Conveyor belts that suffer irreparable damage caused by trapped objects and inner carcass damage caused by heavy impact are considered by many to be unavoidable. As a consequence, growing numbers have fallen into the trap of using low price imported ‘sacrificial’ belts. Ironically, low-grade belts have even less ability to resist damage, resulting in an even faster, more expensive cycle of fitting, repairing and replacing. However, one leading conveyor belt manufacturer, Netherlands-based Fenner Dunlop Conveyor Belting, see things differently and are successfully pioneering a radical change of thinking. Whereas single and dual-ply belts were used for only lighter applications in the past, Fenner Dunlop have since turned that convention on its head.
A single and dual-ply future
Since they first introduced their hugely successful single and dual-ply UsFlex belt more than two decades ago, Fenner Dunlop have continued to develop the concept. Known as the X Series, they not only replace thick, multi-layered belts, they also provide numerous advantages. Although thinner and lighter, Fenner Dunlop’s single and dual-ply belts are actually much more robust and resistant to damage than their multiple ply counterparts.In theory, a higher number of inner plies should result in a stronger belt. However, the greatest influence on the strength and other essential physical properties of a conveyor belt is the design and quality of the ply material used to create the carcass. This is where Fenner Dunlop have a huge advantage over would be competitors because they have their own fabric weaving facility in the USA.
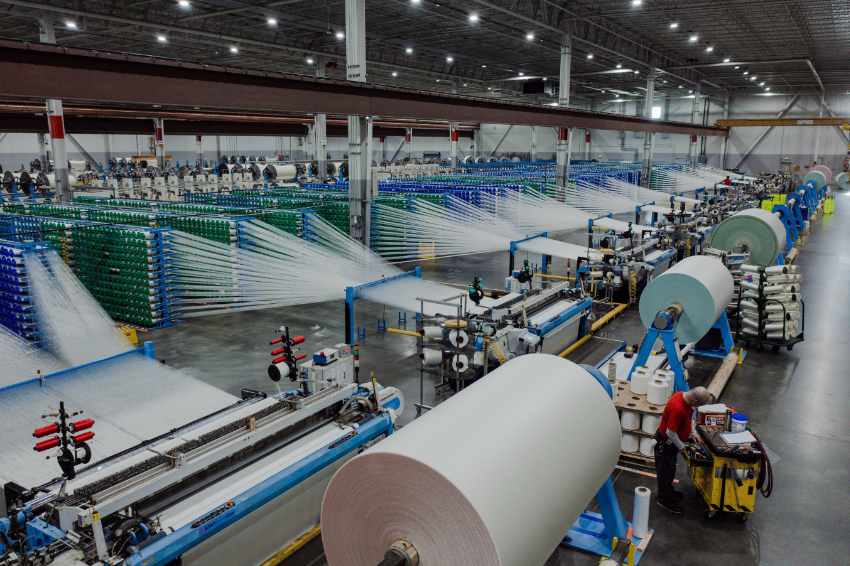
As a result, they have been able to develop a range of unique super-strength fabrics for single-ply belts (Ultra X and Nova X) and their longer established single and dual-ply UsFlex constructions. The carcasses possess a longitudinal rip resistance that is more than 500% greater than multi-ply belts of equivalent rating and up to 300% greater impact resistance compared to conventional belting. So, how does it all work?
The heart of the matter.
The whole working principle of being able to create advantages from using single and dual-ply belts centres on the fabric. Having already developed rubber cover compounds that have long been recognised as being the benchmark for resilience and longevity, their engineers focussed on the design of the fabric. The priority was to ensure that the individual fibres and yarns were of the highest possible quality and strength. Next came the weave pattern, which is where fabric technology becomes difficult to explain.
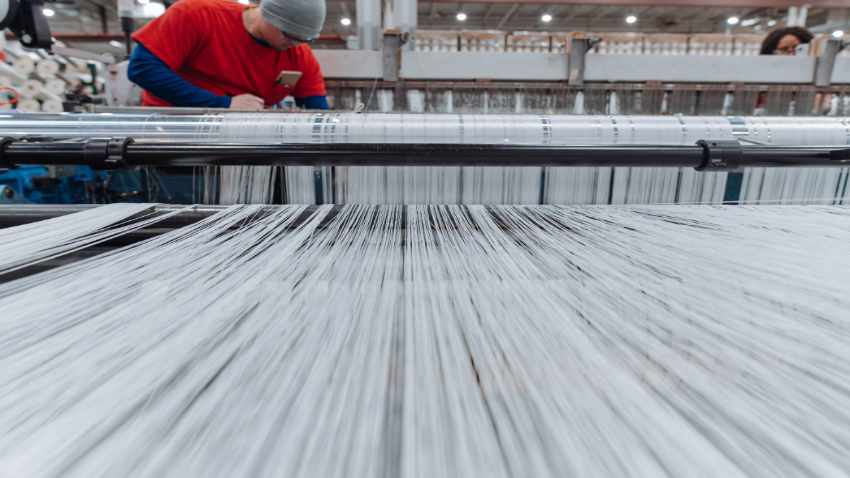
The X Series has (so far at least) three versions of fabric. Ultra X features a specially woven “Crimped warp” carcass, combining crimped polyester warp yarns with strong binder and filler yarns, creating exceptional strength, stability, and impact resistance. The higher tensile strength Nova-X uses an even stronger crimped warp fabric with binder yarns to lock the carcass, providing excellent rip, tear, and impact resistance under load. For the toughest applications of all, there is the even heavier duty UsFlex, which employs a “Straight warp” carcass made of high-tenacity polyester fibres protected by polyamide weft lines.
What all X Series fabrics have in common is that they consist of longitudinal strands lengthwise and heavy strands running crosswise, held in position by a strong yarn. The strands are completely straight in both directions and not interlocked as in conventional fabric, allowing the weft to float free from the warp. This creates a shock absorber effect by dissipating impact energy over a larger area, enabling the belt to withstand the kind of punishment that would destroy a normal multi-ply belt. Arguably even more important is the ability to resist rip and tear damage.
When penetrated and being pulled through a strong, sharp, trapped object, the unique weave design allows the strands to gather in a bundle that can eventually become strong enough to stop the belt or even expel the object causing the damage.
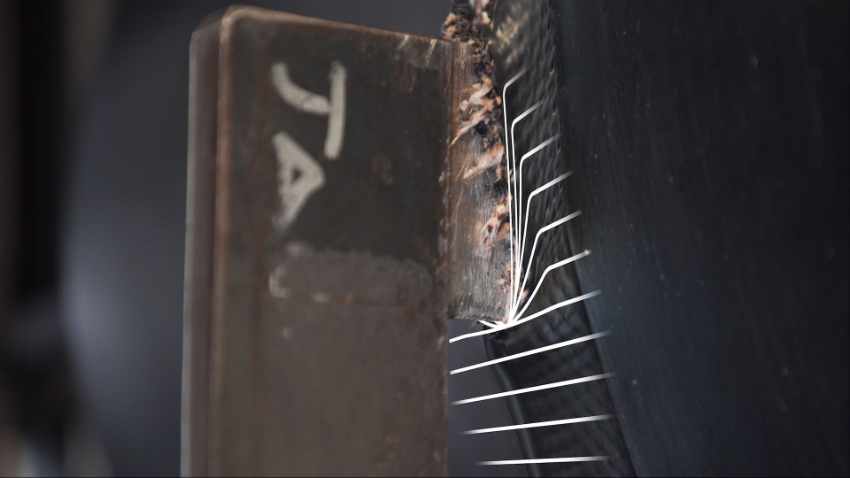
Strange as it may seem, synthetic plies are usually more effective than steel when it comes to minimising the length of a rip. In fact, the UsFlex fabric is so strong that Fenner Dunlop use it as a breaker ply in their steel cord belts. As one operations manager was happy to testify, “We used to replace our belts every three to six months before we started fitting UsFlex belts. Now it can be four or five years before we need to fit a replacement.”
Defying convention. Some find the idea that a single or dual-ply construction belt can possess the necessary tensile strength and also be considerably more resilient and durable difficult to comprehend. The answer lies in a combination of the amazing innate strength of the fabrics together with a higher level of splice efficiency. Although a step splice can be used to join a dual-ply UsFlex, single-ply constructions require a finger-splice joint*. The enormous advantage of finger splice joints is that they retain up to 90% of the belt’s original tensile strength.
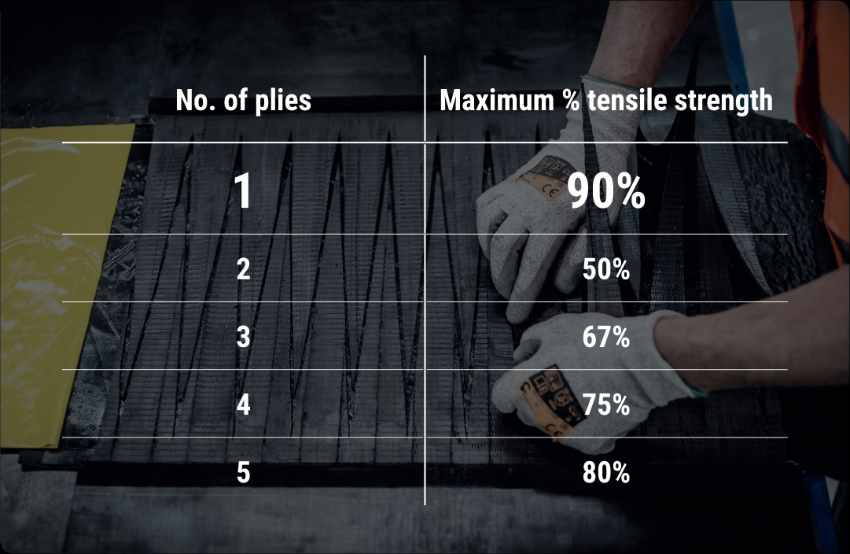
By comparison, a 3-ply step joint only achieves a maximum tensile strength of 67% while a 2-ply step splice only retains a maximum of 50%. Single and dual-ply belts joined by a step splice create equivalent tensile strengths and belt safety factors that are more than comparable to 3 or 4 layer conventional belting. For example, an Ultra X3 single-ply belt can pull up to 56 tonnes. A significant additional benefit of this method is that finger splice joints are stronger and more durable so the need to repair and re-splice joints is much less frequent.
(* Depending on the application, mechanical fasteners can also be used on X Series single-ply belts)
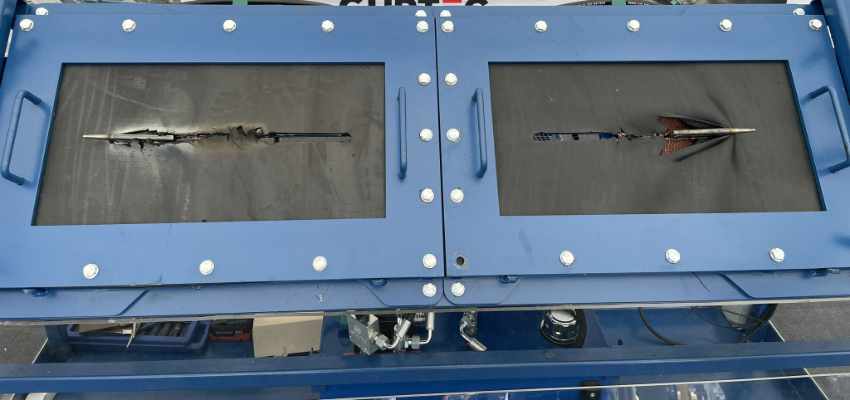
Single and dual-ply – the future has arrived.
Fenner Dunlop freely admit that the Ultra X single-ply construction did raise a few eyebrows at first but as with all ground-breaking innovations, it takes time for a new concept to be fully accepted. Judging by the growing sales, that acceptance seems to be spreading very rapidly. UsFlex is long established while Ultra X has proved a great success since its launch some six years ago. Already a success in North America and soon to be part of the X Series range in Europe, Nova X is a higher tensile version of Ultra X. Although still manufacturing a big range of conventional multi-ply and steel cord belting, Fenner Dunlop’s management certainly regard their X Series single-ply and dual-ply belts as the future of industrial conveying belting. Given the evidence, the future seems to have arrived already!
Autor: Bob Nelson