Inrotech is one of the world’s leading companies within robotic welding technologies and solutions. Started as a spin-off from Odense Steel Shipyard, converting its welding production from giant gantries with off-line programming to self-thinking and mobile welding robots. Both for Odense Steel Shipyard as well as for Inrotech, these first systems were a remarkable achievement All robots are “self-thinking”, all without any help from the operators. Place them near the welding target, press start, and they will do the rest.
The flexible and compact robot solution developed by Inrotech breaks in all areas with existing stereotypes, both mechanically, functionally and logistically. Inrotech has developed a product that combines high technology and simplicity in a way that moves robotic technology from experts to ordinary people. This is made possible without sacrificing either flexibility or reliability, but rather enhancing these parameters,
Easy Engineering: What are the main areas of activity of the company?
INROTECH: A long-time engagement at Odense Steel Shipyard (OSS), Lindoe (Maersk owned), which was one of Europes largest and most well-known shipyards, he was working with the very large welding gantry systems which OSS had in operation. This sparked the idea of a totally different concept: Instead of gantries and robots of enormous proportions and work intensive off-line programming, make small and mobile welding robots provided with a technology based on sensing and logic instead.
Inrotech was born out of the shipbuilding industry and shipbuilding still represents a main market segment together with market segments like: Off-Shore, Wind & Hydro and Heavy Industry in general
E.E: What’s the news about new products?
INROTECH: The Inrotech-Crawler is a highly advanced state-of-the-art piece of robotic welding technology, which has the potential of revolutionizing the welding business. Although it includes advanced technology, it is extremely easy to use: Install the titanium rails in a proximate distance to the welding groove. A few options like: welding wire type, groove design ect. have to be selected on the intuitive user interface.
Define start and stop points and press “start”. The robot now automatically identifies the welding groove by means of a line scanner and automatically calculates the number of passes, location of each pass, welding speed and weaving pattern; no matter position or plate thickness.
The weight of the robot carriage is approximately 45 kg. The Inrotech-Crawler has the ability to target a large number of welding jobs in the global industries. Butt-weld connection and other connection types requiring multipass welding, almost no matter shape or position, is a potential welding target for the Inrotech-Crawler. Obvious targets are; large pipes connections (in- and outside), assembly of blocks in shipbuilding, Storage tanks, Construction, Wind & Hydro and many more. Can be employed in workshops or at construction sites.
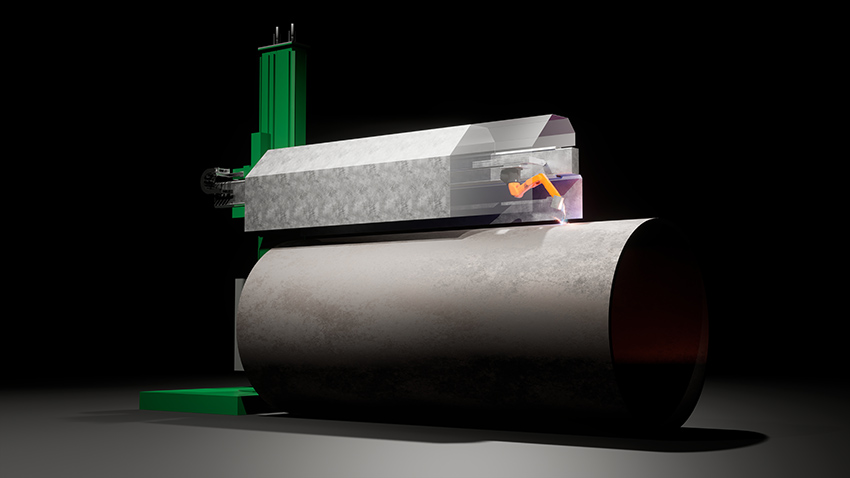
Mobile welding robots
Normally it has been considered that welding automation can be utilised only in the early stage of ship block construction, when structures are relatively simple and easily accessible. The possibilities of using welding automation in the rambling structures of the later production stage have been considered minor, even though a big ship block contains a great number of similar, repeatable welds.
The situation where similar welds are done repeatedly is an optimal application for welding automation, and this is the case also in the block assembly phase in ship manufacturing. However, lack of space has been the main obstacle to utilising the well-known benefits of automated welding in the later stage of shipbuilding.
This solution makes it possible to automate the similar, frequently repeated welding tasks in ship block assembling phase, which helps maintain welding quality on consistent and optimally high level. Furthermore, the welders can avoid working in narrow spaces that may impose a risk for their health and safety.
Neither offline nor online robot programming is needed, because the welding robot is highly adaptive. It is capable of recognizing the required welding tasks by itself, so there’s no need for an operator to continuously supervise each robot. The daily operation is straightforward and easily manageable also for welders with hardly any experience of welding automation.
Compared with the traditional solutions, the system is light in weight, flexible and compact – an investment that provides a fast ROI.
E.E: At what stage is the market where you are currently active?
INROTECH: Inrotech is currently active in wind industries. The Danish renewable energy company Bladt Industries has placed a significant order for Robotic Welding of large structures.
The order includes six fully automated Inrotech-C&B(Column&Boom), equipped with KUKA Robots, Lincoln Power Units and Enabl Tower Structures. This solution is specifically developed for automatic multipass welding of plate joints (butt-joints).
“Inrotech could offer the best solution for our needs and they have been flexible and supportive during the whole decision-making process. Our team reached the final decision based on the feasibility for our installation including the technical acumen demonstrated, and we were pleased with good cooperation between the teams involved.”, says Søren Hermansen, Senior Project Manager at Bladt Industries.
As a part of the investment, Inrotech provides support for welding parameters and the station’s lifecycle services.
The investment covers a maintenance contract that includes annual maintenance, updates, and remote online support. Additionally, Inrotech delivers production support, training, and installation supervising, tailored to Bladt Industry’s requirements.
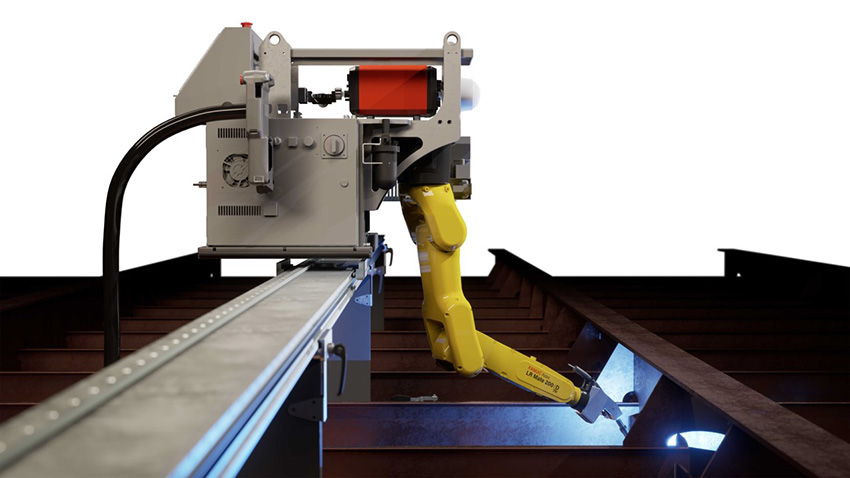
Inrotech has also received an order of several welding robots developed for vertical multipass welds. The Inrotech-Vertigo is purchased by the Danish windtower manufacturer Welcon and will be used during construction of floating foundations for offshore wind turbines, which enable new paths towards a cost-effective green energy transition in wind markets.
Inrotech’s automated robot welding solution is specifically designed according to Welcons’ requirements in order to efficiently handle complex welding’s on floating foundations, designed by Stiesdal.
“The design of the Stiesdal floating foundations allow us to use welding robot technologies during the manufacturing process. This will help us making floating foundations ready for serial production which will support the green transition. Our first welding robots from Inrotech was deployed in 2016, and their technology has proven its worth in our production line: without any programming involved, the system works fully automatic and providing welding of high quality”, says Rune Holm, Project Manager, Welcon.
E.E: What can you tell us about market trends?
INROTECH: Offshore wind farms are increasingly in demand and they are moving further away into deeper waters. We are experiencing a clear trend of more heavy and larger foundations, also towards floating foundations.
Quality standards for basic materials and the welding joints of monopiles in general are also becoming more strict with more demanding requirements. This has created a demand not only for high welding capacity, but also for high welding quality, increased process capabilities and flawless welding joints.
By 2050, a massive global expansion with offshore wind is expected. In the EU, the goal is to fivefold the current 12GW installed offshore wind by 2030, and again fivefold by 2050, so that the EU reaches min. 300GW offshore wind. The British offshore wind market is expected to reach “forty by thirty”, ie 40GW by 2030, against the current 10GW, and also in the US, US President Biden has ambitions to reach 25 GW offshore wind capacity by 2030.
“We know that the global market for offshore wind turbines will grow significantly in the coming years. We also know that the Danish wind turbine industry must continue to make massive investments in order to maintain its leading position, which is particularly significant in offshore wind. Therefore, we are very positive about the step that Bladt Industries is now taking with an expansion of production capacity in Odense. It will resonate in the global wind turbine industry, and we need to continuously mark ourselves as a pioneer within robotic welding for wind industries.
E.E: What are the most innovative products marketed?
INROTECH: Our Inrotech-C&B which is an intelligent welding robot for demanding MIG/MAG welding automation purposes for wind industries. The Inrotech-C&B is running on an external axis attached to the side of the welding boom. It provides a smooth and simple operation resulting in excellent welding quality.
With a user-friendly control system, it gives you full control over the Inrotech-C&B from one touch screen, while providing accurate report from the process and saves all the needed welding data for later use.
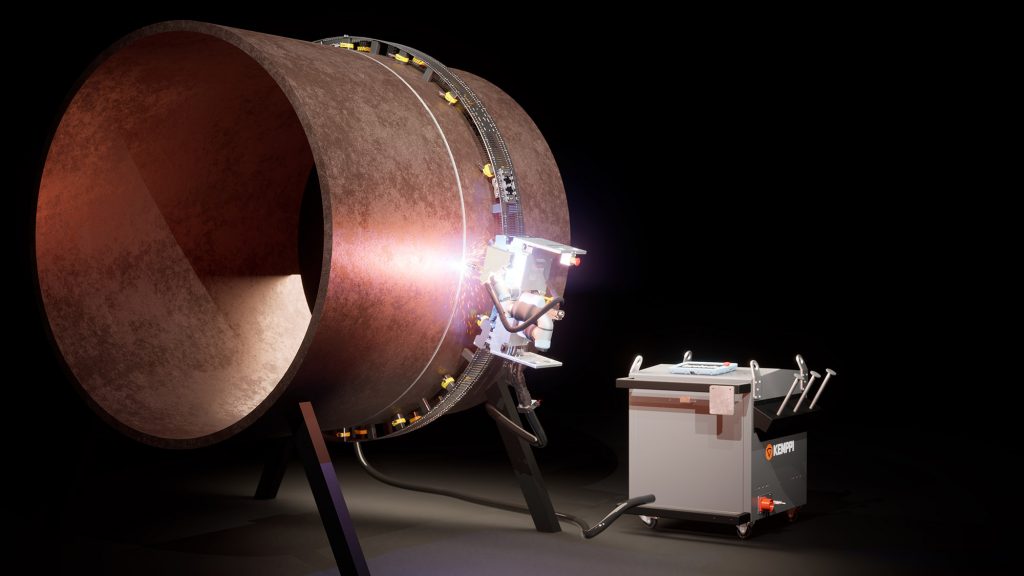
Welding targets
It’s ideal especially for automatic multipass welding in PA position of plate joining and longitudinal seams on cans of 15-150mm for wind industry with Inrotechs’ WeldLogic Technology, taking tolerances of the weldgroove into consideration and automatically compensating for variations.
Inrotech-C&B & WeldLogic Technology
Based on a scanning of the weldgroove, the robot automatically plans the full welding process: number of passes, location of each pass and the appropriate welding parameters, given the allowed heat-input window, the groove geometry and the welding position.
Simple operation & efficiency
As the Inrotech-C&B is not depending on any accurate global coordinate system, but rather taking reference point in the object itself, no accurate positioning is required: The robot will figure it out by itself!. The scanning of the weldgroove and planning of the welding process is done automatically. The monitor is built into a sturdy casing, which is integrated in a floor mounted console.
The user interface consists of a windows-based touch screen with simple choices for the daily operation. All commands are icon based in clear (local) language. No codes are required! The very simple and intuitive design of the user interface makes it easy to operate the system and allows high welding speed, while reducing manufacturing cost. This has been the case for the Danish steel manufacturer Welcon since 2016.