Easy Engineering: Why do users choose your products / solutions?
Hottinger Brüel & Kjær: Hottinger Brüel & Kjær (HBK) might be a new name, but it’s one that’s backed by decades of experience in metrology and measurement.
HBK grew out of the union of two market-leading brands – HBM and Brüel & Kjær. Together, we’re combining expertise from both companies to provide our customers with highly advanced, integrated solutions for testing and measurement.
Customers turn to us for the expert advice and experience that has grown out of many years spent building industry-leading equipment for engineers. And we use that experience to provide our customers with what they really need: technology that they can rely on to help them get the job done quickly, efficiently, accurately, and reliably. Technology that helps them bring safer, more energy-efficient, and innovative products to life faster.
We support engineers across every stage of the product lifecycle, from simulation to physical testing, data analysis, manufacturing, and monitoring. Our solutions cover the whole measurement chain too, from sensors and data acquisition to data preparation, evaluation, and engineering services.
HBK is a trusted partner of engineers in the automotive, aerospace, audio and telecommunications, and transport industries and supports research at universities and metrological entities across the globe.
E.E: Can you give us some examples of projects in which your products / solutions were used?
Hottinger Brüel & Kjær: Our products are used across the complete lifecycle of our customers’ products.
In the early development phase, during mechanical tests, our sensors measure force, strain, displacement, and other mechanical quantities.
In the verification phase, HBK sensors are a key component of test stands and are used to measure press forces, tightening forces, and loads in production environments.
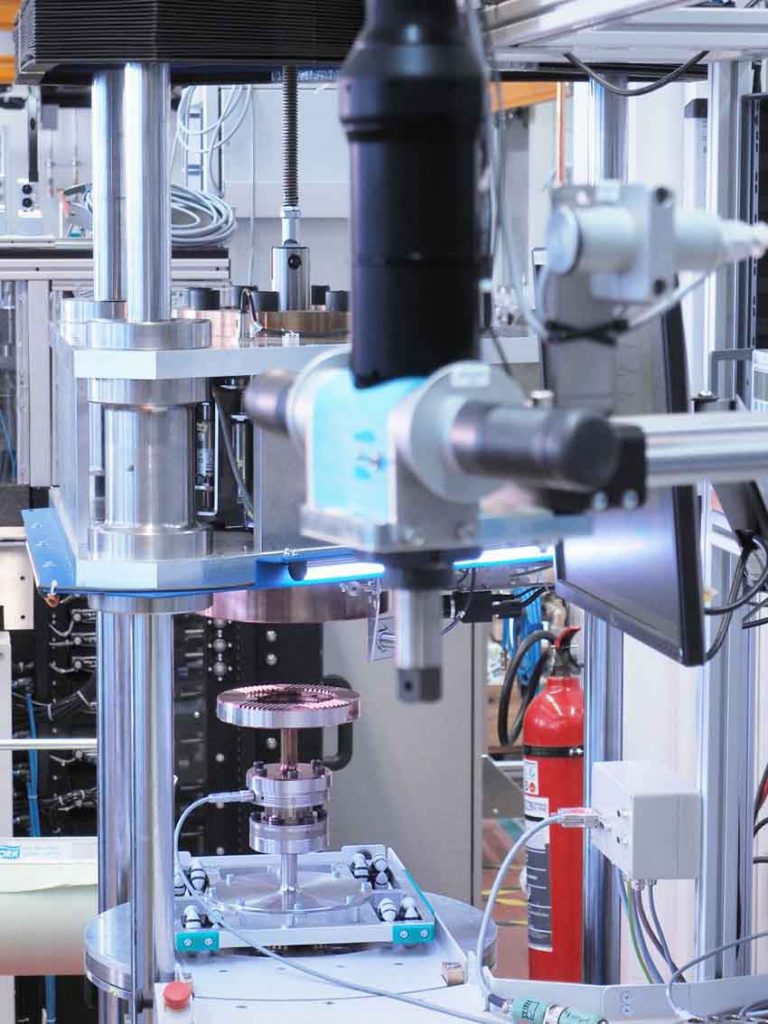
Finally, HBK sensors are key components in many of the machines built by our customers.
The range of applications is very broad. Some of our customers use HBK sensors on truck scales, where multiple load cells are used to measure the weight of an entire truck. Others use them in end-of-line test stands for every piece of their machinery to do things like measure the torque or the sound and vibration of a motor before shipping it to a customer. Our sensors are also used in the testing of excavator components at Liebherr, the press force monitoring at Schuler Presses, and many torque sensor applications, where they provide the automotive industry with best-in-class accuracy.
E.E: What products / solutions were used in these projects?
Hottinger Brüel & Kjær: HBK offers many different sensors for strain, load, force, displacement, and pressure, as well as accelerometers and microphones.
Most of our sensors are based on conventional strain gauges, but we also offer piezoelectric force transducers and optical strain gauges. These sensors are complemented by a range of measuring amplifiers and DAQ systems, along with software that helps engineers complete the measurement task at hand as quickly and efficiently as possible.
Let’s stay with the example of a press machine mentioned earlier. When a force is applied to the structure on which the sensor is mounted, deformations occur – and the size of those deformations depends on the amount of force that’s applied. This is how extensometers, like the SLH700, can determine the press force indirectly. That way, small and large forces can be economically measured with the same sensor once it has been calibrated, and there is also no influence on the structural integrity of the machine when using a strain link rather than a force sensor which would require being installed within the machine.
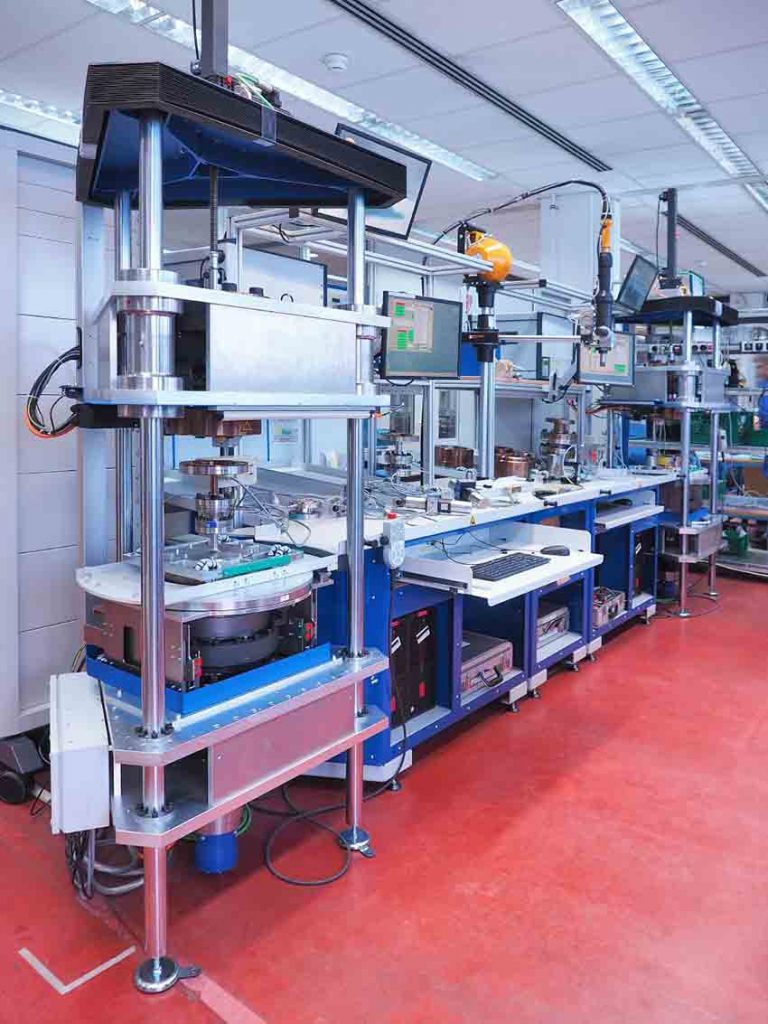
E.E: What special characteristics do your products/solutions have compared to others?
Hottinger Brüel & Kjær: SLH700 strain links, just like many other HBK sensors, are hermetically sealed, are made from stainless steel, and come with a high degree of protection (IP68). We also offer a range of other cables that are resistant to oils and other potentially aggressive fluids.
The key is that our customers can always find the right HBK sensor for their measurement task. They might find it in our range of standard products, or they might use the so-called “K-Mat” option, which makes it fast and simple to configure sensors according to their needs. Additionally, HBK has the capability to produce customized sensors in small and large quantities.
Another useful feature is the choice between passive sensors or the SLH700VA, which has an integrated digital amplifier and a voltage or current output. This option also exists for a variety of force transducers, covering a measurement range between 50 N up to 10 MN.
Our extensometers with integrated electronics use a special adjustment method, which guarantees the maximum output signal with minimal noise and much better resolution. Crucially, this adjustment doesn’t require any special knowledge, so it’s easy for any customer to implement.
E.E: How did your products / solutions improve productivity / efficiency for the users?
Hottinger Brüel & Kjær: HBK sensors offer unparalleled accuracy (which also translates into efficiency and economic advantages) as well as robustness, longevity and an associated low TCO.
To make this a bit clearer, a reliable sensor means that the machine is running the way it should. If the sensor fails, the machine will not work at all, which leads to production downtime. If the sensor doesn’t measure the way it should, the production yield decreases with too many rejects. Reliability, in terms of functionality and accuracy, is, thus, key for increased productivity and efficiency.
In the case of the SLH700, there is always a buffer of 10% in the upper and lower parts of the measuring range. Higher strain signals – the kind that, for example, appear in the event of a failure – are amplified and transmitted.
The characteristic curve can also be negative. Both elongation and shortening can be converted into a positive signal. The built-in measuring amplifier provides low noise and a bandwidth of 2 kHz.
Bear in mind that it is essential to permanently store the span – that is, the difference between the minimum and the maximum – so it’s imperative to reset to zero after a power failure.
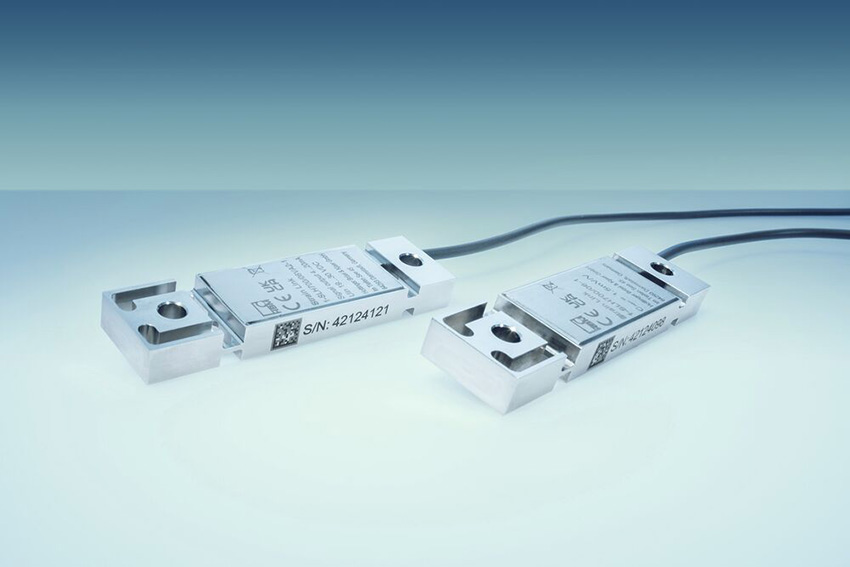
E.E: How do users work better with your products / solutions?
Hottinger Brüel & Kjær: Precision, robustness, and flexibility are always our priorities, because that’s what our customers need to work better.
They need to know they can trust our sensors to gather precise data that they can rely on, so they can deliver their results with confidence. We achieve that by making our sensors highly user-friendly, combining high-performance sensors with common connectors, state-of-the-art interfaces, and standardized profiles.
HBK sensors are traceable to the national standard, so you can rely on them to provide trustworthy results – as well as use them for reference measurements and calibration tasks.
Once they have access to high-performance sensors, in combination with user-friendly digital electronics, our customers can run tests faster and more efficiently – all without sacrificing reliability or compliance with industry standards and regulations.
By providing engineers with equipment that is robust and resilient, we also give them peace of mind that their sensors are performing as they should, without the need to quadruple-check every sensor every few minutes. As part of this, we integrate our digital electronics directly into our sensors, so that users can see directly into the equipment, understand how it’s performing, and get easy access to the information they need to keep sensors running in peak condition. The result is a new ability to create predictive maintenance schedules and avoid downtime. They can also finally dispose of additional electronics or gateways. Crucially, the robustness of our sensors also significantly brings down total cost of ownership.
Finally, our customers need their sensors to be able to flex to fit a wide variety of use cases and situations, so they get the most value from their investment. HBK sensors can be used in a wide range of tests and have connectors that can be swapped out quickly and easily. This means engineers can minimize the time taken to change tasks or switch from one type of test to another, greatly speeding up the whole process of testing and measurement.
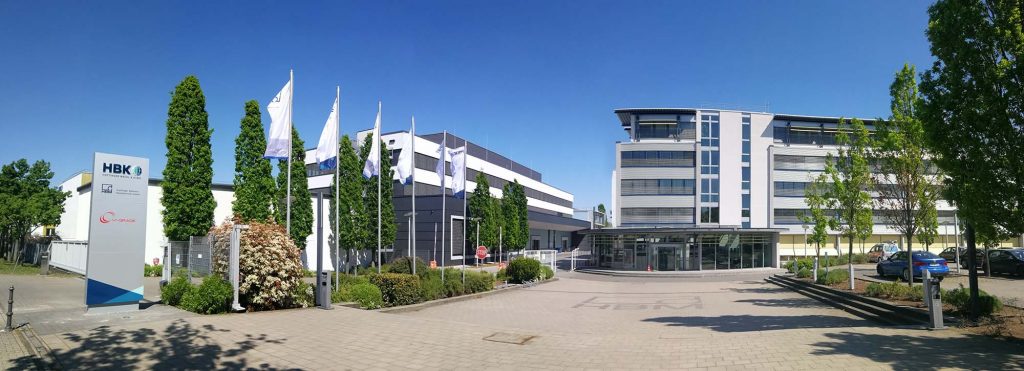
E.E: Which are the most successful products / solutions in your lineup?
Hottinger Brüel & Kjær: HBK’s portfolio of digital sensors has started gaining momentum, as more and more industries and users are interested in digitalization and the associated benefits. We know that the most successful, efficient, and accurate test engineers will soon be relying heavily on digital sensors that can transfer data automatically, provide users with in-depth performance information, and help them follow the data collection process more closely. That’s why we’re continually exploring new digital products, like the Fit5 and Fit7 load cells, which offer the legacy CAN or RS485 interfaces. The previously mentioned SLH700VA strain sensor and the range of amplified force sensors also mark a major step toward building a digital portfolio, starting with 4-20mA or 0-10V outputs.
HBK sensors cover all commonly used interfaces, and we are looking to add additional digital interfaces in the near future. So, stay tuned!
If you’d like to find out more about how HBK can help test engineers work better, you can find out more on the HBM or HBK websites. Or, if you’d like to ask some more in-depth questions, email Paul Zolnierek, Platform Owner & Growth Initiative Driver for Industrial Smart Sensors at paul.zolnierek@hbkworld.com