Reinforce3D is a Spanish industrial tech company that has developed a disruptive solution, the CFIP (Continuous Fiber Injection Process). This patented technology reinforces 3D-printed parts after they’re manufactured—something no other method does—by injecting continuous fibers like carbon, aramid or glass into internal channels.
The result: parts that are lighter, stronger, and more structurally advanced. The company’s mission is to overcome the mechanical limitations of additive manufacturing and unlock new performance standards across industries.
Interview with Blanca Garro, CEO & Ingrid Algarra, Marketing and Communication Specialist at Reinforce3D.
What are the main areas of activity of the company?
Blanca Garro & Ingrid Algarra: Our core activities include developing and commercializing CFIP machinery and fibers; integrating this process into existing industrial workflows; and collaborating with partners in aerospace, mobility, and advanced manufacturing to co-develop applications. We also support our clients with reinforcement trajectory design, feasibility analysis and prototyping, among other options.
What’s the news about new products/services?
B.G & I.A: At Reinforce3D, we launched our Delta machine at Formnext 2023 and have since improved it by working closely with our customers for specific applications. Now, we’re developing the modular Delta, a fully automated version designed for 24/7 industrial production.
In this new system, the injector will be mounted on a robot arm or collaborative robot, enabling fully automated reinforcement without operator support. We’re also upgrading other modules for continuous resin mixing and higher fiber capacity to support large-scale manufacturing of final parts.
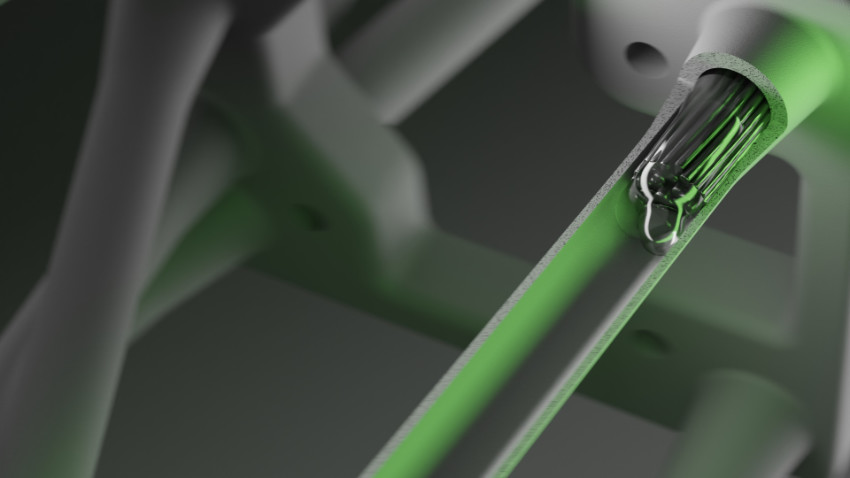
What are the ranges of products/services?
B.G & I.A: Reinforce3D offers a complete solution built around our CFIP technology, which includes the Delta reinforcement machine, specially developed fibers and other supplies tailored for the process, and soon, software tools such as our design checker to support fiber path planning and structural optimization.
We also provide application engineering and technical support to help partners implement CFIP in their processes. For companies still exploring the technology, we offer reinforcement as a service, enabling them to test the advantages of CFIP before committing to full-scale adoption.
What is the state of the market where you are currently active?
B.G & I.A: The market for high-performance components is evolving rapidly across several key sectors, with a clear trend toward lightweighting, sustainability, and structural optimization. Industries like aerospace, automotive, and high-performance sporting goods are under constant pressure to deliver parts that are not only lighter and more efficient, but also strong and reliable under demanding conditions. Additive manufacturing has made great strides in enabling complex designs and customized production, yet many companies still face limitations when it comes to mechanical performance. This gap creates significant opportunity for solutions like CFIP, which unlocks the full potential of AM by addressing the structural weaknesses that have so far prevented broader industrial adoption. We see a market that is hungry for innovation and ready for technologies that bridge the gap between design ambition and manufacturability.
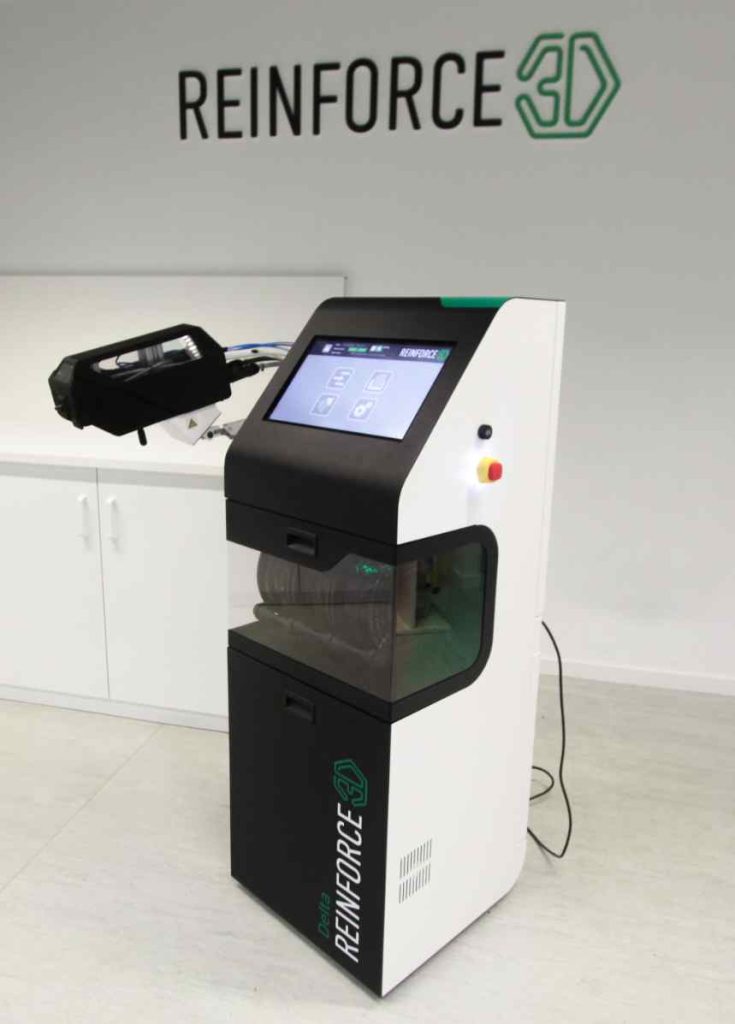
What can you tell us about market trends?
B.G & I.A: There’s a strong shift toward functional, load-bearing 3D-printed parts, especially in aerospace, defense, and automotive. Sustainability is another driver: reducing weight leads to lower emissions and energy use, which is key across industries. We also see a rise in hybrid manufacturing, where technologies like CFIP extend the capabilities of existing AM setups by enhancing performance post-printing. This is a major mindset change—from seeing AM as a design tool to seeing it as an industrial solution.
What are the most innovative products/services marketed?
B.G & I.A: Our CFIP technology is the first of its kind to reinforce a 3D-printed part after it’s been built. This breakthrough makes it possible to place fibers along complex 3D paths, through layers, and across assembled parts. It can be applied to parts made with any printing technology and material—polymers like PEEK or TPU, metals like aluminum or titanium, and even ceramics. This level of post-manufacturing flexibility and structural optimization simply didn’t exist before.
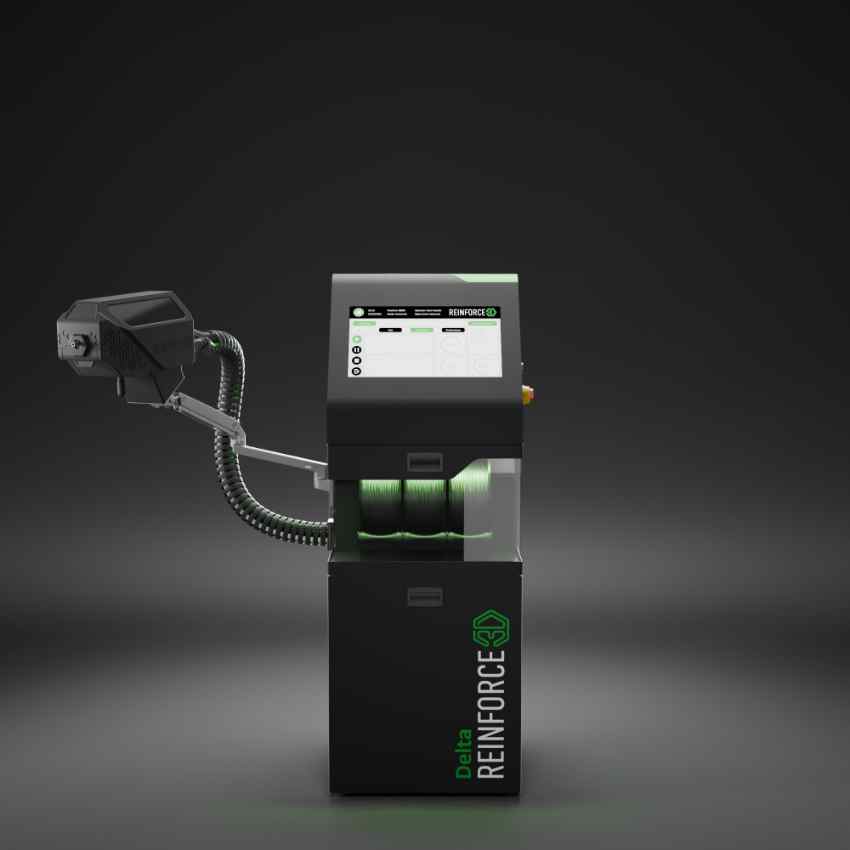
What estimations do you have for the second half of 2025?
B.G & I.A: In the second half of 2025, we expect to continue expanding the company to a new level, bringing in strategic partners and collaborators that will help us accelerate both our reach and capabilities. Our focus will remain on selling CFIP machines and supplying advanced reinforcement solutions to an industry that is increasingly required to adapt to fast-changing performance, sustainability, and efficiency demands. We believe the need for stronger, lighter and more adaptive components will continue to grow, and our technology is positioned to meet that challenge with precision and scalability.