Atlanta Stretch Ibérica are specialists in semi-automatic and automatic pallet wrapping machines converting your end-of-line production into an efficient and fast space. Years of experience in the world of consumables and packaging machinery make the company a team ready to adapt the system to achieve your goals.
Interview with Martí Gavaldà Miracle, Marketing Manager at Atlanta Stretch Ibérica.
Easy Engineering: Which are your best-selling products / solutions?
Martí Gavaldà Miracle: The merger of Atlanta Stretch Ibérica and Comarme means that we have a complete end-of-line with one of the best automatic pallet wrappers on the market, the Mytho A, and our star case erector, the F2000 + F470, as well as more affordable products such as the SFERA semi-automatic robots and wrappers such as the EVA and the Synthesi.
The first two machines are automatic and are game changers for any type of end-of-line, product, or company. It is clear that the future of the packaging industry lies in the automation and sustainability of modern machinery to streamline processes and reduce costs, in this, these two machines are unbeatable.
E.E: Why do users choose your products / solutions?
M.G.M: They choose our products because they are the standard in innovation and quality, demonstrating this with many patented models with durability above the competition as well as a very competitive price/quality ratio.

They also choose us because being a small team, we have a lot of maneuverability, and having the support of Atlanta Stretch (Italy) greatly reduces production costs.
One of the features that our customers really appreciate is how specific the designs can be, adapting a machine to their tailor-made end-of-line.
E.E: What special features do your products / solutions have?
M.G.M: Myhto A: We have two models, one with a column and one with an arm, the only one on the market.
Arm: This is one of our most innovative patents. It adapts perfectly to any pallet height and has an electronic pre-stretch system with stretch film insertion. It also has a top cover installed at the rear of the machine, making it perfect for confined spaces.
Column: It is possible to install it with two pre-stretching heads, with a single welder, this system allows us to reach 60 pallets/hour. Its 90º entry and exit make it very adaptable to any type of end-of-line.
F2000: This is the best on the market in terms of quality/price ratio, as well as being highly adaptable. One of its great advantages is its double-adjustable modular outlet. The first module forms the box and the second module seals it, normally with adhesive tape. The advantage of this is that it can be exchanged for a module of gummed paper or any other type of sealing material, so you don’t have to change the whole machine, just the module itself.
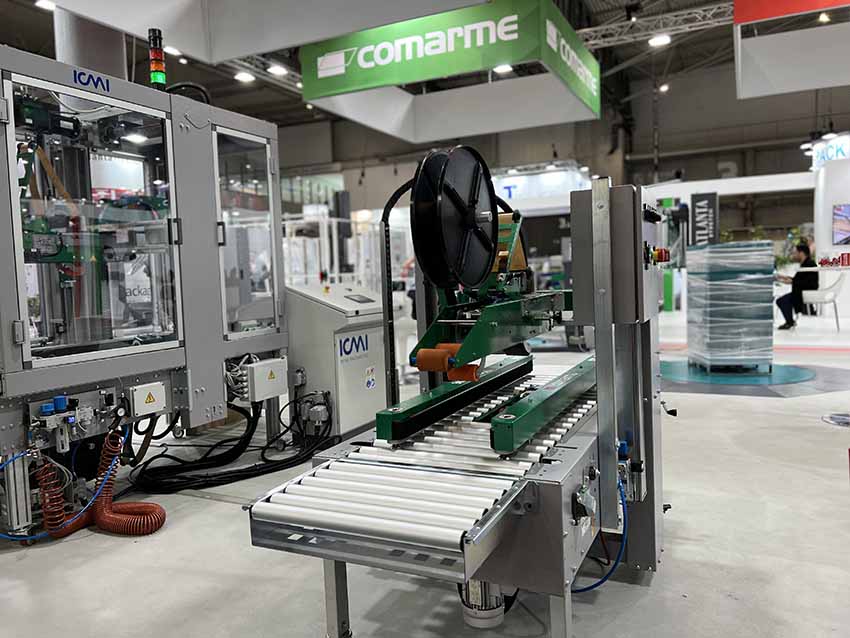
E.E: Tell us a short tutorial of how a task is done more efficiently with one of your products / solutions.
M.G.M: The biggest problem with not using our products is that the alternative is to do it manually. By automating the process, you just have to put the pallets in the packaging area and let the machine work alone.
E.E: How did your products / solutions improve efficiency for the users overall?
M.G.M: Increased Productivity: We wrap pallets quickly and efficiently, which has increased the productivity of companies. With the use of a pallet wrapper, workers can wrap pallets in a fraction of the time it would take to wrap them by hand. This means that workers can focus on other tasks, which increases overall productivity.
Reduced Labor Costs: By automating the wrapping process, pallet wrappers have reduced labor costs for our clients. With fewer workers needed to wrap pallets, we can save on labor costs and allocate their resources elsewhere.
Improved Safety: Wrapping pallets by hand can be a dangerous task. Workers can injure themselves by lifting heavy pallets or by getting tangled in the wrapping material. Pallet wrappers have improved safety for workers by automating the process and reducing the risk of injury.
Consistent Wrapping: Pallet wrappers provide consistent wrapping, which ensures that the products are securely packaged and protected during transport. This helps to reduce the risk of damage to products during shipping and can save companies money on replacement costs.
Overall, the use of pallet wrappers has improved efficiency for users by increasing productivity, reducing labor costs, improving safety, and providing consistent wrapping for products.
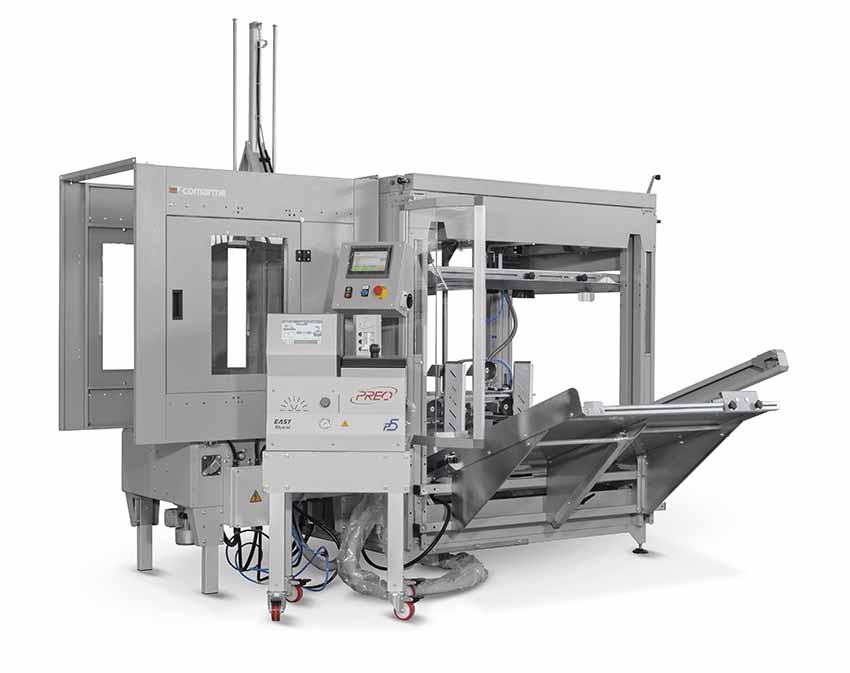
E.E: Give us some examples of projects in which your products / solutions were used?
M.G.M: The packaging sector gives us the privilege of being able to work with all types of companies and end customers. Any product that requires large-scale production needs to be palletised and packaged.
Our client portfolio includes large companies such as Adidas, Clesa, Nestlé, Shell, Bimbo and Gallina Blanca.
E.E: What products / solutions were used in these projects?
M.G.M: Case 1:
- Infeed section for pallet truck with elevator
- Three sections of accumulated rollers
- Mytho A with automatic column and cord system
- Section with integrated weighing system
- Three accumulation sections
- Unloading section with pallet lift for pallet truck
Case 2
- Case erector F2000
- B520 HM case sealer with Nordson hot-melt glue fuser
- Roller section for product insertion
- Top sealer F470 HM with Nordson hot-melt glue fuser
E.E: What was the feedback from users?
M.G.M: The first thing you might think about with these projects is that they might take a long time or not come out perfectly. The usual feedback from our customers is that the objectives were met, expectations were exceeded and that the treatment was friendly and familiar, providing immediate solutions to any specific problems that might arise.
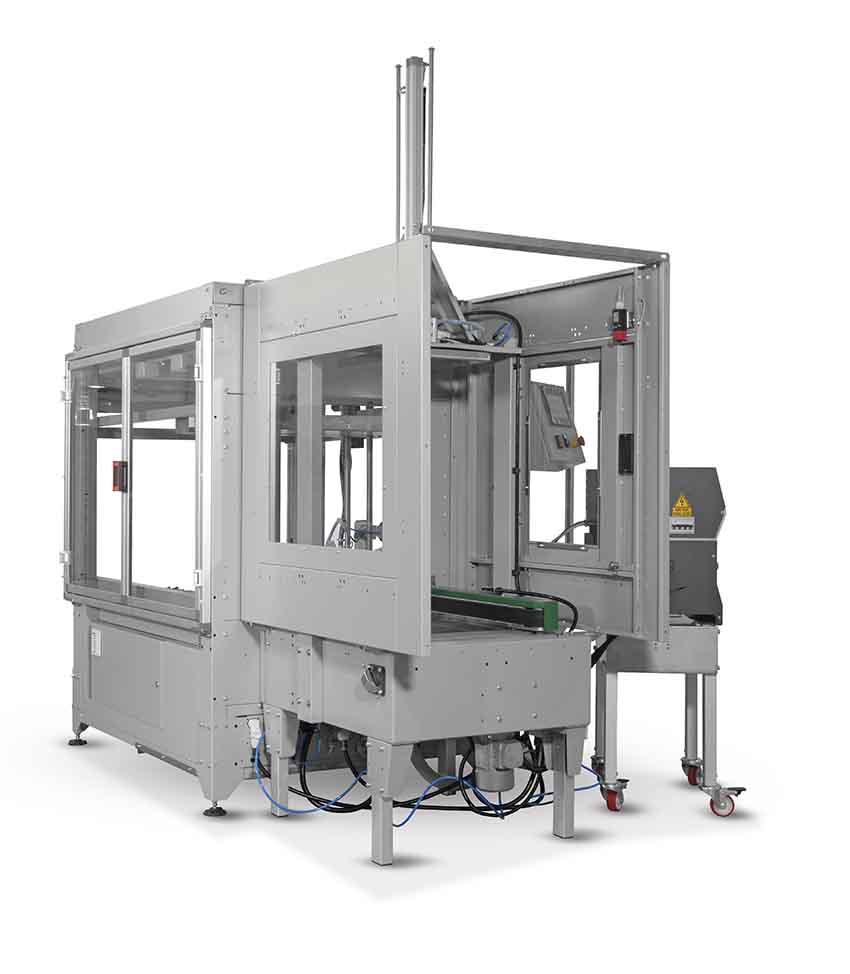
They often tell us that the quality/price ratio is very good and that they like to work with leading brands as there are always spare parts for the 24/7 technical service we offer.
E.E: How can users work more sustainably with your products / solutions?
M.G.M: The key to success for any company is to do the job specifically tailored to their needs. If you study your products and their qualities you can better plan what type of machinery is best suited to your format or packaging.
The type of head you need, especially pre-stretch, will help you save on film, radically reduce your carbon footprint and excess waste and reduce production costs.
Once the machine has been decided, designed and adapted to the needs of the company, it is all a matter of choosing the programs to improve the stability of the load.
If all these variables are met to perfection, there is no doubt that the sustainability and efficiency of our products increases to 100%, and that is what we specialize in.
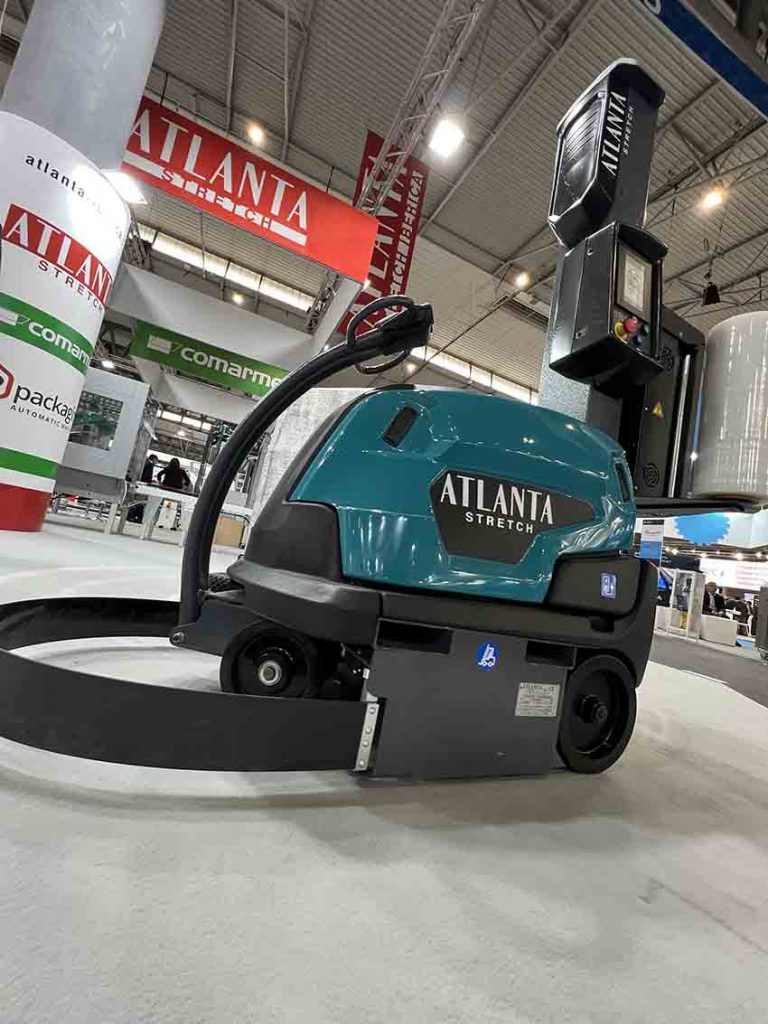
E.E: What are your forecasts for the first half of 2023?
M.G.M: So far, we have started the year very well, the problem that is noticeable is that it is not going to be a very favourable year for the sector in general. Talking to our competitors we realise that there are some companies that are at 40% of sales compared to the previous year.
It should be noted that in Spain a tax on plastic has been approved, making it difficult to sell as the price has increased by €0.45/kg.
For the time being, we will be cautious and we will speed up some commercial strategies to increase our presence in Latin America and grow internationally.