SAG is technology leader in Rheocasting – a special casting process for aluminum in a semi-solid state. Rheocasting offers a total package of benefits for which VOLVO honored SAG with an innovation award.
Learn more about the advantages of lightweight components with SAG’s Rheocasting technology in an interview with Aaron Meierschitz, Head of Business & Operations Rheocasting, SAG New Technologies.
Could you provide us with some insights into Rheocasting?
With our Rheocasting process (a special casting technology) we are able to produce lightweight aluminum parts, which have the benefits of high pressure die casting parts but can offer some more important features. Caused by the high casting quality, it is feasible to replace components that were traditionally forged, while still meeting the mechanical strength requirements. Thanks to the good die filling and solidification properties, both thin-walled and thick-walled structures can be realized in one component. Together with the good mechanical properties, a considerable potential for lightweight construction can be realized. SAG has set the goal to refine the Rheocasting process and has been a pioneer in industrializing a unique approach to it for years. Since then, we have succeeded in producing high-quality components for large-scale automotive serial production. And the demand is continuously rising.
What are the advantages of components made by Rheocasting?
The net weight of vehicles, which tends to increase due to the design, can be significantly reduced by using weight-optimizing SAG rheocasting components. This fact leads to reduction fuel consumption and thus CO2 emissions. Rheocasting is in demand wherever components are exposed to highly dynamic loads and maximum weight reduction is to be achieved. With aluminium components made with Rheocasting technology SAG gives OEMs a clear advantage in sustainability and efficiency.
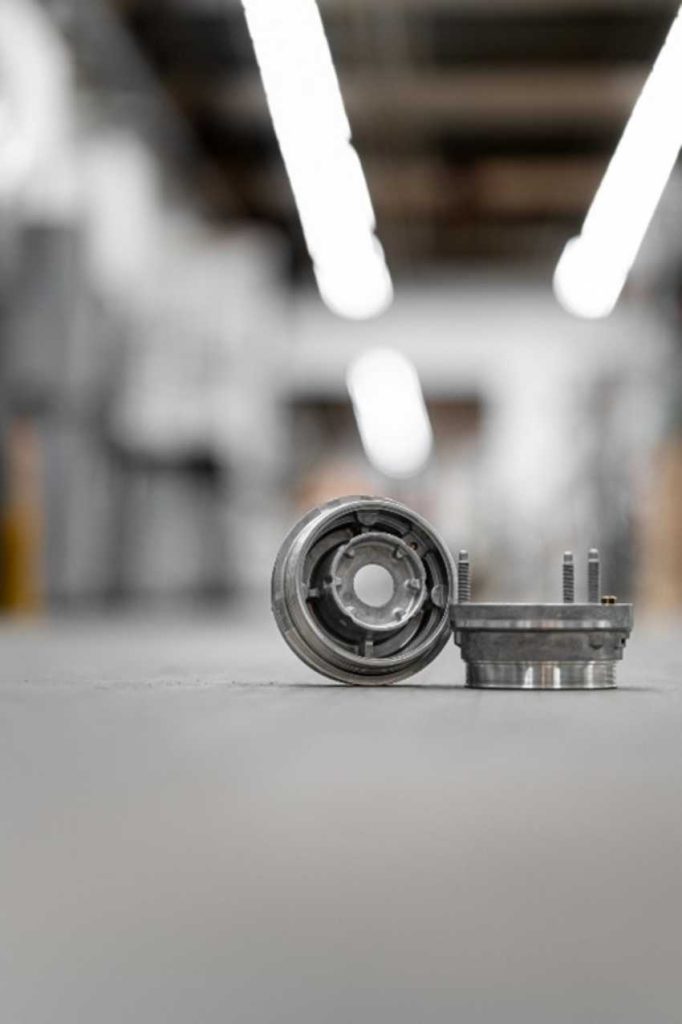
What is the difference between Rheocasting and conventional high pressure die casting?
Both Rheocasting and die casting utilize high-pressure die casting machines. However, Rheocasting necessitates an additional process step and equipment for material preparation. In the Rheocasting process, aluminum is manipulated in a semi-solid state, implying that some of the molten phases have already solidified into a globular shape. Consequently, the filling is executed in a laminar flow. This results in fewer defects in the part, extended tool life due to lower temperatures, and a highly dense part.
What are fields of applications of Rheocasting?
The areas of application are nearly limitless. Rheocasting offers several features that can be leveraged for various applications. For instance, Rheocasting parts can be welded to be helium tight, which is crucial for pressure vessels or components of a car’s air suspension system. Even without welding, the low porosity of Rheocasting parts proves beneficial for components like CO2 manifolds in cooling systems. Moreover, the superior casting quality of Rheocasting enhances the mechanical properties to such an extent that forged parts can be replaced. This allows mass reduction and near-net-shape design. SAG’s rheocasting lines are dedicated to large-scale production. Once a CAD design is available, our R&D team brings a product to series production readiness in short time. Seems that Rheocasting is a great technology with much potential.
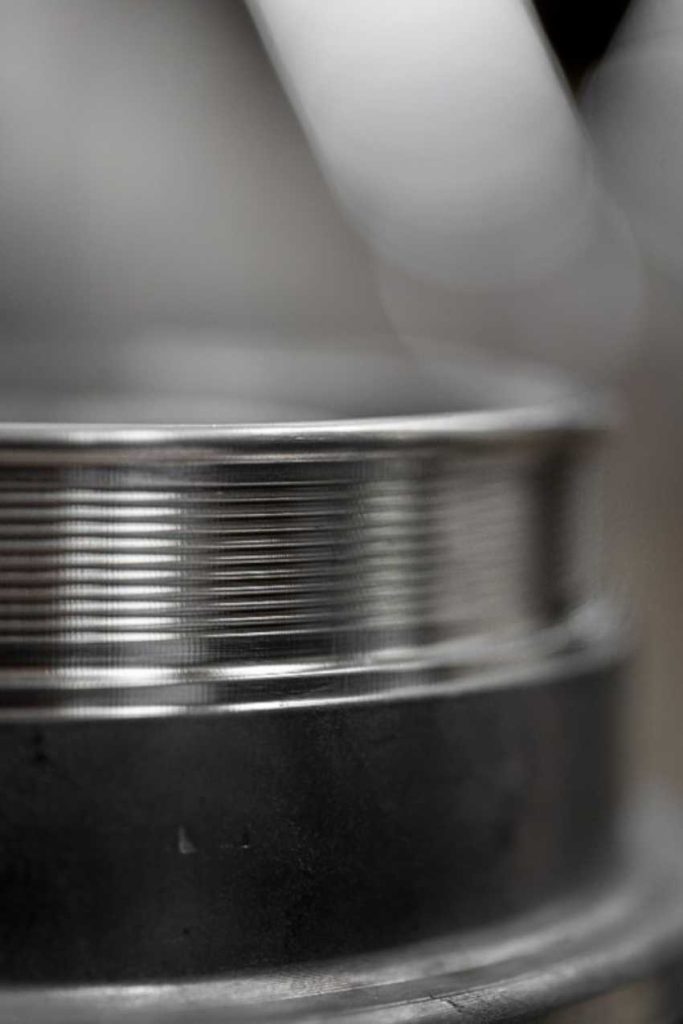
What is your conclusion?
Indeed, Rheocasting is a transformative technology with immense potential. Its ability to produce high-quality, lightweight parts and components cost-effectively makes it a game-changer in various industries. The process’s unique advantages, such as reduced energy consumption and CO2 emissions, further enhance its appeal. With the increasing demand for such innovative and sustainable solutions, Rheocasting is ready to play a significant role in shaping the future of manufacturing. The SAG Group, with its pioneering work in this field, is well-positioned to lead this change. In conclusion, Rheocasting represents a significant step forward in sustainability and efficiency.
Pictures Copyright: SAG New Technologies