Mexico is one of the world’s ten biggest producers of Municipal Solid Waste on account of its vast size and large population. The country generates around 120,000 tonnes of waste a day, which add up to 44 million tonnes a year. This situation has been further aggravated by an increase in waste (estimated at between 3.3 and 16.5% according to a study conducted by the Instituto Nacional de Ecología y Cambio Climático de México – the National Institute for Ecology and Climate Change) due to the country’s lockdown period, which has affected patterns in consumption and medical treatment. In this situation, the new sorting plants based on the automation of waste management, take on even greater importance for their potential to improve the environmental situation in Mexico and boost the circular economy.
“STADLER aims to be a driver in the change that Mexico needs to achieve a green economy standard shaped by technological innovations and business models. Both will undoubtedly bring environmental, social and economic benefits,” explains Natalya Duarte, Sales Manager for Mexico at STADLER.
The new sorting plant inaugurated by Operadora de Ferrocarril y Manejo de Rellenos (OFMRS) is testament to this trend towards automation. This private company, which specialises in final disposal for MSW, has joined forces with STADLER to develop a plant in the city of Cuautla (Morelos, Mexico) capable of managing comprehensive waste treatment for 16 municipalities in Morelos and a small part of Mexico City.
“This project was born of the vision shared by OFMRS and STADLER on waste management. This vision has led to a technological proposal and the development of a new operating model,”, says Natalya Duarte. “The aim was to recover different types of recyclable packaging and materials and re-distribute them back into various production chains, as many times as possible. This innovative business and management model makes such projects feasible, as well as making them more profitable due to the highly-efficient sorting process and high purity levels of the materials.”
Crisóforo Arroyo, General Manager for the La Perseverancia landfill, underlines his confidence in STADLER: “Our decision to invest in the project with STADLER was not only based on their reputation as a serious leading German technology firm in the sector, but also on the fact that this comprehensive project was sustainable and took domestic market conditions into account.”
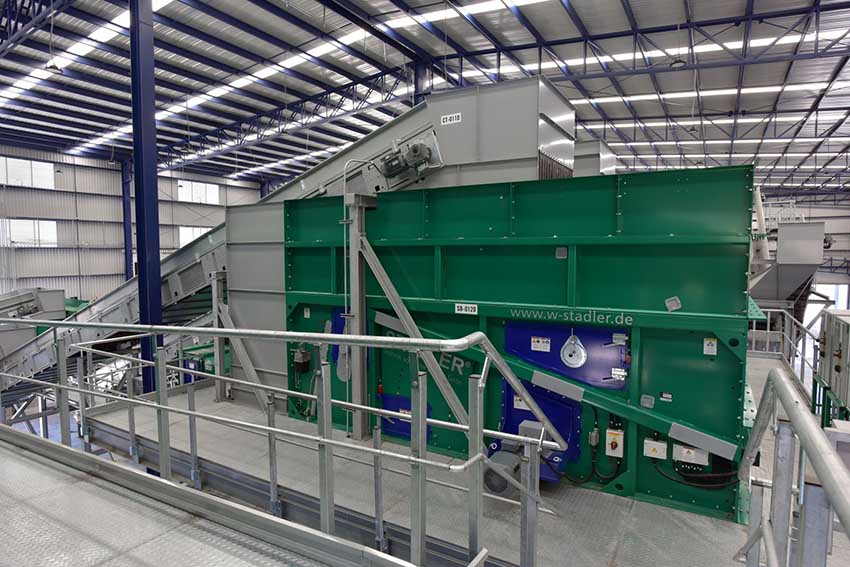
“This new plant fulfils our objectives on many levels: generating a purer biogas; reducing the carbon footprint; strategic alliances with firms that recycle and transform recycled input materials into green packaging; re-distribution of recycled input materials within a circular economy; and the creation of shared value based on sustainability and quality,” adds Crisóforo Arroyo.
“Our aim is to turn this project into a knowledge exchange platform for the various parties involved in the recycling chain and an ongoing laboratory where new waste management processes can be tested across the country,” says Natalya Duarte.
OFMRS, a process based on automation and technology
Within this circular economy-based approach, the most important points that set OFMRS apart are its high degree of automation (among the highest in the country), its ability to sort by type of polymer and color, and its management model.
With facilities spanning 3,800 m2, and a maximum output of 640-700 tonnes/day, OFMRS sorts, classifies, compacts and commercialises MSW, recovering materials including cardboard, paper, carton packaging, plastic, glass, and ferrous and non-ferrous materials. Biogas is also recovered from organic waste and fed to two Guascorde 1 mW power generators with a power output of 2mW. The energy generated is supplied to two companies in the state of Mexico through the power supply network owned by state-owned power utility CFE.
The plant’s automated closed-loop system comprises ten cutting-edge machines and thirty-five recirculating conveyor belts.
The process starts with reception of the MSW, which undergoes several processing stages, including the removal of ‘non-recoverable’ waste. It is then sorted into three groups: firstly, fine, metal and organic waste, which is sent to a reject container; secondly, flat or 2D waste (cardboard, paper, plastic wrap and carton packaging); and finally, bottled or 3D waste (PET, HDPE, PP, carton packaging and aluminium). The last two types of waste are forwarded to a manual sorting area. Finally, the conveyor belt feeds the materials into the compactor and the final product is ready: recoverable waste bundles (cardboard, paper, plastic wrap, carton packaging, PET, HDPE, PP and aluminium).
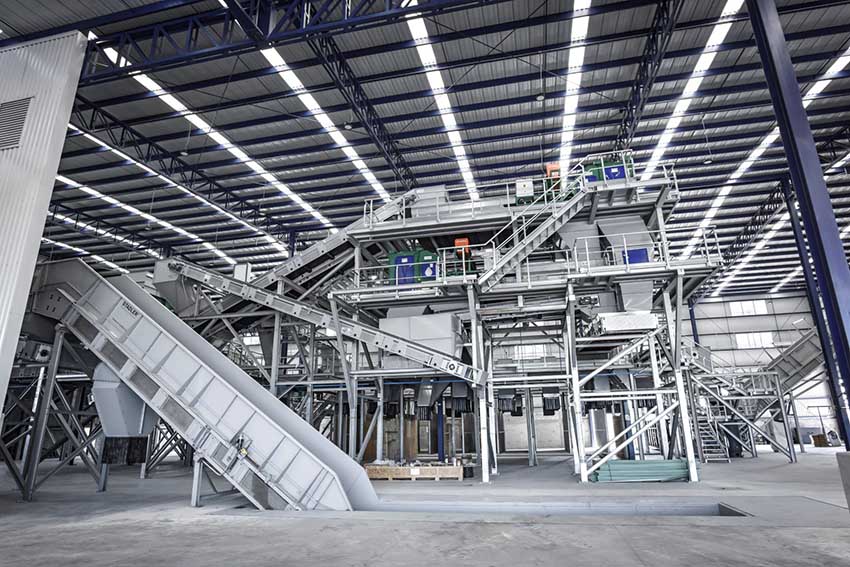
In the spotlight: the circular economy and environmental protection
In order to improve work practices, productivity, Occupational Health and Safety (OHS) and environmental protection, OFMRS has been operating to international ISO 9001 quality, ISO 45001 OHS, and ISO 1400 environmental standards since mid-2020.
According to Natalya Duarte: “This is the first project in Mexico that involves different parties in the recycling chain with the aim of protecting the environment. It is also the first national project that sets out to industrialise and professionalise the process, seeking the highest efficiency and purity levels and adhering to the strictest quality standards, including ISO.”
“The adoption of tried and tested German STADLER technology results in an attractive business model for using, recovering and recycling waste. By recovering waste in this way, the consumption of natural resources, water and energy is reduced,” according to OFMRS.
STADLER, integrated projects that can be relied on
STADLER works closely with clients to optimise its integrated projects. It provides clients with advice and support throughout the whole project and during the business model proposal: working out the project’s financial structure, developing the distribution channels, operating advice, designing the technical proposal based on the project’s specific requirements, and providing after-sales service, which includes maintenance plans and spare parts stocking in greater volumes and for longer periods.
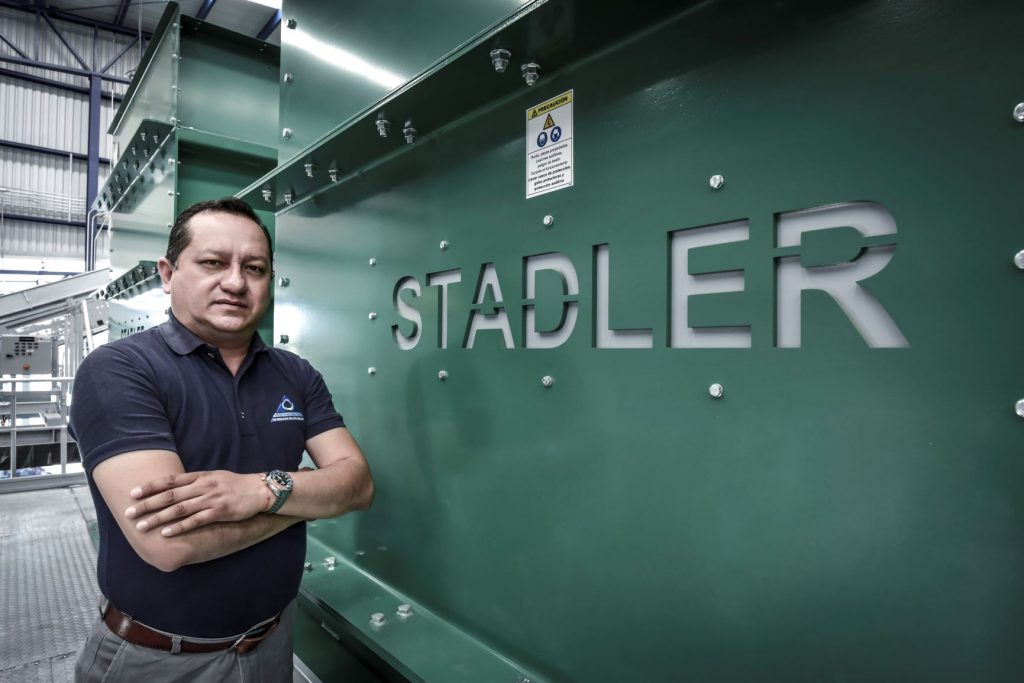
“Also, and even more importantly, STADLER provides ‘operational assistance’ which means that the technology provider continually oversees the client’s facilities. This guarantees maximum operational efficiency for the plant, which supplies its end product to leading companies in the food sector. These services include input/output waste profiling studies, quality control on selected materials and production, and more,” Natalya Duarte notes.
OFMRS confirms that the German company’s approach was a crucial deciding factor when it came to choosing a partner for the project: “Our decision to work with STADLER was not only based on their experience in the MSW sorting and recovery process, we also knew that they could help us to consolidate the project from a technical, administrative and financial perspective. STADLER also understands our needs and adapts the design of their technology to our new processes to professionalise MSW management.”