Induction heating has been around ever since Nicola Tesla discovered and harnessed the phenomena. His industrial applications made much of the modern world we know today possible. So, what exactly is Induction heating? For most applications it is the use of an alternating magnetic field on an electrically conductive part. The magnetic field pushes and pulls electrons within the material. The energy used to do this is dissipated as heat within the part. When properly controlled through coil design and current control, this can produce precise, repeatable and predictable results. This can be seen in modern induction stoves in many kitchens around the world. These stoves require a special pot with a bottom that can accept the magnetic field. Precise current control through an engineered coil provides even controllable heat with a nearly infinite temperature control.
But did you know that Induction heating has solved many industrial challenges as well?
#1 Removal of worn-out boiler tubes from a tube sheet.
The issue: In large industrial boilers as found in many power plants water is fed in to a large header then up through small tubes to another header where the heater water or steam is gathered and sent to be used other places in the power plant. These tubes degrade over time and must be replaced. Within an industrial application these headers my be 3” or thicker and 48” in diameter with 1000’s of 2” diameter holes where the tubes are inserted and then rolled and expanded into the holes. In the past skilled technicians used cutting torches to slice the tube and then beat it out with chisels. Many times, this resulted in damage to the tube sheet that required welding and machining prior to fitting and rolling in new tubes.
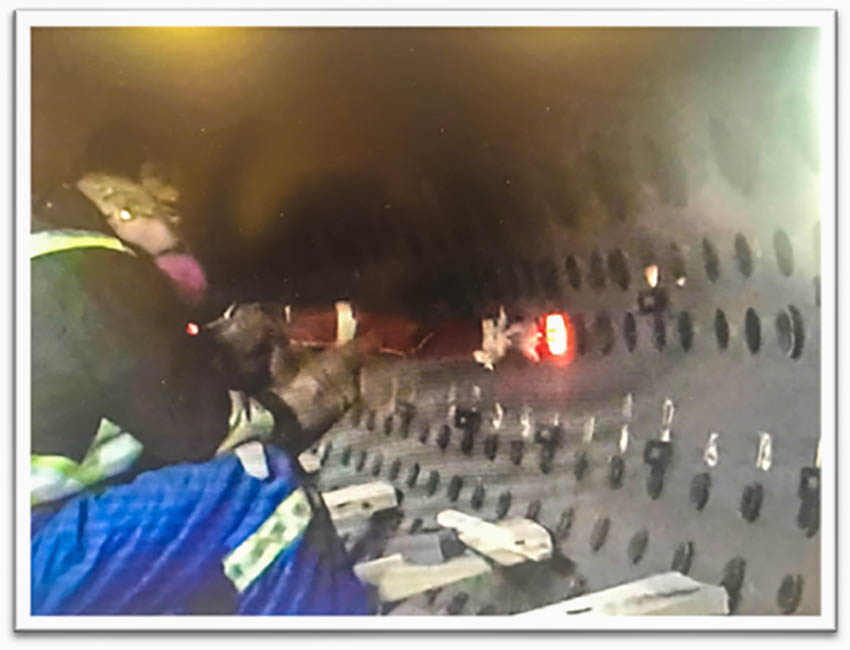
The solution: Use a specially designed portable induction machine with a specially designed internal coil. This heats the tube rapidly where it is rolled into the tube sheet. The tube reaches 2500F (Approximately 1370C) within 30-90 seconds. This rapid heating causes the tube to attempt to expand but, since it is constrained by the tube sheet and is heated to a malleable temperature, the tube shrinks. At the same time a hydraulic puller can be used to pull the hot tube out while it is still hot.
#2 High Temperature Testing/Thermal Cycling
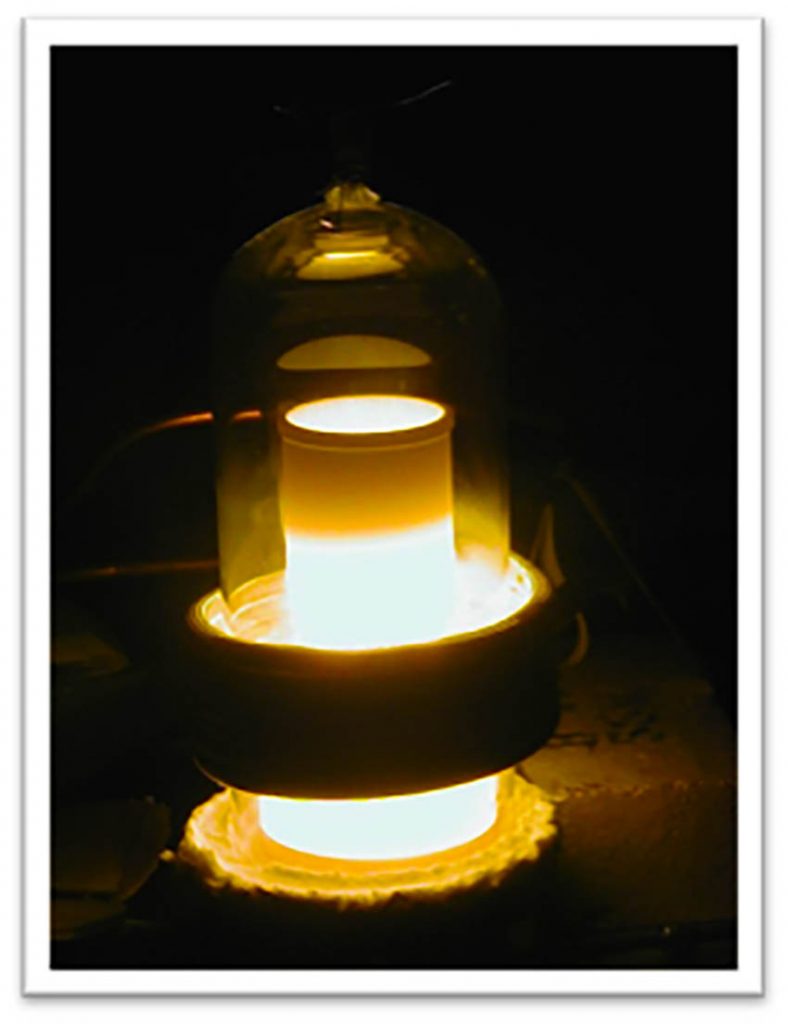
The issue: High temperature testing can be difficult as normal resistance heating methods are limited by the melting point of the heater elements. The higher the temperature the more difficult this is to achieve.
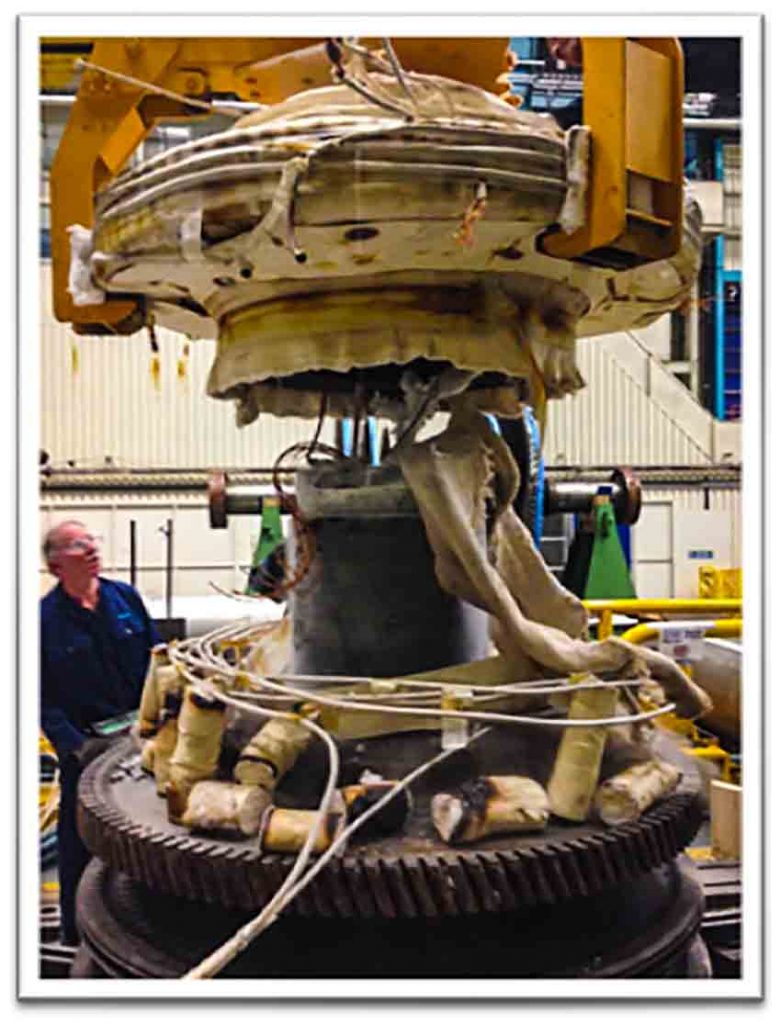
The solution: Induction, when engineered correctly, does not have any top temperature limit. One example where an induction machine and an engineered coil, test cycles can easily be run to 4000F (2204C) where the only limitation is the support of the part or material being subjected to these high temperatures. These testes were done to evaluate high emissivity coatings and catalysts that normally run at excessively high temperatures.
#3 High Speed Curing of Coatings
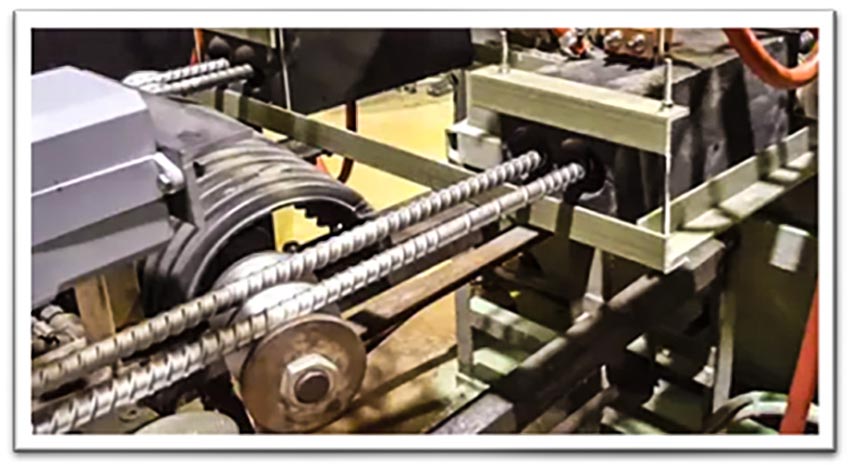
The Issue: Protective coatings can take time to dry or must be melted on to provide an adequate coating bonded to the substrate. Coating Rebar, Angles, bars and much more was done using industrial gas fired ovens moving material through these ovens at speeds up to 300 feet per minute.
The solution: custom built induction machines were used along with engineered coils to provide heat to the parts prior to coating them. For powder coated parts these bars pass through the powder booth shortly after the induction heating. This adds enough heat to melt the powder and adhere to the parts consistently and evenly and since the heat is so fast, its only on the outer surface causing a rapid cooling after the coating adheres. This greatly reduces the production line length. The same can be done for painted on products, force curing the paint shortening the overall line length and removing a source of heat and CO2 within assembly plants.
#4 Thermal Expansion
The issue: Large heavy shrunk on parts of a Turbine or Generator rotor need to be removed to repair or replace the part or components underneath. In the past Electrical resistance heating or flame rings were used to heat and thermally expand large components for removal. Electric resistance has limitations in its total heat input and flame rings can severely affect the metal or burn adjacent components and combustion byproducts are poisonous to humans.
The solution: Custom designed portable induction heating equipment and flexible coils are used to apply the magnetic fields and heat in the appropriate places to thermally expand these components for removal. This is not limited to the power generation industry. Applications can be found in Steel Mills, Paper Mills and Sugar Plantations to name just a few.
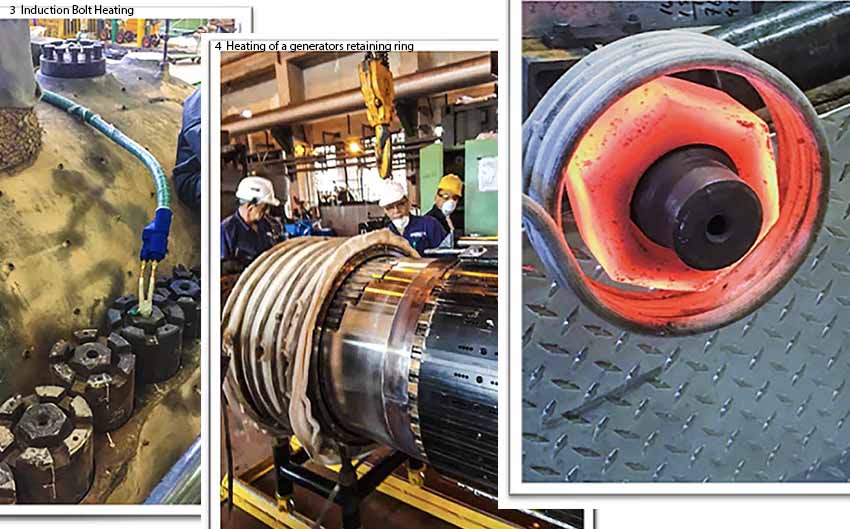
#5 Disassembly of Rusted Nuts and Bolts
The issue: In many industrial places bolted flanges are common. These flanges are outside and exposed to the weather and may become corroded or rusted to the point where they cannot be removed by simple torquing methods.
The solution: Induction coils can be wrapped around these rusted and frozen nuts. Then when the heat is applied two things happen. The rapid expansion helps to break the bond formed by the iron oxide and the second is the further degradation of the rust into finer particles. These smaller particles no longer lock the nut to the threads allowing for the mechanical turning and removal of the nuts.
Note: These are just a few of many industrial applications for Portable or Stationary induction heating machines. New applications are found every day.
Autor: Jeff Weinacker, President Mobile Induction Solutions, at Thermo International.
For Help with Field Heating applications give Jeff a call at 973-970-9500 or visit Thermo’s webpage Thermo International Services LLC – Induction Heating Specialists