CEBES is a Czech family-owned company based in Brumov-Bylnice, founded in 1999. Its roots, however, trace back to 1947 with a longstanding tradition in the production of electromechanical sliding contact components. Today, the company employs over 320 people and operate a 15,000 m² production facility that includes the own R&D center. The company is structured into two main divisions – Industrial and Automotive – focusing on the development and production of components for industrial applications and the automotive sector. CEBES specializes in heavy duty commutators, slip rings, and brush holders, which they supply to global partners for use in electric motors, robotic systems, wind turbines, aerospace, and medical technologies. Their services span the entire process – from development and prototyping to automated series production.
Interview with Roman Švach, Head of Sales and Marketing at CEBES.
What are the company’s main areas of activity?
Roman Švach: CEBES primarily operates in the wind energy sector, where we produce complete slip ring assemblies for wind turbine generators. In the field of e-mobility, we supply brush holders and slip rings for electric vehicle motors. Another key area is the production of commutators for rotating electrical machines, which are used across a wide range of industrial applications.
What are the latest developments in products/services?
R.Š: The most significant innovation is the launch of series production of brush holders for the sixth generation of BMW’s electric vehicles, the Neue Klasse platform. This project has been in intensive development for over 4.5 years – from initial concept through testing to finalization of the production process. The official start of series production is set for August 1, 2025. In addition, we have launched a new company website that presents our technological focus and international presence in a more modern and accessible way.
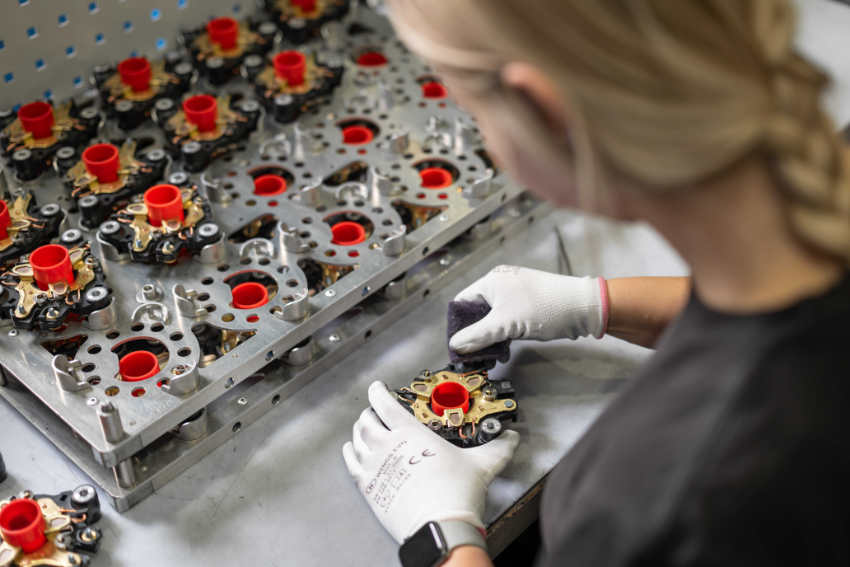
What is the range of your products/services?
R.Š: CEBES offers a wide portfolio of products and technological services, covering the entire process from development to serial production. Our key products include SUKaT pressed commutators for traction motors requiring high mechanical durability, brush holders for traction motors with the option of service and repairs, and slip ring assemblies for wind turbines supplied to leading European manufacturers. A significant part of our product range also includes slip rings and brush holders for the automotive industry and energy sector, as well as screw-mounted commutators, particularly suitable for demanding traction drives, where we also offer complete overhauls using original parts.
Beyond final components, we also provide a wide range of specialized services. With our in-house R&D center and long-standing expertise, we can deliver turnkey solutions – from initial design to final product delivery.
What is the current state of the market in which you operate?
R.Š: The market is currently very dynamic, primarily driven by the rapid growth of e-mobility and industrial digitalization. At the same time, there is increasing demand for highly precise and reliable components – an area where we excel thanks to our automation, certified processes, and experience.
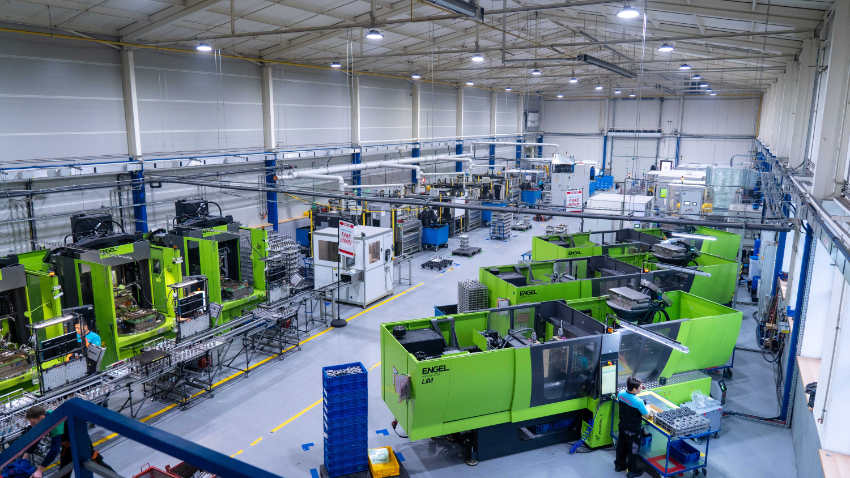
What can you tell us about market trends?
R.Š: Across all major sectors, there is a growing emphasis on product longevity, maintenance-free operation, and compact design. In the field of e-mobility, the focus is on developing reliable components that outlast the service life of the vehicle itself. Our components for electric drives are designed to operate maintenance-free, providing long-term reliability even under extremely demanding conditions. There is also a growing pressure for compactness – the ability to deliver maximum performance in minimal space – a trend evident not only in automotive but also in industrial applications.
What are your most innovative products/services currently on the market?
R.Š: Our most innovative solutions are the result of integrating in-house development, design, and automated manufacturing under one roof. This approach allows us to respond flexibly to customer requirements and create advanced products with high added value. A key trend is the emphasis on top-tier quality, long-term operational reliability, and compact design – meaning the ability to integrate complex functions into space-saving units. It is this combination of technical precision, smart design, and maintenance-free durability that makes our products the preferred choice for demanding applications across various industries.
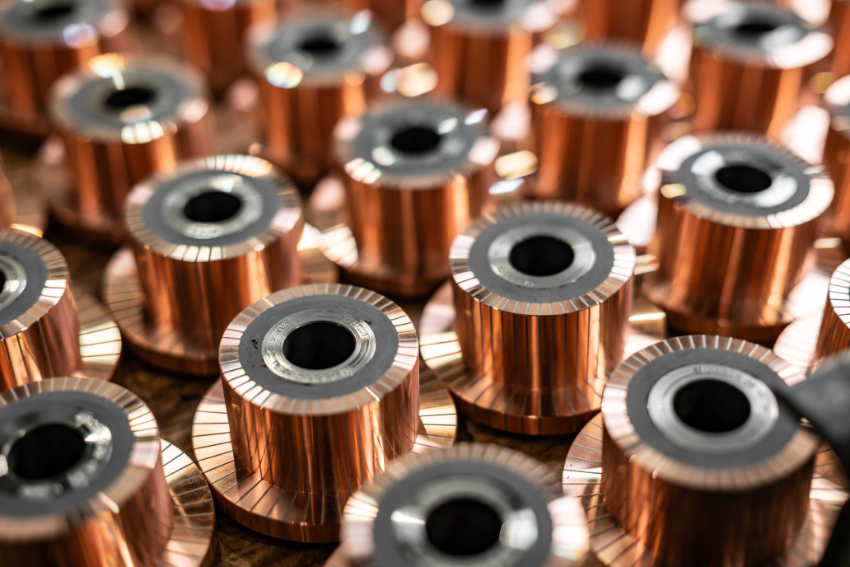
What are your projections for the second half of 2025?
R.Š: In the second half of 2025, we expect continued growth in both our main divisions. In Automotive, we are building on a successful long-term partnership that has seen us supply slip rings and brush holders for BMW’s fifth generation of electric vehicles. We are now launching the series production of a new generation of brush holders for the Neue Klasse platform, representing a significant technological and commercial milestone. In the Industrial division, our focus is on developing slip rings and brush holders for 8MW wind turbines – a solution designed for the most powerful next-generation turbines.