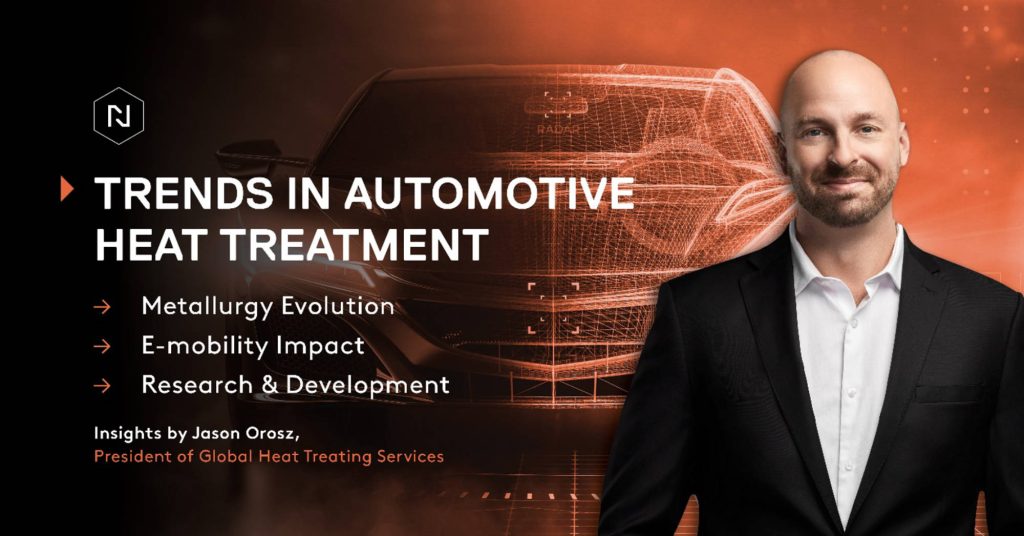
INSTALLMENT 1: EVOLUTION OF HEAT TREATMENT IN THE AUTOMOTIVE INDUSTRY
The automotive industry stands at the crossroads of evolution. As consumer demands shift and the industry further embraces zero-emissions and sustainability, heat treatment processes crucial for ensuring component functionality and durability are undergoing a transformation.
In this insider’s piece, Jason Orosz, President of Global Heat Treating Services at Nitrex, examines six forces shaping the heat treat landscape for automotive manufacturing.
- Metallurgical Evolution: Nitriding and Nitrocarburizing Reshape the Norms
In automotive part manufacturing, upstream processes focus on facilitating machining and providing basic strength, ductility, and dimensional stability. Downstream processes concentrate on improving the durability and longevity of substantially or completely finished products.
While plating methods are often used downstream, there is a shift in the rise of advanced surface treatment processes like low-temperature nitriding and ferritic nitrocarburizing. These eco-friendly treatments herald a departure from conventional and less sustainable plating methods. For example, chrome plating of brake systems is environmentally and health-wise harmful due to carcinogenic hexavalent chromium waste. That’s why many OEMs and tier-1 manufacturers now choose controlled nitriding and nitrocarburizing for their environmental goals.
Unlike plating, which simply coats the metal part, nitriding and nitrocarburizing represent a metallurgical evolution of the steel itself. This transformation process at the surface ensures increased durability without the environmental drawbacks associated with processes like chrome plating, underlining the intrinsic advantage of nitriding that “nothing can fall off or fail catastrophically.”
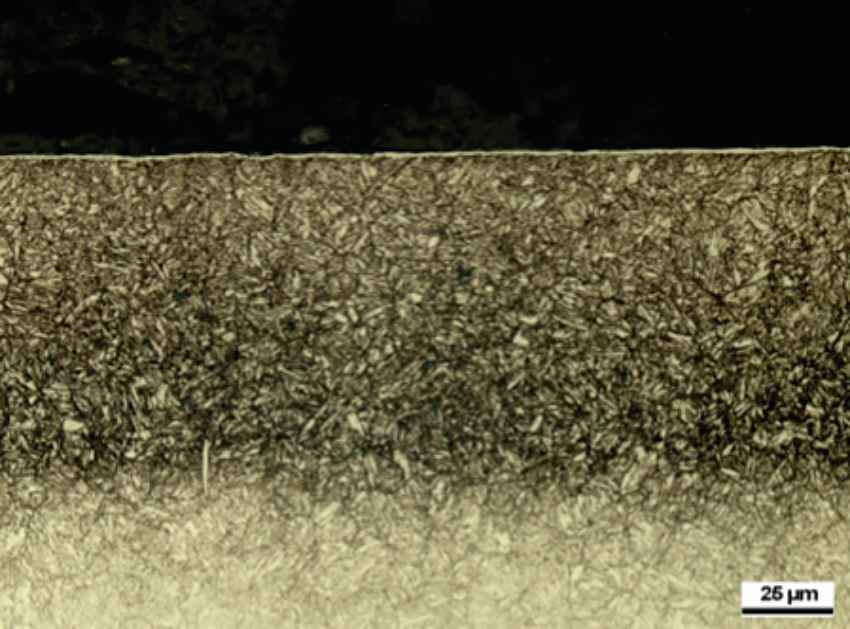
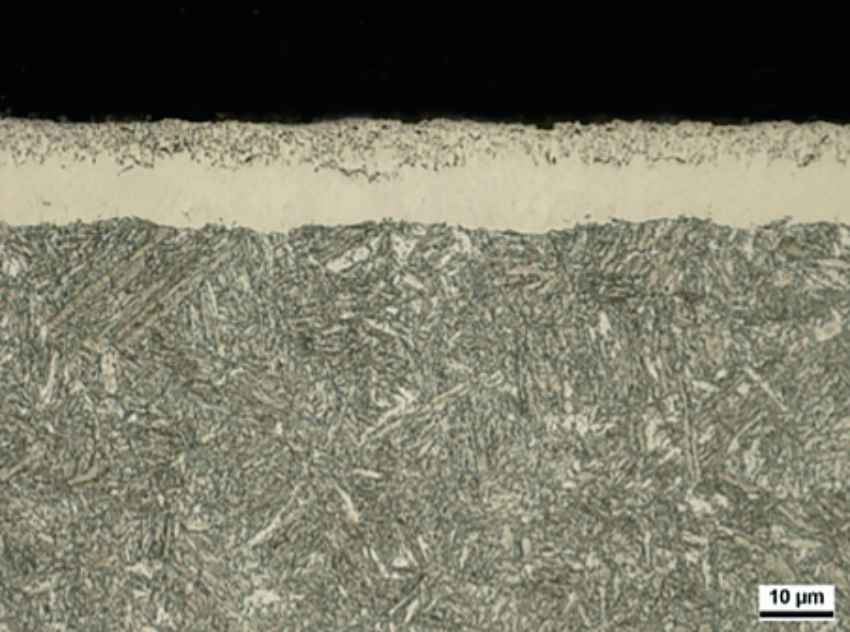
- E-Mobility Impact: Navigating Heat Treatment Challenges in Electric Vehicles (EVs)
As the automotive landscape transitions to electric vehicles, a shift in component designs and associated heat treatment processes becomes imperative. While the overall number of components requiring treatment may decrease due to simplified powertrains, the weightier nature of EVs necessitates additional heat treatment in specific areas like suspension, braking, and steering systems.
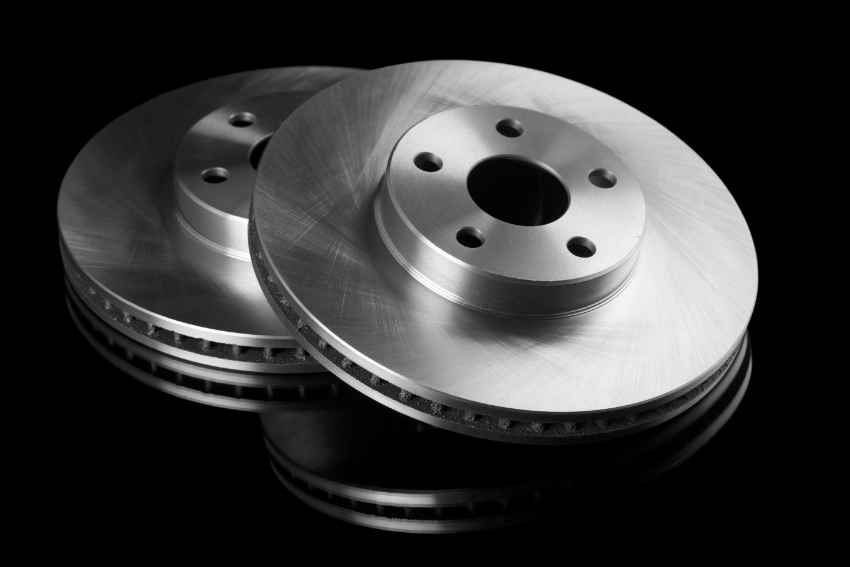
Moreover, the transition to electric vehicles introduces challenges related to particle emissions. Stringent requirements, as outlined by Euro 7 regulations, focus on reducing particle emissions from sources such as brake rotors. With regenerative braking systems potentially accelerating corrosion on rotors, innovative solutions like Smart ONC®, an advanced nitrocarburizing process with post-oxidation, are gaining traction to meet environmental standards.
- Research and Development at the Helm of Efficiency and Sustainability
Nitrex’s commitment to innovation is evident in its extensive R&D operations across North America and Europe. As both a manufacturer of heat treatment equipment and a commercial heat treater, Nitrex has achieved remarkable advancements in efficiency and sustainability.
Nitrex continuously looks to increase process efficiency and sustainability and has done so by 100 to 150 percent over the last 10 years. The development of new sensors and control systems has allowed the company to push the envelope of the types of surface layers it can produce, improving quality and performance, and often surpassing salt spray fog testing, like the ASTM B117, or cyclic corrosion testing operations favored by many automotive OEMs.
Installment #2, featuring insights on Sustainability, Strategic Decision-making, and Technical Partnership, will be available for reading on {date}.
* This article is drawn from the insights shared by Jason Orosz, President of Global Heat Treating Services at Nitrex, in a podcast broadcasted in July 2023. It offers a strategic perspective on the dynamic changes shaping the future of heat treatment in the automotive component industry. If you are interested in listening to the podcast, visit https://www.nitrex.com/en/podcast-automotive-heat-treatment-expert-insights/.
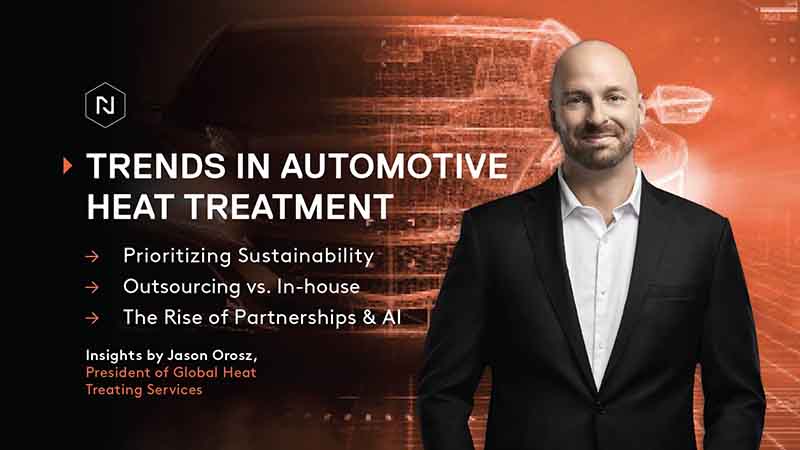
INSTALLMENT 2: NAVIGATING SUSTAINABILITY AND TECHNICAL INNOVATIONS
Installment 2 delves into the transformative landscape of heat treatment within the automotive industry. Building upon insights from Jason Orosz, President of Global Heat Treating Services at Nitrex, in the first installment, this continuation highlights the industry-wide shift towards sustainability and the growing significance of technical partnerships and Artificial Intelligence. Join us as Jason discusses how heat treatment is evolving to shape the future of the automotive industry.
- Sustainability Driving Industry-wide Change
Over the decades, consumer expectations for consistently higher standards in quality, performance, and cost have driven OEMs and car manufacturers to demand enhanced processes from their suppliers. For heat treaters, this translates into the need for tighter dimensional tolerances and more exacting metallurgical requirements, contributing to the continuous pursuit of excellence.
Today, a notable shift is occurring, placing a growing emphasis on sustainability across the supply chain. While suppliers are yet to establish specific targets, Nitrex observes a commitment to improving environmental footprints, suggesting the forthcoming establishment of precise goals as the industry defines a baseline for common surface treatments.
While eco-friendly processes like nitriding and nitrocarburizing lead to enhanced repeatability and sustainability, this next-generation impetus has fostered further advancements in process control, cleanliness, traceability, and efficiency. The latest hardware and software innovations enable more resource-efficient use of process gases and energy, minimizing environmental impact. The enduring commitment to quality, now intertwined with a growing emphasis on sustainability, is shaping the manufacturing landscape of automotive production.
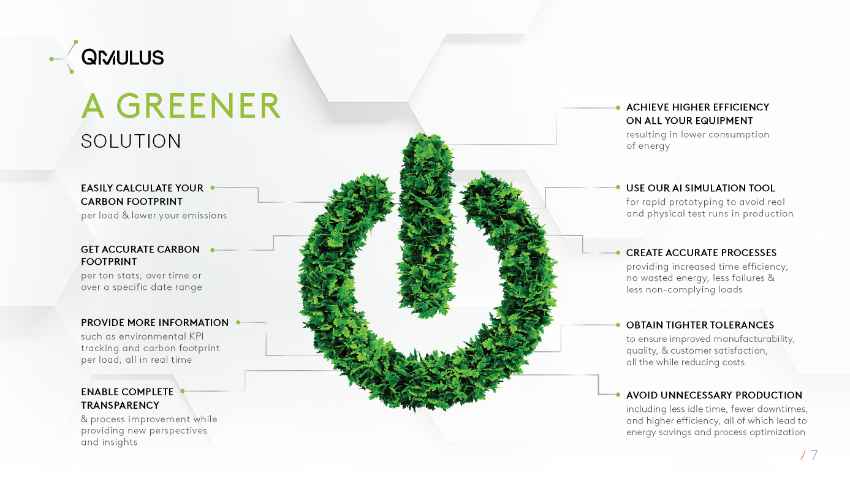
- Strategic Decision-making: Outsourcing vs. In-house Capabilities
In the evolving landscape of the automotive industry, OEMs and component manufacturers grapple with whether to outsource or maintain in-house control. During uncertain periods, the prevailing wisdom for many is to retain minimal in-house capability.
Navigating the balance between outsourcing heat treatment work and investing in in-house equipment is a delicate dance. Nitrex observes a growing demand for heat treatment equipment, particularly in brake rotors, where the appeal of maintaining control over processes during the deployment of new approaches is evident. However, as specific processes become standardized across components, a shift towards outsourcing emerges. This strategic move enables manufacturers to redirect their focus to unique expertise, often centered around component design. Moreover, when space constraints become pivotal, manufacturers concentrate on their core strengths and outsource other surface treatment work. Given the significant investment in deploying equipment, manufacturers lean towards seeking third-party assistance, especially in well-established markets.
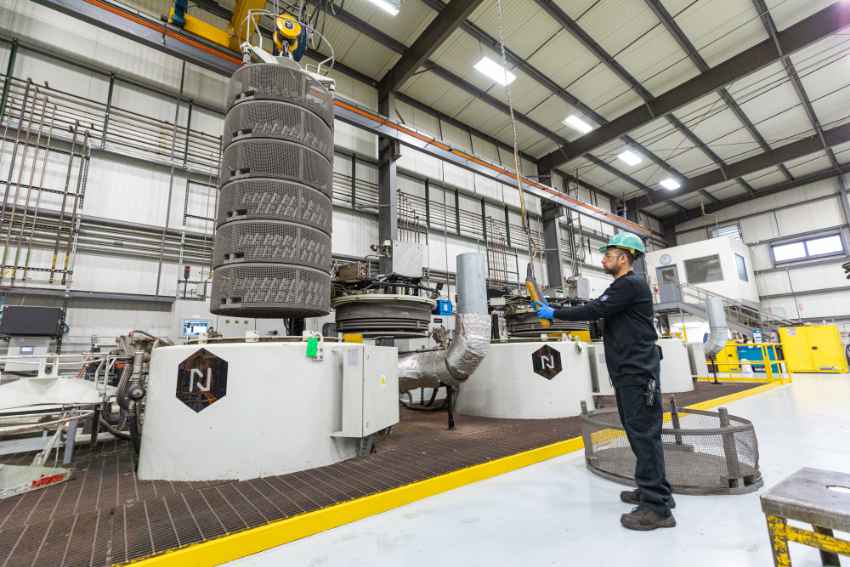
- Technical Partnerships and the Dominance of Artificial Intelligence
In the dynamic automotive industry, collaborations stand out as a cornerstone, with parts suppliers strategically forming technical partnerships with major tier-1 car manufacturers. These partnerships grant part suppliers increased influence over component design and production. Nitrex recognizes the vital role of these collaborations, acting as pivotal bridges to address the shortage of skilled professionals with metallurgical data expertise in heat treatment.
This trend is also propelling the industry towards embracing artificial intelligence and machine learning, as with Nitrex’s substantial investments in QMULUS. This new IIoT platform utilizes machine learning and cloud computing to analyze past heat treatment recipes, constructing a predictive model for achieving quality outcomes. It can be connected to all the key treatment furnaces and supporting equipment, ensuring strict compliance with regulatory frameworks and allowing artificial intelligence notifications for any deviations from predetermined outcomes.
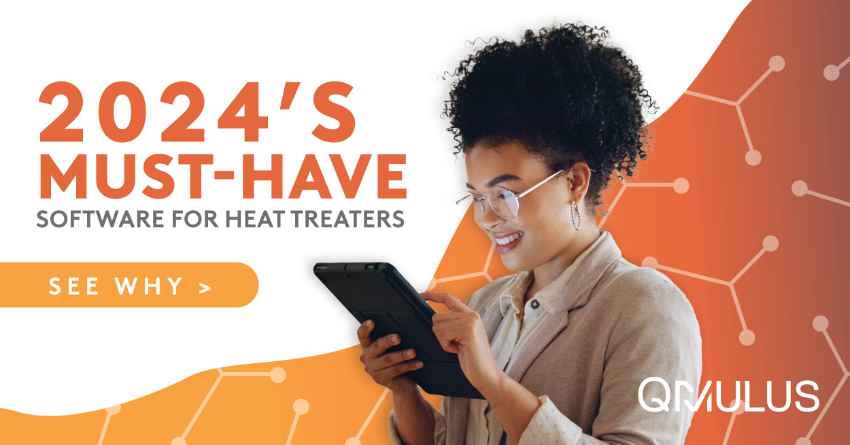
Nitrex’s next evolutionary step in digitalization involves optimizing data utilization in machine learning and cloud computing, pushing the boundaries of sustainability and repeatability. Analyzing and monitoring process control with these tools will drive the next waves of improvements and efficiencies in the industry and help lower the carbon footprint associated with heat and surface treatments.
Missed the foundational insights on metallurgy evolution, the impact of e-mobility, and the latest in research and development discussed in Installment 1? Read the first installment here.
* This article is drawn from the insights shared by Jason Orosz, President of Global Heat Treating Services at Nitrex, in a podcast broadcasted in July 2023. It offers a strategic perspective on the dynamic changes shaping the future of heat treatment in the automotive component industry. If you are interested in listening to the podcast, visit https://www.nitrex.com/en/podcast-automotive-heat-treatment-expert-insights/.