A major global maker of off-road equipment is an example of how savings, simplification, and sustainability can go hand and hand. For several years, this company participated in Cortec’s plastic recycling program, allowing them to streamline its engine parts packaging process and save significant money while reducing waste. This program’s financial and environmental benefits highlight the importance of collaboration for sustainability.
The manufacturer’s major engine facility receives a diverse array of parts – from engine blocks and heads to countless small components, sourced from dozens of suppliers across the U.S. and internationally. All components are packaged in VpCI®-126 bags that provide corrosion protection. However, a long-standing, yet outdated, practice once involved suppliers adding unnecessary oil to these bags during packaging.
This seemingly minor detail created a major inefficiency. The oil contaminated the VpCI®-126 bags and their corrugated plastic liners, rendering them unusable for recycling or reuse and contributing to unnecessary waste. Recognizing this costly and unsustainable practice, Cortec® Corporation, a global manufacturer of corrosion inhibitors, proposed a game-changing solution: eliminate the oil and implement a closed-loop recycling program.
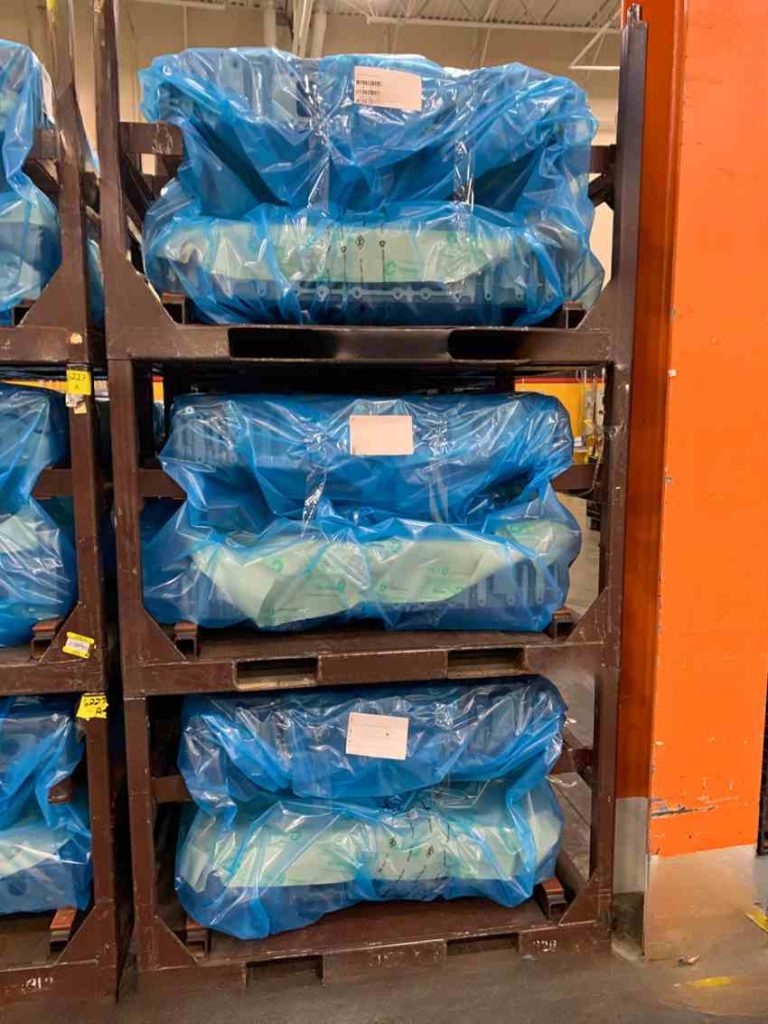
Cortec® suggested the manufacturer return the used VpCI®-126 bags to Cortec® Advanced Films plant (CAF) for reprocessing. The manufacturer embraced this innovative approach, tasking a Six Sigma Black Belt to do a thorough evaluation. Validation testing conducted by Cortec® Laboratories confirmed that the VpCI®-126 bags provided the same corrosion protection without the added oil.
From Waste to Value: Implementing a Circular Solution
The manufacturer eliminated the oil application and invested in a baler to efficiently collect the used VpCI®-126 bags. Cortec® purchased the baled plastic at market rates and covered shipping costs to its CAF recycling center in Cambridge, Minnesota, where Cortec® reprocessed these used VpCI®-126 bags into new VpCI® film products at a rate that could assure quality and performance. While establishing this recycling program presented its share of challenges, the commitment of both Cortec® and the manufacturer to sustainability and efficiency brought this circular economy to a reality.
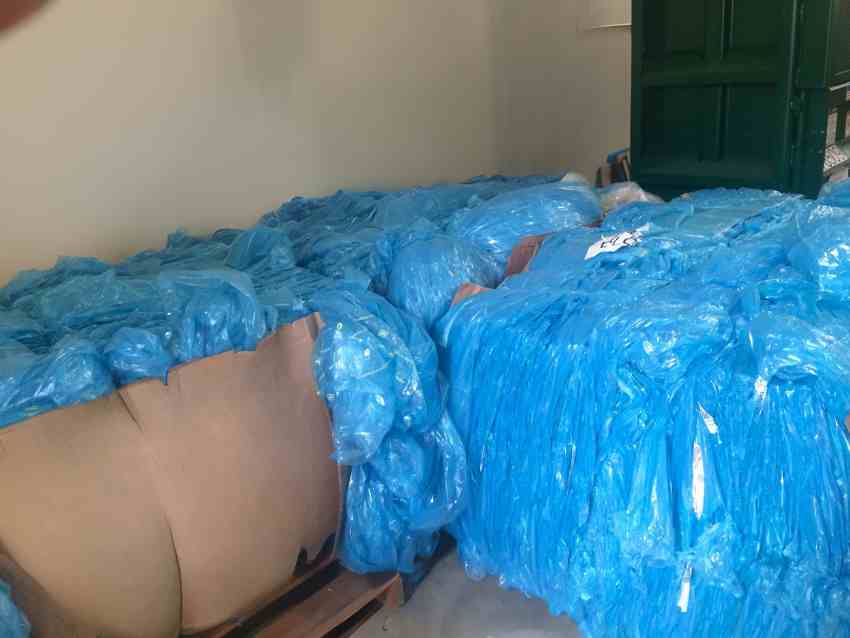
A Triple Win: Cost Savings, Safety Enhancement, and Environmental Stewardship
The results of this collaborative initiative are significant:
- Cost Savings: By eliminating the unnecessary oil, the manufacturer realized annual savings of several hundred thousand dollars.
- Improved Health and Safety: Reducing the presence of petroleum-based chemicals within the plant enhanced health and safety conditions and led to savings on liability insurance.
- Waste Reduction and Revenue Generation: The ability to reuse corrugated plastic liners and the revenue generated from selling used VpCI®-126 bags to Cortec® transformed waste into a valuable resource. The program was able to divert hundreds of thousands of pounds of plastic from the landfill or incinerator.
This successful partnership demonstrates the benefits of embracing a “circular economy” for plastics. At a time when plastic waste repurposing remains a global challenge, Cortec® established a full-circle recycling program that benefited its own operations, its customer’s bottom line, and the environment, while creating a new supply of high-performance VpCI®-126 film. for superior corrosion protection.