AMAZEMET is a Warsaw University of Technology (WUT) spin-off developing technologies supporting 3D printing from metals, creating a production line “from raw materials to finished product”. It has a unique business model that combines sales of its products and IP licensing for new market development. The main drive for developing ultrasonic atomization technology was the limited number of commercially available powders for Metal AM.
Interview with Bartosz Morończy, Application Engineer at AMAZEMET.
Easy Engineering: What are the main areas of activity of the company?
Bartosz Morończy: AMAZEMET’s main activity is the development of equipment that allows for a complete and consistent process of developing new metallic materials and manufacturing components through 3D printing. Our primary focus is on development and supply of rePowder device for production of metal powder with tailored chemical compositions and high quality in 3D printing. Those qualities are high sphericity, low level of impurities, and a narrow range of particle distribution unavailable on the market.
Other activities are devices for post-processing: inFurner – compact high vacuum furnaces for heat treatment to alter the mechanical parameters of the printed material and safeEtch – technology for the automated removal of support structures, enabling more flexibility when designing components for printing, as well as scaling up metal 3D printing production.
Our equipment and experience give us a unique position as a valuable partner to many R&D projects concerning the development of new materials for metal additive manufacturing.
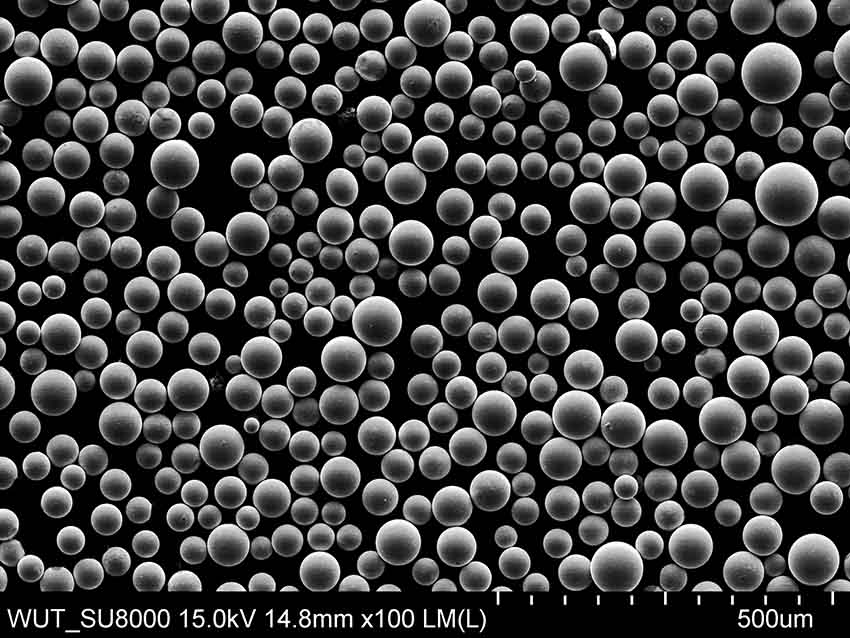
E.E: What’s the news about new products?
B.M: Since last year we have improved the productivity of the rePowder ultrasonic atomizer, and its ease of use. We introduced automatic wire and rod feeders with improved materials ensuring more continuous atomizer operation. We develop a new process for precious and rare earth materials to prevent contamination. In the near future, AMAZEMET will be able to work with an additional form of feedstock material and introduce a new melting source, expanding further the capabilities of ultrasonic atomization.
In the case of our post-processing products, we expanded the size of our processing chambers, enabling more.
E.E: What are the ranges of products?
B.M: AMAZEMET’s product range consists mainly of 3 devices:
rePowder device – powder production of new 3D printing alloys and materials recycling by atomization – primary customers are universities and R&D institutes. The rePowder device allows users to obtain the highest quality powder on a laboratory scale, regardless of the initial form of the material In the case of high-value materials precious metals, titanium powder production using rePowder is characterized by lower costs than other methods. 4 patents and 8 applications protect the solution.
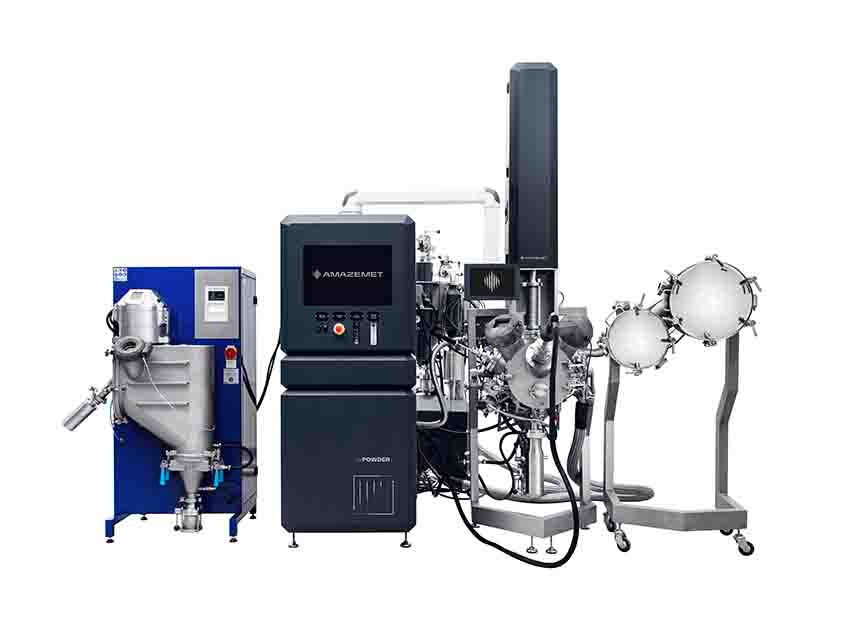
safeEtch device uses technology that eliminates labor and extensive postprocessing and automates the support removal, as well as polishes parts with complex geometry The technology is based on an ultrasound-assisted chemical reaction, and it is used in routine by our partners. It allows mass finishing for PBF titanium implants – primary customers are implant manufacturers and dental clinics. Advantages – automation of the most expensive processing step, enables mass-production of small parts, ASTM B600 complaint. The technology uses the patent in force and three applications.
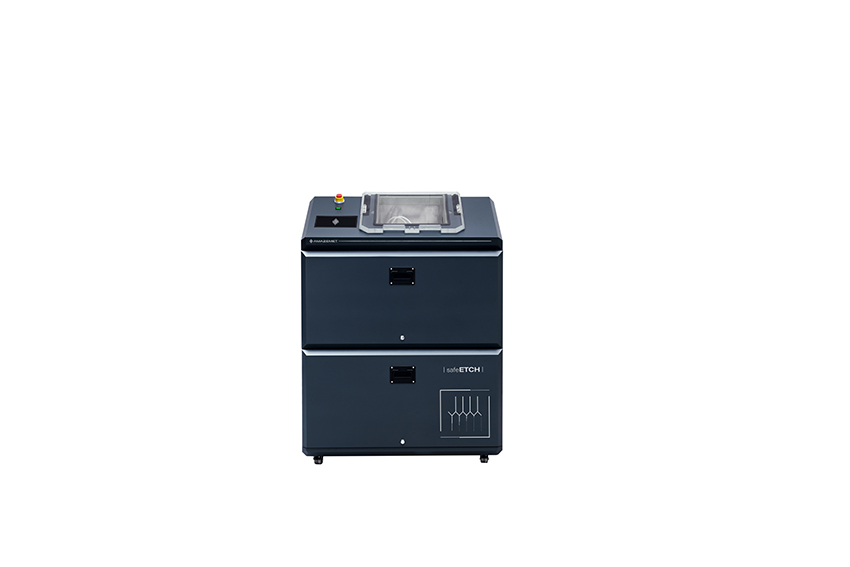
inFurner high vacuum furnace complementing the post-processing of 3D prints. AMAZEMET created a series of vacuum furnaces with a relatively small working chamber and an attractive price. The goal was to make a comprehensive solution that does not require additional infrastructure for specialized units using 3D printing technology.
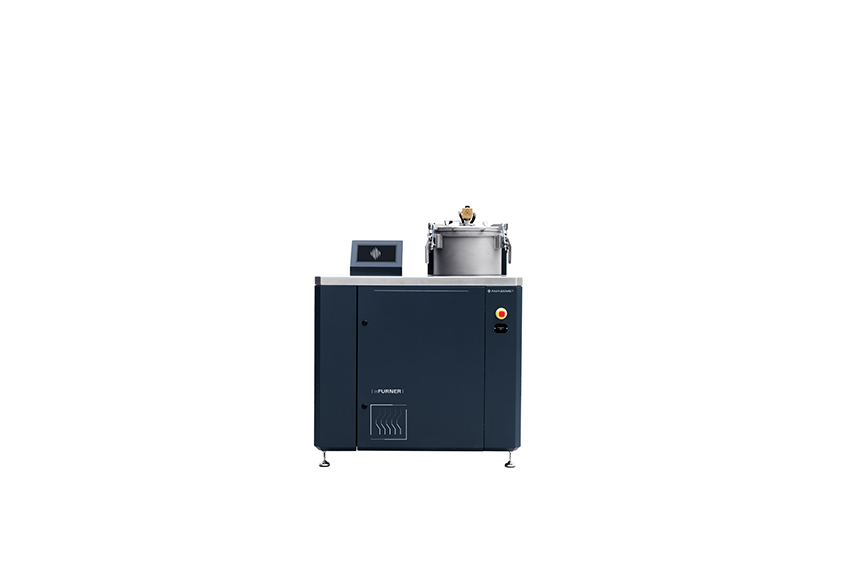
Apart from the mentioned devices, AMAZEMET offers custom engineering in metal additive manufacturing, materials characterization and R&D, and vacuum equipment.
E.E: At what stage is the market where you are currently active?
B.M: Ultrasonic atomization is an upcoming market exploiting the current industry gap in powder production. AMAZEMET is globally the leading supplier of ultrasonic atomizers and is in the process of raising awareness about the technology, and its possibilities. Possible customers are all the universities, R&D institutes, and departments interested in materials development for additive manufacturing. Other clients would be people interested in atomizing precious and rare metals, which are usually not feasible to atomize by using industry-standard gas atomization technologies.
E.E: What can you tell us about market trends?
B.M: Current market trends in the additive manufacturing market revolve around developing specialized tools supported by Ai to optimize the shape of printed parts, actively control the printing process, and develop new materials explicitly designed for additive manufacturing.
AMAZEMET’s contribution to those trends would be that the rePowder device is designed to hasten the process of new material development by allowing the testing of multipower different powder compositions.
On the other hand, the safeEtch device allows for the large-scale post-processing of even the most complex shapes designed by the Ai algorithms.
E.E: What are the most innovative products marketed?
B.M: rePowder and safeEtch – are both unique and innovative products. Technologies used by these devices are patent-protected and open whole new possibilities in the areas of new materials development for metal 3D printing, and printing scalability and final product quality.