Habermann Aurum Pumpen is a global manufacturer and distributor of industrial pumps, valves and fittings. The products are manufactured in Bochum and exported from there to customers in Western Europe, North and South America, the Middle East, Asia, Africa and the CIS countries, among others.
Habermann Aurum Pumpen’s slogan is, therefore, as simple as it is impressive: Made in Bochum. Made for the world. The company’s history dates back to 1927. Many outstanding developments, especially in the field of slurry pumps, can be traced back to Habermann Aurum Pumpen. This vast experience, the know-how of the employees, experienced engineers and sales specialists at the company’s worldwide locations enable it to develop both innovative and custom-fit pump solutions for partners and customers from a wide range of industries. Another focus of the company is the aftersales business field.
Habermann Aurum pumps are particularly durable, which makes it all the more important for the company to ensure professional maintenance and, if necessary, repair.
Here, customers benefit once again from Habermann Aurum Pumpen’s experience: In the gigantic company archive, in which the most diverse construction plans from the past almost one hundred years are documented, answers and solutions to all pump questions of the customers can be found – even if the original product was not purchased from Habermann Aurum Pumpen or installed by Habermann Aurum Pumpen. All this is appreciated by customers worldwide, including many medium-sized companies from different countries, local companies, but also global industry giants such as ThyssenKrupp, Liebherr, BASF and Arcelor Mittal.
“We know how, because we did it ourselves,” says Zia Safi, Managing Director of Habermann Aurum Pumpen, summing up his company’s brand essence: “We have been in a continuous growth phase for several years, opening up new markets and developing new industrial solutions. This is a great recognition for our work. And an obligation for us to continue writing the success story of our company.” By the way, when asked what makes his products quality, Mr. Safi responds with the following simple formula: “The best pump is the one that does what it’s supposed to do: pump.”
Interview with Zia Safi, Managing Director of Habermann Aurum Pumpen.
Easy Engineering: What are the most digitized solutions?
Zia Safi: Digitization is an important topic for us. As a traditional company, we are always keen to actively shape the future, i.e. to develop modern processes ourselves instead of being driven by the developments of others. This is our responsibility towards our history, but above all towards our employees. Habermann Aurum Pumpen GmbH has therefore often been a trendsetter in the field of centrifugal pumps, and we want to repeat this in shaping digitalization in our industry. In doing so, we are essentially concerned with two areas: First, of course, we design our pump, valve and engineering solutions so that they always meet the most modern technical requirements, and second, we network our employees all over the world with state-of-the-art knowledge management programs. It doesn’t matter whether it’s an engineer who is repairing a plant or a customer service representative who is advising a new customer at a trade show, for example. Both always have access to the know-how of our entire technical team in order to offer and implement high-performance, sustainable as well as, last but not least, price-efficient solutions.
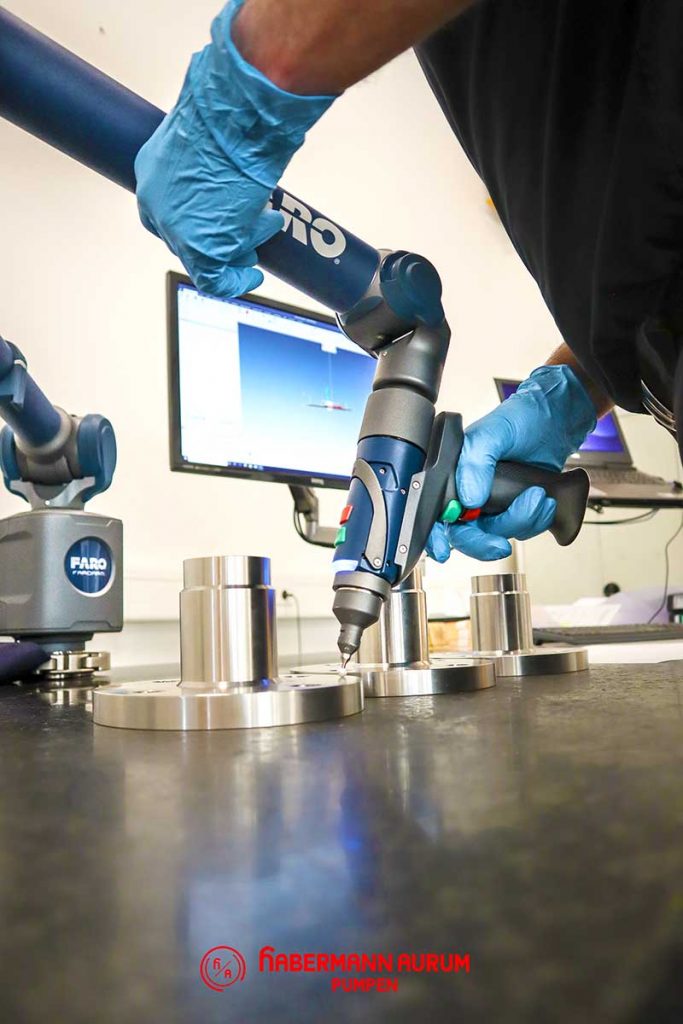
E.E: What are the features of these products / solutions?
Z.S: In the area of knowledge management, we work with state-of-the-art hardware and software specially tailored to the needs of our employees. The content is available to our global team in a variety of languages, and communication between them is naturally also in real time via text, voice and video. But this is of course standard today and has therefore long been established in our company. After all, we have been active worldwide for many decades. However, these opportunities that have arisen from digitization are fundamental to our international success, because we have local subsidiaries in all key sales countries. Our own employees work there in close coordination with our headquarters in Bochum on the one hand and with our local customers on the other. Without the best possible technical knowledge management, implementation would not be possible.
E.E: What are the advantages for users?
Z.S: Our customers benefit in particular from the state-of-the-art technical equipment in planning and production. In mechanical processing, for example, our machines enable us to process materials to an accuracy of 0.005 millimeters. By way of comparison, a human hair is 0.1 millimeters wide. That’s why I always like to say that hair precision is not precise enough. In design, we work with the best drawing programs based on our extensive company archive, which documents all our pump solutions from the last 100 years. This allows us, based on close communication with our customers, to understand the solution from our wealth of experience that most closely matches their requirement and then customize it to meet their unique needs. This combination of traditional and modern is unique. We are really proud of it. Because only we, as a traditional company with highly qualified employees, can offer this, because it is precisely this combination of experience and expertise that makes innovation possible.
E.E: In what kind of projects are they used?
Z.S: As I said, the customer and his requirements are at the center of every project. Based on our experience and expertise, we help them find an innovative and unique solution. In doing so, we take advantage of the opportunities offered by digitization and constantly invest in new hardware and software as well as in the further training of our employees.
E.E: Are you planning to implement digitization in other products / solutions?
Z.S: We are currently updating our ERP system. It is getting new functions that will make work more efficient and improve the learning from the processes. We want to be faster with our customers and be able to install their Habermann Aurum pump more quickly. By the way, we always involve our employees and try to implement their ideas, because they work with it in their daily practice, nobody knows better than them how we can improve. No computer in the world can replace our experts.

E.E: How important is digitization in your field?
Z.S: State-of-the-art technology enables us to combine tradition and modernity, and it creates the conditions for comprehensive knowledge management between our employees and all our customers around the world. Digitization is therefore something we can neither imagine nor stop in the future – and that’s a good thing. Because we will continue to improve with it in the future.
E.E: In which directions do you think digitization will develop?
Z.S: For me, this is not a speculative question, but a work assignment. We want to consciously shape digitization and use it to create new opportunities wherever it helps us in our work. Be it in order processing, construction or knowledge management. So, my answer is clear: digitalization will develop in the way that is necessary for Habermann Aurum Pumpen GmbH. I am quite confident about that. But just as confidently, I also say that some things will not change as a result of it. The best pump, for example, will always be the one that does what it is supposed to do, namely pump.
E.E: What was the feedback from employees on the digitization process?
Z.S: I have to disappoint you: Our employees don’t experience the digitization process as something that passes over them and which they then comment on in an annoyed manner in conversations about the good old days – On the contrary, our employees actively help shape these processes, we all work on them together and on an equal footing. In my view, this is also the basis for their success, because it is the expertise of our employees that distinguishes us in our daily work, so we must also organize further developments of our business processes in such a way that they help them in practice. And once again, we succeed.
E.E: Which industries do you think will be more digitized in the future?
Z.S: Without question: retail. And the winners will be those who can make good service digital. However, thanks to knowledge management and experience in modern communication, I see Habermann Aurum Pumpen GmbH on a good path here, too.
E.E: Has the current situation led to your company implementing digitization earlier than predicted?
Z.S: Actually, no. Of course, we also have more home offices during the pandemic, but we had created the technical prerequisites for this long before, precisely because it is a prerequisite for our international work.
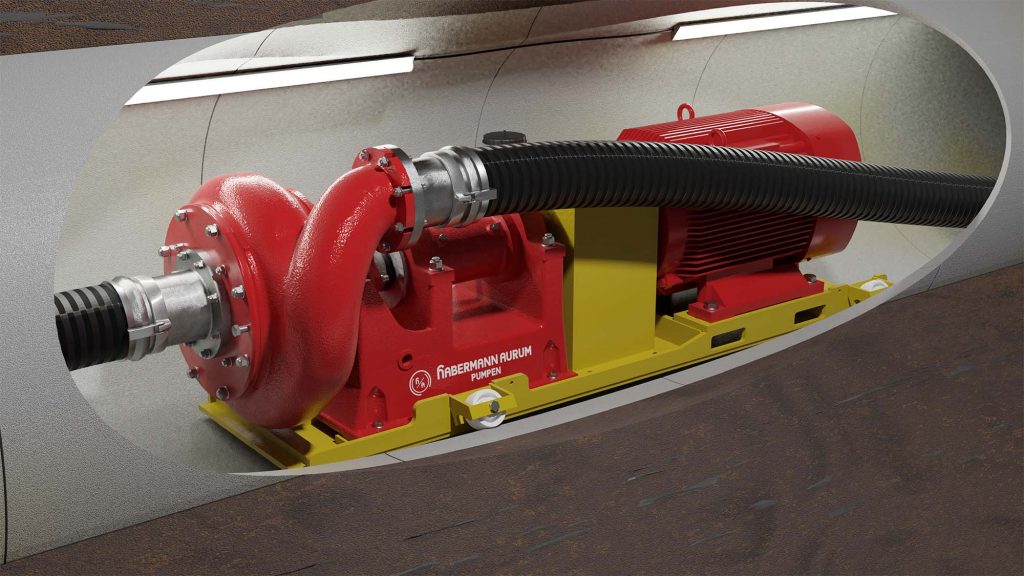
E.E: What are your forecasts for the first half of 2021?
Z.S: We hope that the vaccination and testing strategy will be better implemented on site. Because despite all the successes in digital distance working: I haven’t spoken to some colleagues in person in a room for months, and I already miss that. That’s why I’ve promised my employees a big barbecue as soon as that’s possible again.
And as far as digitization is concerned, we are currently converting our order management software. We want to complete this process soon so that we can then offer our customers shorter delivery times. So, you can look forward to that – just like we look forward to the barbecue (laughs).