Electroder is a technology company with its vision to empower the battery industry with advanced research & development software and professional industrial services. Electroder’s innovative solution can support cell manufacturers, OEMs and energy storage companies to conduct R&D activities for best performing, manufacturing friendly and sustainable battery cells with 60% less time and half the cost compared to trial-and-error approach.
Interview with Luke Hu, Co-Founder & General Manager Global at Electroder.
Easy Engineering: A brief description of the company and its activities.
Luke Hu: Today, the world’s journey towards a sustainable future has been unlocked by the transition to e-mobility and energy storage with the invention and application of lithium-ion battery, but unfortunately it is also limited by the speed, cost and how good we are at developing these critical components. Electroder’s mission is to solve this critical problem.
Today, we are mainly operating in China and Europe, and support clients all over the world where battery cells are being developed and manufactured. Our investors include leading technical VCs, e.g. Robert Bosch Venture Capital. Recently, we are proudly awarded as a Technology Pioneer by the World Economy Forum and made our contribution at the 2024 Davos Forum.
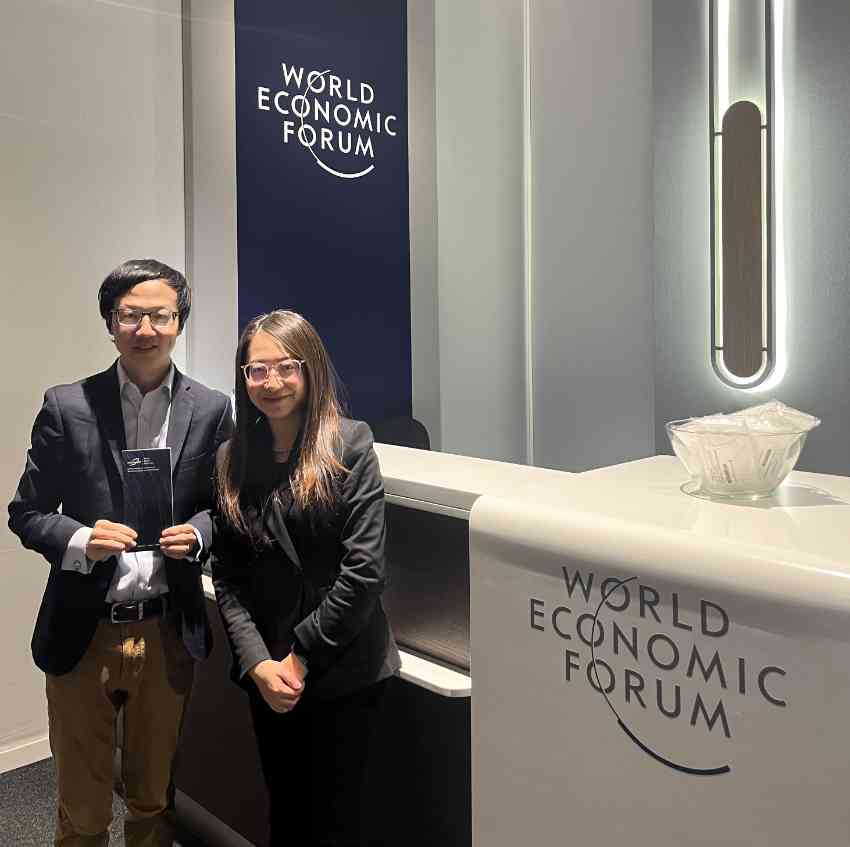
E.E: What are the main areas of activity of the company?
L.H: Electroder develops state-of-art software and engineering service for battery cell R&D. Our software is an easy-to-use and powerful tool for researchers and engineers to build and validate cell design concepts. We have four main modules which can be subscribed separately or combined.
ElectroderMOD is a quick design module to evaluate cell capacities, dimensions and BOMs (Bill-of-Material) for all formats of batteries, including prismatic, pouch, cylindrical and more.
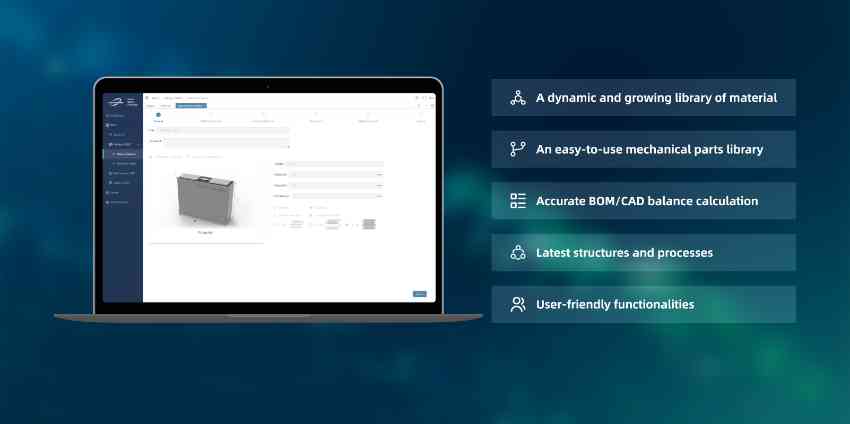
ElectroderLIFE is a comprehensive tool which can predict life cycles and ageing behaviors of cells at default or customized working conditions.
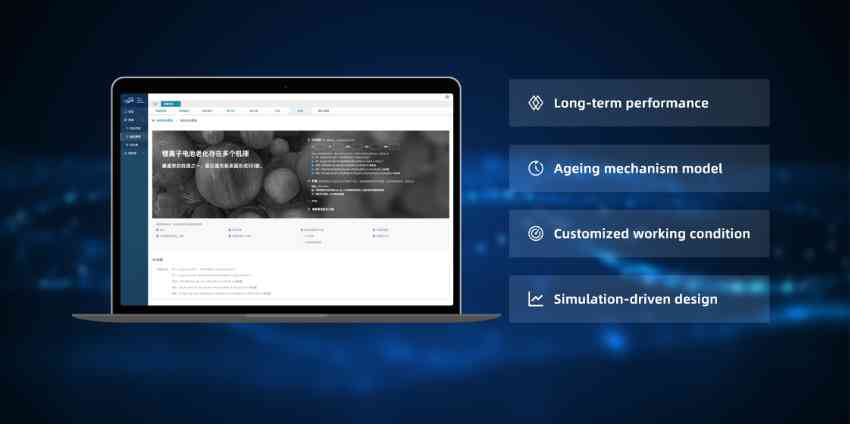
ElectroderSIM is a powerful simulation driven design software with cutting-edge heterogeneous electrochemistry and thermal model at world-class accuracy.
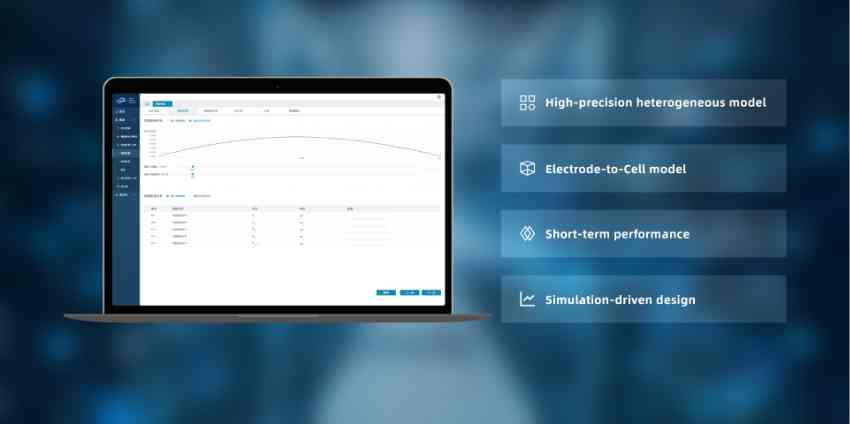
We are also developing a new tool to empower battery design with artificial intelligence, named ElectroderBDA – Battery Design Automation, which can level up design process to the next level.
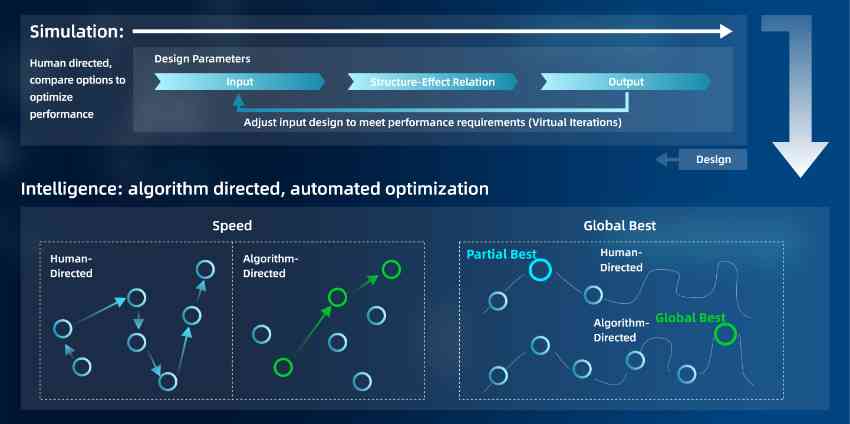
Besides these products, we also offer our clients independent engineering solutions from concept-level consultancy to turnkey design. We also work on research projects of advanced battery design, for example solid-state and sodium-ion.
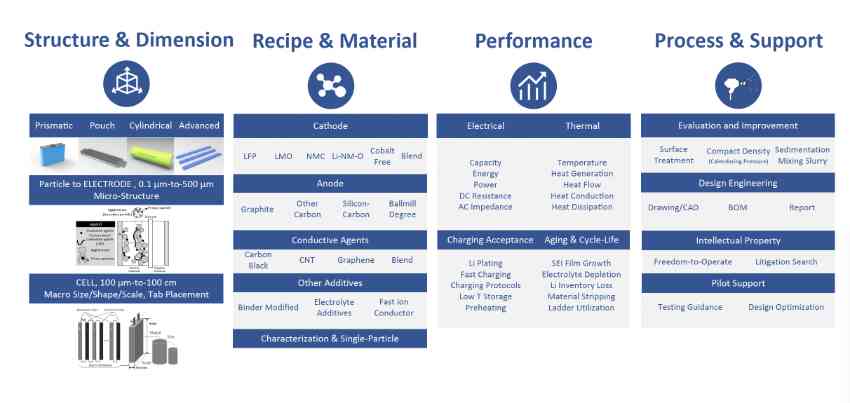
E.E: What’s the news about new products/services?
L.H: We recently announced that ElectroderMOD is open to trial and subscription in Europe region. For those who are interested, they can contact or submit a request through our website. Potential clients can also express their interest in testing our new modules when they are coming to release.
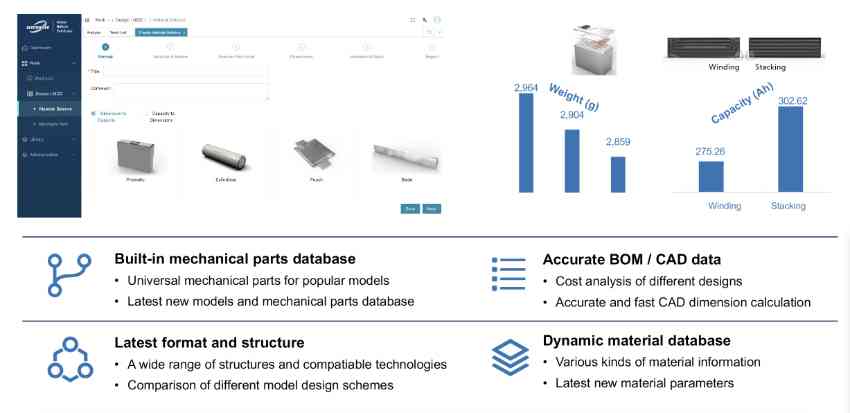
Regarding service projects, our specialized team are working on many projects with automotive OEMs which are to produce or design their own cells and energy storage clients with the target to increase battery cycles.
E.E: What are the ranges of products/services?
L.H: Our products and services cover a wide range of needs in battery cell development. For mechanism design, we have accumulated good know-how in both traditional formats like prismatic and new formats like large cylindrical or blade cells. For chemistry, we leverage our experience in both NCM and LFP to develop the most optimized solution. For simulation performance analysis, our software and services cover electrochemistry, thermal and ageing which are essential for design optimization.
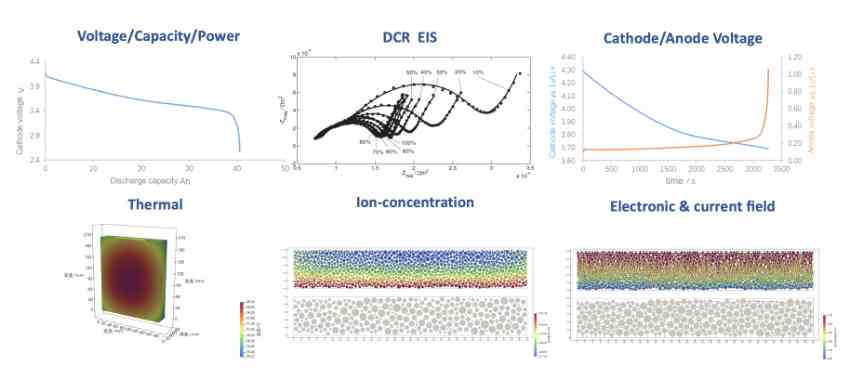
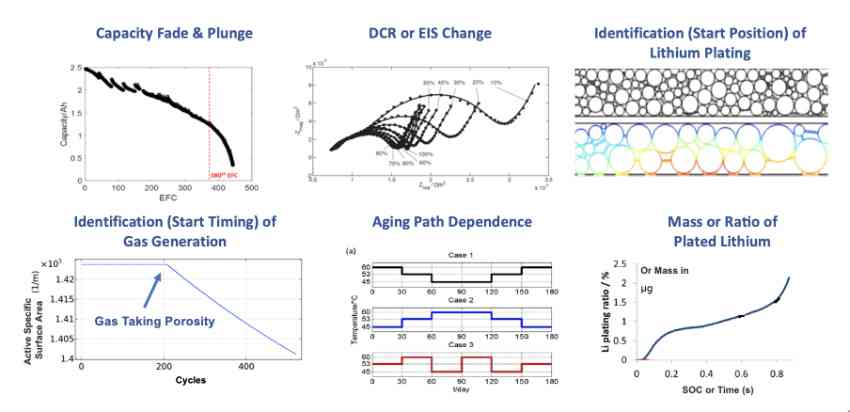
E.E: What is the state of the market where you are currently active?
L.H: The battery market has seen rapid growth for the past decade. However, the development technology in place for most manufacturers are still quite conventional. A trial-and-error approach involved sample building, testing and repeating, which takes too long and consumes lots of material, energy, equipment and staff hours.
Simulation-driven approach has been used in some cases, but the right solution requires essential elements including:
- Accurate performance analysis
- Direct input of design related parameters
- User-friendly for engineers to adopt
The cell development process is coming to a tipping point.
First, we shall expect more intense R&D activities. One the one hand, more mobility applications are being electrified – cars, trucks, municipal, maritime and aviation, leading to a growing number of cell models for different features. On the other hand, energy storage systems are becoming very competitive, resulting in development activities towards more affordable, long durable (battery cycles) and of course more reliable solutions.
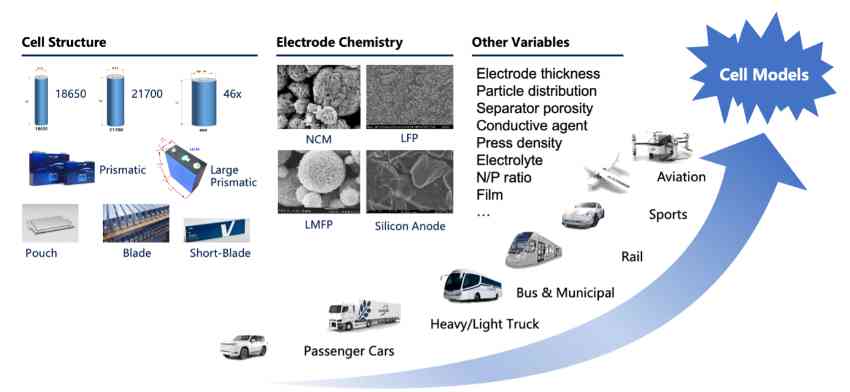
Second, due to the rising demand of cell models, the capacity to conduct development by trail-and-error will soon be reaching to limit if not already. We already start to see more and more successful cases of virtual design, simulation driven advanced validation and the application of artificial intelligence in cell development. Time-to-market and reworks will be significantly reduced where virtual design is applied.
Finally, we will start to see more engineers and technicians, besides specialists, can start to carry out simulation-driven analysis in cell development. This will have a positive impact because the ones who know about battery and those who understand simulation can collaborate for the best performance and manufacturability. It is exciting to develop a toolbox full of useful modules for those who design ‘energy’.
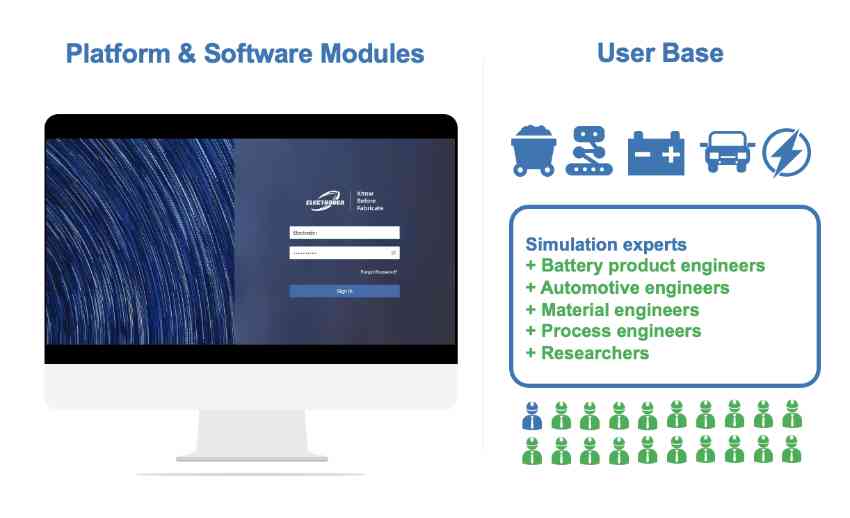
E.E: What estimations do you have for the beginning of 2024?
L.H: 2024 will be an important year for battery and energy transition, especially in Europe. We will start to see the first wave of cell production by local companies. We are going to see some cell startups getting more successful with their product while some others struggle a bit in financing their commissioning and capacity ramp-up. We are going to hear about more automotive and system OEMs developing and/or manufacturing their own battery cells. One thing to be sure, our journey to a resilient supply chain and sustainability future will be more solid.