What is Dedert, and what are its areas of expertise in industrial drying?
Dedert has been at the forefront of industrial drying technologies for over 50 years. While spray drying is well-known and commonly used in early developmental stages, Dedert continues to innovate specialized drying features to achieve high-quality drying for a wide range of applications, focusing on sustainable, energy-efficient operations for full-scale commercialization.
Dedert specializes in other dryers besides spray drying, including ring drying, flash drying, roto-flash drying, and fluid-bed drying. Each dryer has unique features and custom drying systems for consumer applications in various industries. Learn more about the history of these drying processes and how Dedert utilizes a wide scale of drying technologies.
What are the various types of dryers that Dedert specializes in, and what are some examples of typical products that each type of dryer can process?
Spray Drying: Spray Drying was developed by a French engineer, Alexis Millardet, in the 19th century to create dried wine yeast for the wine business. Today, a Spray Dryer is an industrial machinery used to turn liquids into powders or granules. This whole process is done in a single step. The liquid is atomized into tiny droplets, and the moisture is subsequently removed by drying the droplets in a hot air stream. The result is a fluid powder that is simple to carry and package. In comparison to other drying techniques, spray drying is a common process in the food, pharmaceutical, and chemical sectors because of its high efficiency, adaptability, cost-effectiveness, and consistent product quality.
Single-Stage Drying: The Single-Stage Spray Dryer is the most common and flexible solution for drying a full range of products in the food and chemical industries. Dedert’s Single-Stage Spray Dryers are equipped with a proprietary hot gas distributor, which ensures optimum contact with the drying medium in the drying chamber. The liquid feed is dried to a fine powder in the drying chamber, discharged from the cone bottom, or conveyed with the exhaust air to a primary separator, cyclones, or a dust filter. Depending on the specific application, the drying configuration is primarily co-current but can be offered in other configurations; for heat-sensitive and difficult-to-dry products, integrated cooling for the chamber, roof and hot gas distributor are provided.
Single-Stage Drying Applications:
Chemicals
- Insecticides
- Catalysts
- Titanates
- Monoammonium Phosphate
- Al2O3
- SiO2
- Diammonium Phosphate
- Kaolin
- Silicon Oxide/Nitride
- Zinc Oxide
- Ammonium Sulfate
- Zirconium Oxide/Silicate
- Urea-Formaldehyde
Food/Pharma
- Food ingredients
- Proteins
- Maltodextrins
- Flavors
- Microcrystalline cellulose
- Gelled starches
- Meat replacers
Multi-Stage Drying: Dedert’s Multi-Stage Spray Dryer is used to dry more advanced particles. Such powders are termed agglomerated or granulated powders, i.e., smaller individual particles are stuck together to form an agglomerated cluster by multiple individual particles. A multi-stage dryer allows for coarser particles with enhanced reconstitution properties to be formed. The spray dryer would, in this case, feature an integrated fluid bed located at the lowest point of the drying chamber, while the exhaust air would leave the chamber through two openings in the roof of the dryer. External fluid beds are often used for many purposes: post drying and cooling of the powder and dedusting as the fluidization would elutriate the finer particles and carry these to the cyclone or bag filter.
Multi-Stage Drying Applications:
- Foodstuffs
- Pharmaceutical ingredients
- Agrochemicals
- Dyestuffs
- Fungicides
- Water treatment chemicals
Flash Drying: Flash Dryers were invented in 1932 by Dr. Rosin. Flash drying is a simple, versatile and efficient drying technology that Dedert has used in many industries to approach the removal of moisture from customers’ products. Flash Drying was developed to address the need for a fast and efficient way to dry heat-sensitive materials. A key advantage of Dedert’s Flash Drying is its ability to dry materials quickly and at lower temperatures, which minimizes the risk of thermal degradation. The short residence time also prevents the formation of lumps or agglomerates, which can be a common problem with other drying methods.
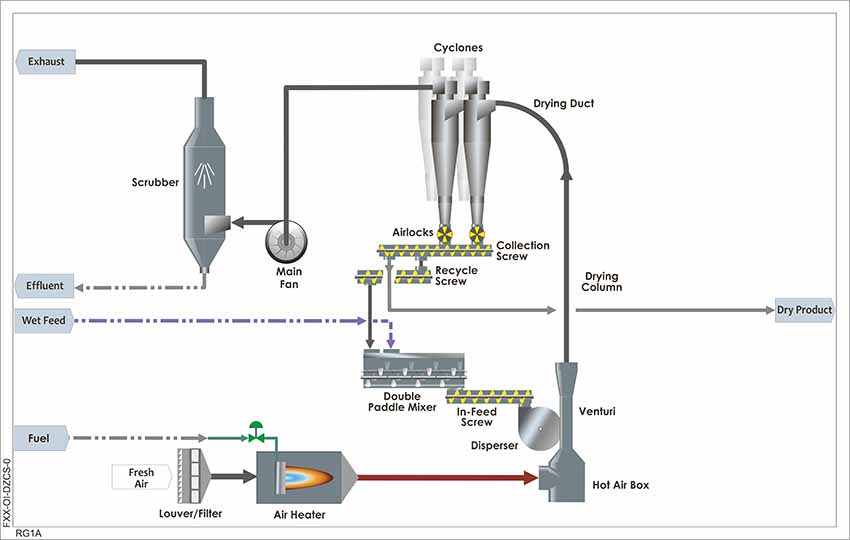
Typical Flash Drying Applications:
- Native Starch
- Sodium Bicarbonate
- PET flake
- Calcium Silicate
- Expandable Polystyrene (EPS)
- Copper Powder
- Corn Masa Flour
- Aspirin
- Dicalcium Phosphate
- Coal
- Polyacrylonitrile (PAN)
Ring Drying: Ring Dryers were invented in 1948 by Dr. Barr. The ring dryer is a modified flash dryer. This process involves feed materials passing through a ring, which is heated and dried using a pneumatic system. Dedert’s Ring Dryers is a suitable system for applications that require longer drying times because it allows for internal recycling and extended residence time compared to other dryers. The ring dryer uses a Manifold classifier to centrifugally separate heavier and wetter particles recycling them back into the drying stream while allowing the inner and drier material to pass out to the cyclones.
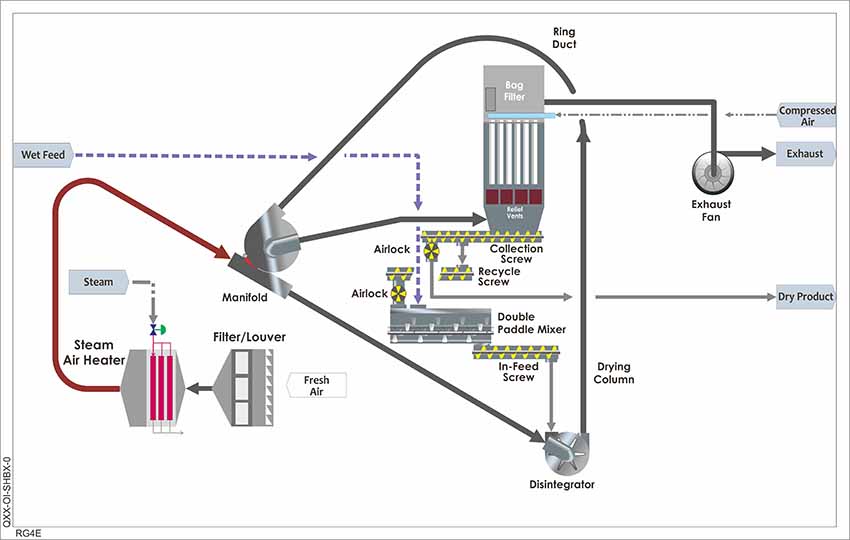
Typical Ring Drying Applications:
- Casein
- Wood Pulp
- Vital Wheat Gluten
- Silicas
- Zeolites
- Precipitated Calcium Carbonate
- Kaolin
- Pigments & Dyes
- Epsom Salts
- Paper Sludge
- Protein
Feed-Type and P-Type Ring Dryers: Since the original invention of the Full Ring Dryer shown above, the principle of centrifugal separation and recycling of solids has been further developed and tailored to process other materials including Feed-Type and P-Type Ring Dryers.
The Feed-Type Ring Dryer was developed in 1964 to allow the ring dryer to be built on a very large scale. The dryer is so called because it was initially developed to dry animal feed products from cereal processing and alcohol distilleries. Today, many large feed dryers are operating at over 36 tons/hr of evaporation.
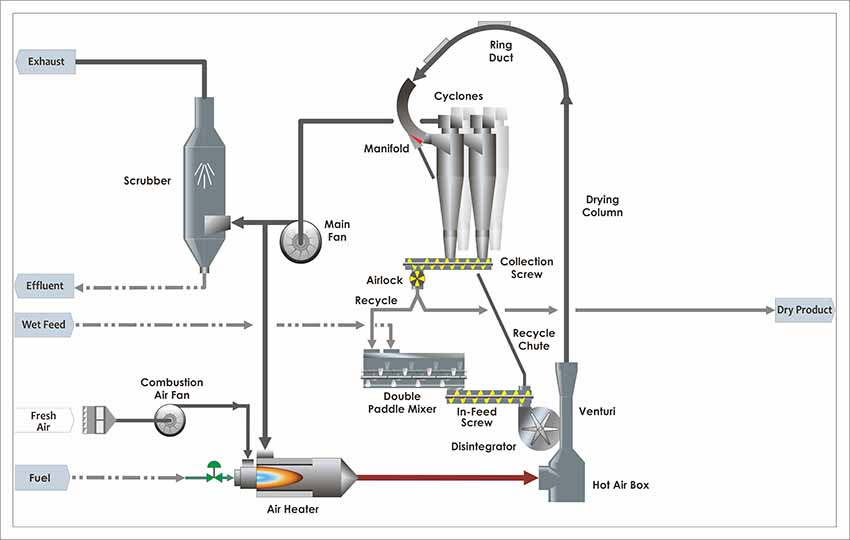
Feed-Type Drying Applications:
- Soy fiber
- Corn fiber
- Distillers Dried Grains (DDGS)
- Animal feed
- Organic sludges
- Municipal sludge
The P-Type Ring Dryer was developed in 1974 to give extended residence time when drying modified starch. The P-Type Ring Dryer recycles product into the cooler part, allowing for very gentle thermal treatment. Dedert uses Ring-Dryer systems for our customers’ applications and continues evolving the design. Customers value these specialized ring dryers in various industries for drying materials.
P-Type Drying Applications:
- Ethyl Cellulose Resin
- Heat-Sensitive Materials
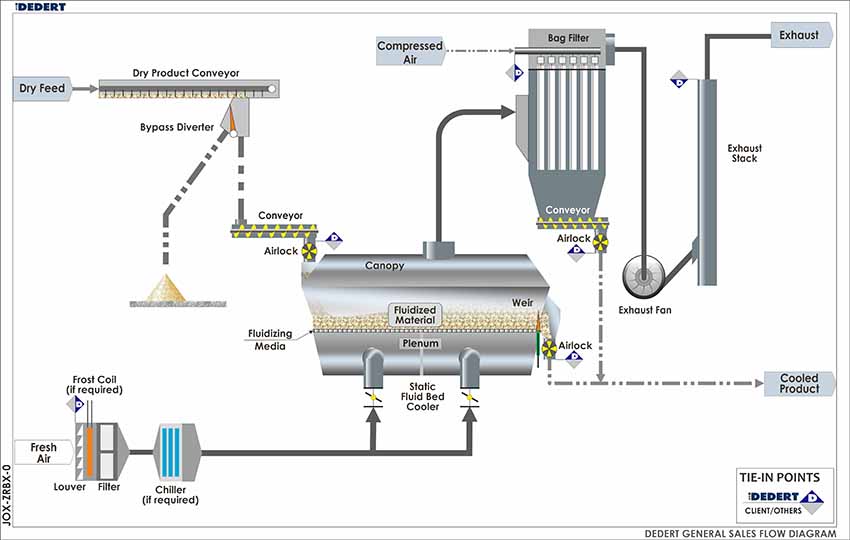
Fluid-Bed Drying: Fluid-Bed Drying was first developed in the 1950s, a type of industrial dryer to uniformly dry granular, crystalline, or other powdered materials. Applications are fluidized with streams of hot air or gas quickly and efficiently because this type of drying has an increased surface area to promote even drying.
Fluid-Bed Drying Applications:
- Ammonium Sulfate
- Coal
- Casein
- Corn Germ
- DDGS
- Detergent
- Fertilizer
- Ion Exchange Resin
- Nylon
- Polyacrylamide
- PET
- Potash
- PVA
- Sand
- Sodium Chloride
- Sodium Sulfate
- Sugar
- TSP
- Urea Prills
Roto-Flash Drying: Roto-Flash Dryers have been around since the early 20th century. It is also known as a Spin-Flash dryer, and Dedert uses it to primarily dry filter cakes, pastes, and viscous slurry. The dryer features a low-speed vertical agitator to distribute the dried materials and has a limited capacity for scale-up, with a maximum capacity of up to 50,000 acfm. The hot air inlet included in the Roto-Flash dryer is an efficient drying mechanism, and the dryer is compact and does not require feed conditioning, making it a cost-effective and energy-efficient drying option.
Roto-Flash Drying Applications:
- Titanium Dioxide
- Silica
- Iron Oxides
- Kaolin
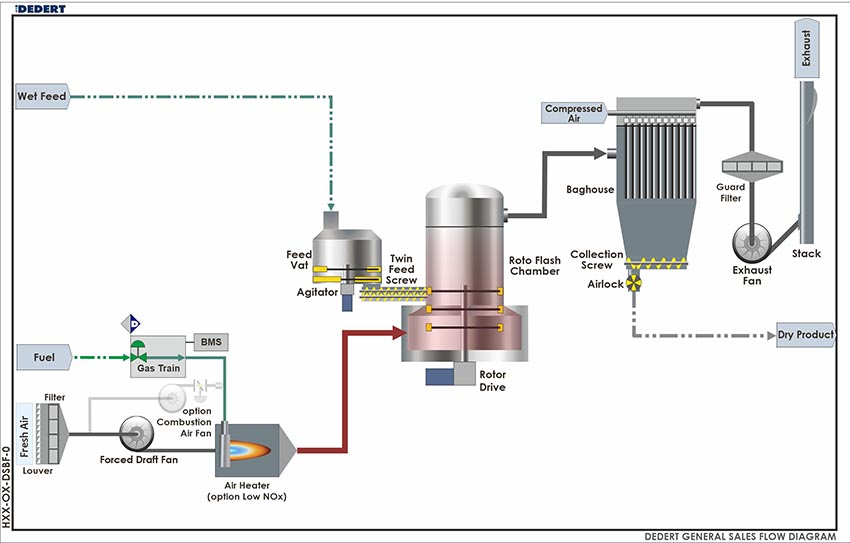
Why Should You Utilize Dedert’s Dryers?
Dedert’s engineers are well-equipped with the latest tools and technologies to design and develop customized drying solutions for various applications. Dedert’s solution-centric approach allows them to understand customers’ needs and requirements and develop cost-efficient, sustainable and reliable drying technologies. Furthermore, Dedert’s commitment to sustainability is reflected in its drying systems, which utilize energy-efficient technologies, reduce waste, and minimize environmental impact. Dedert’s dryers are designed to provide maximum efficiency, reliability, and performance while minimizing operating costs. Dedert’s comprehensive understanding of drying technologies and ability to provide customized solutions make them a trusted partner for customers in various industries.
Visit https://dedert.com/contact-us/ to contact a team member about your drying inquiries.