The automotive industry, in particular, has been experiencing a significant transformation in recent years with the integration of advanced technologies to enhance production processes and improve overall efficiency.
Artificial Intelligence (AI) can be a powerful tool within this sector, revolutionizing manufacturing operations and test systems. By harnessing the capabilities of AI, automotive manufacturers can optimize production, increase productivity, and ensure higher quality standards.
There are, however, challenges associated with data acquisition and the implementation of AI systems within this industry. By understanding these challenges and exploring potential solutions, manufacturers can effectively leverage AI technology to achieve competitive advantages and drive innovation.
Key Takeaways
- Automotive industry is adopting AI to optimize production, increase productivity, and ensure quality standards.
- AI benefits include: predictive maintenance, quality control, efficient testing, demand forecasting.
- Challenges: complex data collection, privacy/security issues, infrastructure demands, skill gaps.
- Solutions: IoT integration, data partnerships, data augmentation, PoC testing, continuous monitoring.
- Controlar’s contributions: QIO2 IoT platform, display & piston ring inspection through machine vision & AI.
- Results: improved production, precise testing, cost reduction.
Benefits of AI Implementation in Automotive Manufacturing
One of the promising applications of AI in manufacturing is predictive maintenance. By analyzing sensor data, AI algorithms can identify potential equipment failures before they occur. This proactive approach can help to prevent unplanned downtime, reduce maintenance costs, and improve operational efficiency.
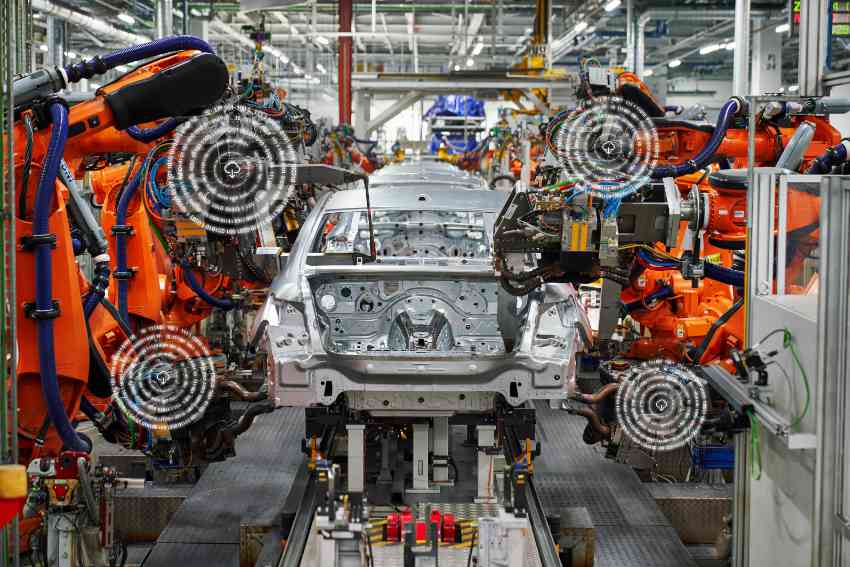
BMW uses AI to predict when its manufacturing equipment is likely to fail. This allows the company to schedule preventive maintenance before the equipment breaks down, saving millions of euros each year.
Another application of AI in the automotive industry is quality control. AI-driven systems can analyze vast amounts of data from various sources and, by comparing it to predefined quality standards, they can identify defects and irregularities in manufacturing processes and products, reducing the likelihood of faulty products and ensuring consistent product quality.
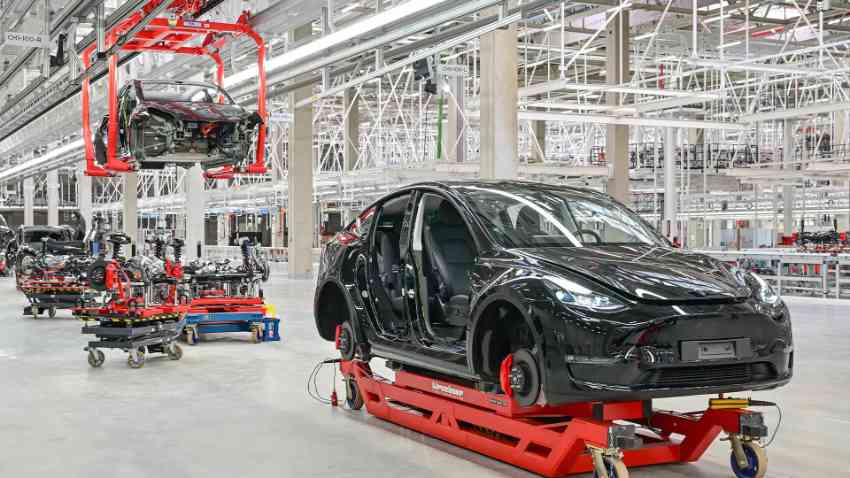
Tesla uses AI to inspect its vehicles for defects. This has helped Tesla to reduce the number of defects in its vehicles, improving customer satisfaction.
In addition to predictive maintenance and quality control, AI is also being used to improve the efficiency of automotive test systems by automating data analysis and identifying potential issues and anomalies. This automation process significantly reduces manual efforts, enhances testing speed, and ensures a more thorough evaluation of product performance.
AI systems can also use machine learning to analyze historical data and identify patterns that can be used to predict future demand. This can help to improve demand forecasting and reduce inventory by 30 to 50 percent, ultimately saving costs by eliminating the transport, storage, and supply-chain management of unneeded goods.
By preventing unplanned downtime, reducing maintenance costs, improving quality control, and automating test systems, AI can help automotive manufacturers to improve efficiency, profitability, and customer satisfaction.
What are the Challenges of AI Integration in the Automotive industry?
The successful implementation of AI systems in the industry relies of several factors such as: data collection; regulatory and security challenges; ethical and privacy concerns; other technical considerations.
1. Data Sources and Collection
Acquiring the necessary data for AI applications poses several challenges. The automotive industry generates a vast amount of data from various sources, including sensors, production machines, quality control systems, and customer feedback. Gathering and integrating this data can be complex due to factors such as data fragmentation, heterogeneity, quality, and data silos.
DATA FRAGMENTATION
Fragmentation refers to the scattered nature of data across different systems and departments within an organization. Manufacturing processes generate data at various stages, from raw material procurement to assembly and testing. Consolidating and integrating this fragmented data is crucial to gain a holistic view of the production process and enable effective AI-driven decision-making.
DATA HETEROGENEITY
Data from different sources may have varying formats, structures, and levels of granularity. This heterogeneity complicates the data integration process, requiring significant effort to standardize and harmonize the data to make it compatible for AI analysis.
DATA QUALITY
For data to be used in these systems, there is the need for it to be accurate, complete, and consistent. Data quality is a crucial step to ensure that decisions are made based on accurate information, helping to improve the efficiency of operations.
DATA SILOS
Data silos are isolated repositories of data that exist within different departments or systems, hindering the seamless flow of information. Breaking down these silos and creating a unified data ecosystem is essential for harnessing the full potential of AI. However, achieving data interoperability and integration across departments and systems can be a complex task.
2. Data Privacy and Security
The automotive industry deals with sensitive and confidential data, including intellectual property, trade secrets, customer information, and compliance-related data.
Manufacturers must adopt comprehensive data governance frameworks and establish clear policies and protocols to ensure data privacy and security throughout the AI implementation process.
DATA PRIVACY
Regulations, such as the General Data Protection Regulation (GDPR), impose strict requirements on the collection, storage, and processing of personal data. Manufacturers must comply with these regulations and implement robust data protection measures to safeguard personal and sensitive information of the systems that will be integrated in the vehicles.
DATA SECURITY
This is another critical aspect, as automotive manufacturing systems are vulnerable to cyber threats and attacks. AI systems depend on large volumes of data, and any compromise in data integrity or security can have severe consequences. Implementing robust cybersecurity measures, including encryption, access controls, and regular vulnerability assessments, is essential to protect data from unauthorized access and ensure the integrity of AI-driven manufacturing systems.
3. Infraestructure and Resource Requirements
Implementing AI systems in the automotive manufacturing industry requires robust infrastructure and resource capabilities. The scale and complexity of data processing, machine learning algorithms, and real-time analytics demand high-performance computing, storage, and networking capabilities.
DATA STORAGE
To handle large volumes of data, manufacturers need to invest in scalable and high-capacity storage solutions, including both on-premises and cloud-based storage options. This will ensure that data is accessible, secure, and readily available for AI applications. Additionally, high-performance computing infrastructure is required to process and analyze the vast amounts of data efficiently.
Networking Infraestructure
AI systems often rely on real-time data streaming and communication between various manufacturing processes, sensors, and systems. Robust and low-latency networking capabilities are necessary to facilitate seamless data flow and enable timely decision-making.
4. Workforce Skill Development
Integrating AI technologies into the automotive manufacturing industry necessitates a skilled workforce capable of leveraging these advanced tools effectively. However, there is often a skills and knowledge gap when it comes to AI implementation.
Manufacturers need to prioritize workforce skill development initiatives to bridge this gap. Collaboration between data scientists, engineers, and domain experts is crucial for successful AI implementation. Encouraging cross-functional teamwork and fostering a culture of continuous learning and innovation can create an environment conducive to effective AI adoption.
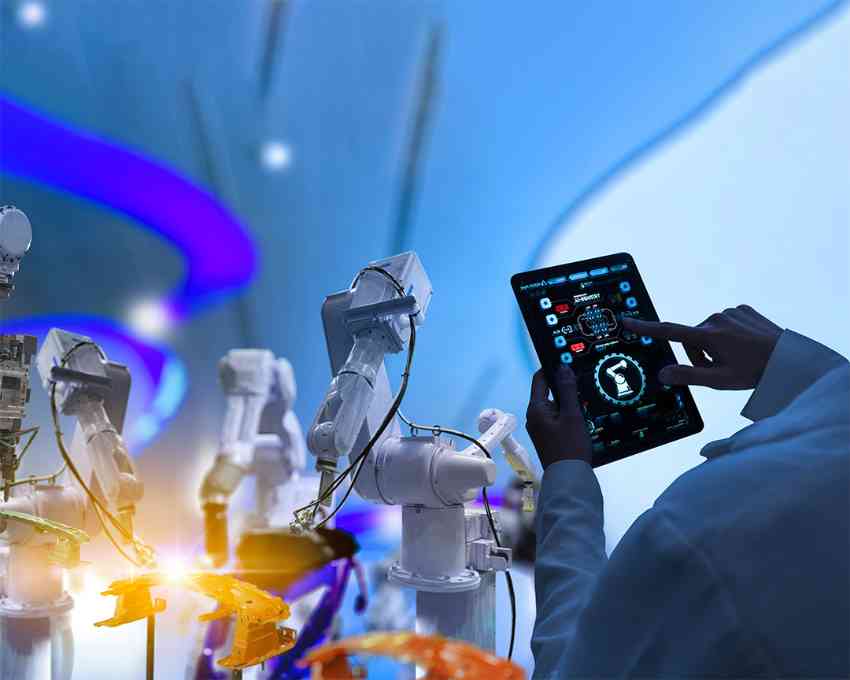
How to Overcome the Challenges of Data Acquisition for AI Integration?
To overcome some of the challenges previously presented, several strategies and best practices could be used:
1. IoT Integration
Leveraging Internet of Things (IoT) devices and sensors can facilitate real-time data collection and monitoring. By embedding sensors in manufacturing equipment, and production lines, manufacturers can capture valuable data throughout the production process, enabling better decision-making and process optimization.
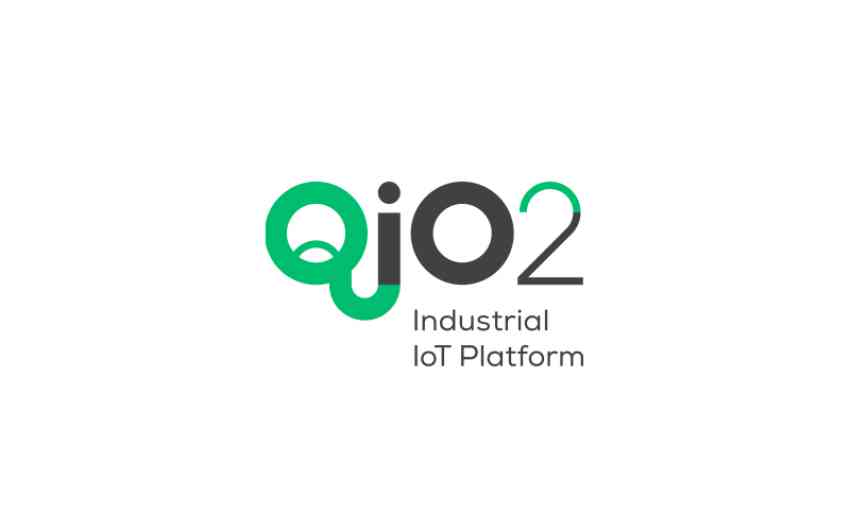
2. Data Partnerships
Collaborating with suppliers, customers, and other stakeholders in the automotive value chain can help establish data partnerships. Sharing data with trusted partners can provide access to additional data sources, enhance data quality, and facilitate a more comprehensive analysis of the manufacturing processes.
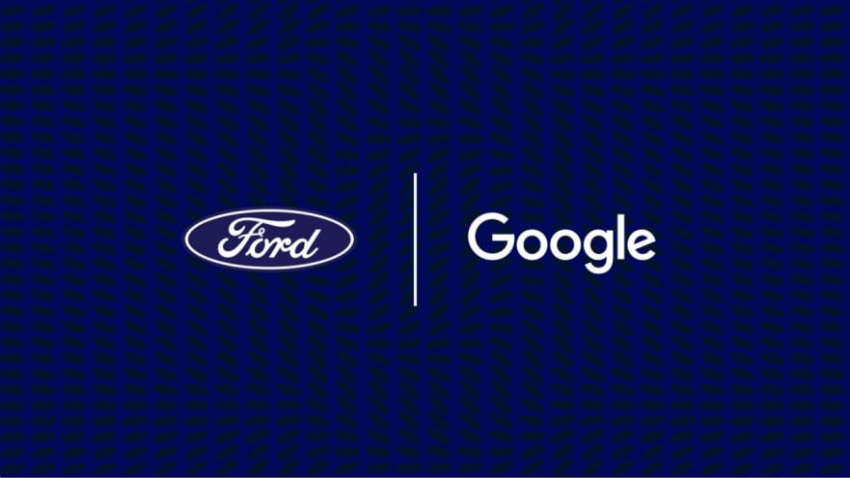
In 2021, Ford and Google announced a partnership to develop a new generation of connected cars. The partnership will give Ford access to Google’s AI technology to create new features and services for its vehicles.sensors, actuators, and gateways.
3. Data Augmentation
In cases where data volume or quality is insufficient, manufacturers can employ data augmentation techniques. This involves generating synthetic data or enriching existing data through techniques like data interpolation, extrapolation, or simulation. Augmented data can help overcome limitations and enhance the effectiveness of AI systems.
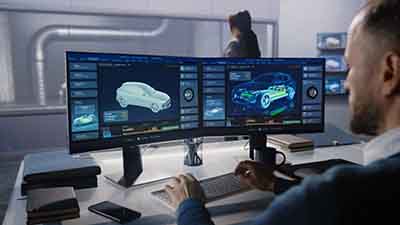
By using synthetic data to train AI models to identify potential problems with the production line, manufacturers can prevent problems before they occur, improving the efficiency of the production process.
4. Proof of Concept (PoC)
Conducting a PoC before full-scale implementation can help assess the feasibility and performance of AI systems. A PoC allows manufacturers to test different AI algorithms, evaluate their impact on production processes, and identify any technical or operational challenges early on.
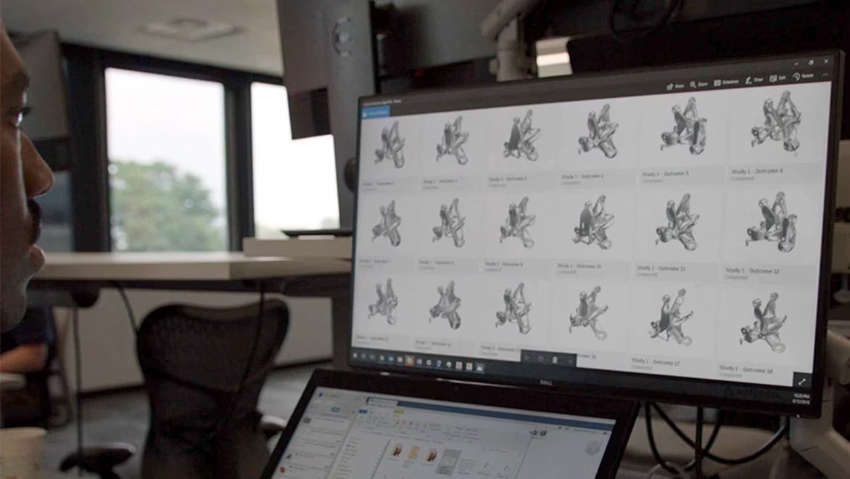
GM uses AI-based generative design to develop PoC for new car parts that are lighter and stronger than the original parts. This will help improve the fuel efficiency and safety standards of GM vehicles.
5. Continuous Monitoring and Evaluation
Implementing AI systems is an ongoing process that requires continuous monitoring and evaluation. Establishing performance metrics, conducting regular assessments, and leveraging feedback from users and stakeholders can help identify areas for improvement, optimize system performance, and drive continuous innovation.
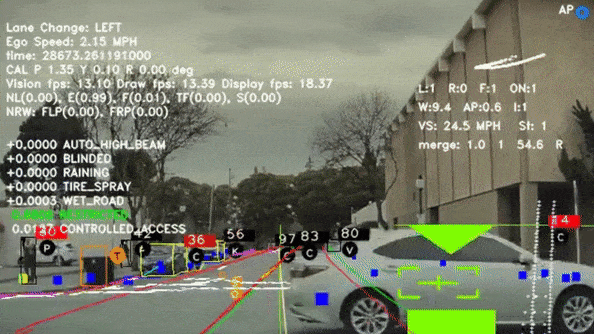
Tesla’s Autopilot uses AI to self-navigate and avoid obstacles. After monitoring its performance, engineers found that these systems were underperforming in routes with unexpected obstacles. Tesla was then able tomake changes, improving its performance.
How Controlar Helps Manufacturers Overcome the Challenges of AI
- IoT Integration Platform
Controlar has developed QIO2, an IoT device management platform for industrial monitoring applications that uses LoRaWAN® and Wi-Fi communication to increase the coverage of the factory floor.
This is a highly scalable solution, allowing the simultaneous use of a high number and variety of sensors, actuators, and gateways.
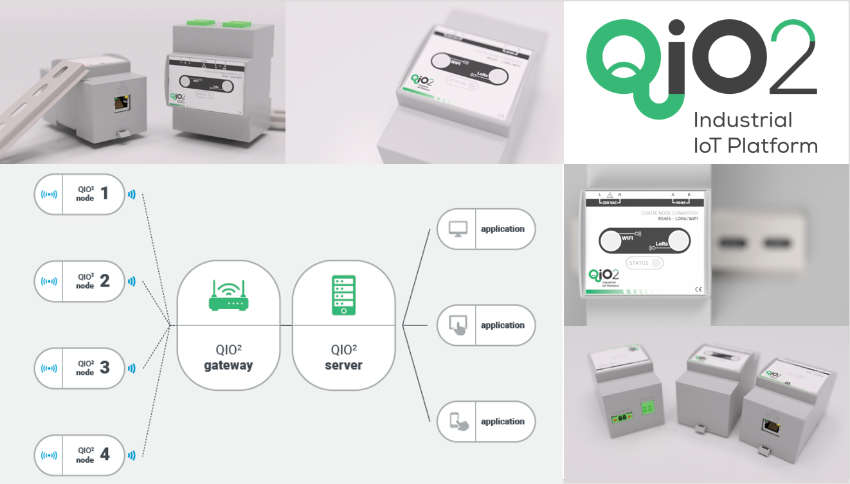
QIO2 can be used with a Cloud-based or on-premises. All the retrieved data is then centralized and can be analyzed with different dashboards in which alerts can be set for certain variables.
Controlar IoT management platform keeps all the information secured with the implementation of encryption modules in the communication layers and database. This solution has great potential for a large number of industries, when it comes to be a part of the AI revolution.
- Quality Inspection and Defect Detection with AI
Controlar is comitted to use AI in several innovative systems that has been developing recently.
Controlar has partnered with Visteon and Fraunhofer Portugal to develop an innovative machine for automotive display inspection, using machine vision and artificial intelligence.
This project aims to develop a machine that can automatically inspect and detect any defects or anomalies in automotive displays, which are an integral part of modern cars. The machine will use high resolution vision systems to capture images of the display, and artificial intelligence algorithms will then analyze these images to identify any defects.
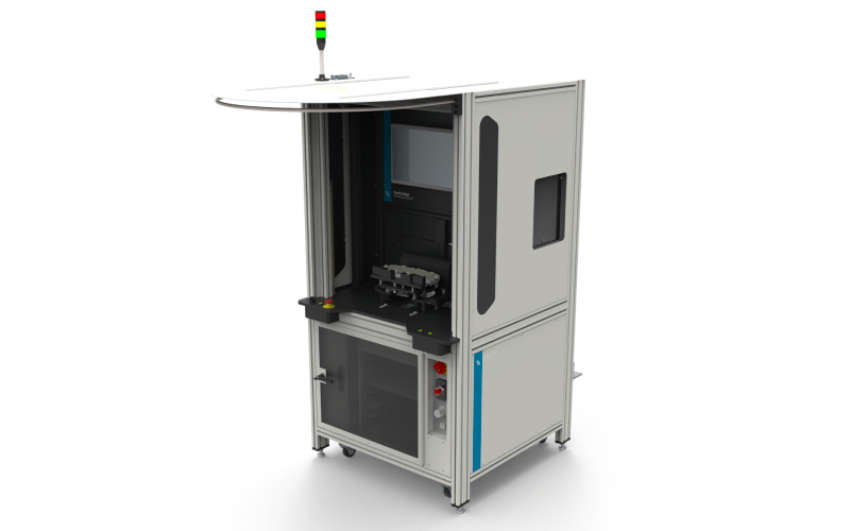
The partnership between Controlar, Visteon and Fraunhofer Portugal brings together the expertise of three leading entities in the fields of automotive electronics, machine vision, and artificial intelligence. This collaboration is expected to result in a machine that will set new standards for automotive display inspection and improve the quality and safety of modern cars.
Controlar, together with MAHLE and CCG, has been developing a machine to automatically detect defects on piston rings, in order to fully automatize the test of these crucial products of vehicles.
This machine has the capability to deal with piston rings with different dimensions, and to detect their defects in real-time, in order to improve production efficiency, and increase the quality of the product. It includes AI algorithms, that together with high-resolution cameras, are able to fulfill the objectives of the project.
Conclusion
The integration of artificial intelligence (AI) in automotive manufacturing has brought about significant advancements in production optimization and test systems. With AI-powered algorithms, test systems can automate processes, detect defects, and perform virtual testing, resulting in faster and more accurate evaluations of product performance.
However, there are some challenges with using AI in automotive manufacturing. Data acquisition poses difficulties such as data fragmentation, heterogeneity, and data silos, which require effective strategies like IoT integration, data partnerships, and data augmentation. Additionally, ensuring data privacy and security is crucial to protect sensitive information and comply with regulations.
Nevertheless, the advancements in AI-based test systems have proven to be invaluable for the automotive industry, allowing manufacturers to achieve higher testing accuracy, greater efficiency, improved product quality and reliability, all of which resulting in reduced costs for manufacturers.
Author: Pedro Vieira | PhD in Biomedical Engineering | R&D + I Project Manager