NPPower, is a start-up from Slovenia, that is transforming innovative ideas into high-quality solutions, and has just entered the international market of AM with their Malachite 3D printer for metal. Focusing on open minded R&D and clever problem-solving, its young team aims to put the company on the global map of additive manufacturing.
Interview with Maša Virant, Administrator of NPPower.
Easy Engineering: What are the main areas of activity of the company?
Maša Virant: The company’s main drive is to make cutting edge technology accessible and affordable to individuals as well as businesses, our focus being on finding solutions in the quickly evolving and expanding field of additive manufacturing. This mindset has also taken center stage during the process of design and creation of our new 3D printer for metal, the Malachite. Regardless whether you want to print machine parts with intricate geometries, hidden channels and voids or challenging internal passages, produce functional prototypes in just a matter of hours all the while saving on material, or just explore your imagination by creating unique and stunning designs and jewelry, the Malachite 3D printer for metal undoubtedly deserves your attention.
E.E: What’s the news about new products?
M.V: The Malachite is the result of 2 years of extensive research and development and has certainly turned many heads during it’s unveiling at this year’s Formnext in Frankfurt Germany, owing to its sleek design and compact size while nevertheless boasting a build volume of Ø125 x 100 mm.
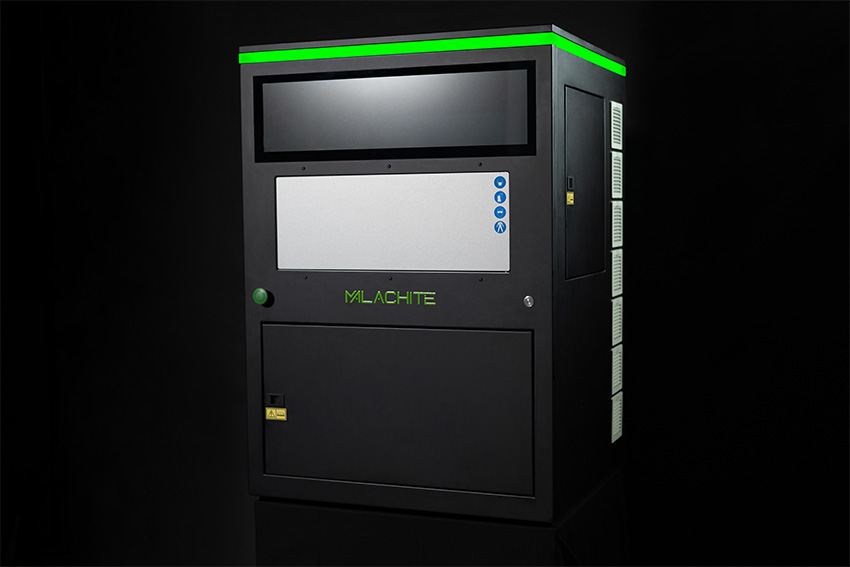
Measuring only 715 x 705 x 1020 mm (WxDxH) and weighing 220 kg, it’s easily one of the smallest LPBF machines around, giving a whole new perspective on the term tabletop 3D printer. What is more the entire printing process is additionally accelerated by a double-piston powder loading system that adds metal powder from both the left and the right side of the print bed in turn, greatly minimizing coater downtime.
The eye-catching printer stands out from the crowd with its unique 360° LED status bar, making the outdated semaphore obsolete and enabling monitoring of the printing process from anywhere in the room. Combined with a precise in-chamber camera that offers a general and detailed view of the print bed alongside an intuitive user interface, it makes operating the Malachite simple and straightforward.
By implementing a 200 W fiber laser and galvo scanner, the printer allows for swift and efficient creation of complex and unique objects that result in thin-walled as well as intricate lightweight designs. With its remarkable printing flexibility, it is suitable for printing all non-reactive metal powders such as Cobalt-Chrome, stainless steel, Bronze, Brass, Nickel, etc., furthermore offering a layer thickness ranging from 15 to 85 µm. It is intended for both free-standing floor- and tabletop use, but can also come with a matching stand suitable for powder canister and equipment storage. The exceptionally low power consumption averaging 500 W in addition to an average inert gas consumption of 0,3 L/min point toward the Malachite’s sustainability and longevity.
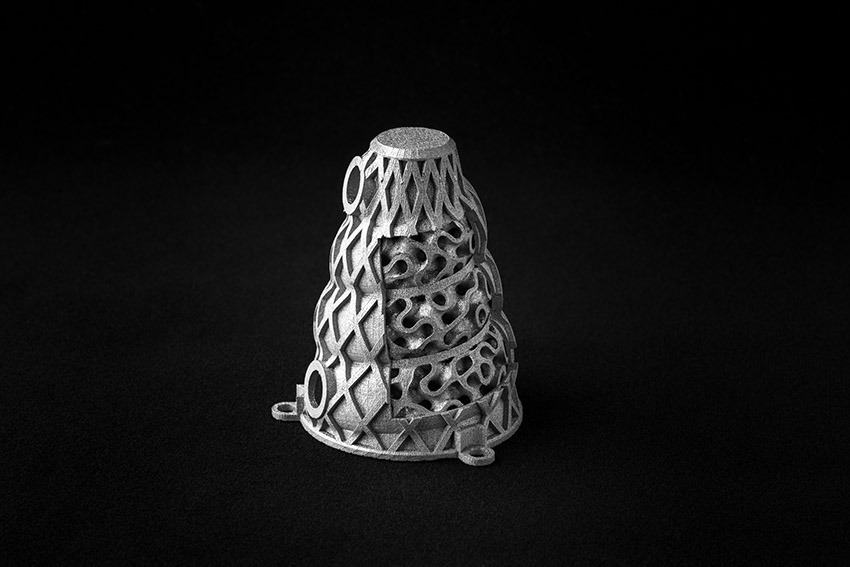
E.E: What are the ranges of products?
M.V: We have just begun our journey down the path of metal additive manufacturing, but we nevertheless have big plans for the future. To begin with we intend to expand our portfolio with a couple of metal printing machines with greater build volumes. The obvious next step after that, which is already under way, is to introduce a 3D printer suited for working with all reactive metal powders.
E.E: At what stage is the market where you are currently active?
M.V: The AM market in general is just beginning to blossom and we believe it to be a great opportunity for us that Slovenia’s AM market for metal is virtually untapped as of yet. With this unique position and a product with characteristics that are a novelty even in light of the global industry, we truly aim to achieve something great.
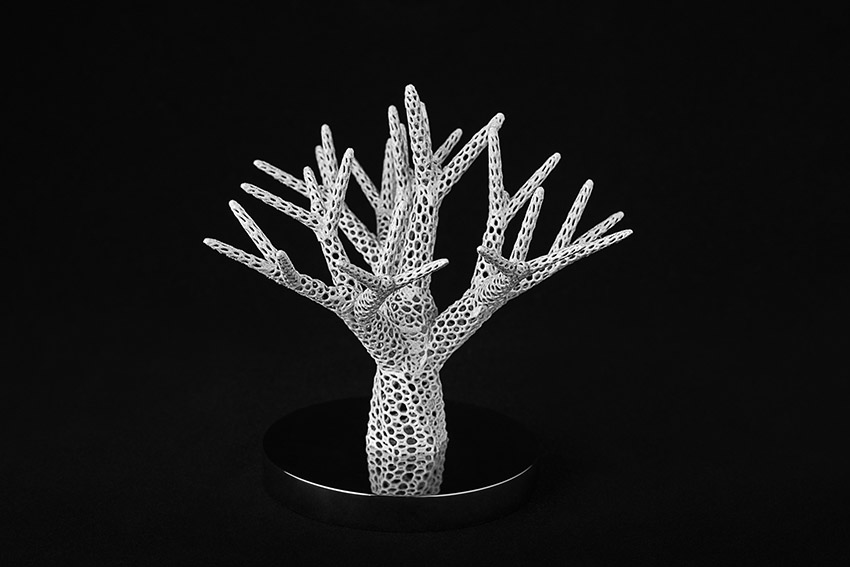
E.E: What can you tell us about market trends?
M.V: Since additive became more widespread in the 2000s the industry has evolved and grown significantly, even more so in the past year and a half during the COVID-19 times. Businesses globally have seen the great advantages and benefits of implementing additive technology in their everyday operations, revolutionizing current processes, setting an exponential upward trend. The future of metal additive manufacturing will be extremely exciting.
E.E: What are the most innovative products marketed?
M.V: It would be safe to say that anyone stepping along the path of AM is headed for the future. But whether they actually leave a mark is a question of constant improvement and innovation alongside having a good ear for consumer needs. With the growing demand for quick, simple, and cost-effective production of parts taking the forefront, our company and products have a clear and advantageous position in the international market. We intend to stand with the innovators, helping customers fulfil their potential by offering them the solutions their businesses require.
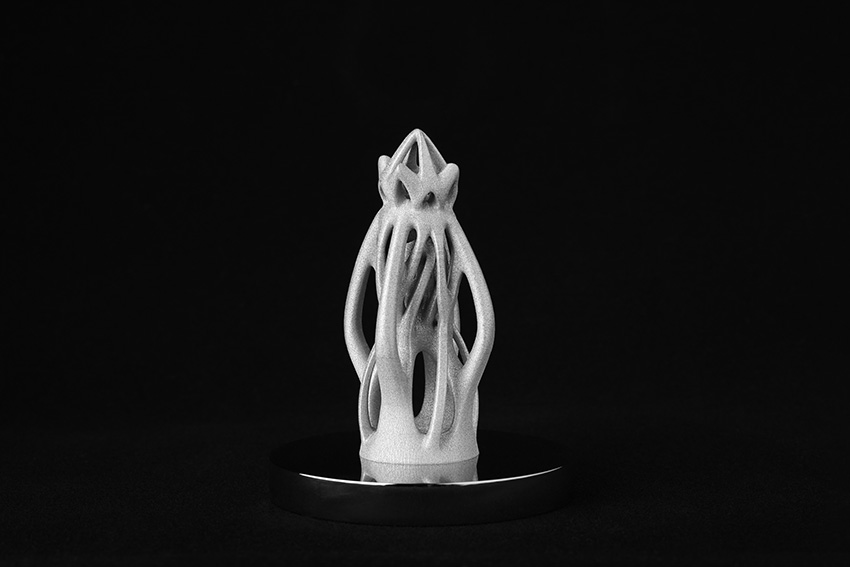
E.E: What estimations do you have for the rest of 2022?
M.V: The year 2022 has been really big for us, seeing how we launched our first 3D printer for metal on this year’s Formnext. We have no intention of slowing down in the coming year though, as we will be taking on the local market at next year’s IFAM fair in Slovenia and already have plans of cooperation with schools in Slovenia to educate younger generations of the possibilities of metal AM. Be sure to follow us on social media and LinkedIn to stay up to date with all that’s going on.