Lizotte Machine Vision develops and manufactures custom-built quality control, grading, and sorting equipment for the global food processing industry. The company’s systems combine X-ray, colour inspection, and other vision analyses tools in order to sort out the defective product out of the processing line or to grade each product by colour, size, defect, and more. With those technologies, they are capable of detecting shape defects, weight discrepancies, color defects, blood spots, fat, skin, breading imperfection, overcook/undercook, low-density foreign material along with high-density foreign material.
Over the years, Lizotte has established an expertise in combining those multiple technologies, in order to develop custom systems for each of their customer-specific applications. From products randomly placed on a belt to a product in a dedicated line, the innovative ejection mechanism is designed to make sure that the system ejects only defective products out of the processing line.
Interview with Mathieu Bosse, Business Development Director at Lizotte Machine Vision.
Easy Engineering: What are the main areas of activity of the company?
Mathieu Bosse: The main area of the company is to manufactures food sorting and grading system using innovative vision technologies for each specific application. Each customer gets is own custom built system based on is inspection requirement, his size requirement, his processing rate, his products size, the stage of is product (IQF, fresh, cook, hot, cold, raw, etc) and all the other requirements.
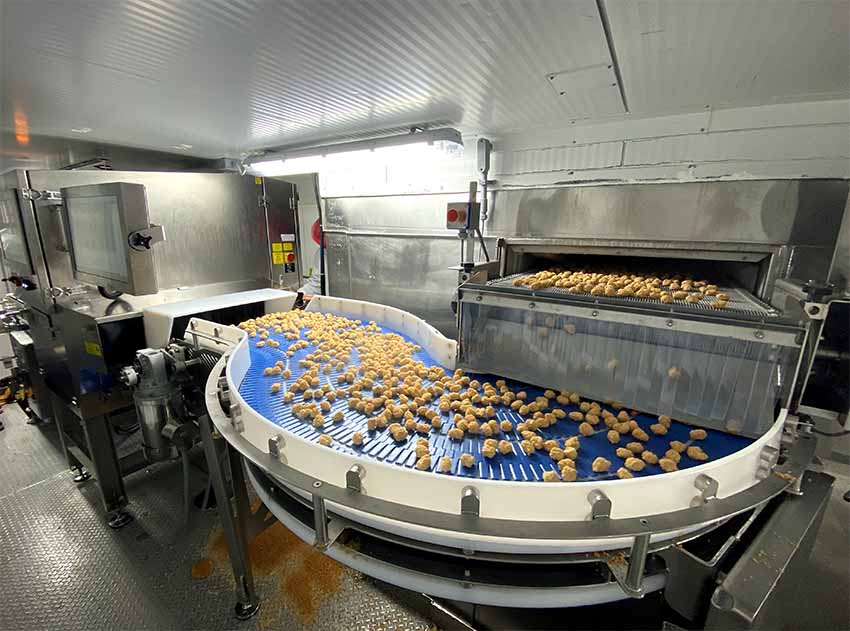
E.E: What’s the news for 2020 about new products?
M.B: Since every application we developed is based on an actual needs our customer requires, each system we do is a new product using similar technologies. We combine the needed ejection mechanism based on the product size and state of processing, the right x-ray and/or color inspection system to reach their inspection goal within the right foot print for their facility.
E.E: What are the ranges of traded products?
M.B: We work in 5 main food categories but our system are expendables to any industries. Our main industries are the poultry, meat, bakery, seafood and canning. Our product can be defined in 3 different categories: Sorting system, grading system and can inspection system.
Sorting system: Our sorting system combines x-ray and/or color camera to inspect the whole width of a processing belt in order to see each product that goes through and automatically ejects the defective products.
Grading system: Using x-ray and/or color inspection, our grading system can grade per size, color, length, species, weight and other grading criteria, each piece that comes one after each other in a grading lane.
Can inspection: Inspection 360 degrees of the seam of each can, this innovative system ejects any can with seaming imperfection such as spurs, drops, vees, miss chuck and more.
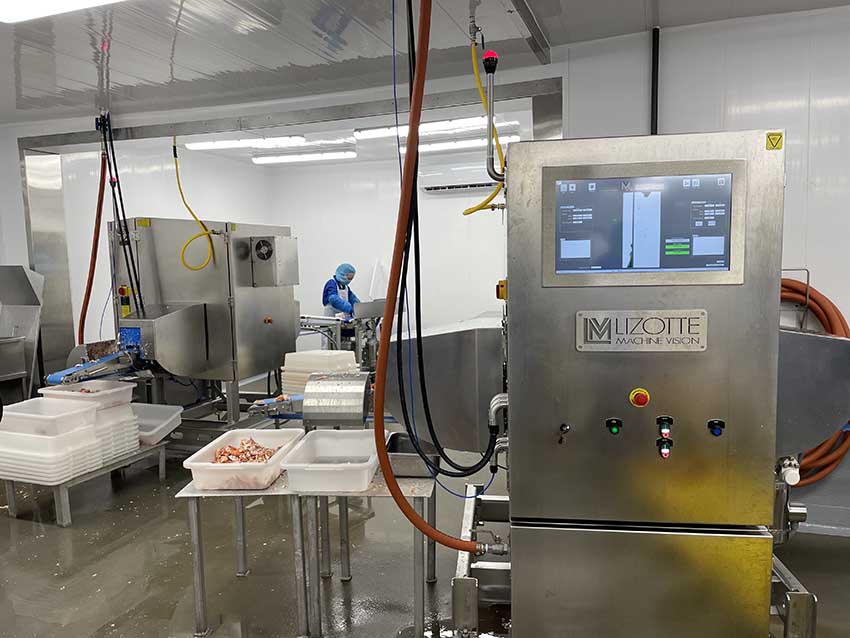
E.E: At what stage is the market where you are currently active?
M.B: The market is definitely growing in all industries that we are in since there’s a lot of labor shortage in the food processing industry. So, the industry is trying to automate a lot in order to relocate employees in jobs where it can’t be done by machinery.
E.E: What can you tell us about market trends?
M.B: In terms of market trends, there’s a lot of interest for quality control and grading system right now in order to automate the manufacturing process. The offers are growing but the demand is also in a rise. So, there’s a lot of interest in using high technology such as x-ray and color inspection to see defects or grading criteria that a human eye can’t see. That way, you are creating a much constant inspection/grading process without any need for manual labor.
E.E: What are the most innovative products marketed?
M.B: Since each system we developed is innovative in a sense, we have many innovative technologies that make us different than other manufacturers in our industry. Here’s a couple of examples of innovative system we did recently.
Chicken breast inspection: Our chicken breast inspection system detects on both sides of each breast any color defects, fat, skin and breast discoloration. On top of that, it can be coupled with an x-ray station to detect bones, stainless steel, non-ferrous metal, ferrous metal, glass and ceramic. Once the system detects a visual defect, it automatically ejects the defective chicken breast out of the processing line.
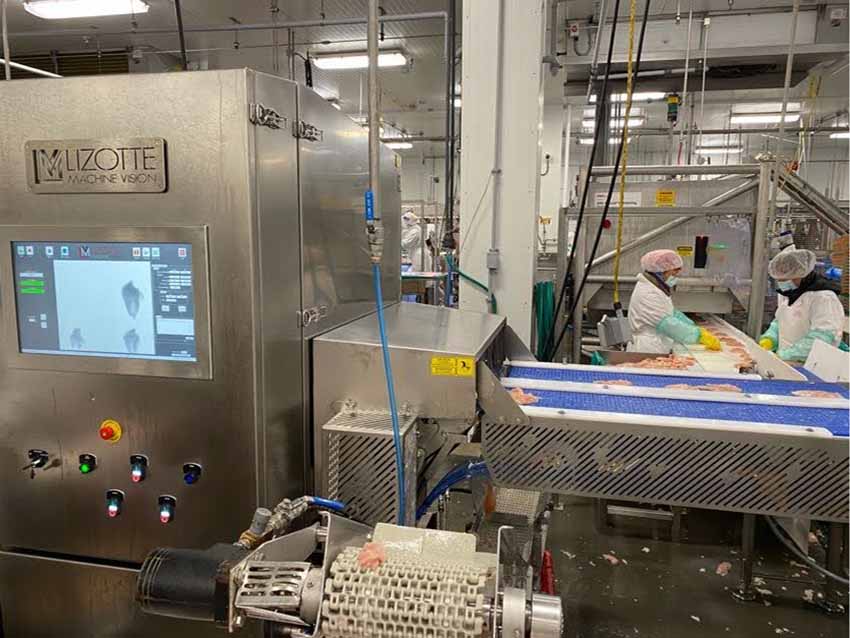
Sorting system with x-ray and color inspection: One of the things we are making different from other sorting system manufacturer is that we can combines x-ray and color inspection in the same system. It allows us to detect internal defects, weight discrepancies, shape defects, size defects along with the defect detectable by color inspection such as: breading defect, blood spot, fat, skin, plastic, rubber, low-density foreign material (plastic, rubber, cardboard, paper, belt pieces) and much more.
E.E: What estimations do you have for 2021?
M.B: 2022 should be our biggest year so far since our foundation in 1985. By adding a lot more protein and different cuts of meat in our portfolio, we are now ready for any types of meat products that needs to be graded or sorted.