FTT is an engineering and manufacturing company based in Verona, Italy, specialised in producing high-quality cellulose fibre thermoforming lines for premium packaging applications. The company’s goal is to improve and promote this technology worldwide to help customers in the plastic to natural fibre transition, with a net positive impact on environment.
Established in 2014, under a substantial ownership and management change in 2021, FTT has already consolidated its market share worldwide, with high-quality and high-reliability equipment running at customers premises.
FTT aims to stand as a reference point for the development of sustainable packaging and thermoforming technologies, anticipating market demands, developing tailor-made solutions, and leading the transformation of the packaging industry.
What are the main areas of activity of the company?
FTT machines are designed to produce non plastic high-quality packaging, made of natural fibres. With the latest developments in technology, packaging made of natural thermoformed fibre is perfectly suited to any application: our customers are using our technology provide their clients with packaging for cosmetics, food and beverage, electronics, pottery, and more. In the next future we will have hot drinks cups and lids, coffee capsules and other containers made of moulded fibre.
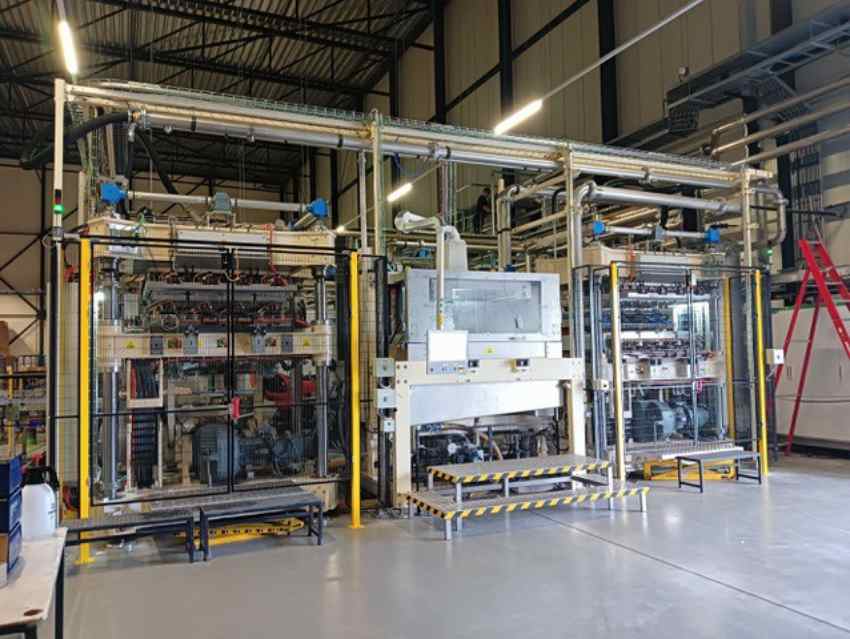
What’s the news about new products?
Innovation has always been the focus of FTT, continuous research carried on in team with our customers and with our partners has been going on since day one, and it is written in our DNA. Our R&D department is constantly looking for new materials and new technologies, to support our customers in finding the best solution for their needs.
What are the ranges of products?
Our products are fully automated natural-fibre thermoforming lines, which come in different sizes and different production capabilities, all shaped around our customer needs.
The main components of each line are:
- the pulp preparation unit, where the raw dry material (natural fibre) is pulped and mixed with water in very precise ratios.
- the forming station, where the pulp-water mixture is sucked onto a porous mould by means of a vacuum pump and shaped to form a 3D object.
- the pressing unit (thermoforming) where the object that was previously shaped in the forming unit is pressed and dried under heat, creating a rigid artifact in its final shape.
Currently a dry process machine is at prototype status in our R&D laboratory.
At what stage is the market where you are currently active?
All packaging, with focus the ones who are leading the change from plastics to natural fibre.
High level, luxury and premium products made by companies who are committed in sustaining a higher cost in the short term to replace fossil products with sustainable natural fibres and become leaders in the field of sustainable high-quality packaging.
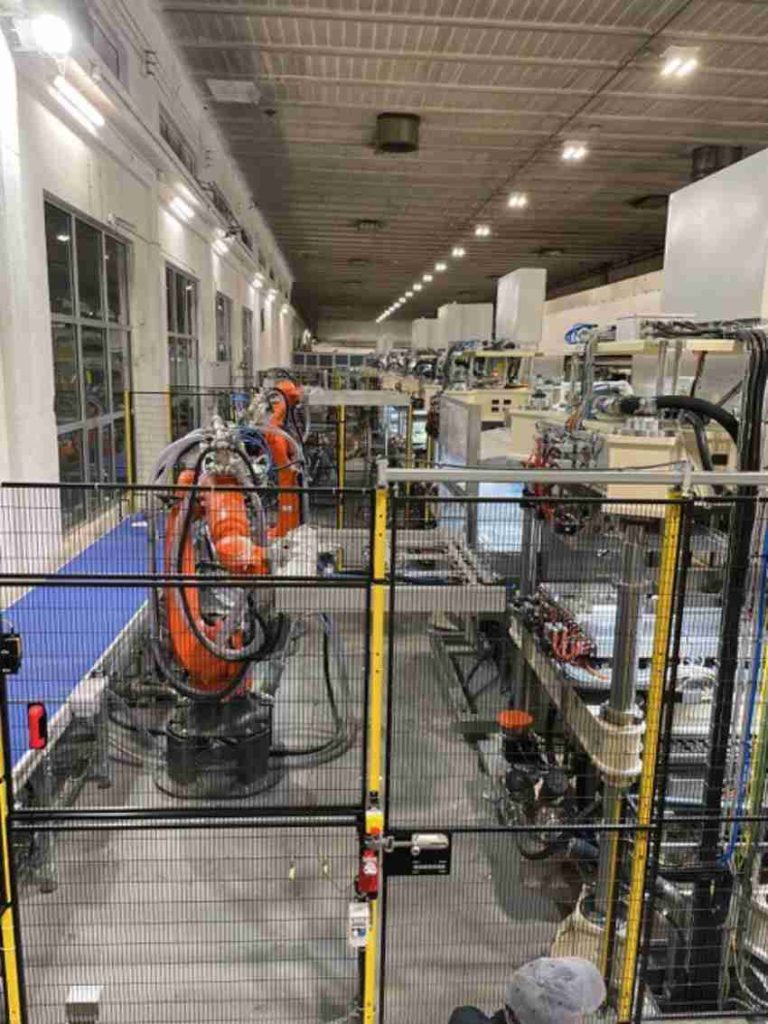
What can you tell us about market trends?
Worldwide there is a huge interest in moulded fibre products, increasing in any field: sustainable and compostable materials are more and more popular in different markets. In the short term plastic will remain No.1 material for packaging, but it is clearly evident that alternative materials, like cellulose and other natural fibres, are taking a growing market share year over year, especially in the premium segment.
What are the most innovative products marketed?
All our cellulose fibre products are innovative and studied to best fit the needs of our customers. Products can be made just of pure cellulose, but can also be composed of multi- layered natural fibres, film coated, dry processed fibres, and more technologies are coming from our R&D. Thermoformed products is a relatively young business and it is growing rapidly, with outcomes that are only to imagine.
What estimations do you have for 2023?
FTT has already three big orders to deliver and is working on several new technologies with dedicated prototypes. We are also developing new fibres with our partners, new additives, and new processes, all to meet and help our customers with their requests for new sustainable, high-quality and high-tech product. 2024 is a very challenging year!