Civan Lasers develops and manufactures lasers for material processing applications such as welding, drilling, cutting and metal additive manufacturing. As of today, Civan employs 180 people in Jerusalem, Israel.
The team of innovators at Civan Lasers have dedicated the past decade to developing new laser technology for use across industries. Their Dynamic Beam Laser system allows manufacturers to control beam shape, frequency, sequence and focus steering to improve quality and speed. Through their advanced capabilities, Dynamic Beam Lasers open the door to countless new applications for materials processing.
Easy Engineering: A brief description of the project / projects.
CIVAN LASERS: Valeo, one of the world’s largest Tier 1 suppliers, wanted to improve its battery cooler manufacturing process in order to manufacture larger battery coolers due to the demand to increase EV’s travel range. They were manufacturing with brazing, but looking for a better, more cost effective alternative.
Using Civan’s Dynamic Beam Laser with its unique ability to control beam shape and frequency, Valeo was able to quickly test different beam shapes and frequencies to define the optimal process for a high quality leakproof weld. AIMEN participated in the process development and supporting analysis of the testing, which took place in Civan’s application lab. This proof of concept was presented at the recent EALA conference in May 2021.
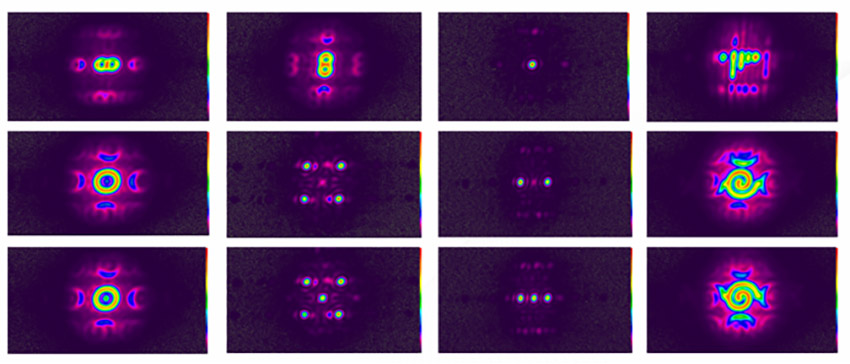
E.E: What were the needs of the client?
CIVAN LASERS: Valeo provides its customers with a full range of auto parts, from individual components like HVAC units and front-end modules to full smart systems including global thermal comfort systems and intelligent battery solutions.
In an effort to reduce their carbon footprint and be more competitive, Valeo set out on a mission to change the way they build their battery coolers. They had been using the popular method of brazing in order to join the parts, but wanted to replace this method with laser welding which is both more environmentally friendly and more cost effective. At the same time, Valeo wanted to ensure that they could create a strong weld with no leakage so as not to compromise on the quality of the product.
E.E: Why did the client choose your products / solutions?
CIVAN LASERS: Before choosing Civan’s Dynamic Beam Lasers, the Valeo team tested leading market solutions using laser beam wobble, but they were not able to achieve the desired quality at the high feed rates required for manufacturing.
Following this, Valeo tested Civan’s Dynamic Beam Lasers and achieved satisfactory high quality welding results at 15m/min. Civan’s platform allowed engineers to conduct a multitude of tests in a short period of time and instantly see results. By changing one condition at a time, they were able to identify the ideal shape, frequency, and feed rate for the strongest weld with minimal spatter and porosity.
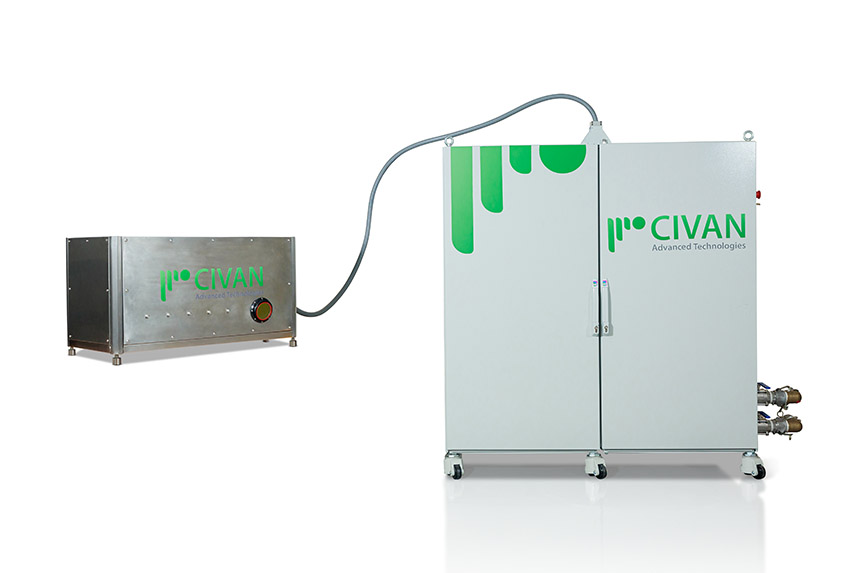
E.E: Please describe how was the project implemented?
CIVAN LASERS: After determining that an hourglass beam shape was optimal, the next step was to optimize the shape frequency to achieve minimum spatter. While state of the art scanners can reach 5khz, Valeo tested the Dynamic Beam Lasers in a range of 10kHz to 300kHz and revealed the optimal weld to be at 150kHz – a speed at which there was almost no spatter. Next, they adjusted the feed rate from 12 m/min to 15 m/min. The result of this test was a similar seam weld width regardless of the feed rate. Once all of the tests were complete and the optimal settings were determined, the final step was to conduct a leak test and make sure that all of the joints were tight. All samples proved to be leak proof confirming the success with Civan’s Dynamic Beam Laser.
E.E: Were there any products with special characteristics used?
CIVAN LASERS: The defining special characteristic of Civan’s Dynamic Beam Lasers is the ability to change the beam shape easily to any arbitrary shape. Most laser beams offer at most a limited selection of pre-existing shapes with no opportunity for flexibility.
Civan’s Dynamic Beam Laser allows the user to design and build beam shapes and sequences independently. This means that as circumstances change, the user has the flexibility to adjust beam shapes as needed to ensure optimal penetration and minimal defects.
E.E: How did your products / solutions improve productivity for the client?
CIVAN LASERS: Civan’s Dynamic Beam Laser showed Valeo a potential new way for them to produce large battery coolers for future e-mobility market needs.
The Dynamic Beam advantage for process development is the complementary software that is used to design new beam shapes. These shapes can then be quickly tested to find the optimal beam shape for each specific weld. This flexibility allows for rapid process development and eliminates spatter.
Valeo will now investigate the use of the Dynamic Beam Laser to create complex shapes at a feed rate greater than 20m/min, welding copper and welding dissimilar materials.
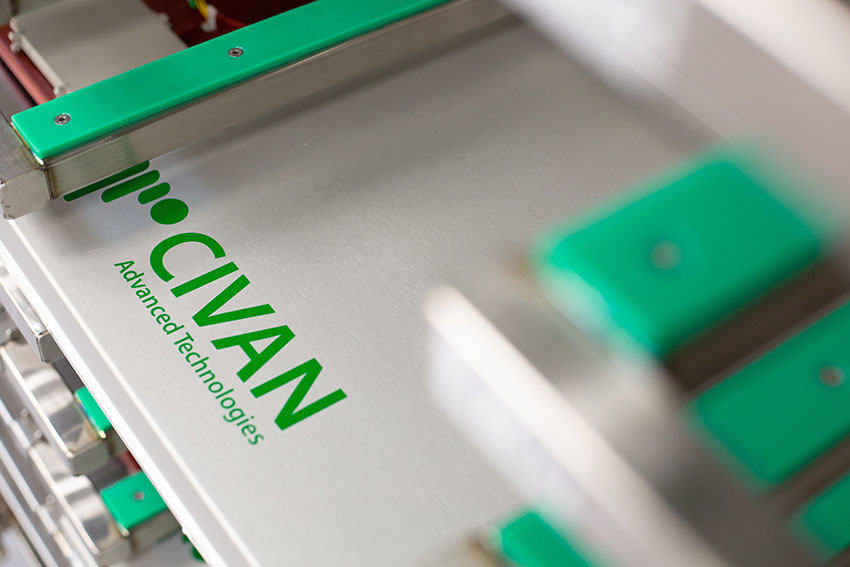
E.E: What was the client feedback after implementation?
CIVAN LASERS: The positive results have brought the idea for testing more difficulty applications as higher speed and welding of dissimilar materials.