High temperature turbine engine components have garnered increased interest in longer life coatings. In applications where precision and durability determine success, G-M Enterprises, a Nitrex company, is making significant strides with advanced aerospace coating technologies. Specializing in Vapor Phase Aluminide (VPA) and Pack Cementation coatings, these processes are redefining industry standards for enhancing gas turbine components, from thrust chambers to turbine blades, rocket nozzles, and beyond. For over 30 years, Nitrex’s vacuum division has collaborated with leading engine makers on these processes.
Today, operator safety and long-life furnace design has led to a resurgence in Nitrex VPA systems. Designed for the demanding environment of aerospace applications, where prolonged high-temperature operation is crucial for fuel efficiency, the Nitrex Sealed Atmosphere Retort Furnace (SAR) for VPA plays a pivotal role.
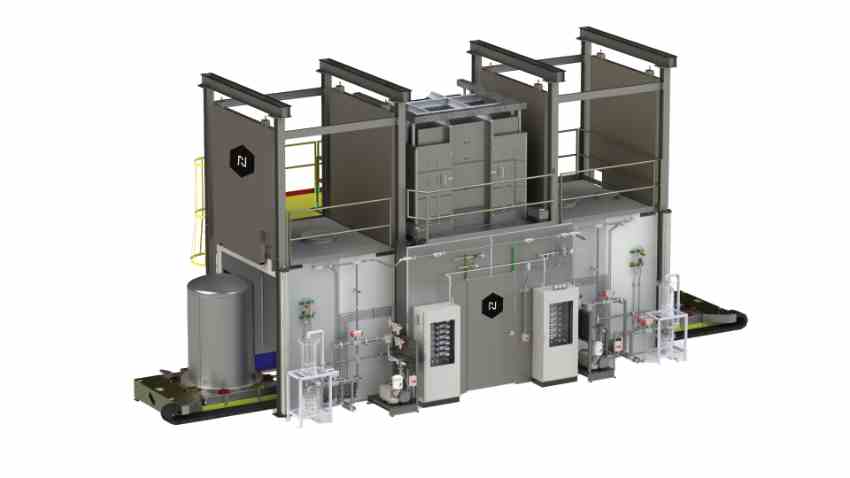
Technical Innovations in Nitrex SAR Furnaces
Through meticulous design and control, Nitrex SAR furnaces reliably produce additive layers that act as protective barriers against oxidation and corrosion, ensuring the integrity of the aluminide coating and eliminating concerns of spalling, peeling, or blistering that can lead to premature failure or malfunction of mission-critical parts. The flexibility of SAR furnaces makes it possible to achieve specific thicknesses and microstructures without impacting mechanical properties.
What makes the Nitrex SAR design unique is the central furnace, which services two bases that automatically and safely move into heating positions and into cooling positions. The system allows for adequate load build time in a safe, secure, and cool environment. Specialized racking, directional flow capabilities, and precise tooling planning enable Nitrex SAR furnaces to adapt to the evolving needs of customers. With over 50 units built, Nitrex’s vacuum division has a long history of providing long-life tooling designs, proper gas flows for vapor uniformity of the coating, and safe handling of exhaust gases. Nitrex can handle various recipes of donor and activator materials and offers both Argon gas and Hydrogen gas systems.
FEATURES
- Enclosed automated base for enhanced safety and convenience during operation
- Cold retort loading protected from any heat
- Automatic movement, heating, and cooling capabilities in an enclosed system allows for installation in temperature and humidity-controlled factory environments
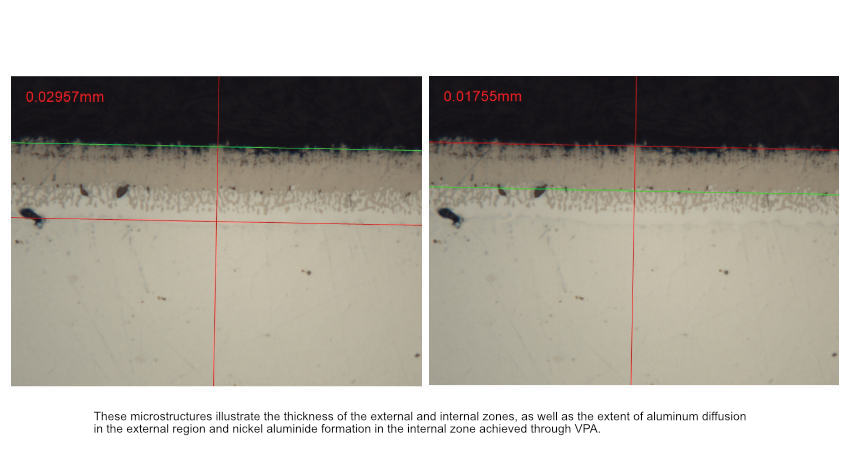
Fundamentals of the NITREX Vapor Phase Aluminizing Coating Process
The Nitrex VPA coating process involves several design considerations, such as gas flow optimization inside and outside of the coating cans, temperature control, rack design, donor material box design and donor material selection and placement throughout the loading can. A precise combination of temperature, gas flow, and activators is used to activate donor material strategically around the parts. Donor materials, in pellet and powder forms, are chosen for their specific contributions to the coating process.
In modern VPA, donor material exists as pellets in special donor boxes, carefully avoiding direct contact with the parts. Pack Cementation, in contrast, immerses parts in a powder mixture of donor material. The aluminide coating isn’t just a superficial layer; it serves as a bond layer for a ceramic thermal barrier coating (applied post VPA process), achieved through the development of an alumina (Al2O3) layer. Process temperatures of around 1800°F–2000°F (982°C–1093°C) for two to eight hours, depending on desired thickness and part requirements, create the perfect conditions for this transformation. During the final stage of the process, the material is slowly cooled with argon at an intermediate temperature to preserve its coat. After that, the system moves the treatment chamber to a fast cool position, and a new load is automatically positioned into the heating chamber. This results in a thin aluminide bond layer of up to 0.005 inches (127 µm) thickness, which provides comprehensive coverage even for internal cavities or blade passages.
Nitrex SAR furnaces and VPA technologies are at the forefront of aerospace coating technology, providing ease of use, unmatched safety, and reliability. Operating at high coating temperatures requires the most advanced alloys for optimal durability. Proper seal cooling design is essential to ensure safety and integrity throughout the process. With a moveable base design incorporating a blend of metal and non-metal hardware, these furnaces are engineered for long-lasting performance and reliability. Moreover, the clamping system is meticulously designed to enable repeatable and secure operation. It’s no wonder that the Nitrex VPA furnace stands as the preferred choice for turbine engine high-temperature coating systems on the market today.
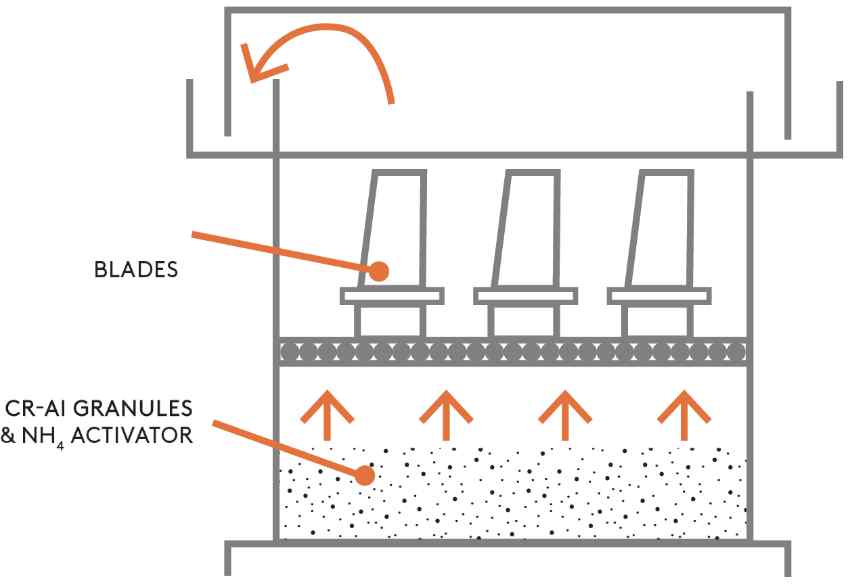
ABOUT NITREX
At NITREX, we’re your go-to for high-temperature vacuum and coating furnaces. We serve clients in various industries, including aerospace, power generation, energy, and commercial heat-treating. Our furnace line from G-M Enterprises, a Nitrex company, is designed and manufactured with meticulous attention to detail, expertly installed by our team, and fully supported throughout its lifetime for the best customer experience. Click Here to download our Free Brochure.