iMFLUX is the only molding technology company that integrates game-changing processing software and machine learning with a state-of-the-art mold shop. The company provides the way to autonomous molding with a new capability to design and mold that impossible part. Their revolutionary low-constant-pressure injection molding platform works on virtually any machine, material, and mold.
Interview with Toi Clarke Jones, Vice President Sales & Business Development at iMFLUX.
Easy Engineering: Which are the most futuristic products / solutions from your portfolio?
Toi Clarke Jones: Injection Molding Software that changes the injection portion of the process from being velocity driven (machine in control) to being driven by the actual plastic melt pressure (resin and mold in control). One of the technology’s primary innovations is a feature called Auto Viscosity Adjust (AVA). AVA was born out of a necessity to handle material variations that occur in the manufacturing process. AVA addresses the challenges of injection molding PCR which until now has been an unmet need and helps to unlock circularity for plastic parts/packaging. The unique closed loop control nature of the iMFLUX technology enables real time adaptive control in ways not possible with conventional molding.
E.E: What are the characteristics of these products / solutions?
T.C.J: iMFLUX is a patented low-constant-pressure process with no flow hesitation. Unlike conventional molding, iMFLUX’s adaptive process controls pressure by varying injection velocity to pack as it fills and does not require a separate pack and hold phase. This closed-loop control is made possible with software and a single machine nozzle sensor. No additional sensors are needed in the mold.
iMFLUX is not an injection molding machine (IMM) but a technology package (software, nozzle, pressure sensor and user interface) that works on virtually any IMM. iMFLUX changes the way an IMM operates, creating a dynamic process. Instead of controlling the velocity of the injection screw, iMFLUX controls the filling process by maintaining a low constant pressure, minimizing the pressure differential across the cavity. iMFLUX with AVA then automatically adjusts the screw velocity based on the plastic pressure reading, enabling an ideal laminar flow and never allowing the flow front progression to stall or accelerate preventing shorts, flash and defects.
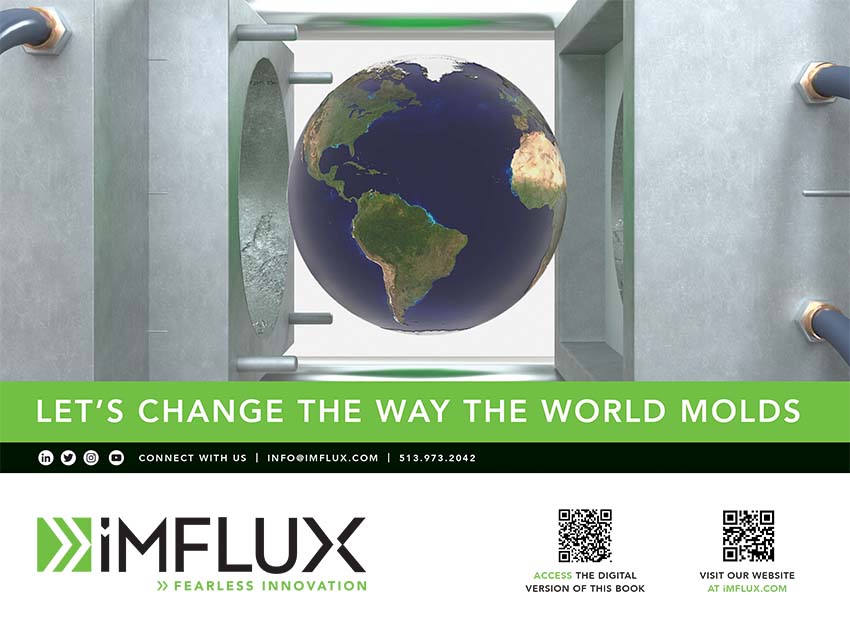
E.E: Tell us about the company’s long-term goals / prospects?
T.C.J: The target customer for iMFLUX is a molder who is dissatisfied with the status quo and open to technology as a potential solution to create better operational outcomes through greater efficiency, use of new materials, unlocking mold design constraints. We find these customers across automotive, medical, electronics, consumer products, packaging, water/sewar, etc.
E.E: Tell us about product innovation and how does it impact the future?
T.C.J: The iMFLUX Technology helps injection molders to embrace the one thing they have spent a career working to avoid…VARIATION.
One of the technology’s primary innovations is a feature called Auto Viscosity Adjust (AVA). AVA was born out of a necessity to handle material variations that occur in the manufacturing process. AVA addresses the challenges of injection molding PCR which until now has been an unmet need and helps to unlock circularity for plastic parts/packaging. The unique closed loop control nature of the iMFLUX technology enables real time adaptive control in ways not possible with conventional molding. It has become a highly valuable sustainability solution for injection molders and their customers allowing them to increase PCR content without the typical tradeoffs associated with conventional molding.
iMFLUX is providing injection molders and brand owners a scalable solution for running highly variable sustainable materials and improving the circularity of plastic.
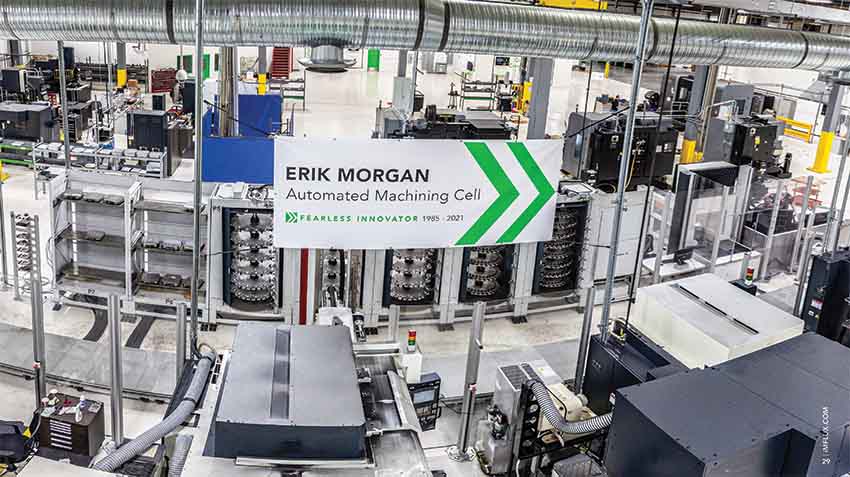
E.E: How will product innovation help the customers?
T.C.J: The unique closed loop control nature of the iMFLUX technology enables real time adaptive control in ways not possible with conventional molding. It has become a highly valuable sustainability solution for injection molders and their customers allowing them to increase PCR content without the typical tradeoffs associated with conventional molding.
E.E: How do employees shape your company’s future orientation?
T.C.J: The technology was developed from deep mastery by our employees, and continues to be shaped by what our engineers experience in the field with our customers, using the powerful algorithms to solve problems that persist (e.g. blocked cavities) and unlock opportunities that were once thought impossible (e.g. flowing thin to thick).
E.E: How does the digital transformation affect your products / business?
T.C.J: We are a software company, providing injection molders with more tools to increase machine learning and make the molding process MORE AUTONOMOUS.
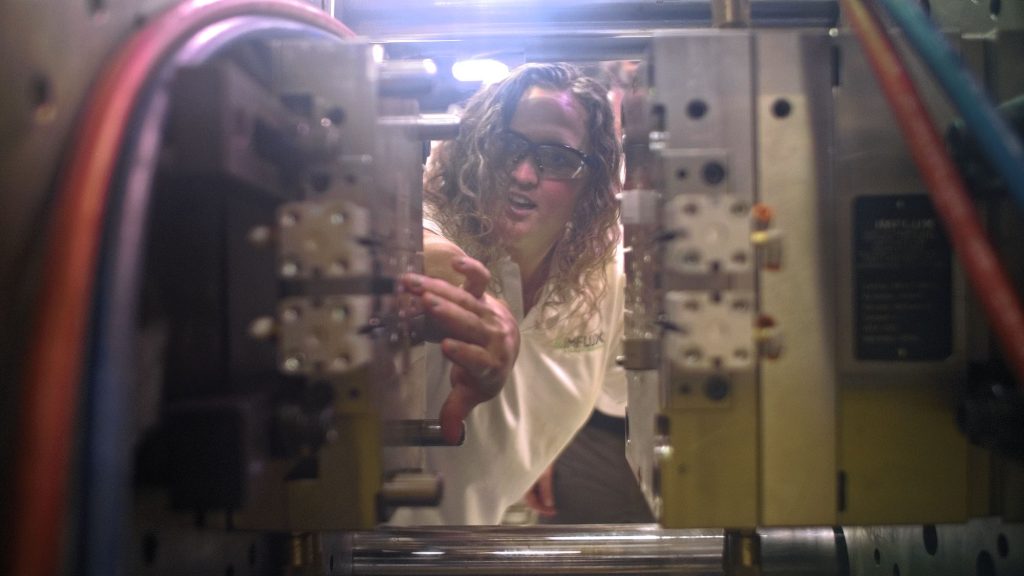
E.E: Tell us about research and development in your company.
T.C.J: Our R&D efforts involve perfecting and commercializing additional features that move injection molders along the Journey to Autonomous Molding.
E.E: How do you overcome the new challenges and this more competitive environment?
T.C.J: We focus on partnership more than competition. We partner with injection molding machine makers, resin producers, sustainability champions, etc. – all with a view that the industry’s moment is now and together we can do more to improve the world’s responsible use of plastics.
E.E: Tell us about the company’s future strategies and how will you adapt to the future.
T.C.J: The demand for our technology requires that we scale delivery faster, which creates an opportunity for new business models and new partnerships in the future.
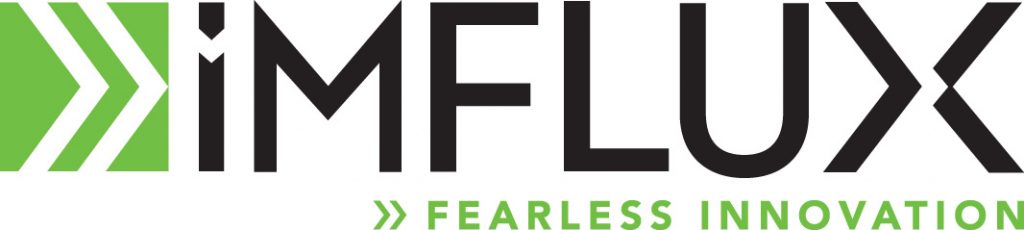