Belt Technologies, Inc. has been producing custom metal belt conveyor solutions for new and existing conveyor systems for more than five decades at its plant in Massachusetts, USA. Belt Technologies Europe has been serving the European and Asian markets on its parent behalf for over 25 years. Sophisticated engineering, advanced manufacturing processes and an unlimited variety of configurations and coatings are available to custom-design belts to suit any application. Stainless steel belts, timing belts, and metal drive tapes are superior, high-quality options for automated production and robotic facilities. To learn more about Belt Technologies and metal conveyor belts, visit belttechnologies.com.
The world is going green with various methods to lower harmful emissions, and industries across the board are making the necessary changes to keep up. Belt Technologies, Inc., is providing a crucial service for vehicle battery manufacturers as their demands shift from lead acid to electric. Next generation batteries are seen as an enabling technology which will help decarbonize our economies and slow down climate change. The challenge is transforming the automotive sector, and western economies are under pressure to make rapid progress to catch up with market leaders in China and Korea. To win this race, new and revolutionary battery production methods are a necessity.
Bloomberg forecasts that EV cars will be less expensive to produce than conventional fossil-fuel powered vehicles by 2027, with this parity being seen as a big milestone and driver for a higher demand for EV batteries. The falling cost of battery production is critical—and metal belts are certainly playing an important part in creating efficiencies.
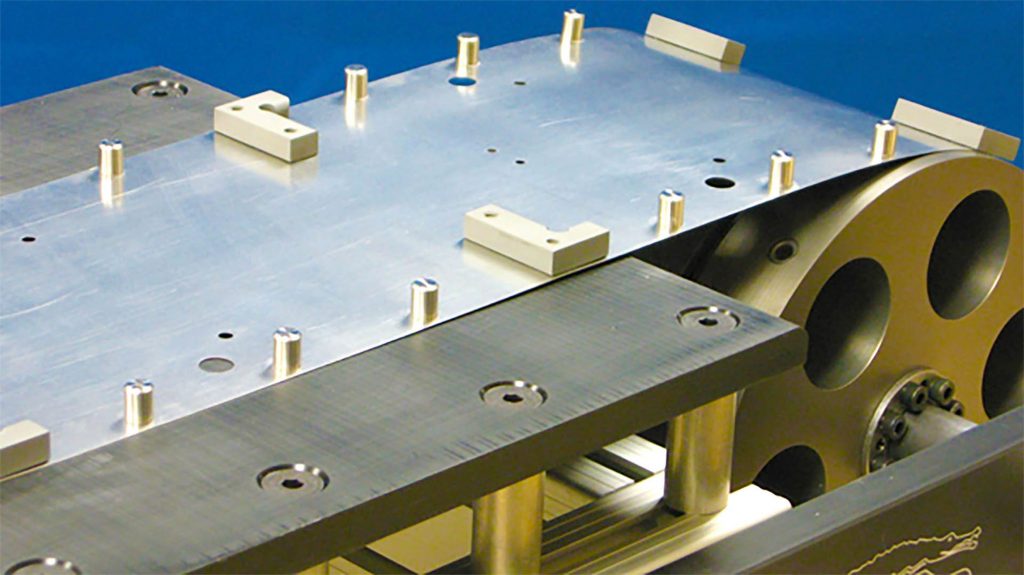
Manufacturers are striving for battery solutions to double battery energy density while decreasing charging times by 50 percent or more. As such, they require unique and sophisticated production technologies. Steel belts are a critical part of the development process, particularly in processes that involve building and stacking of small components; these are facilitated by a metal belt’s repeatability of motion of less than 0.127 mm and tolerances of +/- 0.025 mm.
In Europe, there are currently five major Gigafactories producing these sophisticated batteries and this number is forecasted to increase to more than 11 by 2030, driven by an expected demand for over 300 gigawatt hours of cells by the decade end. In some countries like the UK, there will be a ban on new petrol and diesel cars starting in 2030.
Stainless steel belt technology is certain to help build better batteries. The unique properties and benefits of stainless steel have long made metal belts ideal for automated battery production equipment. Battery components must be transported smoothly and reliably through several production stages, including pasting, filling, assembly, cleaning and pin engraving. Unlike rubber or neoprene alternatives, metal belts provide positional accuracy, smooth motion control and most importantly, chemical resistance. Efficient battery function is after all driven by a complex mix of several chemicals. Belt Technologies can offer machine builders distinctive solutions to their often demanding design needs, with combinations of hole perforations, attachments and coatings allowing them to tailor belt performance exactly to the challenges faced in each application.
For the automotive industry in North America, the shift is about to pick up speed—multiple states, including Massachusetts and California, have already implemented plans to solely produce electric vehicles by 2035. Manufacturers are now working double duty to meet the demands for traditional and electric customers, and Belt Technologies is providing the reliability they desire.
“One of our clients is producing approximately 250,000 batteries per shift—you can imagine the wear and tear that would cause on a traditional belt,” said Denis Gagnon, Belt Technologies CEO. “This same client is seeing a dramatic shift in demand for electric batteries and is able to match that demand with a metal belt conveyor system. Many facilities are in a position which will soon require major production changes, and we can help provide them. We don’t offer one-size-fits-all solutions: our engineering team is known for its versatility, designing and building custom solutions for any existing system our clients can provide.”
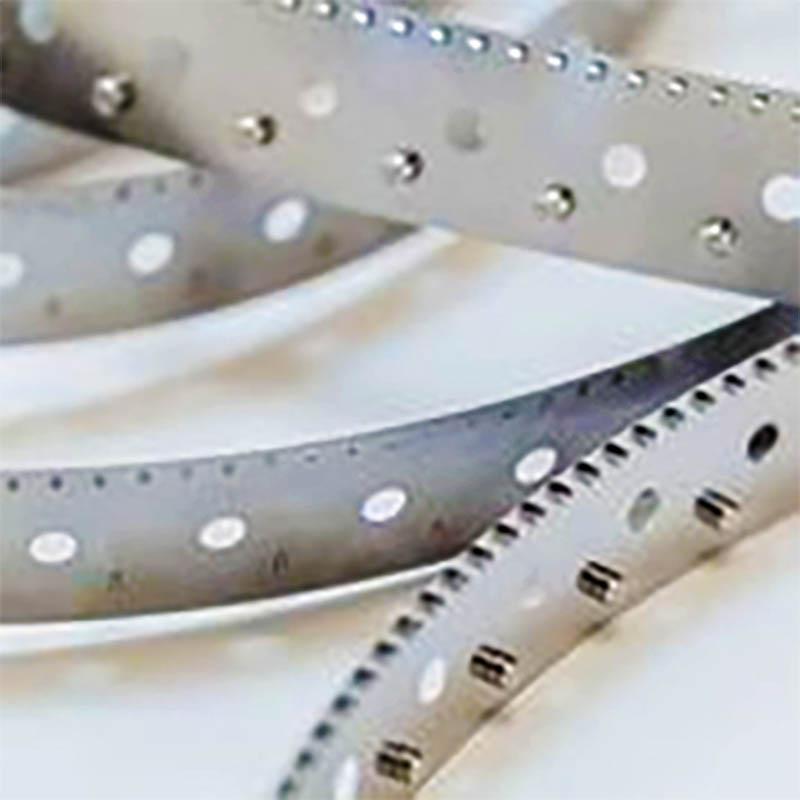
For decades, battery manufacturers have trusted stainless steel belts to operate in clean-room environments and resist chemical corrosion for a more reliable, longer-lasting conveyor system. Belt Technologies President Alan Wosky does not expect that to change any time soon.
“Stainless steel has always been the gold standard for lead acid, lithium-ion and nickel batteries,” explained Wosky. “Belt was and continues to aid in traditional battery production, but as the world now moves in a new direction, it’s exciting that we’re able to remain a part of this new process for electric vehicle batteries as well.”
In addition to the battery industry, Belt Technologies’ metal belts and conveyor systems are used in 3D printing, robotics, medical manufacturing, food production and much more. For more information about Belt Technologies, visit belttechnologies.com.