In today’s world, the tiniest of electronic components, fractions of millimeters in size, are critical to innovations ranging from electric vehicles, data centers, medical devices, to consumer electronics and more. The impact of these tiny parts hinges on the highest levels of performance, and small size often equates to large room for error.
Indeed, faulty components usually lead to defective products, the consequences of which include costly recalls, expensive rework, financial losses, legal disputes, and declines in consumer trust. In 2023 alone, 35 million automotive vehicles were recalled primarily because of electronic component malfunctions.
However, ensuring component reliability and, in turn, product integrity is no easy feat. Defects such as corrosion, contamination, or counterfeit parts can be extremely difficult to detect at such a small scale.
Cybord, the leader in visual AI electronic component analytics, offers an answer to this challenge. Cybord’s Real-Time Interceptor (RTI) solution utilizes deep learning algorithms to identify, intercept, and eliminate defective components before they are assembled on circuit boards.
This AI-powered platform accomplishes more than just ensuring top-tier product security, safety, and quality assurance: It streamlines production, enhances end-product quality, bolsters customer trust, and helps manufacturers drive sustained profitability in an increasingly competitive market.
Imprecise Quality Control Leads to Lost Profits
To filter out defective components before they reach end users, manufacturers have traditionally relied on manual checks and statistical sampling. But these methods are notoriously prone to human error and can allow faulty components to slip past detection. While automated optical inspection (AOI) machines are a vast improvement in automating quality checks, their view is limited as they only scan the top of components, and with most defects appearing on the component’s bottom side, they may go undetected.
Without integrating AI-powered technology like Cybord’s into surface mount technology (SMT) machines, manufacturers often miss component flaws until the final stages of production – if they’re lucky. By then, however, fixing them may become too complex or costly. About 10% of defects discovered at these later stages usually require the entire circuit board to be either reworked or completely scrapped. And with each step in the manufacturing process, the cost of addressing these defects increases by a factor of 10, eating into profit margins and diminishing assembly line efficiency.
Although the profit losses and capacity reductions that result from reworking or scrapping components at later stages are considerable, the financial and reputational damage caused by recalls, when faulty components are discovered by end-users, represents the worst-case scenario for any OEM.
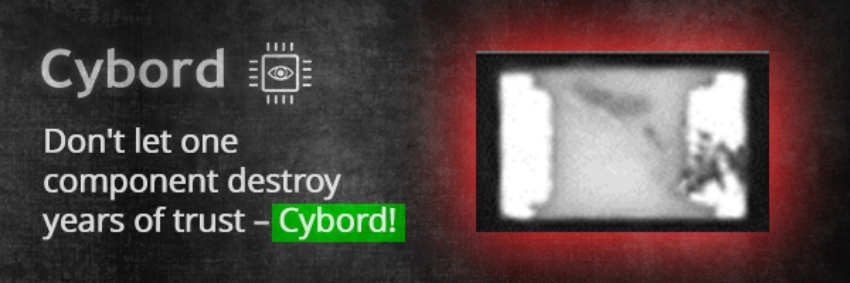
Challenging the Status Quo
Due to incomplete quality control methods, many manufacturers have resigned themselves to factoring in faulty component-related losses into their annual budgets and set aside substantial capital to cope with potential recalls, warranty issues, or legal challenges. In 2022, for example, Kia and Hyundai collectively set aside over two billion dollars – more than half their net profits – to cover potential recall-related costs.
Inefficient inspection methods also push manufacturers to allocate resources towards rework stations – workbenches that are equipped with specialized tools to manually replace defective components on the circuit boards at the end of the manufacturing line. In some cases, circuit boards wind up being scrapped entirely, contributing to material waste and lost operational efficiency. In fact, scrapping and reworking protocols consumes upwards of 2.2% of an organization’s annual sales, which for industry giants typically amounts to six figures or more.
It’s time for manufacturers to undo the profit-draining status quo by integrating real-time AI-powered component analysis technologies. This will help manufacturers transform their quality control processes, protect their profits, and boost overall manufacturing efficiency.
The Solution: Real-Time Interception
AI-driven real-time quality inspection offers manufacturers a reliable means of detecting and addressing defects in electronic components before they are assembled onto printed circuit boards and installed in electronic products.
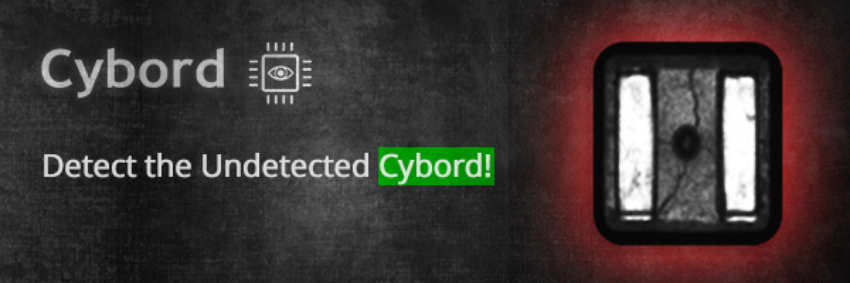
Think of RTI as an MRI for your electronic boards. This software add-on seamlessly integrates with pick-and-place assembly machines, enabling real-time sorting of 100% of components. By detecting and rejecting defective parts before they reach the boards, RTI not only ensures higher product quality but also boosts production capacity, reduces the need for rework, and minimizes the risk of costly recalls.
Every Component Counts!
The rise of real-time AI component quality analysis technologies like Cybord’s RTI platform marks a significant step forward in the pursuit of higher quality and safety standards in electronic component manufacturing.
As the manufacturing industry continues to evolve, the integration of active, real-time visual AI analysis systems will become the new standard, driving a future where high-quality electronic components, streamlined production, and profitability are the norm rather than just an aspiration.
Autor: Asaf Jivilik Vice President of Marketing at Cybord.