Matelex is a young company specializing in the remote monitoring and optimization of the operation of refrigeration installations. Matelex equipment takes measurements on the installations and sends them to a web control interface where they are analyzed and displayed in the form of clear indicators. The Matelex solution provides an answer to environmental and performance issues related to refrigeration by providing new indicators to optimize the operation of refrigeration installations. The Matelex web app allows centralized and remote monitoring of refrigeration plants and alerts in case of leakage, drift or risk of breakdown.
Interview with Marion Lazzarotto, Digital Marketing & CX Manager at Matelex.
Easy Engineering: What are the main areas of activity of the company?
Marion Lazzarotto: Matelex specialises in the connected management of refrigeration installations. These installations, which are essential for the preservation of foodstuffs but also for medicines or vaccines, contain refrigerants. Many of these fluids are greenhouse gases that contribute to global warming and the installations that contain them are high energy consumers.
For example, some of the fluids contained in these installations have a global warming potential 3900 times greater than CO2. In terms of energy, the operation of refrigeration plants accounts for 50% of a supermarket’s electricity consumption.
Faced with installations that sometimes operate in a degraded manner, Matelex’s mission is to provide operators and users with new information that allows them to control installations according to their actual functioning rather than their assumed one.
Our equipment equips more than 2,500 refrigeration plants and has made it possible to avoid the emission of thousands of tons of CO2 equivalent via two major axes:
- real-time leak detection
- reduction of energy consumption
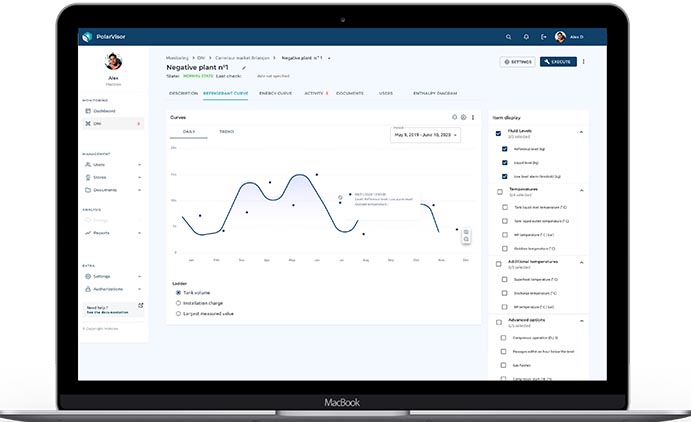
Matelex equipment is capable of learning the normal operation of an installation in order to identify potential deviations and to alert and advise operators on how to improve their performance and reduce their environmental impact.
E.E: What’s the news about new products?
M.L: This year Matelex has developed a brand new web interface for centralized and remote monitoring of installations. This web application, called PolarVisor, provides users with a summary dashboard enabling them to view the entire installation and identify priority actions at a glance using alarms. The interface is enhanced by contour lines, reminders and tips.
E.E: What are the ranges of products?
M.L: Our solution consists of:
A computer called DNI (intelligent level detector): it learns the operation of the system and determines a reference level and triggers an alarm in case of a leak. It is the brain of the solution. The measurement card transfers the data to it, which it analyses and transfers to the PolarVisor wep app.
An Energy Module designed to monitor the electrical consumption of the installation and alert in case of energy drift. It also monitors compressor start-up frequencies and operating times to provide an early warning of potential failure. It also calculates the actual COP (Coefficient of Performance) of the installation.
The PolarVisor web app which displays all the data in the form of clear indicators, KPIs, curves, logs… It allows to launch remote actions such as a recalculation of the reference level but also to adjust the sensitivity of the leak detection, to manage alarms, users…
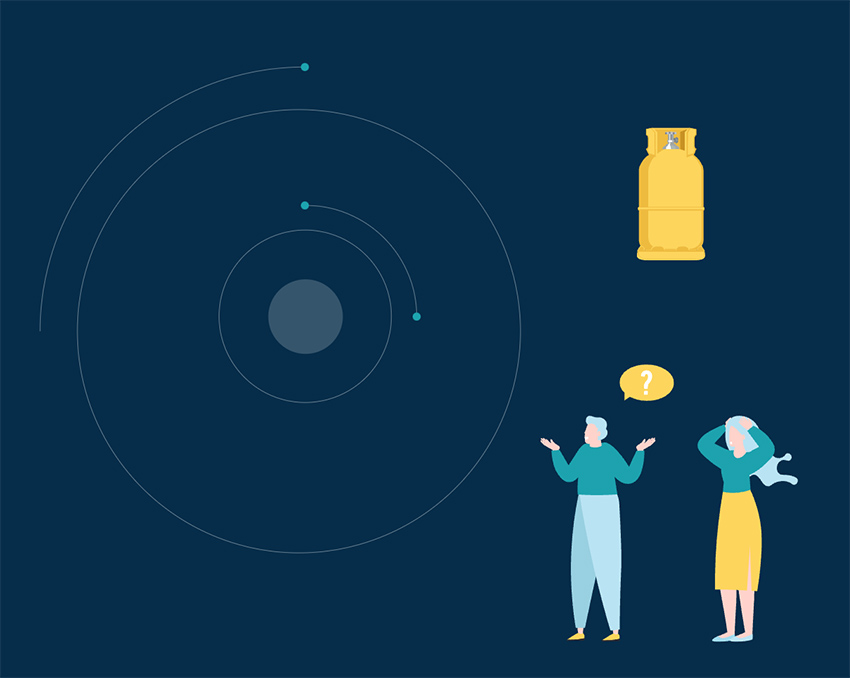
E.E: At what stage is the market where you are currently active?
M.L: The market for leak detection is mature, but leak detection by indirect methods is not yet mature. Direct detection takes place around the plant, with detectors analysing an air sample, portable detectors or foaming products for example. Indirect detection takes place inside the installation with regular measurements, analyzed and reported using an algorithm. This is a big difference because this method allows you to be at the heart of the installation and not miss any leak. Of course, these two methods are complementary because direct detection will make it easier to locate the leak detected by the indirect method.
The market for remote and centralized monitoring for refrigeration is still in its infancy. The IoT in refrigeration is still young and there is a very big potential because it brings:
- New information to improve plant performance
- The possibility of drastically reducing the environmental impact of cooling
- A centralised monitoring platform to simplify the life of refrigeration operators and users
- Refrigerant savings of up to 80% compared to a traditional method
- Energy savings of around 20%.
E.E: What can you tell us about market trends?
M.L: The refrigeration market is moving towards less polluting refrigerants thanks to a restrictive but beneficial European regulation (EU regulation n°517/2014 known as “F-Gas”) for the planet. As the demand for refrigeration increases, it is essential to reduce its environmental impact, which is very significant. The shortage of manpower on the market is not helping, but solutions like ours can save time, be more reactive and efficient and help minimise direct and indirect greenhouse gas emissions.

E.E: What are the most innovative products marketed?
M.L: Our solution is innovative in this market because it makes intelligent data available to refrigeration operators and users. It simplifies management that was previously very technical and sometimes obscure. It offers market players the possibility of having a remote view in real time of this equipment, which is essential to our lives.
E.E: What estimations do you have for 2022?
M.L: 2022 is a key year for us, we are launching a new web app, a new version of our equipment that will allow us to manage up to 4 refrigeration plants. It is also the year of ergonomics, customer experience and user experience. We have created pilot user groups, we are constantly gathering the opinions of our customers and we have them test everything we build. This co-construction approach is key. We are also going to invest in new markets in Europe while keeping our production and development teams in Europe. We are also working on an entry into the USA where we won an innovation award from the ASHRAE experts at the AHR EXPO. We are therefore aiming for reasonable but continuous growth through these investments.