Studio Adaptive Skins was founded in 2018 by designer Jef Montes. Adaptive Skins is a textile architecture studio based in Arnhem with a strong emphasis on responsive materials. A new approach on creating shape within zero waste producing materials, rather than the conventional cutting patterns out of 2D fabric. The materials are applied on the human skin but also connected and experimented to the structure of a building and interior.
Interview with Jef Montes, Creative Director & Innovation Production Developer at Studio Adaptive Skins.
Easy Engineering: A brief description of the company and its activities.
Jef Montes: Our studio is based currently in Arnhem/The Netherlands, but we work across all Europe. Via Adaptive Skins we work on research and development projects that evolve around the systematical innovations, which are currently at the horizon of global change towards more sustainable producing textile and fashion production chains.
E.E: What are the main areas of activity of the company?
J.M: The labels Adaptive Skins and Arca Sphere are indirectly connected with each other, meaning that these two labels have a constant organic flow within the fields of: material sourcing, yarns and filament producing, textile development and fashion production. As an innovation production developer, I report on what I learn from what the current challenges within textile and fashion production chains are, and what is needed to make these systems more sustainable. Most of the time I make the bridges between several partners that contribute to the scope of the European Commission R&D projects. Next to that I also have the opportunity to test these R&D final report results via launching fashion collection pilot projects. I exhibit these capsule collections in Paris, at tradeshows such as for example TRANOÏ, the official tradeshow partner of Paris Fashion Week. Via these platforms I inform buyers about the potential of investing in sustainably produced collections, because in the end the buyers can have a leading role in contributing to the global demand on sustainable materials and production chains. If the buyers keep buying collections that are not really produced sustainable, it will just simply keep harming the environment and create backlash towards what is demanded via global climate summit leaders. Because there is a difference between just buying a textile that has a green label on it, while the actual change has to contribute within the entire chain. Not only buyers have to realize this, but fashion designers in general need to also invest more and more into where they get their materials from, and how this affects the final product from a sustainable point of view. The change needs to happen throughout all the steps between micro to macro. It’s a slow process, but with each step we can create one forward positively. The goals of Adaptive Skins and Arca Sphere match parallelly with the global demand on sustaining our current production chains within the textile industry. As most of us already know, the fashion industry is the second most polluting industry currently on our planet. This needs to change! Our aim is to contribute in a positive way and to play an important role in creating a more sustainable future.
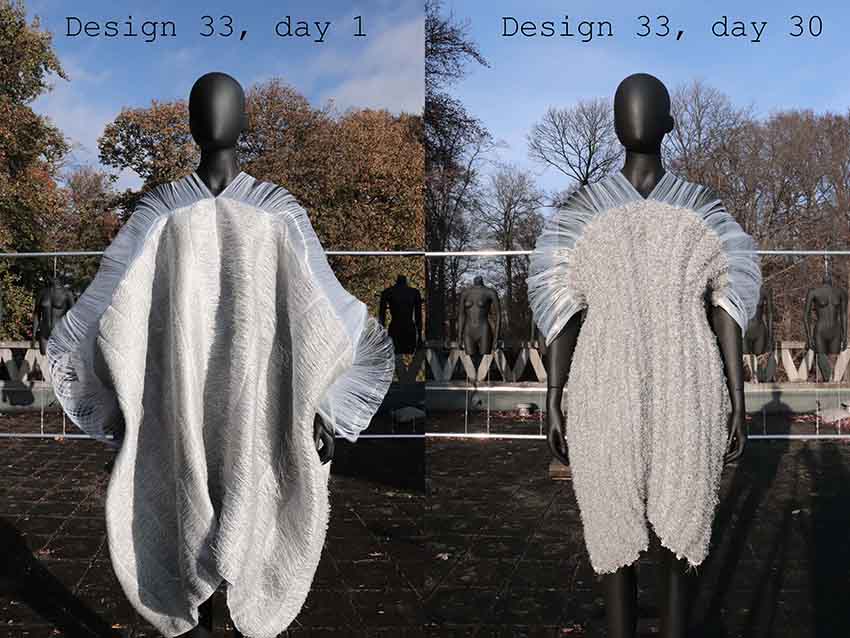
E.E: What’s the news about new products?
J.M: Via European Commission Horizon 2020 project Re-FREAM I was able to work in several tech hubs across Europe. We worked via interdisciplinary teams consisting of: scientists, chemists, technicians, product developers and designers. The goal was to create innovative shapeshifting yarns and filaments, in order to produce zero waste produced fashion garments. The Adaptive Archi-Filament was created in the labs of Aitex Textile Institute Alcoy, Empa federal materials science laboratories St.Gallen and Wk+ @ Johannes Kepler University Linz. The textile blueprints were developed and produced at TextielLab Tilburg. The idea of this experiment was to create a natural process in collaboration with nature. Since the sea level water peaks are rising globally, I wanted to design a creative direction around the topic rainwater. The melting and shaping process of a fashion garment that is manufactured by nature. These initial experiments and final outcomes also opened doors to commercial adaptations. It’s important to mention the essence of what started as a disruptive idea with an artistic point of view, and how this initial road also allowed us to grow towards industrial application scale products. Most of the reactive yarn and filament prototypes that we developed via Adaptive Skins are still within the Lab Scale spectrum, but during the development of my fashion collection for Arca-Sphere I was able to get my hands on a biodegradable PLA multi-filament. Via Aitex it was possible to introduce this yarn as the first industrial application scale product for Adaptive Skins. So, currently Adaptive Skins is offering this product commercially, and we are able to provide large scale demand orders. The added value and benefit of this product is that it’s made from food industry waste, so it’s a sustainable biodegradable product.
E.E: What are the ranges of products?
J.M: The range of products via Adaptive Skins are biodegradable PLA multi filament bobbins, and also bio compostable PHD multi filament bobbins.
The PLA materials are made from corn starch and the bio PHB variant materials are created by bacteria. The bio PHB multi filament quality has the potential to dissolve in the nature without harming the environment, meaning that it’s completely compostable. More information and specifications about these filaments can be found on the website of Adaptive Skins. Besides that, these bio filaments are also produced to create the textiles that I apply within my fashion collections. The range of products for Arca-Sphere currently within this stage are:
skirt, top and dress. The available sizes are: S, M and L. The colors available are: raw white and black dyed variations. The black pigment is produced via Nano Nebulization technology, which reduces the water use over 70%. These processes and quality materials contribute to new sustainability standards. We will keep improving all these elements more and more in the nearby future.
E.E: At what stage is the market where you are currently active?
J.M: Currently I am almost wrapping up my innovation production collection via Search For Fashion, which is an R&D project launched via European Commission Cosme platform. The products are marketed at the mid-scale to mid-high segment. Via Arca Sphere we currently can only accept a specific amount of minimum quantity orders from exclusive boutique buyers. For large-scale commercial orders we are still orienting to potential partners that can develope products to the label standards.
But we are sure that with time we will find good matches across Europe.
We need to grow step by step, that’s also part of the reason why we are launching one set of clothing design each season, because we don’t feel the need to produce an entire wide range of clothing. This will also not be even possible via our brand vision, because we map the entire process via the making of each specific clothing item. It takes a lot of time, love and care to unravel all these steps via for example qr codes and online platforms. Step by step we will expand an entire non seasonal wardrobe via the Arca-Sphere archive, sharing each story on how the designs have been developed.
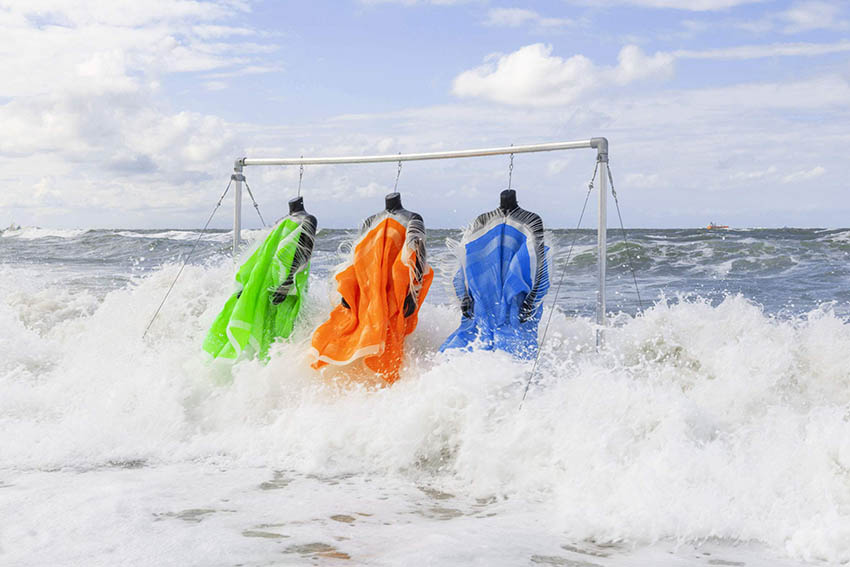
E.E: What can you tell us about market trends?
J.M: The market trends throughout the textile industry have been presented very beautifully at the Heimtextil Messe in Frankfurt this year! My fashion manufactured by rain project was exhibited at the Hyper Nature expo. This expo showcased the industry trends with colors such as fluorescent magenta and platinum green, but also an interesting overview of new techniques and innovations surrounding the topic of nature in its whole. Projects that are inspired by nature, and also projects that collaborate for example with natural elements. For me personally it was lovely to have my rain and sea project exhibited at HeimTextil, because these artistic processes helped me to generate curiosity with the expo visitors. The visitors from HeimTextil actively came to search for my booth at the TechTextilMesse Frankfurt, which is another amazing international fashion and textile tradeshow in Germany. I was happy and lucky to have witnessed this interesting combination of how artistic works can contribute positively towards commercial revenues via Adaptive Skins filament and yarn products.
E.E: What are the most innovative products marketed?
J.M: In my opinion the most innovative products marketed are the ones that have the potential to sustain the textile and fashion industry in an environmentally friendly manner. I personally think seaweed and algae are interesting from a material point of view. For example, Algiknit materials have the potential to be converted into industrial applicable quality yarns, and this will be really promising if such results can be implemented throughout commercial production scale. Besides that, textile production wise I think the knitting industry has a huge innovation potential, because knitting techniques are infinite, and can also produce any kind of form pattern without creating any waste. I love this!
E.E: What estimations do you have for the rest of 2022?
J.M: The year 2022 is almost finished by now, but I do foresee that the year 2023 will lead towards the commercial road for my company. Since we have backed up several R&D projects throughout Lab Scale, we are certainly secure to launch a few strong signature products that will be available via industrial application scale. We are looking forward to market our lines via Adaptive Skins and Arca Sphere. At this moment we are also finalizing a new Haute Couture knitwear line, that has been developed over the last year in collaboration with an amazing knitting Parisian technician, named Damien Semerdjian. This new Haute Couture line will be available on the market medio 2023.