Exacom is a subsidiary of Viscom AG, a leading global provider of non-destructive imaging solutions. The Hanover-based company pools the Group’s expertise in the development and production of specialized X-ray solutions for battery production. A comprehensive portfolio of X-ray and optical battery inspection solutions is offered for this purpose.
Interview with Markus Möller, Business Development Manager at Exacom.
Price: tell us something about the costs from a ROI perspective?
Markus Möller: From a return-on-investment (ROI) perspective, there are multiple angles to consider when evaluating the costs associated with electric vehicle battery production. One critical aspect is ensuring cells meet specifications, which includes preventive measures to prevent risks such as short circuits, lithium plating, and dendrite development.
Failing to address these risks in mass production can lead to costly failures in the field, potentially putting human life at risk. The financial impact of recalls can be astronomical, with examples from the past demonstrating how damaging this can be for a brand’s reputation and sales.
Another crucial aspect is cell quality, including degradation and performance. X-ray inspection plays a vital role here, as it helps ensure cells deliver maximum energy output while lasting through intended cycles.
The battery pack accounts for 30-40% of an electric vehicle’s cost, with the range being the most important factor for buyers today. However, long-lasting batteries with good performance are also critical to safety and driving characteristics, directly impacting revenues.
Given these factors, it’s clear why x-ray inspection is essential. The nature of this process is binary: “good” or “not good.” This decision-making framework has driven the adoption of x-ray inspection in battery production for obvious reasons.
However, as the industry matures, efficiency becomes increasingly important. Let’s break down costs to understand why yield and efficiency are crucial:
- 30-40% of an electric vehicle’s cost is attributed to the battery pack.
- Around 80% of these costs come from cells.
- Nearly three-quarters (75%) of cell costs are driven by materials, with only around 25% going towards manufacturing equipment, facilities, and depreciation.
With opex costs so high, yield plays a vital role. Current waste rates range from 15-30%, but studies show that these numbers can be reduced to approximately 7-8%. Realistic targets for yield are currently around 10%.
Exacom’s equipment is designed not only to make reliable “good” or “not good” decisions based on customer specifications but also to gain process knowledge and initiate continuous improvement. Our metrology approach enables this methodology.
Considering all these factors, the direct or indirect ROI of Exacom equipment is fast and valuable in the long term for manufacturing competitive cells.
What about the costs for maintenance / future upgrades etc.
M.M: When considering X-ray inspection in electric vehicle battery production, it’s essential to think about operational costs beyond just maintenance and upgrades. Let’s take a broader view.
Our Exacom machines are designed not only for safety and high yield of cells but also for minimal dry room space requirements. This is crucial because operating these spaces efficiently can be costly due to the need for capital expenditures (capex) and energy-intensive installations to maintain temperature control, cleanliness, and other conditions. By minimizing machine footprint, we reduce capex and operational expenses (opex) in gigafactories.
We’re committed to reducing our machines’ energy consumption not only to minimize direct costs but also to reduce heat emissions, which is particularly important for dry rooms that require precise temperature control. Another key factor is speed: the higher the throughput, the fewer machines are needed, resulting in less space required and lower opex costs. We can quantify this with a simple ratio of PPM (parts per minute) to square meters.
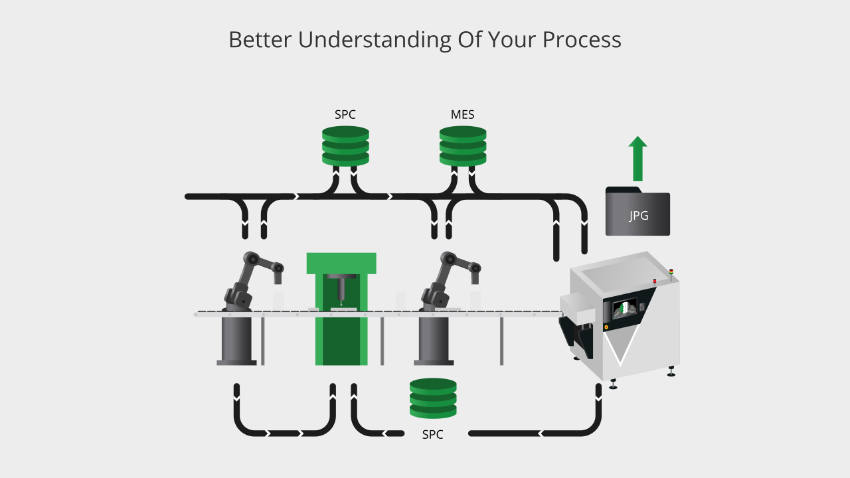
While maximizing machine performance is crucial, we ensure it’s never at the expense of reliability or operational quality. Our maintenance philosophy focuses on both preventive and corrective measures:
- Preventive: designing robust machines that run reliably for extended periods with minimal maintenance
- Corrective: planned downtime prioritized over unplanned downtime, with fast reaction times in case of unexpected issues
Our service and support scheme includes various support levels, training programs, remote operations, and spare parts programs. This approach has been well-received by our customers, who value cost-effective operations with high output.
Gigafactories don’t emerge overnight; it’s a gradual process from R&D to prototyping, pilot lines, first production line, and finally mass production. X-ray inspection plays a crucial role throughout these stages. As a trusted partner, Exacom offers solutions for each stage. We consult in each step of the way based on our extensive experience to tailor our solutions to the customer needs.
Quality: tell us something about the quality behind your products / solutions.
M.M: At Exacom, quality is paramount, since our equipment operates in inline processes. We believe that quality begins with design, and our robust system designs ensure high-quality components and equipment.
To achieve this level of quality, we follow a philosophy of standardization, reducing component variation to focus on reliable operations. We also consider the industrial maturity of components regarding operational and supply chain reliability aspects.
In addition, our systems are designed for dry room spaces with their unique requirements for materials and lubricants. Our design philosophies include:
- Design for Maintenance: minimizing downtime by ensuring easy access to maintenance areas
- Design for Integration: seamless mechanical, electrical, and electronic interfaces with other equipment or the factory.
We also prioritize software quality and AI algorithm reliability.
Rigorous Testing Procedures
Each Exacom machine undergoes rigorous internal testing procedures to ensure functions, reliability, and safety. This includes:
- Internal testing: verifying performance, reliability, and safety.
- FAT (Factory Acceptance Test): reviewing equipment with the customer before shipping
SAT (Site Acceptance Test): ensuring systems perform as agreed upon at their designated site.
Beyond that, we also perform metrology tests according to VDA 5, like measurement system analysis (MSA) or Kappa tests.
Characteristics: what important features should clients search and what features do your products / solutions offer?
M.M: At Exacom, our products and solutions are designed to meet the unique needs of modern cell production. We understand that quality is crucial in this process.
We typically see three x-ray quality gates in modern cell production:
- NDT 1: Inspects jelly rolls or stacks for relative and absolute anode and cathode positions, anode counting, and bending.
- NDT 2: Conducts inspections on assembled cells before electrolyte filling, ensuring correct stack positioning towards cans and crimping analysis.
- NDT 3: Repeats NDT 1’s inspection on assembled cells. Depending on the application NDT2 & 3 can be combined.
We recommend feasibility studies for specific cell designs and specifications to ensure optimal inspection parameters. Our experience allows us to provide guidance before a study becomes necessary.
The customers top priority is ensuring zero escapes in the inspection process, even if it means accepting some false positives (false calls). We use AI-powered solutions to optimize our processes, leveraging vast data sets beyond human capabilities. Supervised training ensures traceability for metrology results.
Exacom’s AI-powered inspections have been proven best-in-class with zero escapes and low false call rates (<1%). Our cross-correlated AI classifiers enable quick fine-tuning of models to customer-specific parameters using smaller amounts of training data.
Functionality: tell us something about ease of use, integration with other solutions or other innovative features of your products / solutions?
M.M: At Exacom, our X-ray machines are designed for seamless integration into production lines. We’re flexible in adapting to various material handling systems, as long as metallic materials don’t obstruct the space between the X-ray source and detector.
Industrial Communication: The Key to Success
To ensure a successful implementation, we prioritize industrial communication:
- Fast, Low-Latency Machine-to-Machine (M2M) Communication: Reliable data exchange is crucial for efficient production.
- Flexible Interfaces: Seamless integration with customer MES systems and image databases ensures smooth operation.
To guarantee a successful implementation, we involve system integrators early in the planning phase, ideally during the initial stages of project development. This collaborative approach enables us to tailor our solutions to meet specific customer needs.
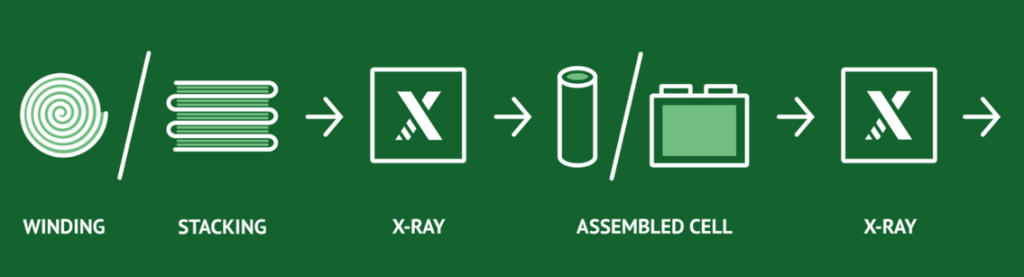
Comparison: what key features do your products / solutions have compared to others on the market?
M.M: While our solutions stand out with their distinct philosophies and approaches, we believe that other key factors set us apart from competitors. These include:
- Dedicated Project Management and Commissioning Teams: Ensuring smooth project flows and efficient commissioning.
- Ongoing Customer Support: Our worldwide service and support packages continue beyond the machine sale, throughout production operations.
Innovative Development and Customization
Cell technologies is constantly evolving, with new generations always in development. Special Developments for Forward-Thinking Customers: Enabling customers to stay ahead of the curve by leveraging cutting-edge technologies before they become mainstream.
Feedback: what was the feedback from clients about your products / solutions?
M.M: The feedback overall is very positive, especially since we speak the “battery language” of the customer, since we understand their processes and pain points. This is quite unique in the market we have been told. We are recognized more as partner than a supplier due to our strong consultancy and our ability to accompany our customers throughout their stages of evolvement. In addition is our efficient project management, our fast response times and our innovative adaptation towards customer applications highly appreciated. We have also got positive feedback in terms of good and clear communication and the fact that every team member is fluent in English makes us a partner who is easy to work with.
Are there any “buy-back”, upgrades or other opportunities available?
M.M: Our current development of business does not require such scheme yet. That might change in the future.
What purchasing advice do you have for clients in your fields of activity?
M.M: When it comes to equipment selection, it is not only about an X-ray machine alone. There are many surrounding considerations, since we are talking about industrial inline equipment. For instance: Euipment optimized for dry rooms; small machine footprints; machine quality, software quality, AI quality; metrology grade; production ready AI piplines; automation controls for M2M and MES; interfaces for transport and handlings systems; comprehensive service and support programs; strong partnerships with people who understand the industry; close communication and collaboration; Companies that can operate on tight timelines.