The Czech startup Neuron soundware develops technology for automated predictive maintenance of industry machinery. Using sound/vibration analysis of the machines, the technology enables it to detect imminent failures that would mean costly repairs and production outages. The technology is based on the combination of artificial intelligence built on neural networks and machine learning, and IoT device nBox, which is receiving and processing the data from sensors. The Neuron soundware technology is being used by clients in their operations all over the world from the Prague Public Transport Company to the manufacturer of semiconductors in Malaysia.
Interview with Pavel Konečný, CEO of Neuron soundware.
Easy Engineering: What are the main areas of activity of the company?
Pavel Konečný: At Neuron soundware we supply technology as a service to the industry. This makes us different from most of our competitors. When we monitor industrial equipment, it is not a one-off job, but a continuous remote online monitoring with data processing through AI. By its very nature, AI is constantly learning, and so the service is always improving due to continuous learning about the behavior of the machine being sensed.
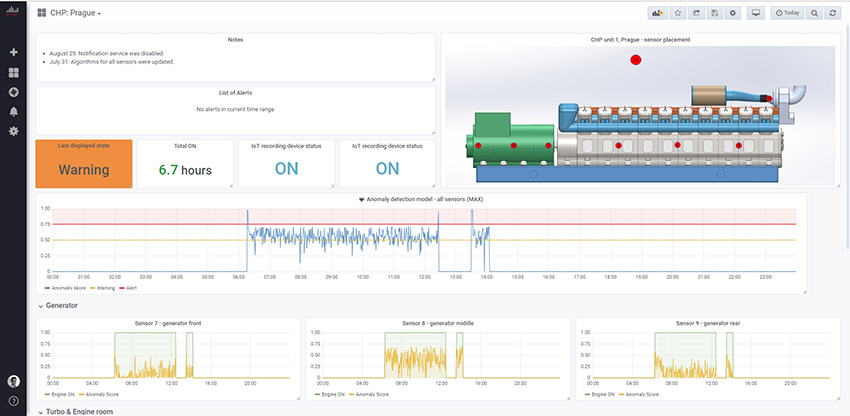
The advantage of technology as a service is sustainability and reliability. Diagnosis is not based on one software version or one machine state, but on the continuous application of the latest knowledge across devices.
An example is the outdoor operation of transformers, whose sounds change as their temperature changes over the year. If we were to measure sound or vibration in a single measurement, we would measure a result that would indicate an anomaly by the change in temperature. Thanks to artificial intelligence, we know how the measurement outputs change continuously during different temperatures, so we don’t have to send ‘false alerts’ to the customer.
E.E: What’s the news for 2021 about new products?
P.K: There are many changes. We have developed a new HW that reflects the specific needs of predictive maintenance. We are now enabling the use of standard IEPE (Integrated Electronics Piezo-Electric) sensors, which will significantly improve the quality of sensing of rotating machine behaviors.
We have also made installation easier for customers by standardizing procedures with those of conventional engineering diagnostics. This has reduced the complexity of the installation, which can now be handled by a typical maintenance specialist with video instructions.
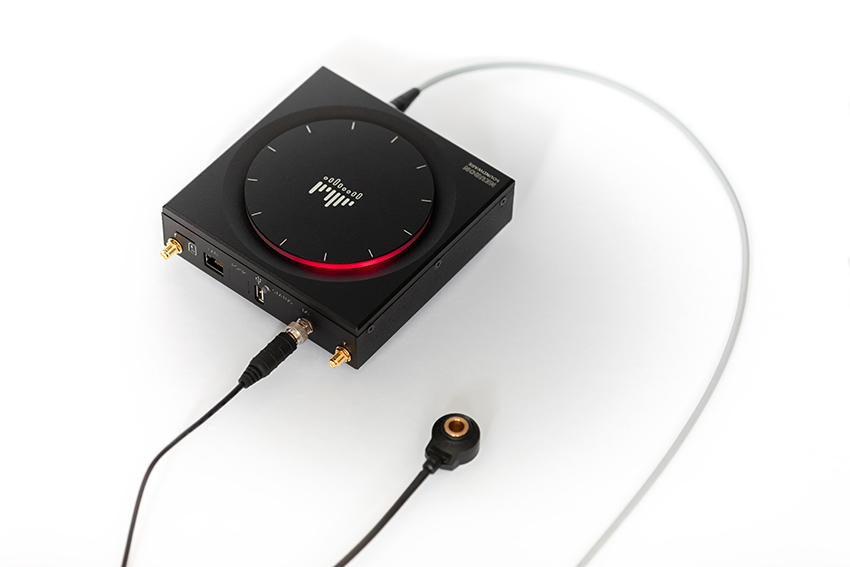
Additionally, we deployed the assisted alert function. The customer now has the possibility to consult the cause of the problem on the machine and how to fix it remotely with our specialist. In addition, we have implemented a machine library in the machine condition assessment, which in practice means that our service is enriched with standard vibrodiagnostic methods and their automation.
We have found differentiation in the market through the diagnosis of specific types of faults for specific types of machines, most recently escalators and pumps. With this knowledge, we are expanding our services further around the world.
Finally, we have improved data processing. Our IoT device processes the sound and vibration data of the machine directly on the equipment (on edge), i.e. directly in the factory. This results in a safer data transfer in terms of the transmission path. If the internet goes down, it doesn’t matter, because the digitized diagnostics takes place directly at the customer’s site.
E.E: What are the ranges of products?
P.K: The first key application of Neuron soundware technology is predictive maintenance, where we focus on accurate diagnosis of specific machine faults. The second is process control. With our technology, we can shorten the production cycle through accurate sound diagnostics of the product output. For example, for gravel crushers, scrap metal melting or colour pigment mills, we can control product quality. This has a characteristic sound that we monitor at a certain stage of the process. Instead of a timed production run, the entire process can take just long enough for the product to reach the desired consistency, shape, granularity, etc. This saves customers up to 15% of production time, which can be used for further production.
E.E: At what stage is the market where you are currently active?
P.K: The market where our technology is applicable is growing at 25% per year and will more than double by 2024. This is a huge opportunity and makes us confident that Neuron soundware will see further unstoppable growth in all markets.
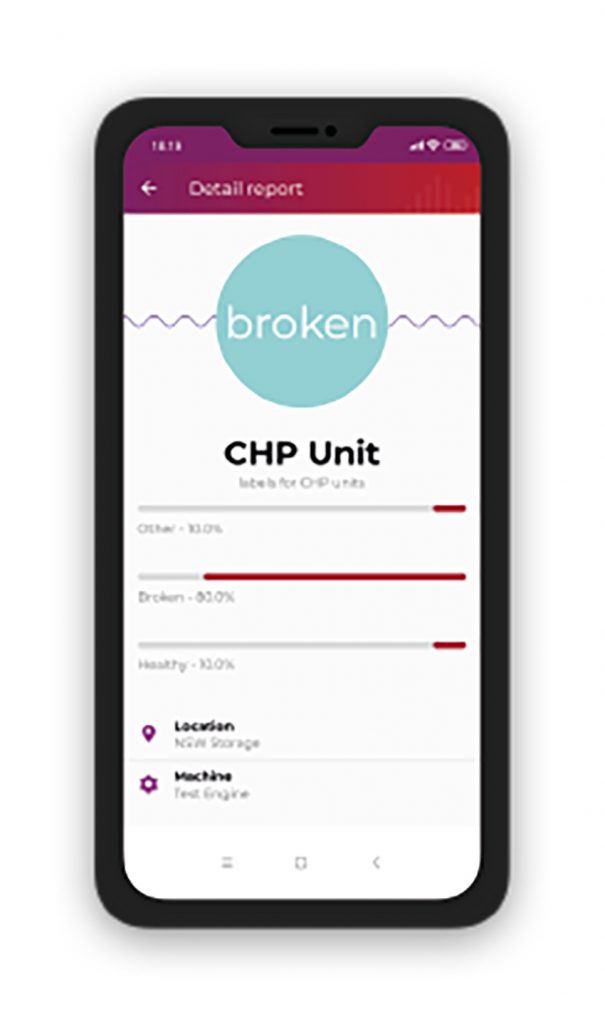
E.E: What can you tell us about market trends?
P.K: Automation is a frequently mentioned topic, as well as the digitalization of maintenance, where our experience at a gearbox manufacturer for the automotive industry is an example. A malfunction on a helium compressor without early identification meant three major things: replacement of the entire equipment, damage to the actual gearbox pieces and, last but not least, up to 16 hours of production downtime. With us, the manufacturer automated maintenance through continuous remote monitoring of the equipment’s condition. It now knows exactly when a specific component of the equipment needs to be replaced to keep it running.
The problem of keeping know-how in the company is also becoming more and more acute due to dwindling experts and senior employees retiring. The drive to retain know-how is leading to the translation of knowledge into digital solutions to replace the dwindling human workforce.
All of these trends have been underlined by the pandemic, where maintenance has had to be carried out remotely as much as possible with minimal physical intervention. In addition to our technology enabling automated machine monitoring and remote maintenance management, we also have in-house diagnostic experts who can assist the production manager in determining machine health and prioritizing maintenance for the entire machine fleet. This is how we operate in pulp and paper mills, for example, where we have excellent experience.
E.E: What are the most innovative products marketed?
P.K: We were among the first in the world to use automated sound analysis and on-site data processing (edge computing) on IoT devices. This brings benefits in data processing speed, as well as eliminating the security risks of transferring data to the server and making it easier to connect to the local data infrastructure.
AI algorithms help pre-process data in the IoT device in real time. Once the data is preprocessed, we engage an expert to accelerate the device diagnostics and increase its efficiency by applying our own analytical expertise from the industrial environment.
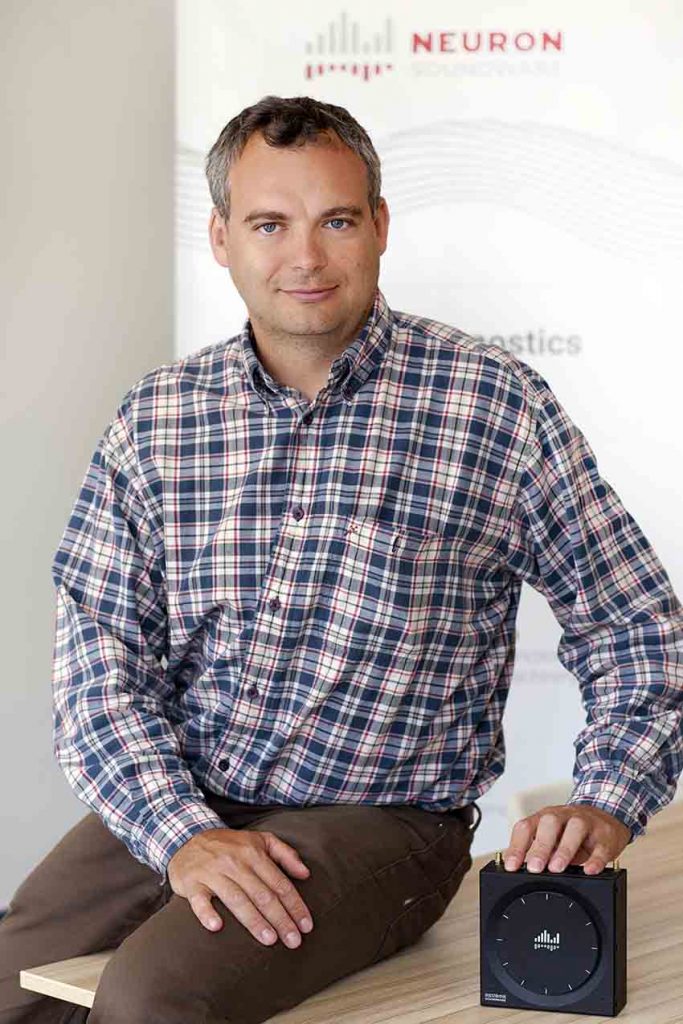
E.E: What estimations do you have for 2021?
P.K: We expect record equipment orders from Western Europe and Asia. In both markets we are seeing a greater readiness for innovation, expensive and scarce skilled labor, and larger budgets allocated specifically for innovation.
In our neighbors in Germany, for example, we are seeing long-term thinking 20 years ahead. See, for example, Germany’s investment in renewables and electromobility. They see into the future; they think in longer time horizons. That pays off in the long term. The same will be true for the digitalization of maintenance. The vision of Industry 4.0 will thus soon start to come to fruition.
In the same way, both Korea and China are very rational in their investments in digitalization. They see the future in investing in modern technology and are making much more long-term decisions than we are used to seeing in other markets.