The Matelex solution enables centralized and connected monitoring of refrigeration installations. These installations contain refrigerants, some of which have a global warming potential 3900 times greater than CO2. Without continuous monitoring, these installations leak and release greenhouse gases into the atmosphere. Highly energy consuming, they consume even more energy when under load and therefore require continuous monitoring.
Reducing the environmental impact of the installations is all the more important as there is a shortage of manpower in the market. Refrigeration installers and maintainers are therefore confronted with aging installations, with no precise information on their actual operation, which offers few prospects for improvement. Faced with these challenges and a growing demand for refrigeration, the Matelex solution makes it possible to combine improved performance and reduced environmental impact.
Innovative feature 1: indirect intelligent leak detection
The indirect leak detection system is based on a learning system of the refrigeration plant operation. Indeed, unlike direct leak detection such as portable detectors, the Matelex intelligent level detector will continuously perform physical measurements (pressure, temperature and level in the HP liquid cylinder).
Following its installation, a learning period will allow the system to determine the normal operation of the installation. Then the detection algorithm will work continuously to determine if the variations in measurements are normal or if they are due to a decrease in the quantity of refrigerant in the installation and therefore to a leak.
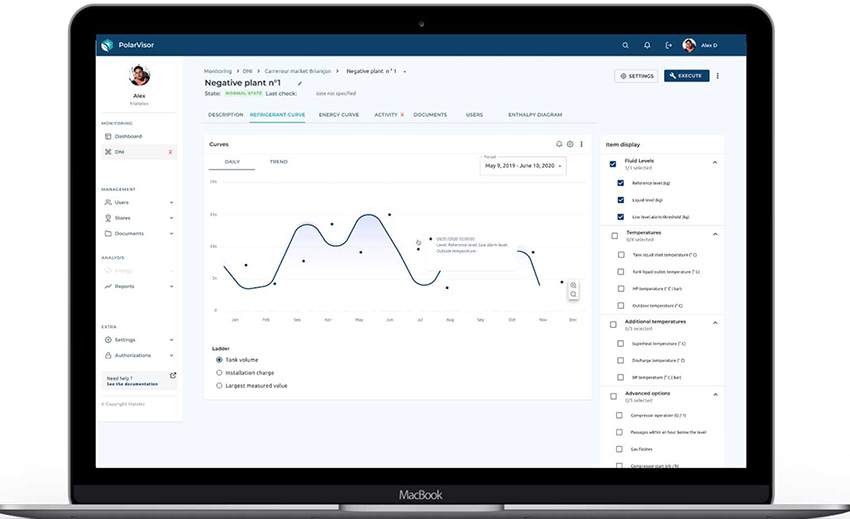
Thus, contrary to a classic leak detection, which will seek to detect the presence of refrigerant molecule in the immediate environment of the sensor, the detection by indirect method seeks to know permanently the quantity of fluid in the whole installation. It is a continuous monitoring allowing to identify and alert as soon as a leak occurs, but also to have the certainty that no leak remains.
Connected to a supervision platform, the leak detection system alerts and estimates the quantities of fluids lost. The objective is to gain in reactivity, to avoid discharges into the atmosphere and a break in the cold chain due to the shutdown of the refrigeration plant.
Innovative feature 2: real time energy monitoring
If a leaking and underloaded installation jeopardizes the proper functioning of the system and therefore the cold chain, it also leads to over energy consumption.
Refrigeration plants, which are essential for the preservation of foodstuffs but also of certain medicines and vaccines, are high energy consumers. For a standard food supermarket, refrigeration represents 50% of the overall energy consumption. It is therefore essential to optimize their operation to ensure an optimized cold production.
The energy monitoring of the refrigeration plant consists in measuring the current flowing through each electric motor of the plant (compressors, condensers, pump…). The objective is to report the precise operating rate of the motors, especially the compressors, in order to be able to analyze them later.
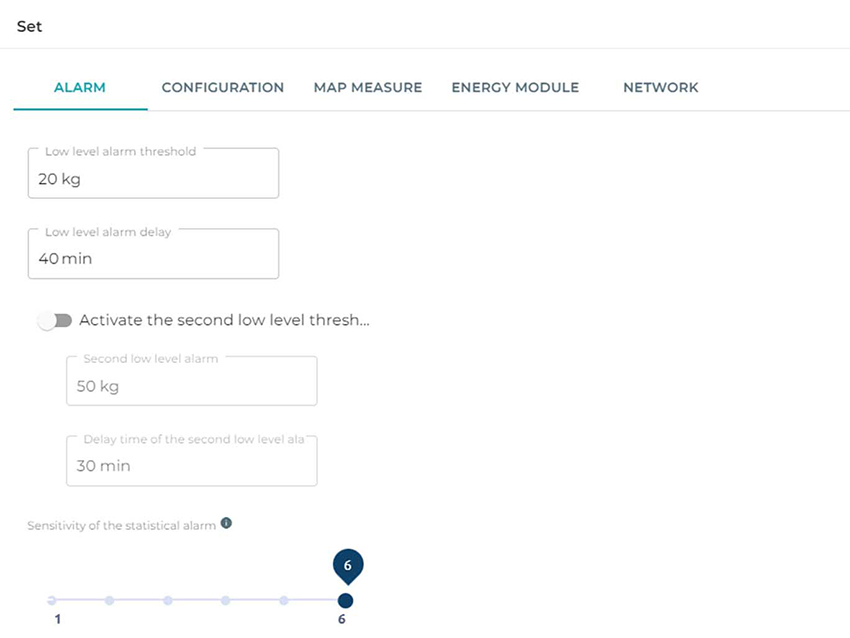
An analysis of the voltage supplying the motors is also made in order to monitor suspicious behavior on the electrical networks that could damage the equipment (voltage jumps or drops).
The solution can therefore cumulate the power of all the motors and thus compare the energy consumption over time. The most innovative part of this system consists in comparing the consumptions between periods while adding other dimensions of comparison like pressures or temperatures. Thus, it is possible to alert the operator that a plant consumes for similar needs.
Contrary to a classic analysis of the consumption of the cooling unit via the general electricity meter, the Matelex energy module allows for a detailed analysis of the electricity consumption and any possible deviations in consumption.
Innovative feature 3: performance improvement advice
Thanks to all the measurements and information collected, the solution is able to reproduce in real time the enthalpic diagram of the plant. This diagram allows to trace the behavior of the fluid in the installation and represents a precious help for the operators wishing to analyze the functioning of the installation and to improve its performances.
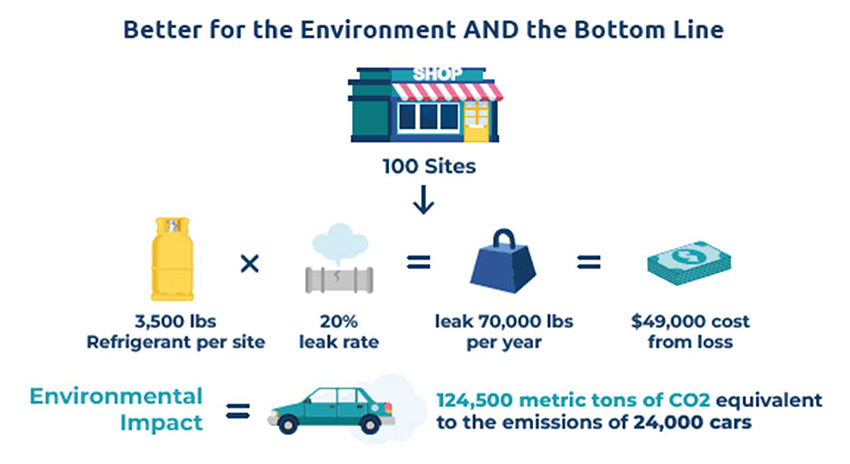
It is also possible for refrigeration operators to take advantage of automatic advice for performance improvement. Thus, the innovation for maintenance lies in a series of advice at the scale of the park according to 3 axes:
Improvement of energy performance. Thanks to the continuous calculation of the coefficient of performance, it is possible for the solution to identify areas for improvement in order to reduce the plant’s energy consumption.
Reducing the risk of compressor failure. According to compressor rebuilding companies, 80% of compressor failures are due to external events (excessive overheating, liquid hammer, etc.). Certain alerts on the settings can therefore prevent these incidents.
Improving the installation of the device in order to increase the accuracy of the analysis. A poorly installed device will not send reliable data, a series of tips indicate how to improve the installation.
Innovative feature 3: web app for centralized remote management
All the measures taken on the installations are analyzed and restituted on a web application of follow-up, one finds there:
- The analyzed data is returned in the form of indicators such as alerts in case of leakage, energy drift or risk of compressor failure.
- The operating data displayed on level curves such as pressures, liquid temperature at the tank inlet, superheat temperature, discharge temperature, etc.
The analyzed data are available on a global dashboard allowing to follow all the refrigeration installations via a single web application. This makes it possible to quickly identify the priority interventions to be carried out, to avoid useless displacements, and to ensure permanently the good functioning of the installations.
KEY indicators:
79% in refrigerant savings compared to traditional leak detection (French independent study