Polysecure GmbH has developed an innovative technology platform of marker materials and detection methods. On this basis, products and materials can be directly marked, practicably authenticated, tracked in a tamper-proof manner and reliably sorted. For the circular economy of the future, Polysecure has developed the disruptive sorting technology Tracer-Based-Sorting (TBS). Packaging waste can now be sorted reliably and efficiently into all desirable fractions.
The company was founded in 2009, currently employs more than 30 people and is based in Freiburg in the Black Forest in Germany.
Interview with Jochen Moesslein, Co-founder & CEO, Polysecure GmbH.
Easy Engineering: What are the main areas of activity of the company?
Jochen Moesslein: Our business areas are mobile product authentication by own fluorescent markers and detectors, tamper-proof individual product tracking by the random 3D pattern of our fluorescent particles, material labeling by our own sequence-defined macromolecules and Tracer-Based-Sorting (TBS) of articles and material flakes by our fluorescent tracers and our own sorting devices and machines. Due to enormously risen relevance of circular economy, especially our disrupt sorting technology creates a lot of interest.
Indeed, TBS is currently the most promising innovation to better sort especially plastics and likewise achieve higher recycling rates. Our particle pattern technology is a second potential game changer: If the fluorescent particles are mixed e.g. in plastics and processed in products in the next step, the three-dimensional position of the robust particles in the matrix material is determined stochastically.
Due to the strong upconversion fluorescence this random pattern is visible and measurable like a fingerprint. It can be perfectly identified at every stage of the product cycle. And in the near future, all you need is a smartphone for the detection process.
E.E: What’s the news for 2021 about new products?
J.M: Our new product is the development of organic marker particles (called „Poltags”) for information storage, authentication and recycling monitoring at molecular level on sequence-controlled macromolecules. Synthesized from different monomers with great precision and efficiency. These “Poltags” are more robust than plant DNA, for example, and can be distributed very easily and homogenously into plastics: quantities in the ppb (parts per billion) range can already be measured with mass spectroscopy. There are many applications for this: a product can be traced back to its authentic batch (in liquids and massive material). In the future we are able to measure the recycling content in an end product and develop a „product passport”, the use of incorrect materials can also be detected.
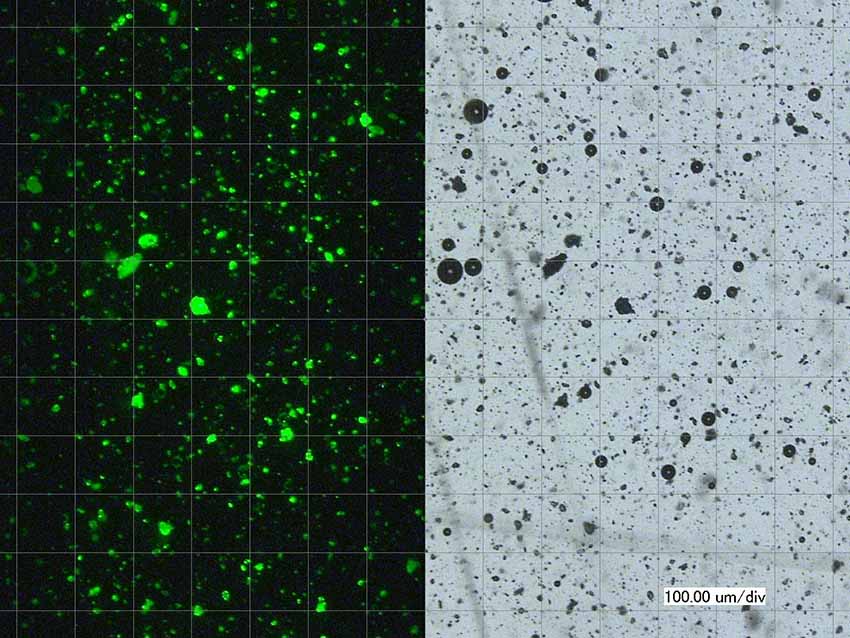
E.E: At what stage is the market where you are currently active?
J.M: Our marker technologies are available on the market, and in recent years we have marked around 70,000 tones of plastics. We have a close partnership for many years, for example with a window manufacturer who marks PVC windows and can then separate PVC containing glass fibers from PVC not containing glass fibers. In addition, we work in close cooperation with major manufacturers and work with scientists from the Pforzheim University of Applied Sciences and the Karlsruhe KIT on the continuous further development of our technologies.
E.E: What can you tell us about market trends?
J.M: The national and international market is characterized by strong competition, low crude oil prices and a lack of innovative waste management, which leads to a lack of innovation and low recycling and recovery rates for plastics. Therefore, we have a need for politics to be more demanding, which is why we are working with other companies and institutions to increase political pressure to reuse plastics and introduce minimum recycling rates. We are also campaigning for new technologies in sorting.
In additional, we are in a strong competition with other companies producing alternative marking technologies. A marking has recently been carried out mainly by the competitor system Digimarc by means of the “watermarks”. The goal is similar to that of Polysecure: to develop a solution for high-speed sorting of plastic packaging with Digimarc barcodes in order to increase recyclability. In our opinion, the implementation of this technology is less efficient and less ecological due to e.g. high ink consumption and there is a lack of evidence that the technology works.
E.E: What are the most innovative products marketed?
J.M: The most innovative product is for sure our Tracer-based-sorting (TBS). We reliably achieve 95 to 100 percent detection – consistently and reliably. This is possible because we sort differently with TBS complete. Conventional processes sort cascade, which means that if you have 10 fractions from the yellow bag, you need at least 9 sorting stages because you can only blow off one fraction at each sorting stage. The more fractions you have to sort, the more sorting stages you need and the higher the costs. Our approach, on the other hand, is first of all separate the material and then pass it through a detection station. In the detection station, precise tracer recognition, object recognition via artificial intelligence and color recognition take place. Afterwards, the sorted fractions are placed in containers. This process is easily scalable – if a fraction is added, an additional container is simply added. So, our approach is to organize plastic sorting like letter or parcel sorting.

E.E: What estimations do you have for 2021?
J.M: Right now we are building the pilot plant for the TBS technology at our campus in Freiburg. For the high-quality recycling of plastics, a sorting technology is indispensable that reliably and efficiently sorts all objects according to defined fractions (> 99 purity). This is made possible by the TBS technology thanks to two innovative main aspects:
The use of fluorescent markers makes it possible for the first time to identify a separation feature that is independent of the packaging material. The markers are oxosulphide compounds doped with rare earth metals specially developed by Polysecure. Their fluorescence property is unique, which means that a correspondingly detected signal can be assigned to the marker particles by definition, as no other object material can cause this. Thus, by combining the markers, various codes can be generated that enable the simple, fast and, above all, unambiguous identification and sorting of correspondingly marked objects.
In the TBS system, all marked objects are detected in a single step and then mechanically deposited in the correspondingly defined fractions. If, on the other hand, one looks at conventional sorting processes, for example in LVP sorting, a large number of sorting stages are lined up, in each of which only one plastic fraction is pneumatically separated from the residual flow. The TBS approach thus not only increases the efficiency of the conventional cascade sorting system, but also opens up the possibility of being able to add or modify further target fractions flexibly and at short notice.
Short Vita of Jochen Moesslein (Co-founder & CEO, Polysecure GmbH)
Jochen Moesslein is a physicist and MBA by training. His initial career was in the solar sector, as a researcher (Stanford University) and then developer of a new solar business for a midsize German industrial company. Thereafter Jochen has been involved in a number of start-ups and growth companies, one of which, a biotech company, went public with an IPO. Another start-up, an innovative dental implant company, he developed and sold to a S&P 500 corporation. With Polysecure, Jochen went back to his roots as a physicist. He lives his dream of contributing to a more sustainable world through developing innovative and good technology. Jochen combines technological understanding with commercial acumen. He is a team motivator and thrives in an entrepreneurial role. With courage and vision on the political and legislative level, ethical entrepreneurs can accelerate the transformation towards a more sustainable world.