Loop Technology are specialists in industrial automation, designing and building innovative systems that improve production rates and product quality for the high value manufacturing sector. Established in 1998, the company has a wealth of experience in machine vision, motion control and robotic integration, providing advanced solutions for companies in sectors such as aerospace, defence and renewables.
Interview with Tom Turner, Marketing Executive at Loop Technology.
Easy Engineering: What are the main areas of activity of the company?
Tom Turner: Our expertise lies in composites automation. From kitting, cutting and layup through to inspection and stabilization of material such as carbon fibre, our systems automate the entire preforming stage for manufacture of composite parts and components. FibreLINE is revolutionary because it offers a step change in material deposition rates meaning composite structures can be built at a much faster rate whilst using less space and energy compared to other traditional manufacturing methods. We also specialize in automated laser cleaning and robotic machining.
Loop Technology are trusted partners of global robot manufacturers KUKA and Fanuc as well as several high value manufacturing research centers in the UK including the National Composites Centre (NCC) and the Manufacturing Technology Centre (MTC). Last year, we announced our participation in the inaugural project at the innovation facility at the Advanced Manufacturing Research Centre in Sheffield (AMRC) alongside Boeing and Spirit AeroSystems. This venture will push forward composites automation technology in aerospace and help meet decarbonization targets in the industry.
E.E: What’s the news about new products/services?
T.T: Our FibreLINE system provides high-rate material deposition for the manufacture of composite structures such as aircraft wings, wind turbines and automotive parts. It is an end-to-end automation solution providing a deposition rate of up to 200 kg per hour. This is a step change compared to AFP which deposits at rates from 20kg-40 kg per hour and other traditional methods.
We also provide highly advanced laser cleaning solutions for applications such as cleaning industrial equipment and moulds, treating surfaces prior to welding and bonding and nuclear decontamination. LoopCLEAN Auto is a next-generation product that leverages our RealPATH software to achieve a pioneering level of automation. It uses 3D imaging combined with singularity and collision avoidance algorithms to clean the component without CAD and offline programming, resulting in significantly less operator interaction.
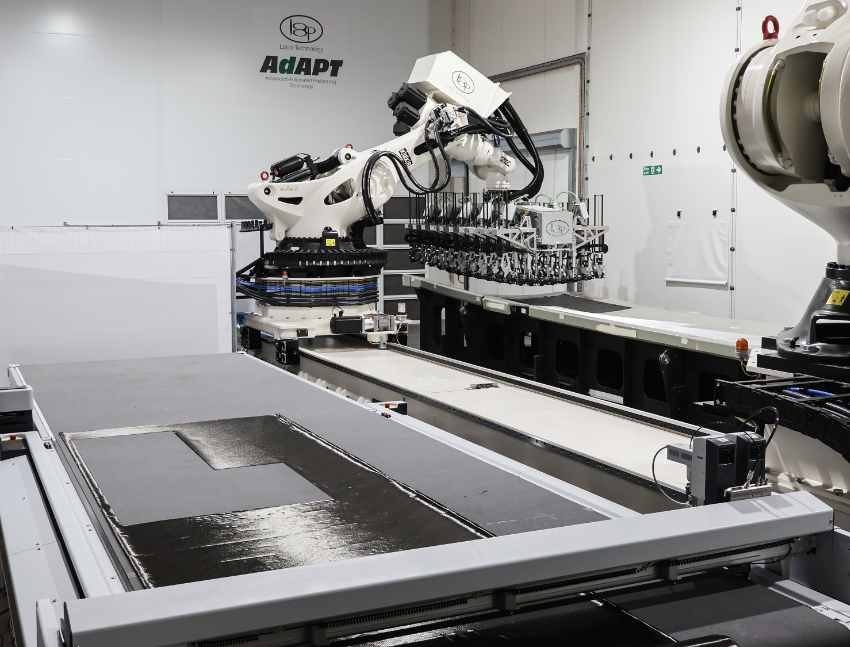
Furthermore, we are specialists in robotic machining systems. RoboMACH HA is an off-the-shelf solution that gives users the ability to machine materials such as cured carbon fibre, wood, foam and plastics with a very high degree of accuracy. It’s a cost-effective alternative to a large-capacity machine tool, providing automated drilling, cutting, trimming, and milling.
E.E: What are the ranges of products/services?
T.T: Our FibreLINE system is available in different configurations. The exact configuration is dependent on the customer requirements and is selected from our suite of products that includes FibreFORM, a state-of-the-art 3D composite ply pick and place end effector, and FibreROLL, capable of handling carbon fibre plies up to 20 metres long. Additional products include FibreKIT that sorts and sequences plies at an exceptionally fast rate whilst optimizing material utilization, and FibreEYE, that uses advanced optical scanning to automate the inspection of material and ensure it is defect free. Moreover, we recently presented FibreLINE 2X1 at JEC 2024, a system that automates preforming when manufacturing smaller composite parts and components such as aircraft fairings, nacelles, ailerons, and wing tips.
The LoopCLEAN range provides varying levels of automation in robotic laser cleaning. Our standard offering gives the operator the ability to program and control the robot via a robotic pendant whilst LoopCLEAN Pro and LoopCLEAN Auto provide increasing levels of automation.
Loop Technology are the official UK distributor and service provider of cleanLASER systems, providing a range of models including the CL 1000 and the CL 2000 that provide average laser power of 1000 watts and 1600 watts respectively. We are also the official UK reseller of Robotmaster, the leading offline simulation solution that dramatically reduces robot programming time through the quick generation of robot trajectories.
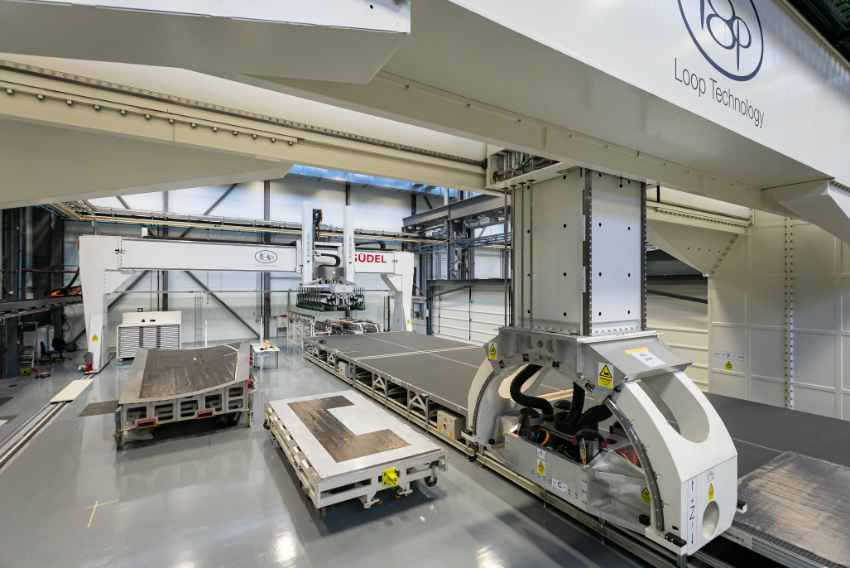
E.E: What is the state of the market where you are currently active?
T.T: The advanced manufacturing sector is experiencing significant growth and investment- it is tremendously exciting time to be involved. There is a boom in the aerospace sector, with 3,850 aircraft orders in 2023 alone and an aircraft backlog of 15,753, the largest on record. The demand continues to grow but manufacturing methods such as hand layup and AFP/ATP alongside labor shortages mean supply cannot keep up. This approach struggles to produce 11 shipsets per month. Innovations in robotics around scale, precision and collaborative working provide a potential route to producing 100 shipsets per month, the target that the aerospace sector needs to achieve to meet the demand.
E.E: What can you tell us about market trends?
T.T: We see more of the market investing in innovative automation solutions persuaded by more demonstrations of how they can provide a tangible increase in productivity and cost effectiveness. The trend towards decarbonization and reaching net zero targets continues unabated and the use of composite material to build lighter structures in aerospace, defence, renewables and automotive is accelerating.
E.E: What are the most innovative products/services marketed?
T.T: Our products are on the frontier of industrial automation technology, solving highly complex engineering problems that were often previously seen as insurmountable.
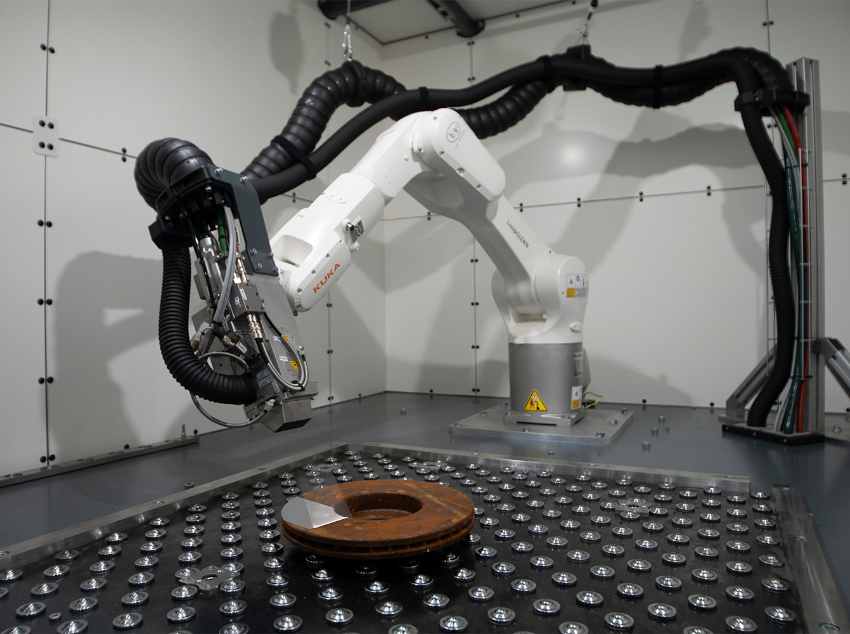
FibreLINE is a unique system for composites preforming automation not seen anywhere else in the world. FibreFORM, a constituent part of FibreLINE, is made up of individually controlled, fixed-pitch grippers positioned along a series of splines. Its award-winning design can manipulate plies to match a complex double curvature 3D surface and place the ply onto a mould with a positional repeatability ± 1.0mm. Its capacity to handle large pieces of multi-axial ply means it can cut the number of pieces required to manufacture an aircraft wing from 100,000 down to potentially 150. It won the ‘Innovation in Composite Manufacture’ at the 2021 Composites UK awards and will now be used at the innovation facility at AMRC. A different configuration of FibreLINE, which uses FibreROLL, has achieved a trailblazing composite deposition rate of 350kg per hour in development trials at the National Composites Centre.
Our RealPATH software is another innovative solution that provides next level automation in the generation of robotic pathways whilst Bravura is a robotic arm that can deliver a process head into confined spaces like aircraft wing boxes.
E.E: What estimations do you have for 2024?
T.T: We are excited to see this groundbreaking new project at the AMRC continue to progress and are thrilled about our expansion into North America having recently announced another FibreLINE order is to be delivered there. Moreover, we will be sharing more insight into our technology from our demonstrator AdAPT cell at our headquarters in Dorchester. Watch this space!