ioTech is a growing company that is leading the electronics manufacturing industry’s digital transformation to be more efficient, clean and low footprint. The company has developed the Continuous Laser Assisted Deposition (C.L.A.D.) technology. This is an additive manufacturing technology that allows 3D printing of almost any pastable material, up to extremely high viscosities.
ioTech is very fortunate to have the backing of two leaders in the electronics industry, Henkel and ASM Pacific Technology.
We officially launched our first product at Productronica, 2021, where we won the Productronica Innovation Award for PCB & EMS, as well as the Elektor Fast Forward 1st prize for best new start up.
Interview with Hervé Javice, CEO of ioTech Ltd.
Easy Engineering: What are the main areas of activity of the company?
Hervé Javice: Anywhere along the electronics supply chain where one material is deposited, etched, sprayed, printed, etc… onto another, the C.L.A.D technology offers a solution with the flexibility and resolution of dispensers, and the throughput of screen printers. Up to 5 different materials can be processed at the same time, including metals, polymers and ceramics.
For example, in the area of solder paste deposition, we can deposit solder balls at high resolutions, but at over 50 times faster than traditional jetting equipment, reaching screen printing productivities.
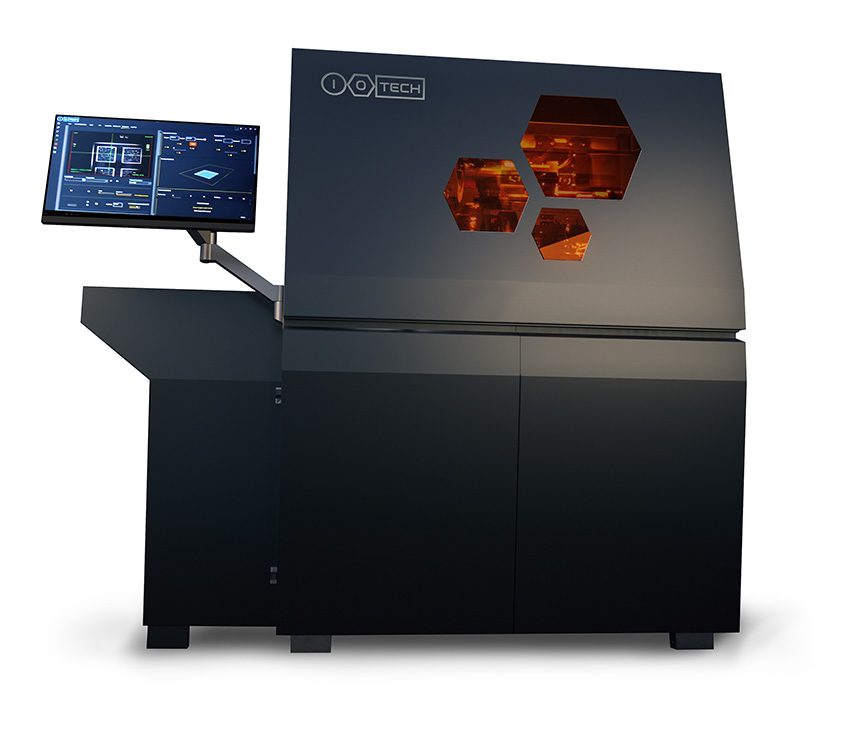
We are working on a number of such applications in the areas of PCB, SMT, semiconductor packaging and EMS.
C.L.A.D. technology is mesh-free, nozzle-free and contactless. This means enhanced performance at lower maintenance costs. As an additive manufacturing technology, it involves less material wastage, and enables innovative designs. Combining multiple steps into one station is less labour-intensive and has a smaller footprint.
E.E: What’s the news about new products?
H.J: We recently installed the first io300 system at a customer site in the UK. We already have a few orders for machines that will be fulfilled in the coming months. These were just initial orders, we expect these customers to acquire multiple units each, to be used as part of their mainstream manufacturing process, providing new capabilities and efficiencies.
E.E: What are the ranges of products?
H.J: The io 300 comes in a number of configurations depending on accuracy, resolution and throughput. There are various additional options the customer can choose from, up to 5 different materials, and different inspection options. We can provide a solution for every need, from high mix low volume specialists to large mass manufacturers.
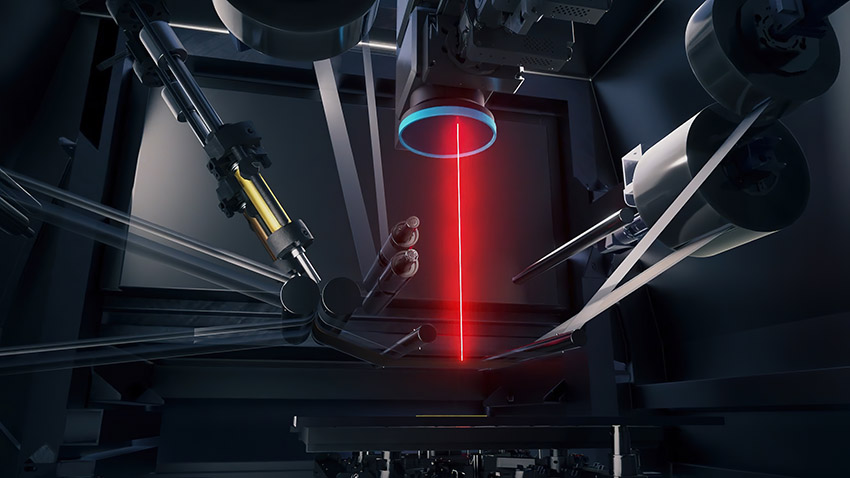
E.E: At what stage is the market where you are currently active?
H.J: Traditional additive manufacturing hasn’t been able to get much of a foothold in electronics, since it almost always requires some modification of an existing certified material. In electronics where each material has been optimized for the best mechanical and electrical properties, it becomes prohibitive to modify the materials and keep all their existing properties.
C.L.A.D. can print existing certified materials, thereby foregoing the requirement for any kind of modification. As long as it can be pasted, up to extremely high viscosities, C.L.A.D can deposit it. Materials with viscosities above 300,000 cPs (300 Pa*s) have been printed. As a comparison, peanut butter is roughly 250,000 cPs (250 Pa*s)
E.E: What can you tell us about market trends?
H.J: As semiconductors reduce feature size every 18 months, current manufacturing technologies for the back end are reaching their limit, and new technologies are required for innovative designs and more compact packages. These become critical for next generation electronics in mobile computing, IoT, automotive and 5G.
ioTech has developed digital manufacturing solutions that support this trend towards miniaturization.
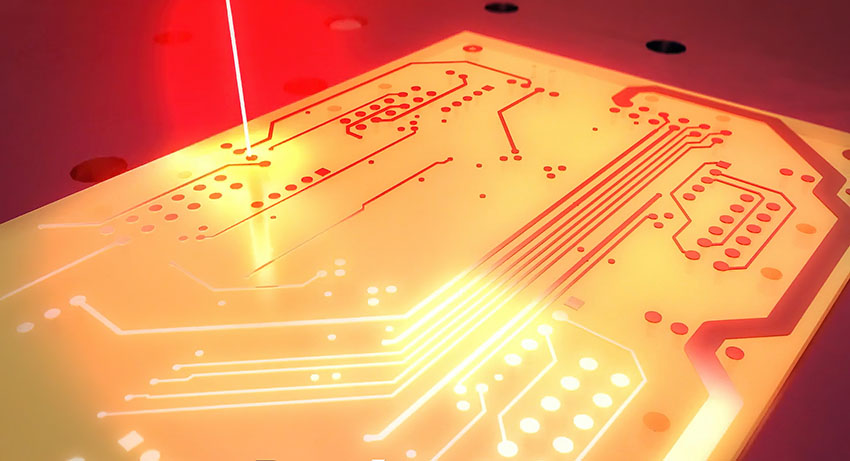
E.E: What are the most innovative products marketed?
H.J: We are currently marketing the io300, widely recognized as one of the most innovative products to come to the market in the past year, as is reflected in the prizes we won and the mentions in the press.
No other 3D printer can print such a wide variety of industry certified materials enabling new designs and print several such materials at the same time. This is truly innovative.
E.E: What estimations do you have for 2022?
H.J: We expect the benefits of C.L.A.D. to become more well known in the electronics industry as ioTech begins to scale up.