Thrace Group is a Greek multinational Group, founded in 1977 in Xanthi, Greece. Through a successful strategic development course has developed into one of the largest producers of Technical Fabrics & Packaging Solutions worldwide. The Group is active in the design, production and distribution of polypropylene products, with production and marketing operations in 9 countries and a sales network extended to more than 80 countries.
Since 2013, the Group has expanded its business activities in the hydroponic cultivation of Mediterranean vegetables in greenhouse facilities being the only ones in the world heated exclusively by geothermal energy.
Easy Engineering: What are the main areas of activity of the company?
THRACE: The activity of the Group is divided into 3 business units that cover more than 25 market segments. Particularly the Technical Fabrics business unit concerns the design, production and trading of synthetic fabrics for industrial and technical use and has an international focus with 97% of sales taking place in the global market. Construction is one of the main market segments THRACE is active in, by providing engineered solutions that enable professionals to conduct their business in a faster, safer, cost-effective, resilient and sustainable manner. THRACE Geosynthetics, building membranes and many other THRACE construction products contribute to efficient solutions in site challenges concerning civil, geotechnical, hydraulic and environmental engineering. Agriculture, landscaping, gardening, medical and hygiene are some of the market segments THRACE products may also find application.
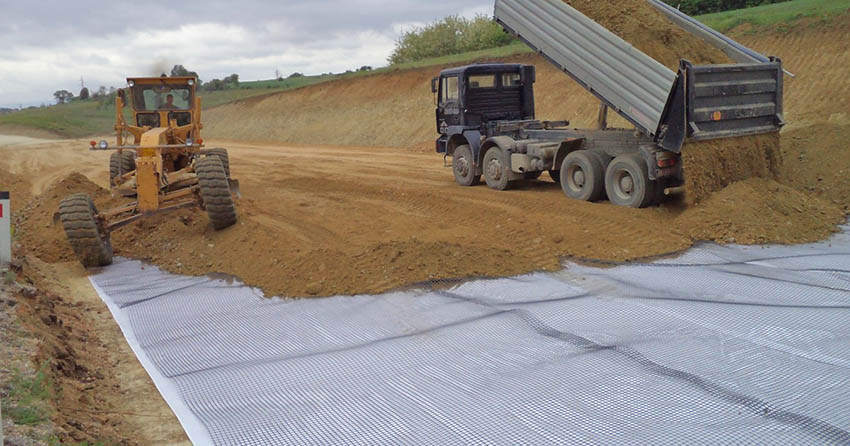
E.E: What’s the news about new products and the ranges of products?
THRACE: Being a result of the continuous innovation the Group experiences the last many years, THRACE has developed 28 different production technologies that allow for the creation of a rich and wide-range product portfolio. In terms of Technical Fabrics, among the capabilities of the Group fall the manufacturing of needle-punched, spunbond and meltblown nonwovens, of woven textiles with slit-films and filaments and the production of geogrids/geonets and composites. Capabilities are further extended to serving environmental engineering applications with Erosion mats, Geosynthetic Clay Barriers and Reactive Filters.
E.E: At what stage is the market where you are currently active and what are the market trends?
THRACE: Being a manufacturer of polypropylene products makes THRACE Group active in markets that are currently dealing with concepts like “circular economy”, “recycling” and “sustainability”, all of them being closely associated with the EU’s primary objective for CO2 emission neutrality by 2050. Accordingly, the manufacture of sustainable & energy efficient products is a trend that cannot be disregarded. Similarly, the development of state-of-the-art technologies for recycling, reusing and recovery of installed products is of high importance. In that context, THRACE Group already designs and manufactures products that ease recycling. It is important to notice that THRACE Group has joined EU’s Circular Plastics Alliance and it has voluntarily pledged to the EU that, by 2025, 8.500 tonnes of virgin raw material will be replaced with recycled ones.
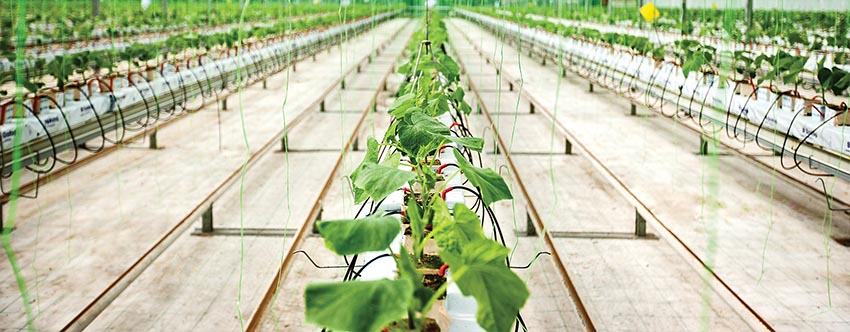
E.E: What are the most innovative products marketed?
THRACE: Among the innovative products manufactured within the Group, Geosynthetics are those considered that make the most significant contributions toward UN Sustainable Development Goals. They are used in a plethora of geotechnical, transportation and other civil engineering applications. Typical applications are their use as filters in subsurface drainage systems, as reinforcing elements in retaining walls, roadbeds and shallow foundations and as drainage media or protection layers in landfill construction. In most cases, they replace conventional construction materials (such as sand, gravel, clay, cement, lime etc.) to provide elegant and safe structures, with competitive construction cost, by following rapid installation procedures that comply with demanding project timeplans. Geosynthetics are proven to impact significantly less the environment in terms of equivalent CO2 emissions when compared to other conventional solutions. Recent studies, with regards to the environmental performance of Geosynthetics, have concluded that Geosynthetics lead to 75% lower environmental impact compared to the environmental performance of competing construction materials.
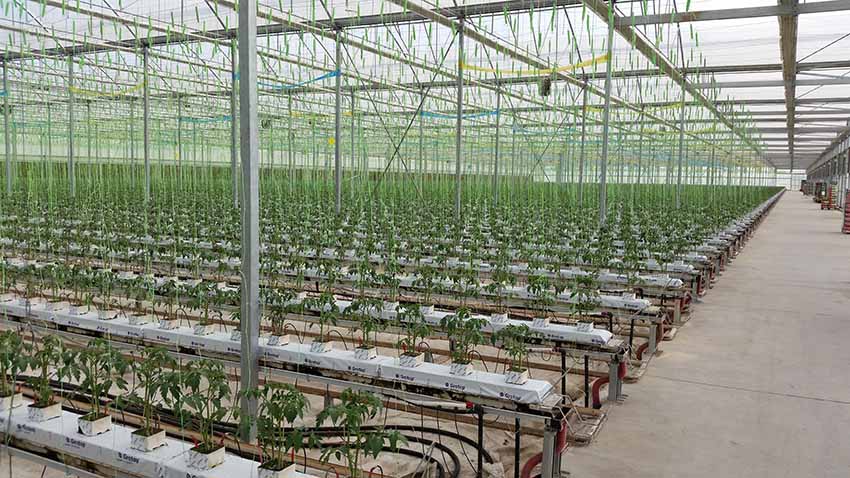
E.E: What estimations do you have for 2022?
THRACE: Certainly, COVID-19 pandemic has disrupted the activities in the construction sector, worldwide. However, the governments have globally adopted investment packages to support the construction industry in the view of both boosting the declining economies and stemming the climate crisis. In that light, the demand for Geosynthetics and other Technical Fabrics is expected to grow further so as to support the infrastructural developments. Moreover, Technical Fabrics relating to medical and hygiene markets are also expected to remain in the spotlight as long as the pandemic is still at its peak.