Junaspin has recently completed a project with a leading automotive supplier where they provided customized lead screws and nuts for client’s manufacturing line. This project aimed to enhance the precision and reliability of the client’s production processes.
What were the needs of the client?
The client needed high-precision lead screws and nuts to reduce downtime, improve accuracy in their assembly line, and increase overall production speed. They were also looking for durable components that would require less frequent maintenance.
Why did the client choose your products / solutions?
The client chose our products because of our reputation for delivering high-quality, precision-engineered components. They were also impressed by our ability to customize solutions to meet their specific needs and our commitment to ongoing support.
What products / solutions were used?
We provided a range of high helix lead screws and trapezoidal lead screws specifically designed for the client’s machinery. These included high-precision lead screws tailored to their specifications.
Please describe how was the project implemented?
The project began with an in-depth analysis of the client’s production requirements. We then designed and manufactured the customized lead screws and nuts. Implementation involved close coordination with the client’s engineering team to ensure seamless integration into their existing systems, followed by rigorous testing to confirm performance improvements.
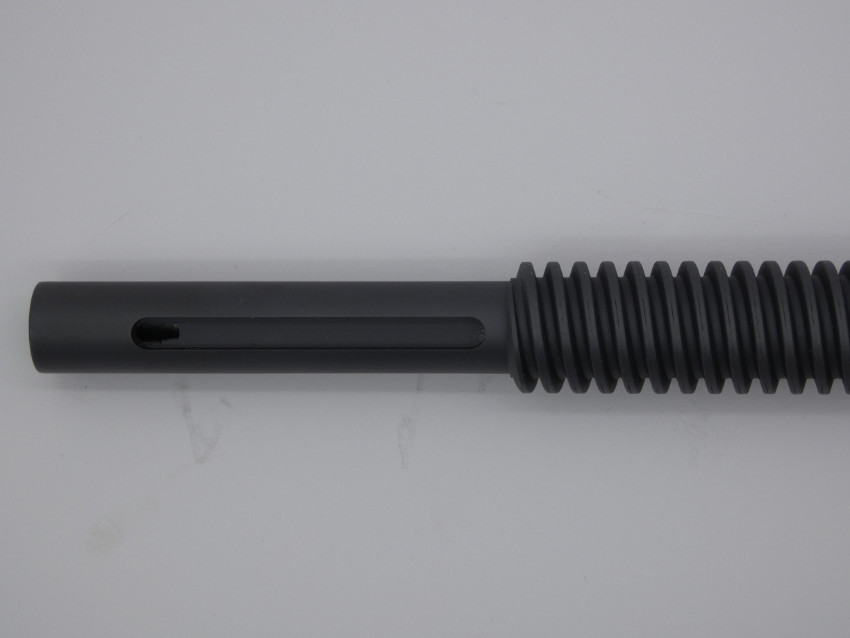
Were there any products with special characteristics used?
Yes, we used spindles with special low friction coatings to enhance durability and reduce friction, as well as threads designed to withstand high loads and speeds without compromising precision.
How did your products / solutions improve productivity for the client?
Our products reduced machine downtime by 20%, improved assembly line accuracy by 15%, and increased overall production speed by 10%. This led to significant cost savings and higher output.
How important was the project / projects for the client?
The project was critical for the client as it directly impacted their production efficiency and ability to meet market demand. Enhancing the performance of their assembly line was essential for maintaining their competitive edge.
What was the client feedback after implementation?
The client was extremely satisfied with the results. They appreciated the improved efficiency and reliability of their production line and noted a significant reduction in maintenance costs. They also praised our team for our professional approach and technical expertise.
How did the solutions provided improve efficiency for the client?
The solutions streamlined their production process, reduced the frequency of machine breakdowns, and increased the precision of their manufacturing operations. This allowed them to produce higher quality products at a faster rate.
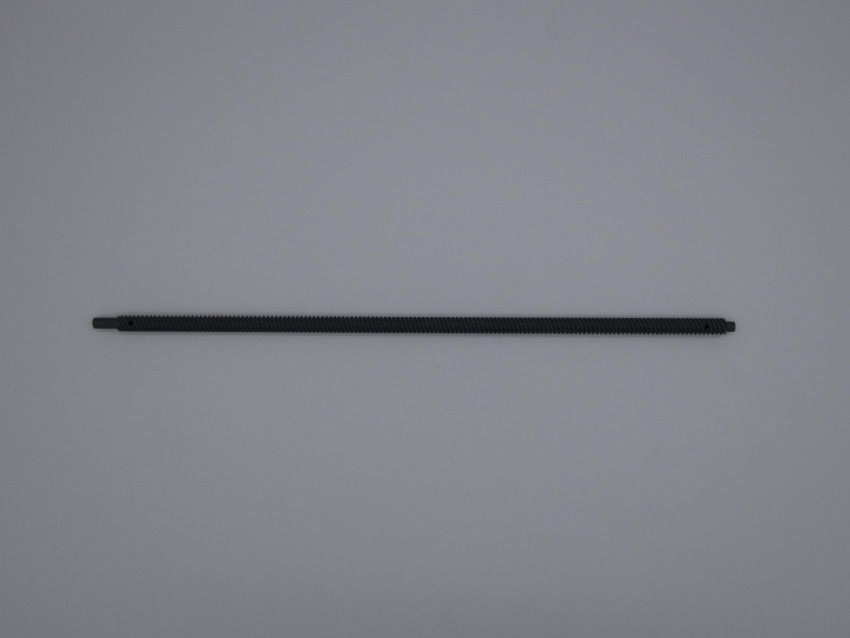
What are your forecasts for the second half of 2024?
We anticipate continued growth and expansion in the second half of 2024. With increasing demand for high-precision components, we expect to take on more projects similar to this case study. We are also investing in new technologies to further enhance our product offerings and maintain our position as a leader in the industry.
junaspin GmbH
Thread Technology and Machine Components
Reetzstr. 46b, 76327 Pfinztal, Germany
Dominik Hartmann
+49-7240/6179651