Easy Engineerig: How popular is pelletizing in the iron ore industry?
HAVER & BOECKER NIAGARA: The constant demand of iron ore leads to the need to mine even low-grade deposits. The diminished quality of natural resources is countered by economic, ecological and technological restrictions that require the processing of the extracted iron ore. An enrichment of iron ore can be achieved by separating unwanted components. This enrichment of iron ore represents a significant process step in steel production. During the concentration, most of the gangue is separated. This reduces transport costs and increases the production rate of the blast furnace and direct reduction plant. Since the iron ore concentrate, which has been comminated to the flotation fineness, is neither transportable nor usable, it must be agglomerated. The growth agglomeration of iron ore concentrate in the pelletizing disc is therefore an indispensable part of iron ore processing.
E.E: Is this method becoming more and more known/popular? And why?
HAVER & BOECKER NIAGARA: The worldwide pig iron production developed in the years 2007 to 2015 with an annual increase of about 3.5%. Iron ore production in 2019 is estimated at 2.850 billion tons, and according to conservative forecasts, global iron ore production is expected to reach 3.119 billion tons by 2028, an annual increase of only 0.9%. In contrast, global pelletizing capacities are expected to increase by 5.5 % per annum until 2025. These figures impressively illustrate that growth agglomeration in the pelletizing disc is not only becoming better known, but also more popular.
In the years from 2005 to 2015, a stable worldwide production of only 56 million tons of sponge iron (DRI) could be observed. In spite of various developments and modern technologies of direct reduction processes, a clear industry focus on the conventional blast furnace converter route was still evident. However, the latest efforts to reduce global CO2 emissions show a trend reversal. From 2017 to 2018 alone, global DRI production increased by 11.6%, and by a further 7% in the following year. Modern direct reduction plants use designed iron ore pellets, with very specific pellet size distributions and basicities. These can only be produced in an economically viable way with modern pelletizing discs.
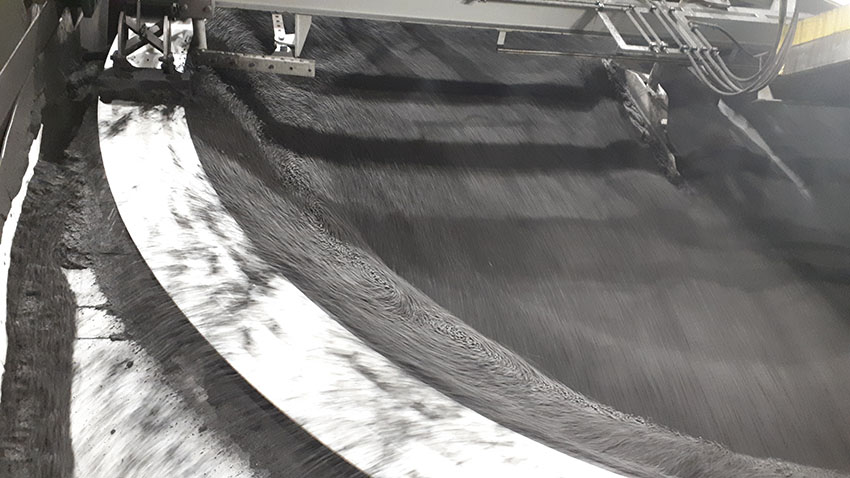
E.E: What equipment is needed to prepare the material for the pelletizing process?
HAVER & BOECKER NIAGARA: To enrich the iron ore, it is necessary to comminute the ore to the flotation fineness and to feed it to sorting processes such as magnetic separation and flotation. The resulting iron ore concentrate is then used with binders, e.g. bentonite or organic binders such as carboxymethyl cellulose and polyacrylamide in the disc.
By adding water in the pelletizing disc, the bentonite swells. The bentonite disintegrates into small platelets, which combine with the iron ore concentrate particles as well as with each other. During the drying process of the pellets, material bridges are formed between the basic substance particles, which significantly increase the dry strength of the agglomerates. During the subsequent firing or hardening of the pellets, the sodium and calcium components act as flow agents, reducing the melting temperature of the basic substance and thus creating local melting bridges at temperatures below the actual melting temperature of the basic substance. As the bentonite binds a part of the pelletizing liquid during the agglomeration process, it is a robust binder with a wide range of application limits. The input of the mineral components is problematic, however, whereby the energy requirement for reduction and melting of these is increased in particular by the increased SiO2 content of the iron ore concentrate pellets. Therefore, especially in the field of DR pellets, there are more and more intensive efforts to replace this binder by organic binders.
E.E: How is pelletizing technology developing in general?
HAVER & BOECKER NIAGARA: For the resource-saving production of pig iron and sponge iron, suitable pellets are also necessary. In addition to metallurgical target values, these are characterized in particular by a narrow particle size distribution and a high degree of roundness. In practice, it has been found that the operating conditions of the pelletizing disc have a strong influence on the pellet quality. Therefore, pelletizing discs are necessary, with which our customers can react to changing material properties as well as to changed target values of the product.
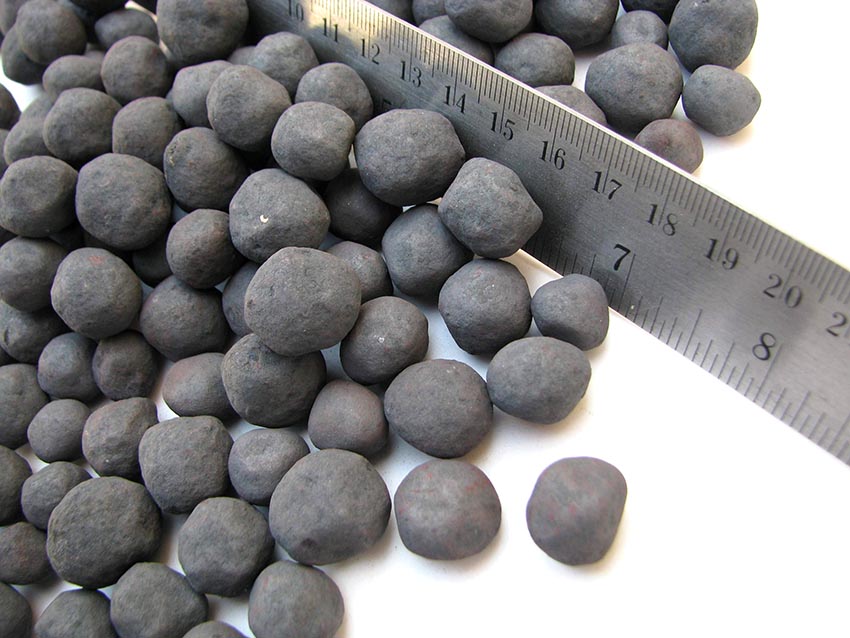
E.E: Are there regional differences?
HAVER & BOECKER NIAGARA: We are seeing global interest in the multi-dimensional automation of our pelletizing discs. The Eastern European market appears to be particularly interested in the HAVER SCARABAEUS technology.
Which companies are already equipped with pelletizing discs and why did the customer decide to use the HAVER SCARABAEUS?
Metinvest Central GOK and Ferrexpo are already equipped with the HAVER SCARABAEUS. Both pelletizing plants have found that modern technology is necessary for the production of narrow particle size distributions for direct reduction processes, which gives the plant operators a wide range of options to stabilise the pelletizing process and achieve optimum output. The modern SCARABAEUS technology, consisting of the HAVER SCARABAEUS, a particle size analysis of the pellets with the HAVER Momentum and the HAVER Processes Management System offers the possibility to preserve the experience of the plant operators for the future and to optimize it with modern technology. Only in this way can ideal DR pellets be produced.
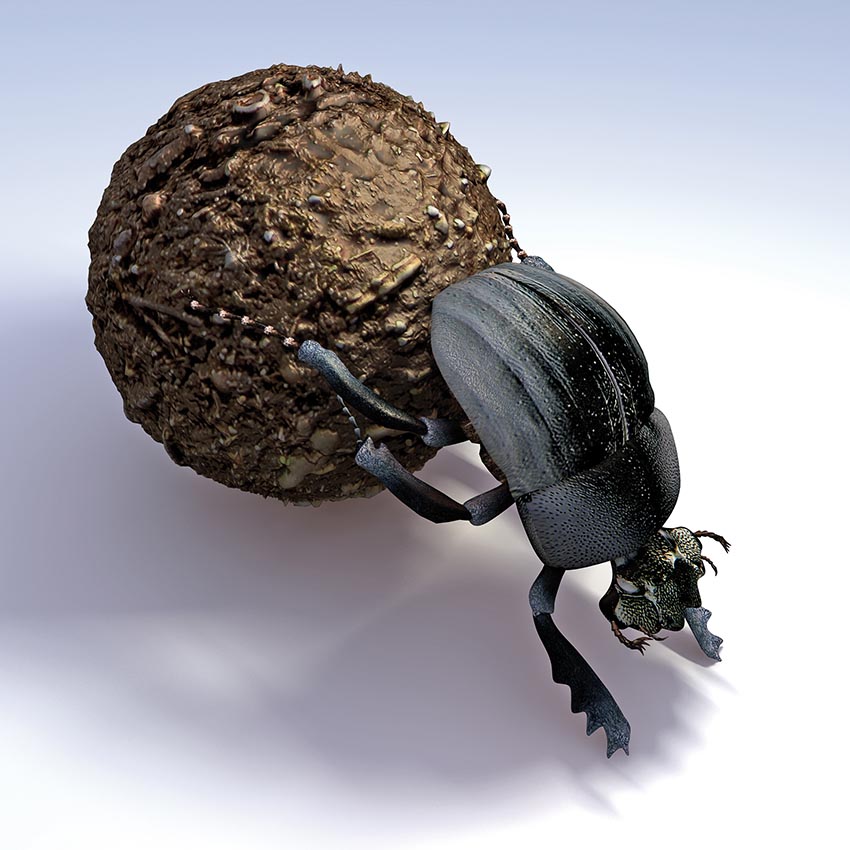
E.E: What kind of service / support does HAVER NIAGARA offer the customer in the decision making / elaboration process?
HAVER & BOECKER NIAGARA: HAVER & BOECKER NIAGARA supports you to develop and optimize your processes, machines and plants. In our test facility are various tests equipment for pelletizing available. The objective of HAVER Process Engineering is to meet your technical requirements and economic benefits. To achieve this, it is necessary to concentrate on the whole pelletizing process, starting with raw materials preparation, dosing and mixing and binder treatment. The core-components of pelletizing are focused in detail to minimize the efforts of final product classification, material circulation as well as de-dusting, safety and environmental protection. Applying recognized technical norms and standards with tailor-made processing leads to a production process that saves energy and resources.