A fully integrated surface treatment solution provider, Nitrex works with the entire aerospace supply chain from OEMs to tier suppliers, offering turnkey heat treatment systems, contract heat treat services, and failsafe digital controls that consistently outperform industry standards. With over 40 years of experience, Nitrex has become a standard-setter to the metal-treating industry. The company caters to the aerospace industry’s stringent quality standards across segments that include aircraft manufacturing, helicopters, satellites, space vehicles, rockets, and missiles, ensuring that mission-critical products function as intended.
Nitrex’s commitment to component reliability, durability, and safety, in addition to compliance to regulatory requirements ensures that customers’ critical parts will perform under the conditions required for the end-use application. Mark Hemsath, President of Turnkey Systems at Nitrex, explains that “we assist customers in selecting the right solution by leveraging our deep knowledge of the industry, metallurgy, heat-treat processes, upstream and downstream manufacturing operations, and component requirements. By working closely with customers, we can identify areas where our solutions can make the biggest impact, optimizing accuracy, achieving compliance, and delivering consistent performance.”
ADVANCED VACUUM HEAT-TREATING FURNACES FOR AEROSPACE
The space tech industry significantly benefits from Nitrex’s vacuum heat-treating furnaces, which are designed to process materials at high temperatures with high purity, enabling a contaminant-free atmosphere similar to the environment in space. This industry requires strict QA standards, and clean environments are essential to meeting those standards. Nitrex vacuum furnaces come in various sizes that can process different parts, ranging from the smallest component that can fit in the palm of a hand to parts the size of a small room.
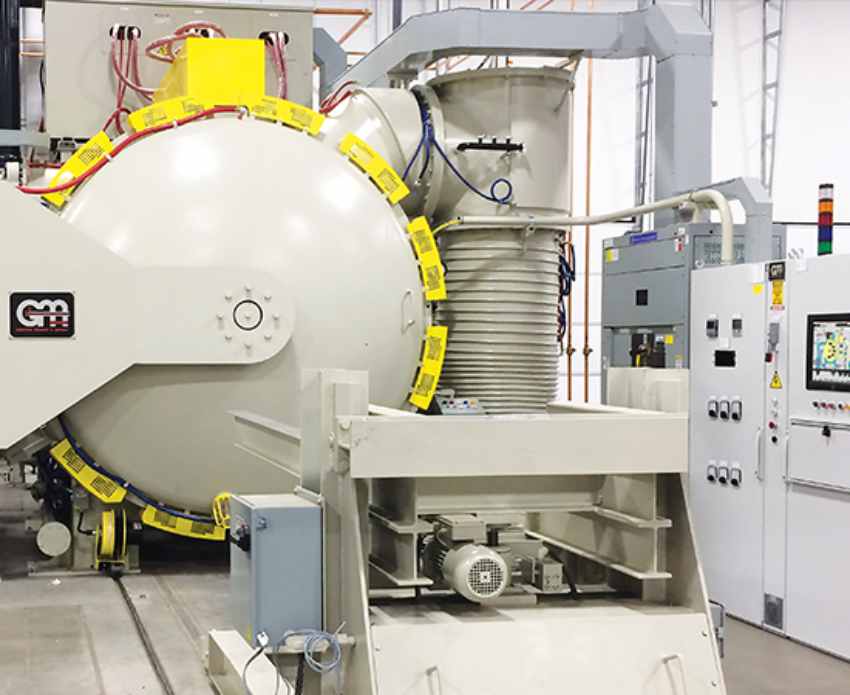
Horizontal vacuum furnace relied upon for processing diverse materials and heat-treating applications, from simple steel to high-temperature nickel-based alloys and titanium.
SPECIALIZED EXPERTISE IN VAPOR PHASE ALUMINIZING
Nitrex’s expertise in processing stainless steel is particularly valuable for the space industry, especially in the complex manufacturing of jet engine turbine blades. Its vapor phase aluminide (VPA) coating furnace applies aluminides onto turbine blades to help withstand high temperatures during aircraft engine operations. Nitrex is one of the few companies offering this specialized system to facilitate long engine life.
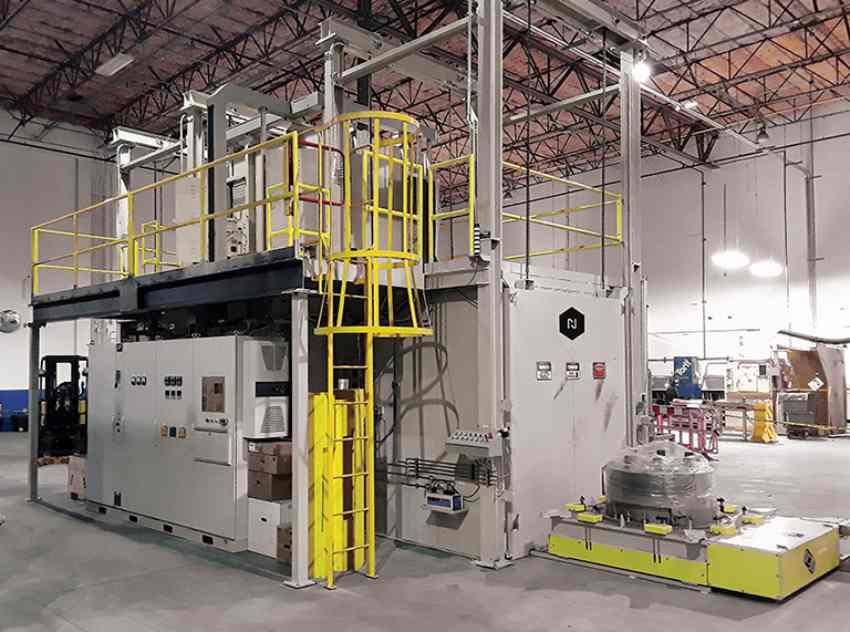
The high-temperature Sealed Atmosphere Retort (SAR) designed for vapor phase aluminide (VPA) coating technology is the go-to furnace for aerospace manufacturers looking to enhance the performance and extend the life of turbine blades and vanes.

Coated blade and engine vane treated with vapor phase aluminizing in a Nitrex sealed atmosphere retort furnace.
CONTROLLED GAS NITRIDING FOR AEROSPACE COMPONENTS
Another popular surface hardening process that is equally effective in optimizing part performance of aerospace components is controlled gas nitriding. Nitrex’s turnkey nitriding systems enhance mechanical surface properties, increasing the surface hardness to significantly improve fatigue strength without affecting the dimensional stability of the application. This is particularly useful for hardening critical parts like engine bearings, fasteners, gears, fasteners, shafts, and valves.
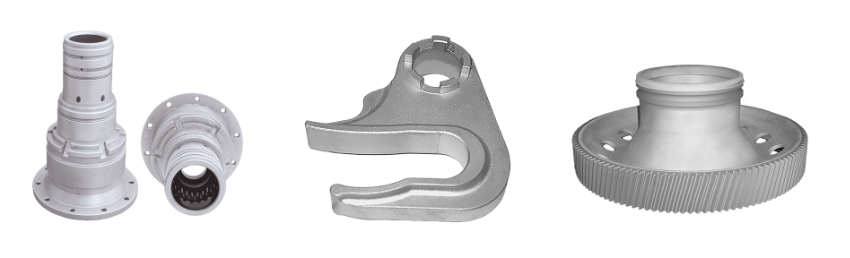
HEAT TREATING SERVICES AND COMPREHENSIVE SOLUTIONS
It’s important to note that Nitrex not only provides new furnace installations but also offers heat-treating services for the military and aerospace industries at its Nadcap-certified heat treating centers. This dynamic interplay between our equipment and services divisions provides Nitrex’s furnace engineers with real-world exposure and hands-on experience in working with aero, space, and military specifications and requirements. As a result, when aero and space suppliers approach Nitrex, they can be confident that Nitrex has a thorough understanding of the critical equipment requirements necessary for their customers’ operations. Drawing on decades of practical experience, Nitrex is also well-placed to suggest manufacturing and product enhancements or even reimagine the customer’s process.
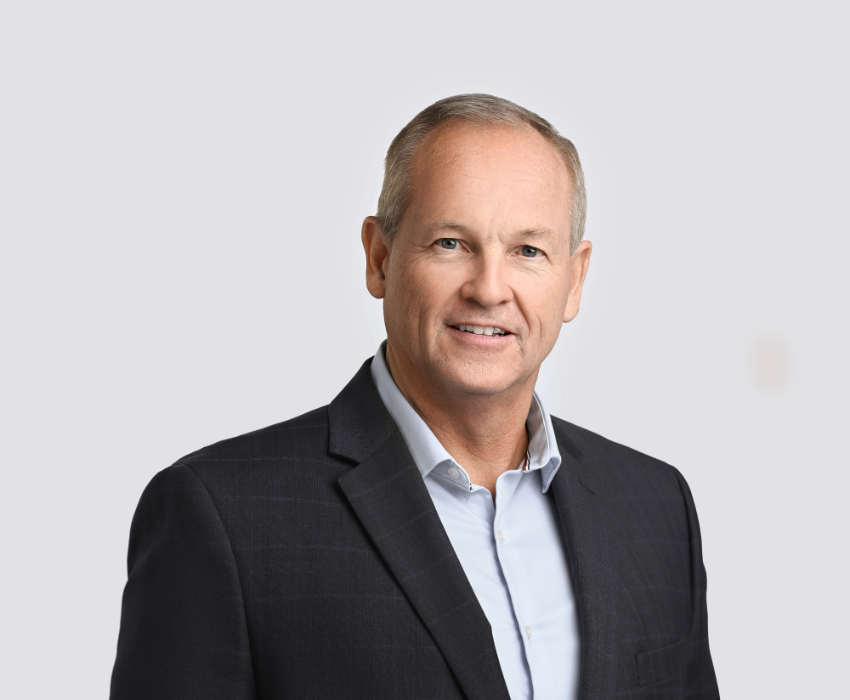
“We assist customers in selecting the right solution by leveraging our deep knowledge of the industry, metallurgy, heat-treat processes, upstream and downstream manufacturing operations, and component requirements.” – Mark Hemsath, President of Nitrex Turnkey Systems.
Nitrex’s vacuum furnace business has been experiencing steady growth over the years, resulting in the company expanding its manufacturing footprint to meet increasing demand. In addition to its existing manufacturing facility in the U.S., the company has also established manufacturing operations in Poland to further support its customer base across Europe and Asia. With its team of experts in the field of nitriding, vacuum, heat treating in general, as well as metallurgy and process controls, Nitrex builds strong client relationships that go beyond price and ensures customers receive a solution that meets their needs for years to come.