Composite Recycling is a Swiss-based startup founded in 2021 that has developed a profitable, sustainable, and mobile solution to recycle glass fibre reinforced plastics (GFRP) waste into high-value glass fibres and pyrolysis with ready markets and existing applications.
Interview with Wendy Perben, Head of Marketing & Communications at Composite Recycling SA.
Easy Engineering: A brief description of the company and its activities.
Wendy Perben: Our mission is to make fibreglass recycling a reality and to divert 100% of GFRP waste away from landfills and incineration and into the production of high-value, high-performance new composites and decarbonated plastics.
Our objectives are to:
- Divert composite materials away from landfills, incineration, and the environment, while enabling continued use of this incredibly functional and versatile material (GFRP).
- Produce high-quality recycled products for reuse in the circular economy.
- Significantly reduce CO2 emissions related to composite manufacturing.
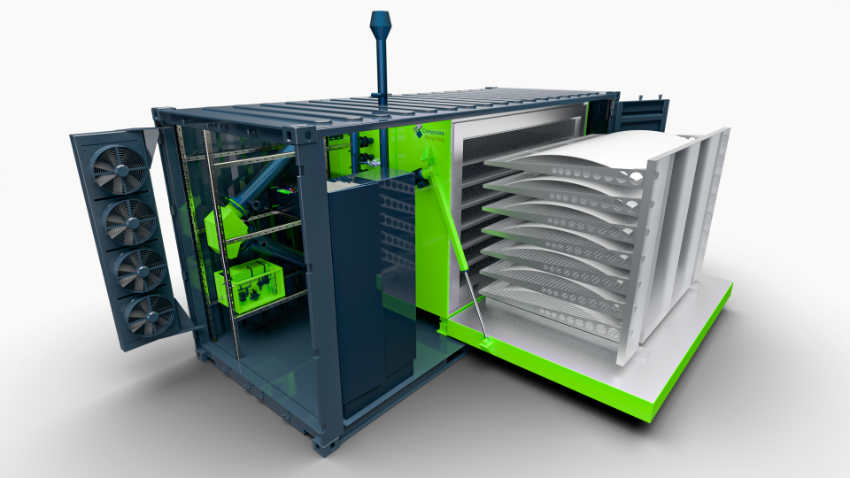
E.E: What are the main areas of activity of the company?
W.P: We have developed a proven and patent-pending pyrolysis and post-treatment technology that recycled GFRP waste into glass fibres and pyrolysis oil that we sell to our downstream manufacturing clients to make new composites. The high quality of our outputs enables their reuse in even high-performance products, distinguishing our offering in the sector.
One unique aspect of our approach is that we’ve developed our pyrolysis reactors to treat composite materials only – rather than attempt to also accommodate other types of waste like other plastics and organic waste. This maximizes the quality and re-usability of the outputs, as well as the energy efficiency and process economics. We also test, design and calibrate each machine to the specific type of GFRP to be treated, depending upon the client.
Finally, to avoid the cost and CO2 impact of transporting bulky composite wastes, we have designed our reactors to fit into a 30 foot container for easy transport to client sites, where they can treat waste on the spot – particularly handy for boat waste in hurricane strike zones, for example, or to move between wind farms or regional manufacturing hubs.
It’s important to note that composite waste does not come solely from end-of-life products. During manufacturing, waste created when cutting shapes out of the virgin GFRP (such as for windows and doors of camper vans) can account for 10-30% of new composites used, depending upon the industry, and is also now landfilled. Fortunately, this waste is easier to recycle, as its content is new and uncontaminated, and the precise composition is easily ascertained.
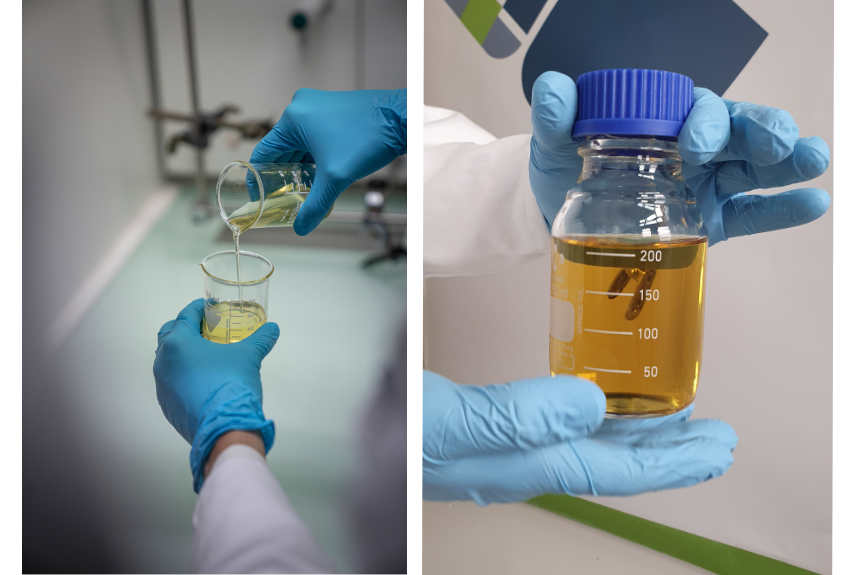
E.E: What are the ranges of products/services?
W.P: Our product offering includes:
- A low-emission, cost-effective, and mobile fibreglass waste treatment service
- High-quality reclaimed recycled glass fibres and pyrolysis oil suitable for reuse
- Waste material testing and recyclability certification.
Our customers benefit from the following:
- Sustainable disposal of composite waste / avoidance of landfilling
- Demonstration and certification of a sustainable end-of-life solution for their products, to comply with regulations and market demands.
- Ability to bring to market new products made with recycled content
- Avoidance of taxes levied on new products without recycled content (such as exist in Italy and Spain for plastics).
- Reduced carbon footprint (and taxes) from new GFRP production by prolonging their useful life via recycling.
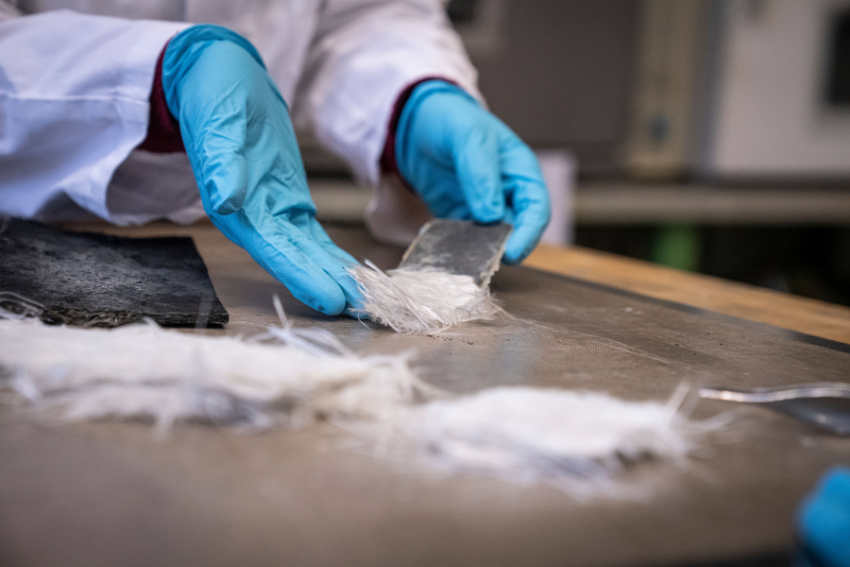
E.E: What is the state of the market where you are currently active?
W.P: The problem of composite waste is large and the need for a solution is urgent. In 2023 alone, Europe produced 500 000 tonnes of composite waste, a number which is expected to reach 800 000 tonnes in 2030. (source: EUCIA) Composite plastics first began to be widely used about 60 years ago. Given that GFRP have a useful life of 30-50 years, now every year, more and more of the earliest-produced composites arrive at end-of-life.
Unfortunately, fibreglass has been designed for strength and durability, not recyclability. Today the most common means of disposing of waste GFRP are either (1) landfilling, which isn’t sustainable, or (2) incineration in kilns (GFRP burns hot and produces a lot of energy), which releases CO2.
Today we see many efforts to “recycle” GFRP. Unfortunately, these methods either destroy the valuable properties of the material – like shredding it to use as filler material, or simply waste them – like slicing up wind turbines to use as bike shelters.
Beyond these options, thousands of wind turbine blades are simply stockpiled in fields for a hoped-for future treatment, while thousands of boats are abandoned along waterways. In 2023 the boating and wind turbine industries alone produced 34 000 tonnes of composite waste in Europe, a figure set to increase to 96 000 tonnes in 2030.
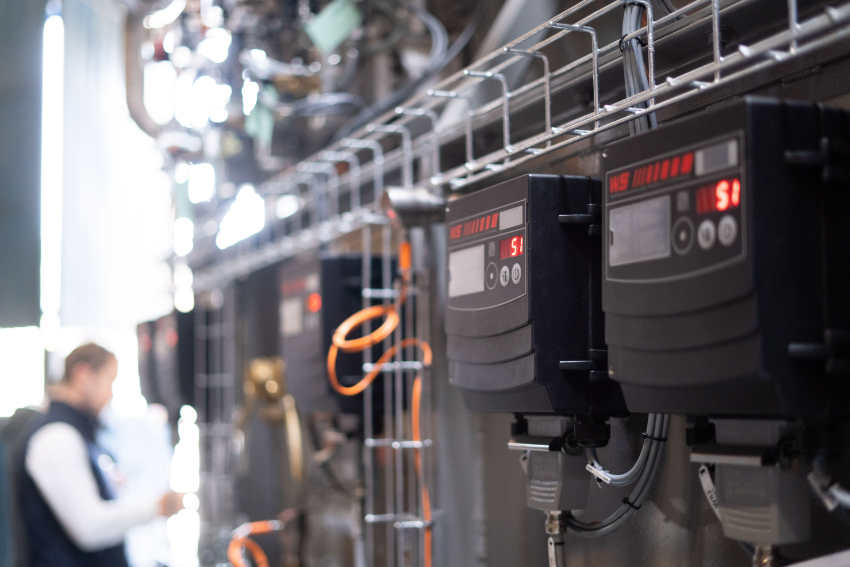
E.E: What can you tell us about market trends?
W.P: While the volume of waste is accelerating, landfills are increasingly expensive and reluctant to accept composite waste. For example, the 2023 rate of EUR 200 to landfill 1 tonne of composite waste in western France will go to EUR 300 in 2025 – up 50% in two years. The same service costs EUR 600 in Northern Italy today.
Meanwhile, regulators are moving to ban landfilling outright. In Europe the EU Directive 1991/31/EC banned the landfilling of all toxic waste – including composite material. However, composite waste was exempted from the ban as no other options existed.
However, this exemption is being lifted over time, country by country. Already the landfilling of wind turbines is forbidden in German, the Netherlands, Finland and Austria. In 2023, Austria banned the landfill of all composite materials as of 31 December 2023, creating a huge challenge for Austrian composite firms, who currently rent storage space for hundreds of tonnes of production scraps while they search for a viable solution.
Regulators are also putting pressure on the production side, requiring manufacturers to plan in the circularity. The automotive industry is under particularly strong regulatory pressure in Europe, where the Directive on end-of-life vehicles (ELV Directive) requires each new vehicle to achieve 25% recycled plastics content by weight by 2030. Electric car battery containers, body panels and hydrogen tanks are already now made of composite materials, but the industry is still far from the target.
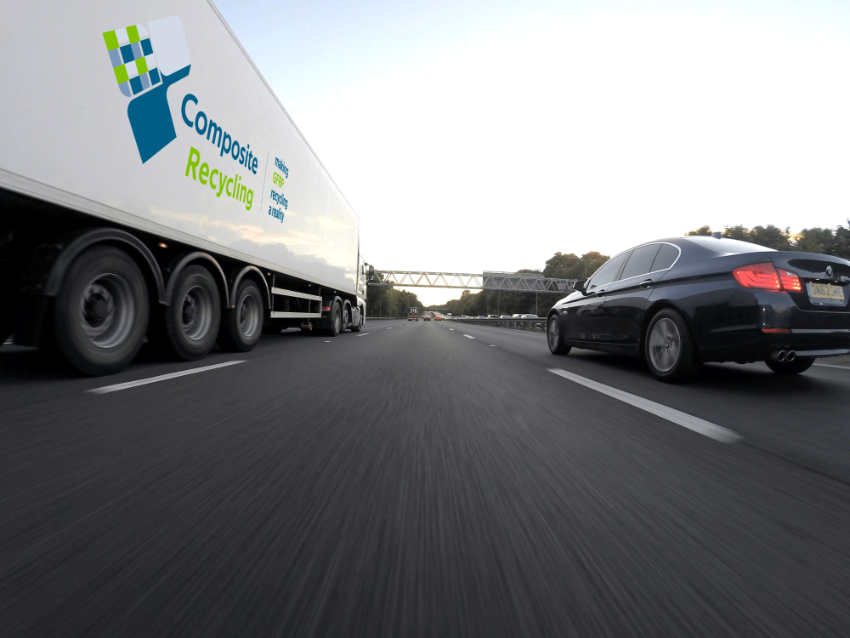
E.E: What estimations do you have for 2024?
W.P: Composite Recycling was founded in 2021 and had its start-up phase in 22-23, during which we formed many key partnerships (such as with industry leaders Arkema, Beneteau Group, Huntsman and Chomarat) and won many startup and industry awards (MassChallenge, FIT, Venture, JEC World, METSTRADE, Monaco SmartYacht, etc).
But 2024 is what we’ve been working so hard toward all this time, because in late summer 2024 we will launch our first industrial-scale mobile recycling unit, commencing our scale-up and industrialization phase. It is a very exciting time, when we will be thrilled to enable our waste treatment service clients to start recycling their waste and our recycled content clients to begin producing “green” versions of their products, both at an industrial scale.
It will mark the beginning of realizing our mission of diverting composite waste away from landfill and into high-value applications.