FreeD Printing is a spin-off from the Ruhr-Uni Bochum and has developed a robot-based multidirectional modeling method for various additive manufacturing processes. It enables model building with the help of a six-axis industrial robot not only with flat, horizontally oriented layers in one direction, as with most 3D printing systems today, but with freely formed non-planar layers, from variable directions and with variable layer patterns.
This results in three different manufacturing advantages over today’s additive and other manufacturing processes:
- The reduction of manufacturing resources, energy, time and cost to be used
- The design freedom is increased and the possibility to print on existing objects even with curved surfaces is introduced.
- By specifying the string and layer orientations, component properties such as surface and strength can be optimized.
Easy Engineering: What are the main areas of activity of the company?
FreeD Printing: FreeD Printing develops the manufacturing systems for the non-planar modeling process with additive manufacturing technology using six-axis robots. The team combines several years of scientific and industrial professional experience in mechanical engineering as well as computer science to develop and design robot-based products and systems.
Plant and process technology as well as process planning software are integrated in the manufacturing systems. Together with scientific and industrial partners, process heads are developed to transfer the modeling process to other additive manufacturing processes.
With an expertise in industrial robotics, FreeD Printing develops its own process planning software to generate the process control programs automatically.
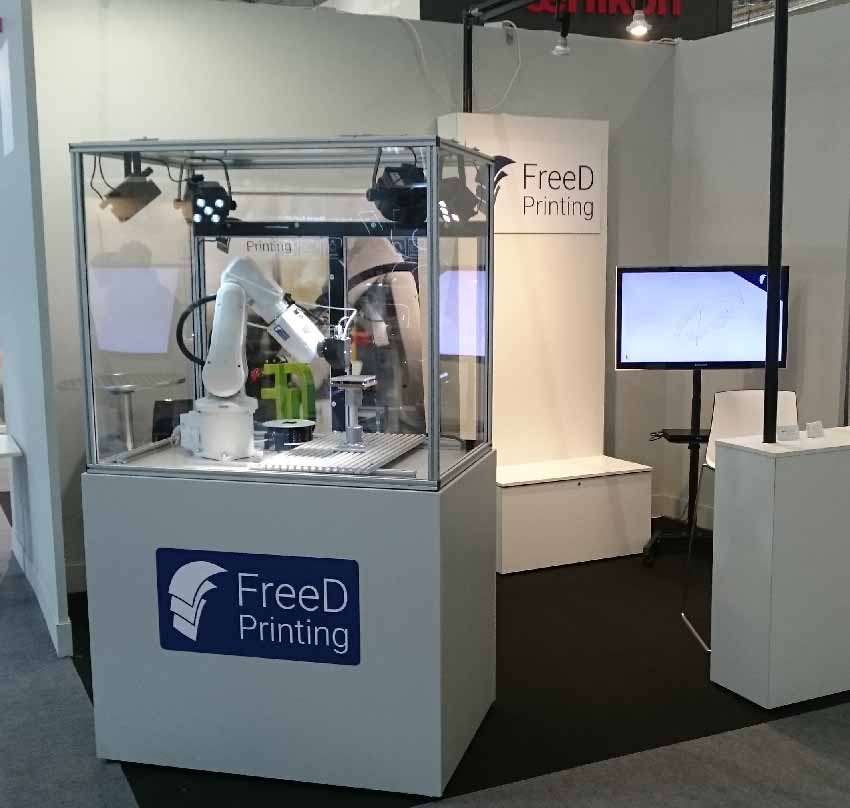
E.E: What’s the news about new products?
FreeD Printing: In the new version of the process planning software, which will be released in the middle of the year, the reduction or even elimination of currently required support structures as well as the modeling on curved surfaces will be possible for the production of a universal spectrum of component shapes, which is not offered by any other planning software available so far.
The integration of a 3D camera system in a new variant of the manufacturing system enables automated modeling on or around existing objects, e.g. for repair purposes or for combining different materials with different properties.
With newly developed process heads, the FreeD Printing modeling process is transferred to metal-based additive manufacturing processes such as LMD (Laser Metal Deposition) and WAAM (Wire and Arc Additive Manufacturing). The size of the build volume can be scaled with the size of the robotic system used.
In addition, process technology for material extrusion based on granulates is being developed to increase the printing speed, especially for large workpieces.
E.E: What are the ranges of products?
FreeD Printing: The developed pilot system enables the production with variable layer patterns using the additive material extrusion process (fused layer modeling). It can be printed with the typical range of materials such as PLA, ABS, PP, PETG, PA and others in a cube-shaped build volume with an edge length of 500mm.
The modularized FreeD Printing production systems each consist of a unit of system and process technology as well as the planning software. The system technology includes the specific robot system as well as the control technology and the machine equipment. The process technology generates the layers according to the specific additive manufacturing process. The self-developed planning software automatically calculates the non-planar layers and the tool paths for the components to be manufactured without the need for any additional input or process know-how from the user.
In addition to the manufacturing systems, technology-specific training and support are offered.
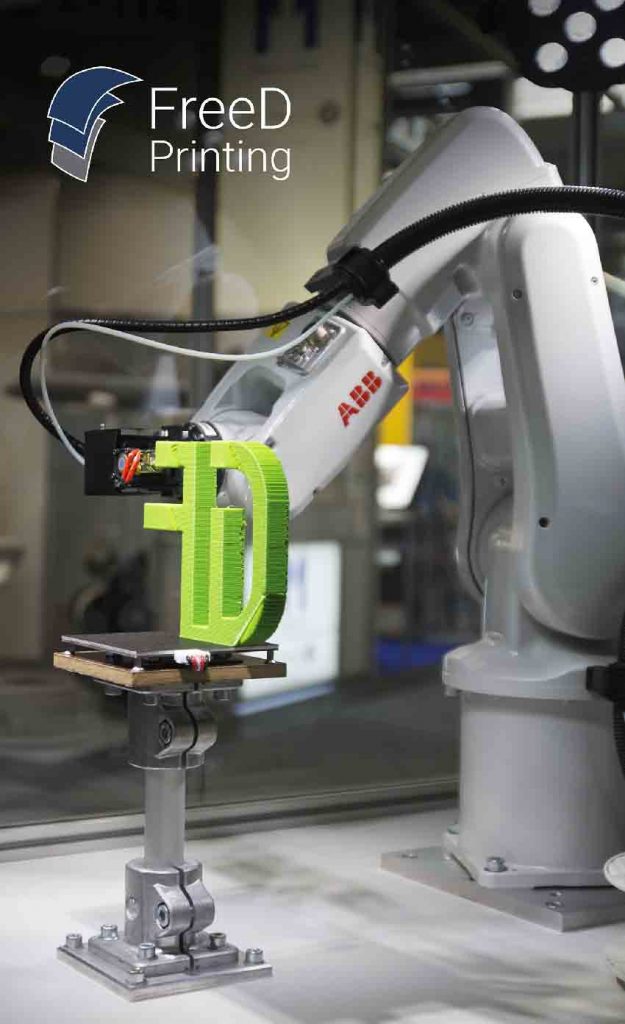
E.E: At what stage is the market where you are currently active?
FreeD Printing: 3d printing is a globally rising market, growing at double-digit rates annually. It is already in use in many application fields and industries. These include the automotive, aerospace and electrical engineering industries as well as mechanical engineering and medical technology.
So far, additive manufacturing processes are often used for the production of prototypes and tools as well as for the production of small lot sizes.
FreeD Printing is currently developing two manufacturing pilot systems for partners and use cases from the medical technology and automotive supplier industries. With the installation of the pilot systems, the market entry is planned during 2023.
Based on initial application partners, FreeD Printing is looking in particular for other interesting use cases for modeling with variable layer patterns.
E.E: What can you tell us about market trends?
FreeD Printing: In additive manufacturing technology, there are many new developments and new products in all sub-domains of manufacturing systems, materials, software and services.
With new developments in manufacturing systems and the materials used, the use of additive manufacturing technology is becoming faster and less expensive than conventional manufacturing processes, and the design freedom of components is also being expanded. As a result, additive manufacturing technology is no longer only suitable for the production of components for the development and manufacturing processes, but is also becoming more and more profitable for the production of components for end customers.
New additive manufacturing systems are increasingly being used to produce large components with dimensions of more than one meter. For example, additive manufacturing technology is now also being used in the construction industry for the production of part elements for buildings.
At the same time, there are developments and a growing demand for modeling with non-planar layer patterns, like the FreeD Printing modeling process.
E.E: What are the most innovative products marketed?
FreeD Printing: Besides the innovative approach of modeling with non-planar layers and variable layer patterns, for which FreeD Printing offers solutions, there are other innovative developments in the field of additive manufacturing technology.
Among the most interesting developments are the measurement and control of the manufacturing process parameters in the process flow. Another interesting development is the automatic change of the material used, such as filaments. This enables the combination of different colors or component properties in the same modeling process.
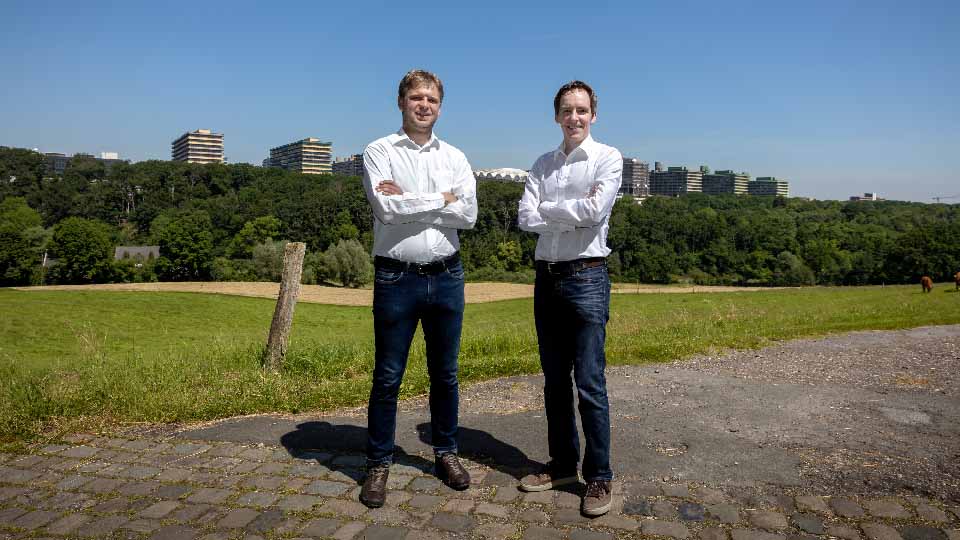
In addition, new materials are being developed for all manufacturing processes and systems in order to improve properties such as the strength of the parts, that are printed with them. For example, fiber-reinforced materials that can be processed using the material extrusion process are now available and significantly increase strength.
E.E: What estimations do you have for 2023?
FreeD Printing: Trends toward product customization and increased manufacturing autonomy in Europe are motivating the use of additive manufacturing technology.
As production possibilities and the achievable manufacturing qualities for components continue to improve, 3D printing will continue to grow and will be used increasingly in many industries.
FreeD Printing will enter the market this year with its first pilot systems and demonstrate the performance of the robotic non-planar modeling process with industrial use cases. Thus, more use cases in additional industries will be identified and the company will continue growth.