Technoplants was founded in 1984 by the president Marco Gualtieri. The company designs and manufactures nonwovens machinery and turn-key plants for automotive, insulation, furniture, geosynthetic and many other sectors. Technoplants is always innovating with patents of new machinery technologies able to process any kind of fibers.
Easy Engineering: What are the main areas of activity of the company?
TECHNOPLANTS: Our main activity is the sale of complete airlay lines. The core machine of this type of nonwoven production lines is of course the airlay machine, that is a forming machine making nonwoven webs thanks to the combined action of opening cylinders and air streams.
Our airlay technology – that we named MULTIline – is a modular system composed of 4 airlaying sections, that we can combine in different ways (for example you can buy only 1 module, or only 2, …); in addition the clients who buy our complete airlay system have the possibility to use only some of the modules and not the others, because the machine is equipped with internal bypasses.
This flexibility makes the range of nonwoven products that can be made very wide: virgin fibers, natural fibers, recycle fibers; bonding with low melt fibers or with low melt powders; basis weights from 10 to 15,000 gsm.
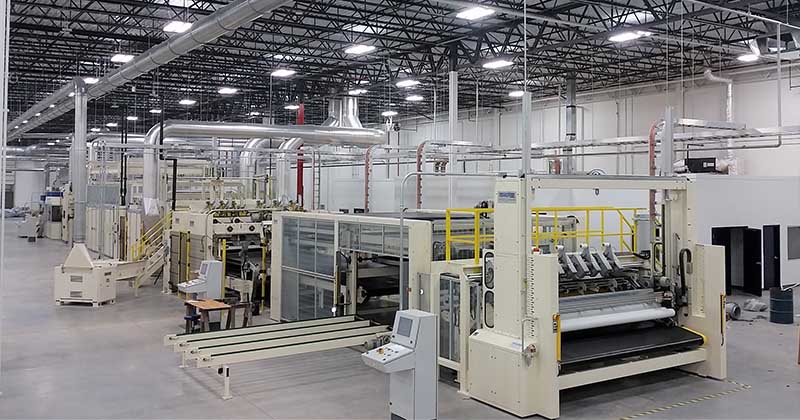
E.E: What’s the news about new products?
TECHNOPLANTS: In the last couple of years we focused on increasing the production range of our airlay machines on both the low and high end in terms of basis weights, expanding it from the old 70 – 5,000 gsm to the current 10 – 15,000 gsm. This is possible thanks to upgraded airlay MULTIline modules:
MULTIline D. A hybrid between airlay card and traditional roller card, to make light nonwoven webs starting from 10 gsm. This new airlay card can be used to feed crosslappers, feed vertical lappers or just to make high-quality low-weight airlaid nonwovens.
MULTIline H. A carding airlay for high basis weights, up to 15,000 gsm. The characteristic to open and homogenize the fibers but at the same time still be able to reach high weights and thicknesses make this airlay model very suitable for polyurethan foam replacement, that means to replace PU foam with nonwoven products able to replicate the same cushion and resiliency, thanks to special elastomeric polyester fibers.
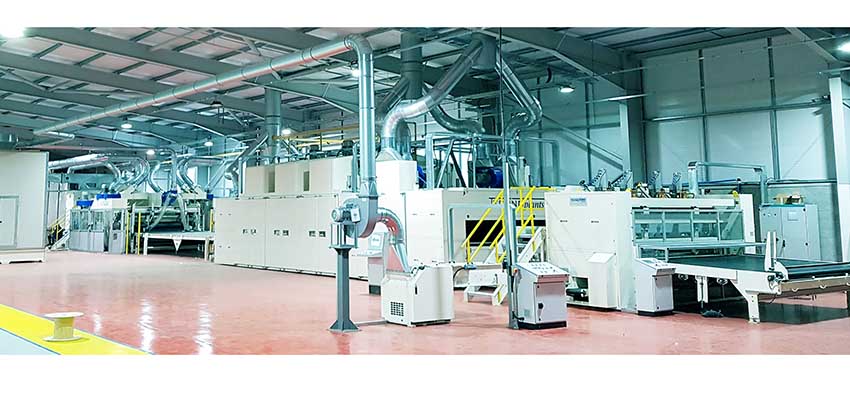
E.E: What are the ranges of products?
TECHNOPLANTS: Apart from airlays, our supply for the nonwoven machinery sector is completed by double belt thermobonding ovens and needle looms for the fabric bonding, crosslappers and then by the machines for transformation into the final format: cutting, winding or stacking, packaging.
E.E: At what stage is the market where you are currently active?
TECHNOPLANTS: Our main market is the sale of complete airlay lines for nonwoven felts and waddings.
Although this is an already well developed industry, there are always new end-products that are developed and new applications for the nonwoven products, where until a while ago nonwovens weren’t used at all. Examples are nonwovens from hemp, recycled leather, tires and even hair!
We are by the side of our clients to carry out this research and development work and to do this we have a complete airlaying pilot line in our premises, where our potential clients can develop their ideas and verify our capabilities.
E.E: What can you tell us about market trends?
TECHNOPLANTS: A big market tendency is for sure sustainability and circular economy.
Customer awareness and government regulations are pushing the nonwoven market to recycle textile wastes into their own products and to replace the non-recyclable ones with recyclable or compostable alternatives.
The airlay is the protagonist of this push, since it is a technology born exactly to process recycled and natural fibers. The airlaid products made from natural or recycled fibers are used in the nonwovens industry for various applications, for example for the automotive industry, insulation, mattresses, and furniture felts.
The other market trend is smart automation and Industry 4.0 solutions: our clients want to improve the automation, machine to machine communication and monitoring of their nonwoven lines.
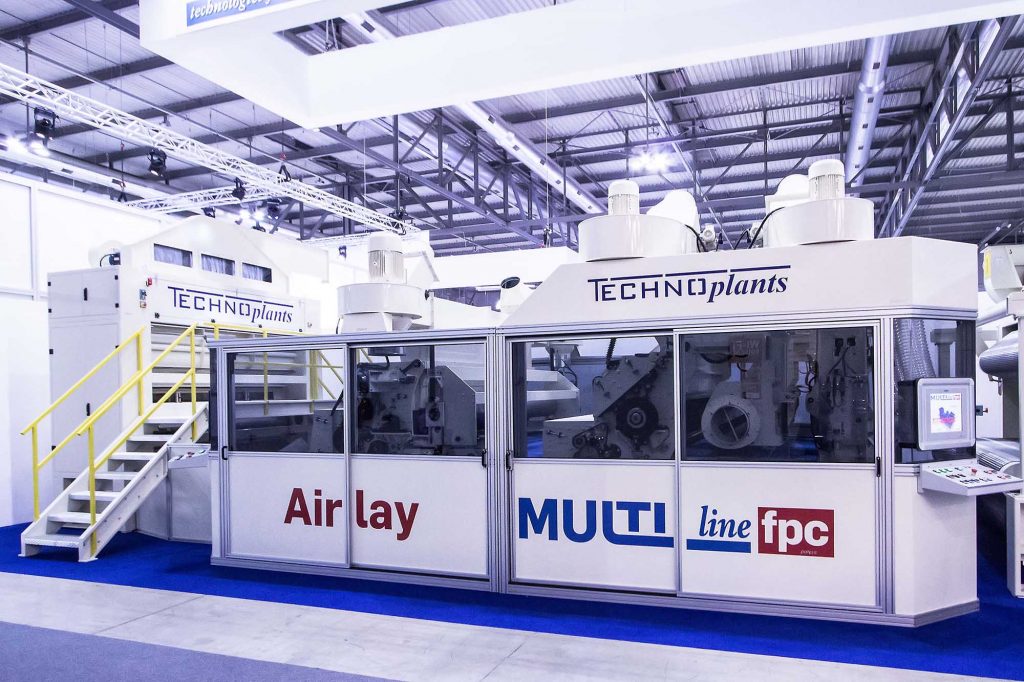
E.E: What are the most innovative products marketed?
TECHNOPLANTS: At TECHNOplants we are continuously improving the current machines and developing new ones, for which we are patent owners. Apart from the new airlay models that we described above, we developed a range of pressing ovens to make compressed, laminated and smoother nonwovens. The scope can be simply to increase the fabric density and stiffness or – in case of recycled nonwovens that go to replace traditional products – to improve the touch and sight of the fabric surface and make it more appealing for the final users.
E.E: What estimations do you have for the rest of 2022?
TECHNOPLANTS: The volatility and rising of the energy costs make it difficult for our clients to plan product launches and new investments, in particular in Europe. Neverthless we expect the good trend of the airlay market to continue. First of all because the push from the consumers for the development of recycled and sustainable nonwovens is stronger than the fears about the energetic crisis; then also because our airlay lines and the nonwoven products that they manufacture are actually of help in the energetic crisis: examples are the hemp and other natural fibers nonwoven insulation used in electric cars and in the building industry. On our part we stand by our clients by improving the energy consumption of our machines with new less consuming models and by replacing the energy sources, for example offering electrically heated ovens instead of gas heated ones.
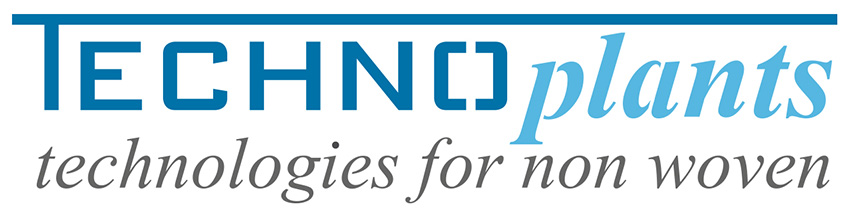
+39 057398471