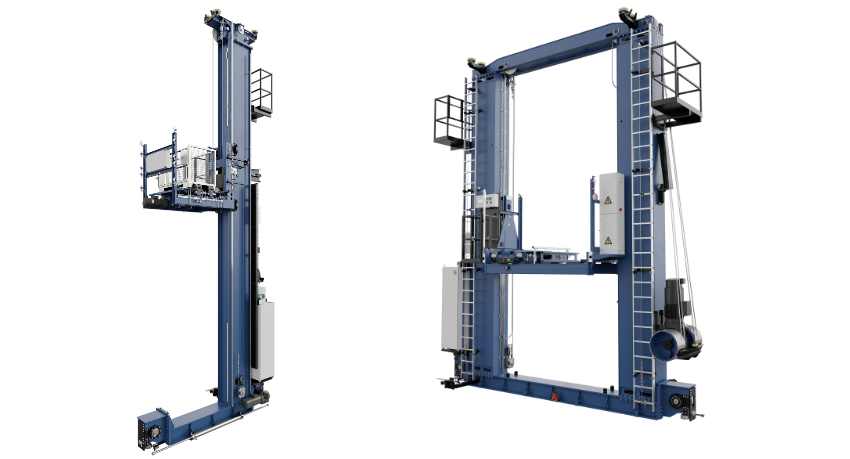
What estimations do you have for the second half of 2025?
A.A: We are very positive about the second half of 2025, as several major projects are now entering the implementation phase. The demand for automation continues to rise. It is particularly encouraging that more and more companies are strategically investing in their intralogistics to address a wide range of challenges:
- Increasing productivity
- Reducing costs
- Supporting employees
- Complying with legal requirements
- All while aligning with their sustainability goals
Our systems enable precisely this balance. Today, more than ever, modern intralogistics is a key driver of resilience – for globally connected production processes as well as for flexible, customer-oriented supply chains.