The Plastics Engineering Group (PEG) is a team of around 15 highly experienced simulation engineers. The main focus and experience lie within the process and mechanical simulation of plastic components, molds and assemblies. Within the past 30 years more than 16.000 projects (meaning parts and / or molds) have been successfully simulated and a large majority of these have – as a result – been optimized in an early stage of development.
Interview with Benjamin Wittmann, Process Engineer at Plastics Engineering Group (PEG).
Easy Engineering: What are the main areas of activity of the company?
Benjamin Wittmann: The customer base of The Plastics Engineering Group is very diverse. In the past 10 years it switched from being a large percentage Automotive industry to many other thrifting industries, such as the Medical, Consumer Goods or Packaging industry. Within these industries we are working closely with OEM’s, mold makers and plastic part manufacturers of all sizes to help improve their part designs from the first step on – meaning from an early design stage on. Whether it is about the producibility, the optics or the mechanical durability of parts, whether the material is filled or unfilled or heavily reinforced – we are able to align the simulation as closely as possible to reality.
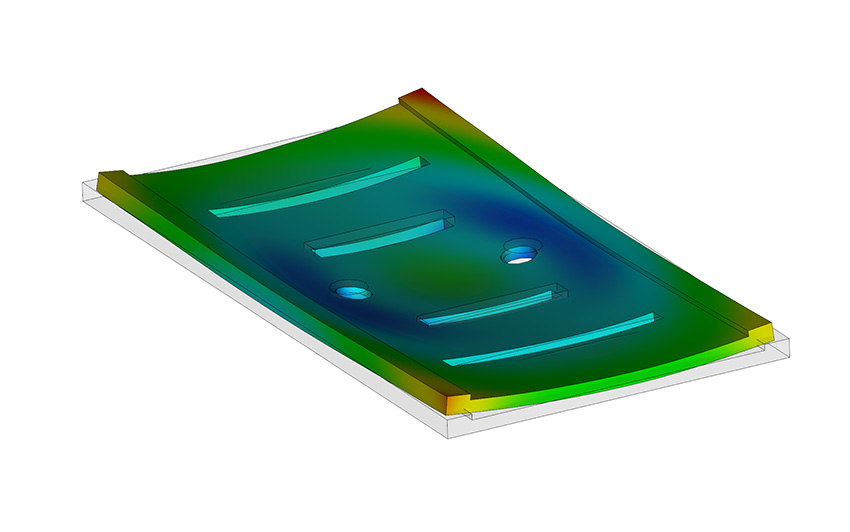
E.E: What’s the news about new products?
B.W: With the development that goes along with the needs of our customers we always adjust our services onto what the market shows what’s required and what not. Additionally, we always adjust and develop our service portfolio onto the development of our software in use – which is Autodesk Moldflow Insight on the process simulation side. Since the software version 2021 for example, chemical foaming simulations are now possible and with that we have strongly increased our expertise in chemical foaming and provide this as a service as well. The same accounts for our material data services – due to the chemical foaming now being available in the software, we now also offer the material characterization of such materials through partner labs.
Currently we are rolling out our new product called PEGASOS, which enables a quick, easy and inexpensive way to receive simulation results without having to buy a software tool yourself nor to regularly pay for consulting services that are more expensive. With PEGASOS the only required input is the CAD data, one or multiple injection locations and the material of choice. Shortly after that the simulation results will be played back to the customer, who now has the choice of either interpreting the results himself or ordering an interpretation session with one of our experts for 30 to 60 minutes. This helps our customers to be more flexible and to receive services much more adjusted to their financial and intellectual needs.
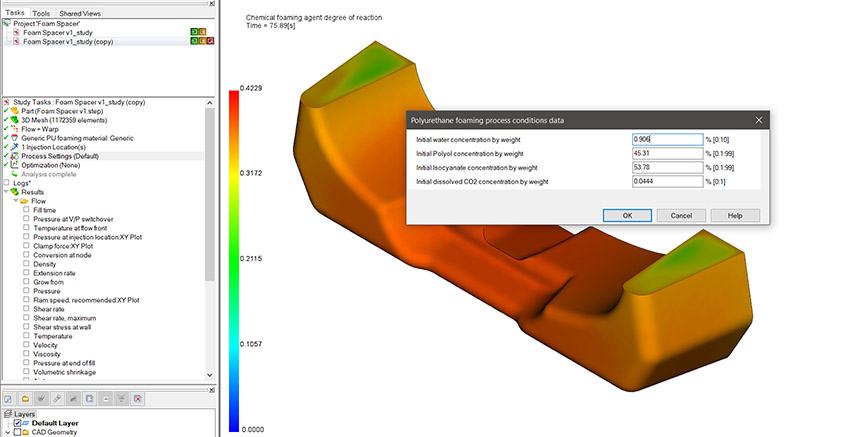
E.E: What are the ranges of products?
B.W: Our products and services include the simulation of the whole product lifecycle from the first design phase to mold design and finally production optimization. Customers contact us in all sorts of phases. New customers mostly get in touch due to projects gone wrong and therefore due to the need of troubleshooting. By working with us during such projects most companies realize the possibilities of an early use of simulation – and stick with us on a long run.
In any case we are providing our customers with a brief consultation of the current status. The following solution making is always as individual as each of our customers projects.
E.E: At what stage is the market where you are currently active?
B.W: Due to our customers ranging from small engineering bureaus to medium sized mold makers to large OEM’s from all industries the stages vary heavily. Mostly the markets are already highly developed, but there is still a lot of potential especially in emerging markets such as the medical industry as well as companies which currently realize their lack of digitalization within their development processes.
E.E: What can you tell us about market trends?
B.W: One market trend is definitely integrative simulation – meaning the transfer of fiber orientation or weld line positioning from the process simulation onto mechanical simulation.
In the past couple of years, we implemented software solutions consisting of Autodesk Moldflow and Autodesk Helius or MSC Digimat at more than 5 customers sites, accompanied by initial and advanced training as well as consultancy during the implementation stage. After one to two years these customers have been reaching the stage of complete autonomy and a fully developed integrative simulation department – as well as much better part quality prediction.
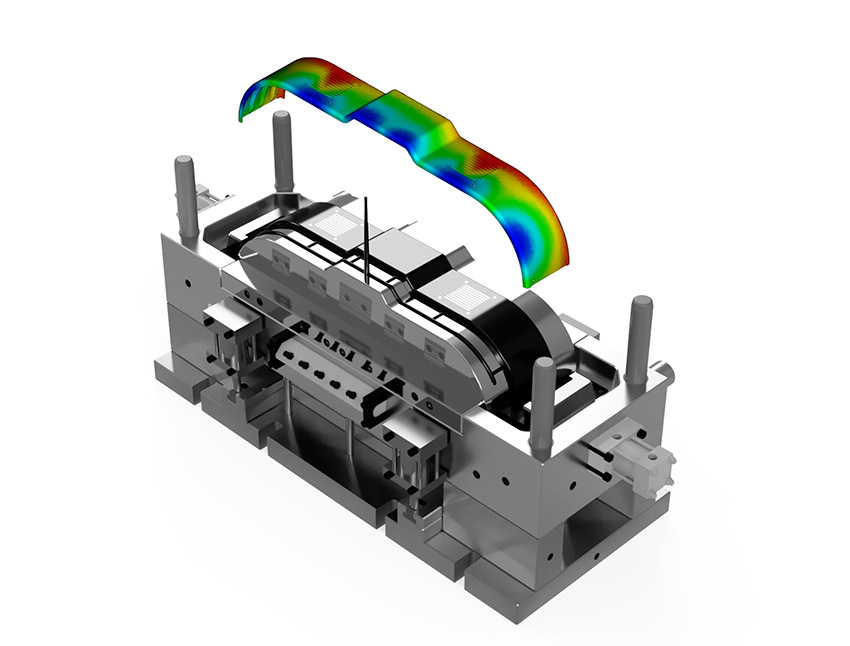
E.E: What are the most innovative products marketed?
B.W: One innovative product is the previously named integrative simulation. Other innovative products are the constantly developing special processes like reactive molding, foam injection molding, gas injection molding, compression injection molding, resin transfer molding and many others. More and more companies integrate these processes into their portfolio and by working together with PEG they can ensure future success.
E.E: What estimations do you have for 2022?
B.W: In 2022 we expect an additional increase of projects coming from new automotive OEM’s as well as suppliers, mostly from the EV sector. But on top we especially expect an increase in aerospace and aviation as well as in the medical sector. Due to the specifications increasing more and more, only few companies will remain having the luxury of not profiting from the insights which simulation services obtain.