PLATIT is a leading manufacturer of high-tech PVD and PECVD coating units for tools and machine components. The company is headquartered in Selzach (Switzerland) as a part of the family-owned independent Swiss technology group BCI Blösch Group. PLATIT built up its own service, support and sales offices in Europe, North America and Asia. These are complemented by a broad network of distributors and partners worldwide. Currently there are more than 550 PLATIT coating systems installed in the world.
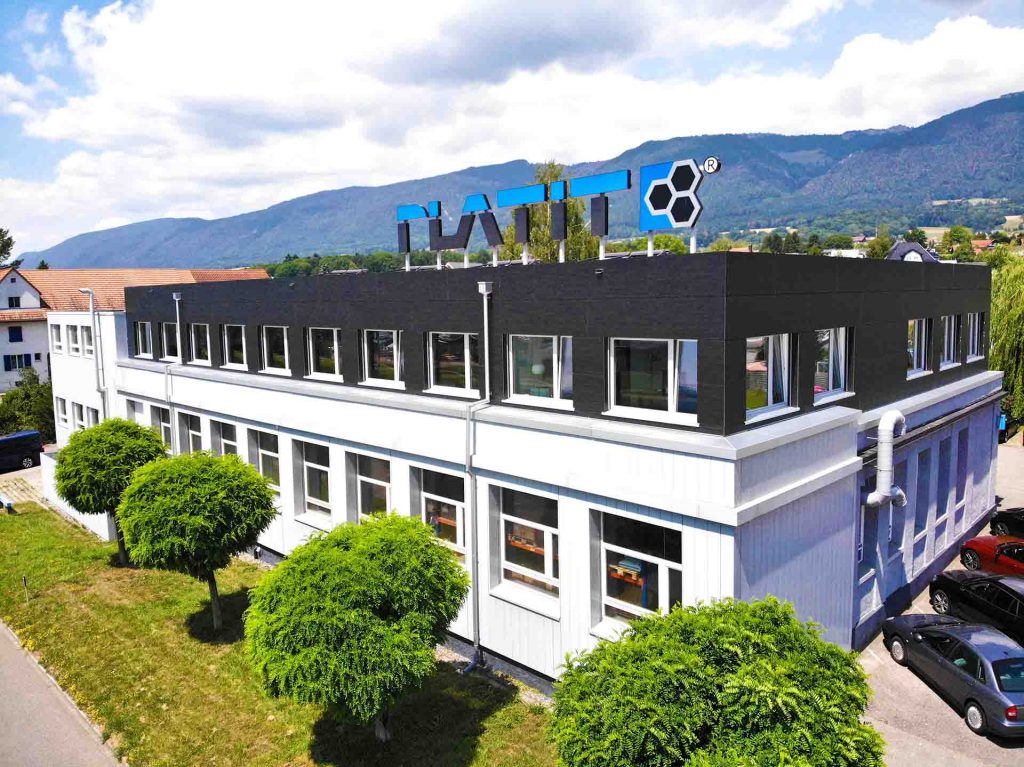
Easy Engineering: What are the main areas of activity of the company?
PLATIT: We set the focus on providing standard coating units for coating tools and machine components with standard market sizes, but also manufacture tailor-made custom coating solutions for special requirements.
In combination with complete solutions for upstream and downstream steps of coating – such as decoating, edge pre-treatment, cleaning, post-treatment and quality control – PLATIT turnkey systems are ideally suited for seamless integration into a tool manufacturing and regrinding process. This is where a customer can look back to almost three decades of coating experience together with us. By providing this know-how to customers, PLATIT is opening up for long-term relationships. The vision is always to enhance the business of the customer as a partner.
This vision is supported by our own service centers in Europe, North America and Asia as well as cooperations with worldwide partner companies, as we constantly strive for fast incident management and short delivery times for spare parts by being very close to the customers.
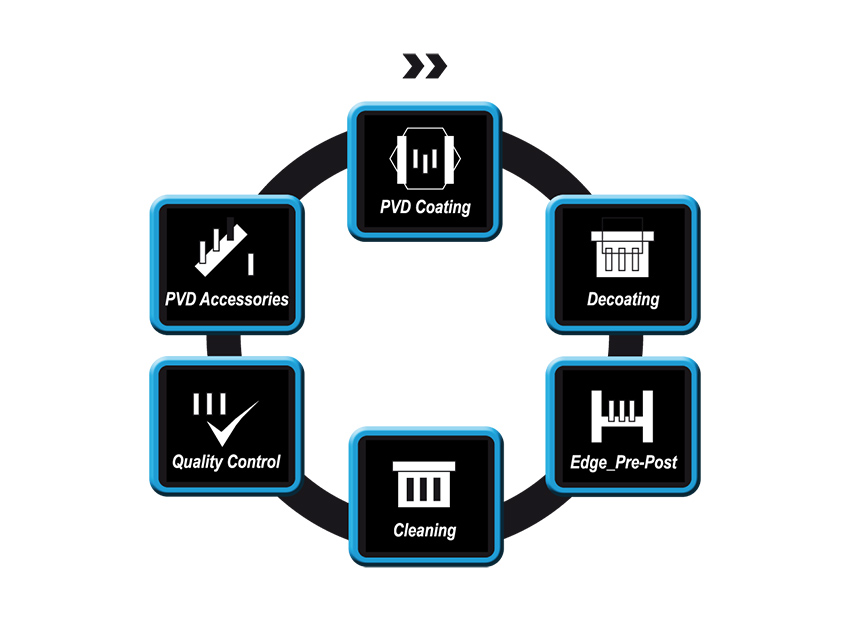
E.E: What’s the news for 2021 about new products?
PLATIT: In 2021 PLATIT will further develop its standard coating units to offer the next generation of compact machines with shortest cycle times. These systems are built to provide highest quality PVD and PECVD coatings for various nitride, oxide and DLC coatings. Keeping that in mind, we set further focus on a user-friendly and flexible software enabling the customer to customize coatings based on their needs.
PLATIT’s engineers and technicians in the Custom Coating Solutions division in Switzerland advise customers and design, develop, manufacture and program systems according to individual requirements. One of our most exciting projects in 2021 is a dedicated coating system for coin minting applications to ensure dustless coatings with good adhesion for the dies to accurately replicate highly detailed relief structures. Using SPUTTER technology, supported by our LGD® technology (lateral glow discharge), we can guarantee smooth high-quality coatings without droplets and no layer defects.
E.E: What are the ranges of products?
PLATIT: The variety of tool geometries and applications requires manufacturers of coating equipment to offer a wide range of technical solutions to best fulfill customers’ needs. Therefore, we offer numerous high-tech standard and custom coating solutions with modular machine designs, high flexibility and good user-friendliness. Profound competencies in cathodic ARC, SPUTTER and HiPIMS technology allows us to integrate these technologies into hybrid processes, creating solutions for different applications. Our open-source philosophy is the main driver that allows customers to adapt coatings to their specific requirements and individual needs. With the highest coating performance in dedicated application fields, our customers can differentiate themselves from the market standard with the help of our engineers and Ph.D.’s.
E.E: At what stage is the market where you are currently active?
PLATIT: The focus of PLATIT’s business activities has been on the tooling market, but the flexibility of the machine designs has allowed PLATIT to expand into further industries. PLATIT’s custom coating solutions and dedicated coatings do not have limits in applications, going from cutting, forming and tribological components towards other markets and requirements.
By using PLATIT’s technology, customers can profit from PLATIT’s know-how. The systems are open to engineers, their parameters and recipes can be customized and further developed based on specific needs. We also value interactions, discussions and sharing knowledge with technology users, as both parties benefit from transparency and openness.
E.E: What can you tell us about market trends?
PLATIT: The market for PVD and PECVD coating is moving towards sustainable environment friendly solutions. This trend in based on major automotive trends for sustainable processes for instance. Coatings result in higher productivity and a longer lifespan of a base material. As a substitute for hard chrome, coatings based on DLC (diamond-like carbon) increase the hardness (at ambient and elevated temperature), oxidation resistance and residual stress, being at the same time recyclable and eliminating the need for hazardous Cr6+.
The hardest DLC coatings in the market are based on ta-C (tetrahedrally bound hydrogen free amorphous carbon). They are characterized with over 50 percent of sp3 content allowing a hardness from 30 to 50 GPa. With a guarantee for stable processes and low maintenance intervals in its coating units, PLATIT provides unique features for customers.
To utilize synergy effects, there are also increasing trends for applying PVD coatings in new industries. As for example, the markets for medical technology, industrial machinery and decorative industry are anticipated to grow in the use of PVD coatings in the future.
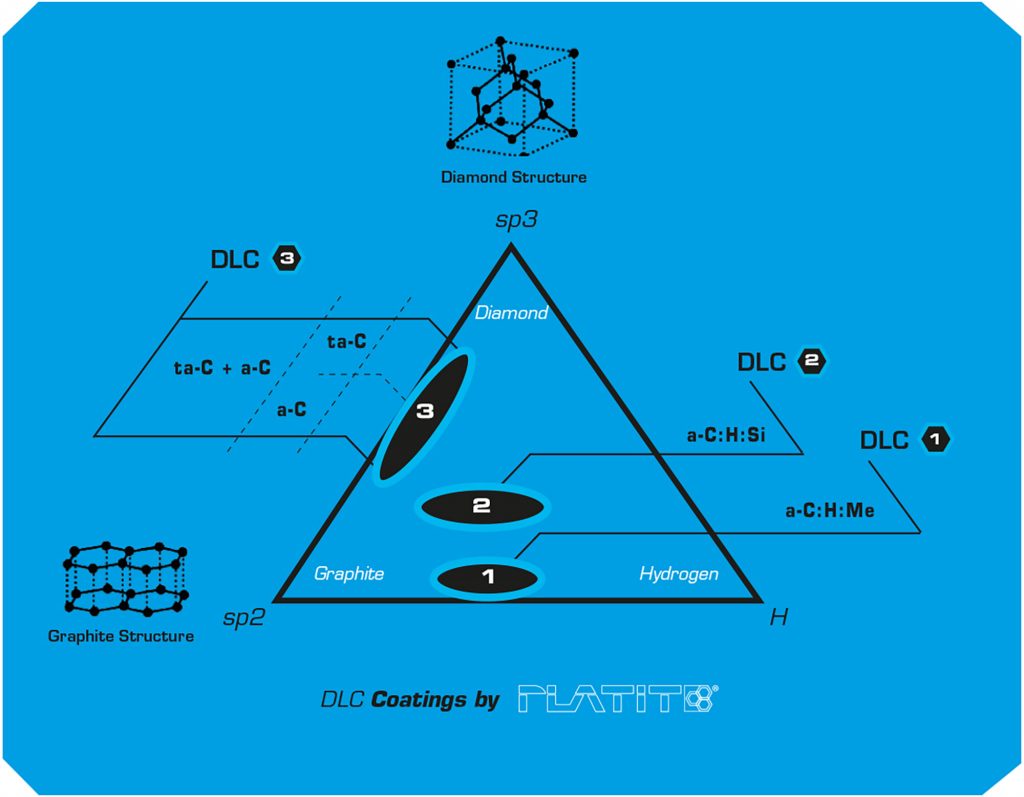
E.E: What are the most innovative products marketed?
PLATIT: Due to its modular design and the range of available technologies, PLATIT’s Pi411 PLUS is the most flexible coating unit. Its basic configuration as an ARC unit with three rotating cathodes inside the door can be modularly upgraded on-site with an ARC or SPUTTER central cathode as well as with PECVD and OXI processes. Unique to this unit is also the availability of LACS® hybrid technology, which allows for the simultaneous deposition of coatings using both ARC and SPUTTER technology.
The broad variety of configuration options as well as the flexibility made possible by the rotating cathodes enables the user to develop customer-specific top-performance coatings. Thus, this coating unit addresses the needs of customers who are seeking maximum flexibility with a full range of coating technologies easily accessible in one machine.
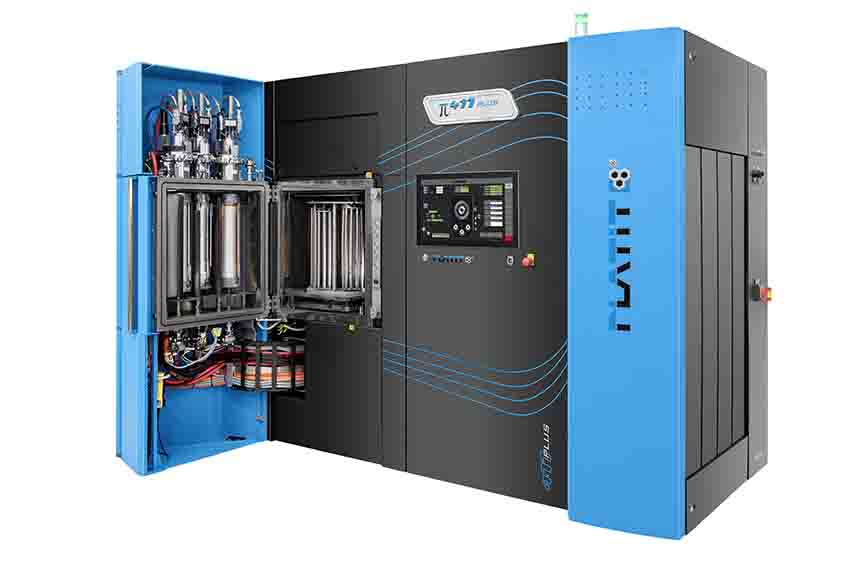
E.E: What estimations do you have for 2021?
PLATIT: 2021 favors companies with flexible business models and fast adaptability. Dedication and knowledge sharing have become essential in the coating world. We believe that it is important to be very close to the customer, more than ever. That being said, we do not only strive to be more local than ever, but also to help the customer experience our coating systems and technological solutions through digital channels.
PLATIT AG HEADQUARTERS
Eichholzstrasse 9
CH-2545 Selzach
+41 32 544 6200