Flash Battery, with HQ in Reggio Emilia, Italy, designs and manufactures lithium batteries for industrial machines and electric vehicles with moderate production volumes and strong needs for customization.
Since 2012, Flash Battery designed and produced more than 15.000 lithium battery packs, studied and customized over 500 different battery models and provided more than 300MWh in several applications including industrial machines and electric vehicles.
Interview with Marco Righi, CEO and Founder of Flash Battery.
Easy Engineering: A brief description of the company and its activities.
Marco Righi: Flash Battery are today installed in more than 54 countries and are daily and automatically monitored by a proprietary remote-control system, the Flash Data Center.
Flash Battery is the most sold lithium battery in Italy that recharges the fastest and requires no maintenance.
But how are we born?
Our business story is a rather special one, because it started in… a garage!
My father had a company that produced high-frequency battery chargers, and given my great passion for electronics, from the age of fifteen I was hired by the company every summer to help out in the repair department (it was the perfect job to learn the rudiments!). My spare time, instead, was spent with my friend and current partner and CTO Alan Pastorelli, building control units to sync strobe lights to music during parties.
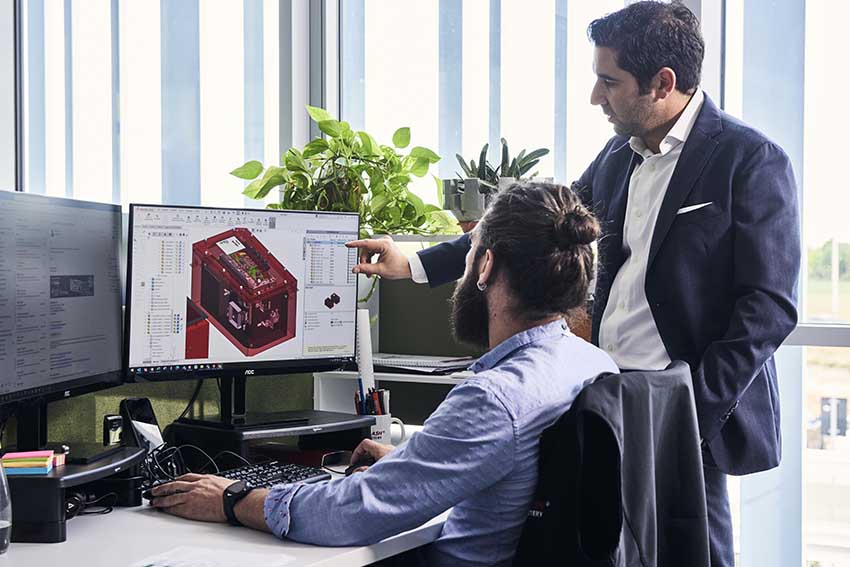
After University, I officially joined my father’s company and I dreamed about growing the company with him one day. But then, in 2006, the unexpected happened: I was visiting a customer in the US when I got a call from my father telling me he had decided to sell the company.
What was initially a broken dream turned out to be a great opportunity. In 2009, I went to a friend who made electric vehicles and I saw lithium batteries from China for the first time, they were interesting, but definitely low-quality.
This was where everything begun! I thought that if I solved the technical problems, I could make an innovation out of those batteries. The main problem was to find a new technology and to equip lithium batteries with a BMS. I got my experimenter friend Alan on board, and we spent two and a half years in my garage working on the electronics to improve the performance of the batteries. We finally succeeded: We managed to keep the cells balanced, even in very large battery packs offering high performance. This made us miles ahead of the competition, who were still producing traditional control systems.
We then opened Flash Battery in 2012: the start-up that was born out of a garage has then evolved to a genuine stable company with its eyes open to internationalization, with a constantly growing turnover (17.2 million in 2021) and 65 employees who share with us the same passion and business vision.
Our rapid growth has been helped by the fact that we had extensive industrial experience behind us, despite being so young: this helped us develop our products with an awareness far beyond what a university start up would have, for example. Our approach has been industrial right from the very beginning. We committed ourselves to develop internally all the necessary skills we needed to produce most of the strategic components. This allowed us to meet market needs in a responsive way.
E.E: What are the main areas of activity of the company?
M.R: Today, the product portfolio boasts more than 500 different types of lithium batteries installed in over 15,000 applications worldwide.
We always kept a clear focus on our benchmark market: whilst a lot of our competitors produce all types of battery, from those for bicycles to those for industrial machinery, our target has always been industry, industrial vehicles and special industrial machinery, consequently producing medium-large batteries. Our main customers come from many sectors of industry, including automation, robotics, logistics, construction, boat building, aerial platforms, electric vehicles, agriculture and airport ground support equipment.
Since 2012, we have been working with top players in the aerial platforms market who chose us to switch from lead to lithium technology, but soon after, many other leading companies in the lifting, construction and special industrial machines joined us. Altogether, the industrial machines segment is worth around 45% of our turnover – a significant and growing figure: more and more customers are saying goodbye to internal combustion engines opting for lithium-based hybrid or full-electric systems.
In addition, the AGV/LGV sector is another important part of our core business, worth around 40% of our total turnover, followed by electric vehicles, vehicles for waste collection and deliveries in old town centres, and many other diverse applications.
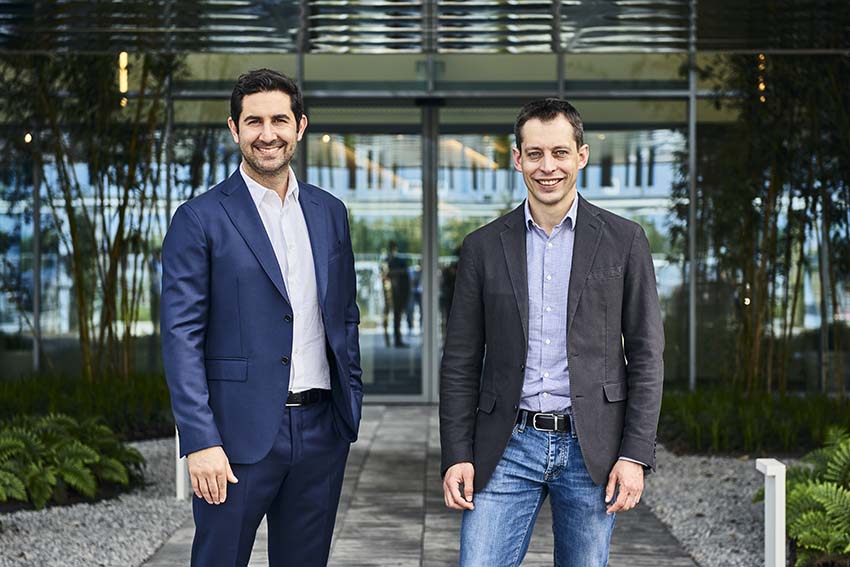
Finally, we are seeing more and more interest coming from the world of construction in general and from other areas like agriculture – which is growing fast and now accounts for 5% of our turnover – which we initially thought would not go down this road, but are actually much closer to electrification than you might think.
E.E: What are the ranges of products?
M.R: One of our main characteristics is high customization. That is why, we do not have a product catalogue and all our batteries are tailor-made to the requirements of each application.
Why? Simply because every application has its own specific needs. The role of Flash Battery is precisely to work alongside the manufacturer in the most difficult part of the process, i.e., choosing the best solution for each application.
You might not know it but analyzing each detail of a product – the type of application; its consumption, size and space; the context and mode of use, etc. etc. – can make a difference and is crucial in giving birth to the perfect lithium battery for a precise application.
Every piece of information is essential to develop the electrification project most suited to our customers’ needs and therefore choosing a supplier with the right know-how and experience plays a strategic role today, especially for manufacturers that are now entering this market and converting their models. Our team of engineers and specialized technicians are by our customers side from the very beginning to assess the solution that can best suit their electric vehicle or industrial machine.
E.E: What’s the news about new products?
M.R: Flash Battery lithium batteries, being totally customized, are always kind of “different”, because each of them is designed according to the specific needs of each single customer.
But what is actually constantly evolving at Flash Battery is our technology.
The 35% of our employees is active in the R&D department and engaged in constant research activities to anticipate market requirements and identify new chemistries, new technologies and increasingly innovative and eco-friendly materials and production processes.
Here, for example, are some distinguishing features of our technology:
The Flash Data Center, the proprietary remote-control software integrated inside Flash Battery lithium batteries, monitors 24/7 the health status of every single battery installed in over 54 countries worldwide. Through a constant check of all battery parameters, it can promptly warn both the user and Flash Battery service team in case of malfunctioning.
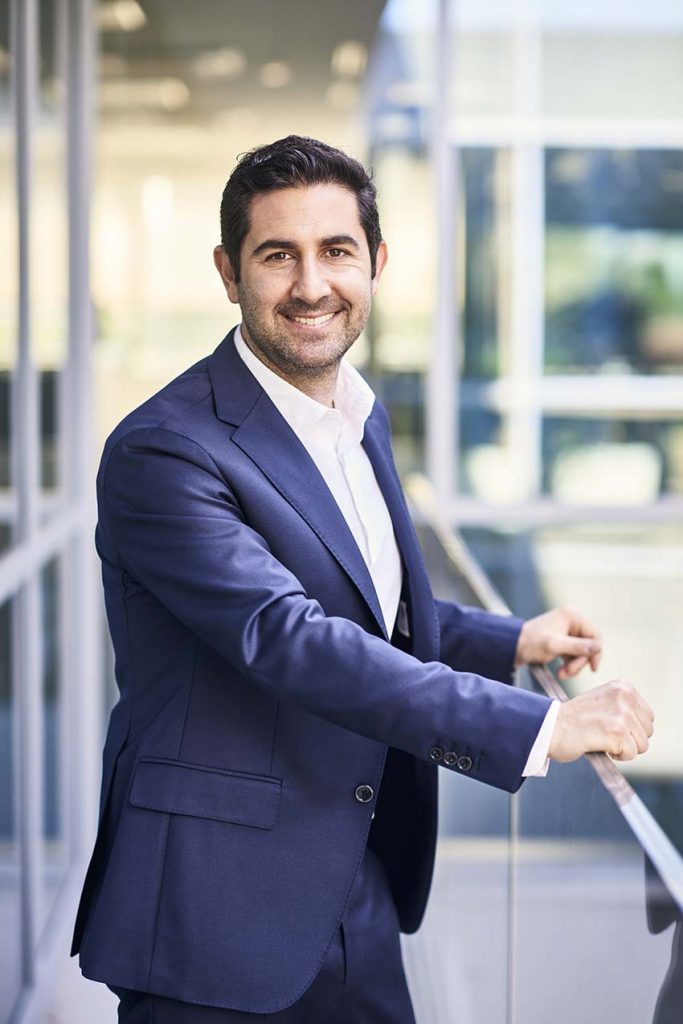
Marco Righi
A very innovative feature of Flash Data Center is the automatic data control, which daily analyses data received on battery operation and sends any warnings, abuses, or anomalies in real time. This nips false alerts in the bud by performing self-diagnostics and predictive maintenance.
The Flash Data Center will soon be available in a new 4.0 version, which will feature an improved interface both in terms of graphics and in terms of the information displayed, with implementation of artificial fleet control algorithms and extremely detailed consumption analysis that will make life even easier for industrial businesses.
Another unique feature offered by Flash Battery technology is the proprietary BMS system, the Flash Balancing System, still unrivalled among our competitors today. Unlike a conventional BMS, the patented Flash Balancing System can act both actively and passively with a balancing power that by far exceeds conventional BMS systems (20A), not only at the end of the charging cycle but also in active mode during charging and discharging. This translates into several advantages, such as ultra-quick balancing times (under 30 minutes) and maximum run time for Flash Battery lithium batteries.
Last but not least, the development of third generation cells enabled us to significantly increase the energy density of our battery packs from 134 Wh/L to 207 Wh/L in just three years. This higher energy density also means a smaller battery pack volume, which does not alter the high safety levels we already guarantee for each of our lithium batteries. How do we guarantee maximum safety? By choosing to use LFP chemistry, which best meets the needs of the industrial world; it is in fact the safest and most stable chemistry on the market, and is available in several large capacity formats, as required by industrial systems.
E.E: At what stage is the market where you are currently active? What can you tell us about market trends?
M.R: The electrification market is constantly evolving. In recent years we have been experiencing an increasing number of manufacturers, willing to take the decisive step towards electrification of their vehicles. Up until five years ago, we would have never thought of electrifying an excavator or an agricultural machine, but today we have several electric prototypes in the construction and agricultural sectors, to name but a few. There is therefore a clear interest in the electrification of increasingly large vehicles, with high-voltage batteries and high power in terms of kW. Today is the perfect time to evolve: compared to global numbers, electrification still accounts for a small percentage, but it is a fast-growing segment and is developing exponentially. It is therefore important, now more than ever, to gain the confidence of the manufacturers of machines and industrial vehicles and to accompany them in this imminent technological change.
As of today, 65% of our customers are based in Italy and 35% are international, but export is rapidly gaining in importance. Flash Battery is both directly and indirectly present across Europe through prestigious partnerships established with very experienced powertrain system integrators active in the major markets. These include Atech in Germany, Efa France in France and Q-tronic in Benelux. Along with Italy, these three markets are fundamental for the progress of industrial electrical transition, together representing more than 80% of all the European market for electrification of industrial machines and electric vehicles.
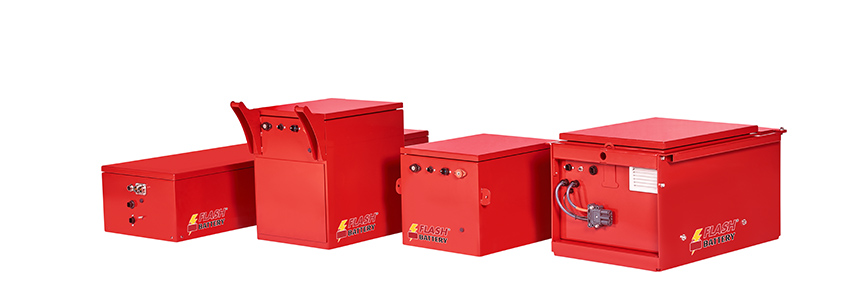
E.E: What estimations do you have for 2022?
M.R: We closed the year with a positive trend and a growing turnover of +25% vs 2020, which in 2021 translates into 17.2 million. The focus in 2022 will be on internationalization: we foresee further growth of our core business and a further expansion of our business relations in European countries, also thanks to the partnerships we are cultivating with leading EU companies in the powertrain segment, thanks to which we can provide our foreign customers with complete electrification packages. Another aspect that we will continue to foster in 2022 is research and technological innovation to obtain increasingly high performing and innovating Made in Italy batteries. We look forward to these new challenges!