TM Technology produces large-scale welded constructions in 3 main directions: marine sector, energy sector and heavy machine components.
Established in 2003, the factory has rich experience in the machine-building industry with continuous accumulation of knowledge, skills and new modern equipment.
Interview with Viktor Petrov – Commercial Director.
Can you describe your company’s approach to driving innovation in product development?
Viktor Petrov: For TM-Technology, innovation is covered with two key factors – creating a dedicated close team and investing in modern equipment. Both are very tough to do for very different reasons but both require resource devotion. In the world of machine building, they go hand by hand.
What recent products or solutions have you introduced, and how are they shaping the industry?
Viktor Petrov: Our solutions stem from our focus on communicating with clients to adapt their large-scale parts to real-world production. This happens with open collaboration and high-class machinery aimed at strategic processes. In TM-Technology’s case, these are cutting, bending, coating and machining.
The most recent investment we made was in a coating line with four chambers each with dimensions 24 x 5.5 x 5.5 meters. The chambers are arranged as follows: shot blasting, phosphating and degreasing, drying, combined painting and drying. The newest investment we made is a Gantry type machine VERXA MW175 with an X axis of 17.5 meters and accuracy of 4-15 microns per meter.
What technologies or trends are influencing your latest innovations, and how do they benefit your customers?
Viktor Petrov: We influenced not just by global trends per se but by the trend of customer requests. We found it is very tough to find a subcontractor to do proper coating and proper machining of large welded parts. I am referring to components for the Marine, Energy or overall machine building industries. They require parts weighing up to 60 tons that need to be processed, which is highly complex. You need people with experience and knowledge and a well-equipped facility. There can be no compromise in either.
How do you ensure your innovations meet both current market needs and long-term industry evolution?
Viktor Petrov: Main ways to get an idea of market demand is a transparent discussion with our current clients. In most cases they have a very strong idea where they want to go long-term with us as a supplier. There are the rare occasions when somebody is willing to adapt their supply chain to our standards because they see additional benefits this way.
Another way we stay in touch with current events and trends is going to exhibitions associated with the industries we work with. There we understand the attendees’ needs, we feel the pulse of the market – what are the trends, what is the “next big thing” and trying to filter out distractions and focus on what is feasible and actually important. The goal here is to prioritise our direction our investment of resources in order to ensure feasibility of our growth.
What challenges did you face while developing your latest products, and how did you overcome them?
Viktor Petrov: TM-Technology’s “product” is the subcontracting service we provide for well-known industry leaders who have given us the trust to handle important heavy-duty parts for their most valuable projects.
Although we would not prefer making it a habit, we have had instances when we would receive a very substantial project with very limited lead-time and unfinished working documentation. On top of that, the projects were for parts between 40 and 60 tons that had to go to another continent on a specific date. We managed to finish the project on time while simultaneously pointing out some mistakes in the documentation that would not have allowed us to proceed if not corrected.
This was a pinnacle of professionalism and openness while working under pressure.
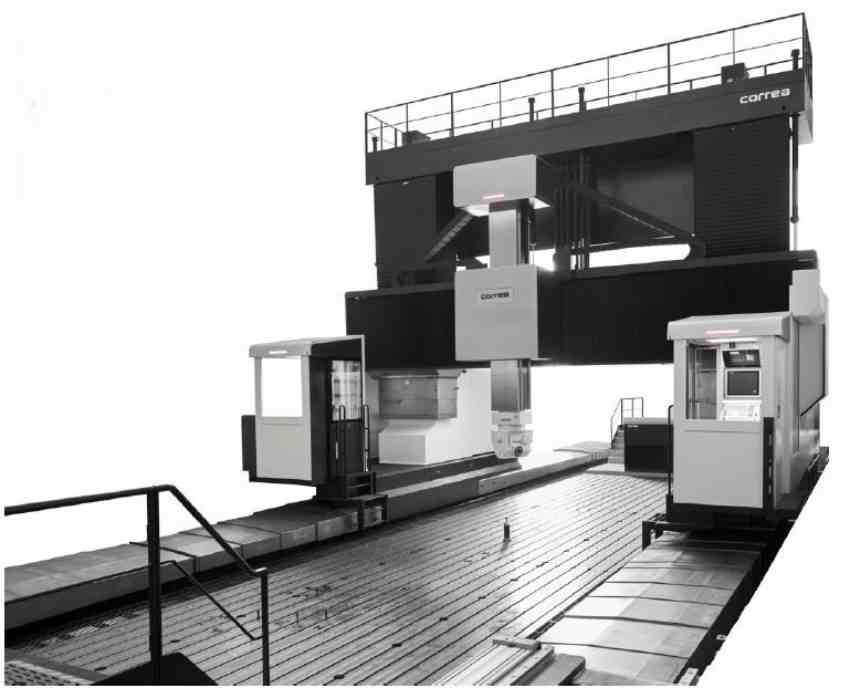
How do your latest products differentiate you from competitors in the market?
Viktor Petrov: I have been told more than once by different partners that TM-Technology is very transparent in communication and open about potential challenges that need to be overcome for each project. Our approach to problem solving has saved time and resources for our partners and they seem to appreciate it. I believe in a way we have positively contributed to the reputation of our partners who are world-renowned within their respective industry be it marine, energy or otherwise.
Can you share any feedback or success stories from customers who have adopted your new innovations?
Viktor Petrov: Due to confidentiality agreements, I cannot specify names but notable US, German and Swedish conglomerates have taken advantage of our advanced coating line and are very eager to expand our cooperation concerning machining due to our new equipment set for August-September of this year.
How is sustainability integrated into your product development strategy?
Viktor Petrov: We have implemented significant measures to ensure that our operations do not have a negative impact on the environment. For example, the coating line alone required an additional investment of €200,000 by TM Technology to meet stringent health, safety, and ecological standards. I am confident that these efforts position us well to meet—and even exceed—ecological industry requirements for many years to come.
What emerging trends or technologies do you think will drive the next wave of innovation in your industry?
Viktor Petrov: Over the past few years, I have observed two significant trends shaping the industry. Firstly, there is a clear shift towards automation—robots are increasingly being used to replace manual labour and reduce individual decision-making. As a result, fewer people are involved in controlling certain processes, and the industry as a whole is becoming increasingly automated.
The second trend is the noticeable increase in foreign workers joining companies in Eastern Europe, which is a relatively new development for this region. It remains to be seen whether this change will be permanent or just a temporary phenomenon.
In any case, automation technologies such as robotic welding, machining, lifting, thermal cutting, and so on, are becoming increasingly advanced and interactive. Initially, new technologies are introduced that are much easier to use. The next step involves different pieces of equipment providing real-time status updates on the location of each part from every order throughout the production cycle. This is undoubtedly the direction in which the industry is heading. Although widespread adoption will take time and will not happen overnight, gradual progress is being made. We have already begun to take small steps towards automation, but this requires significant investment, time, energy, and perhaps a shift in mentality regarding traditional work processes.