Top 3D Shop is a CA-based digital manufacturing value-added reseller and turnkey solutions provider. Top 3D Shop supplies professional additive manufacturing equipment, subtractive manufacturing equipment, 3D scanning systems, robotic equipment, parts and supplies. From 2013, the team behind Top 3D Shop has fulfilled projects for thousands of customers, from small businesses to industry players, brands, and companies, including NASA, U.S. Army, U.S. Navy, Qualcomm, Nissan, Toyota, ELMS, University of Michigan, Troy University, University of Illinois, Texas A&M University, Missouri State University, The University of California and St. Louis County Police Department.
Interview with Egor Driagin, CMO & Co-Founder at Top 3D Shop.
Easy Engineering: What are the main areas of activity of the company?
Egor Driagin:
- Technological audit of the enterprise and evaluation of the effectiveness and potential impact of the introduction of such technologies as additive manufacturing, subtractive manufacturing, 3D scanning, robotic automation.
- Feasibility study of additive manufacturing technology implementation
- Manufacturing process optimization to improve and standardize product quality, improve unit economics, reduce reject rate, increase the speed of launching new products, improve safety and scale up production.
- Selection of the most appropriate technology, equipment and consumables, their supply, assembly, installation and calibration.
- Training of personnel in order to improve and maintain competencies required to implement new production workflows.
- Servicing and maintenance of the supplied equipment.
E.E: What’s the news about new products?
E.D: There are many brands that launched important innovations at Formnext in 2023. In this article, we would like to highlight two brands worthy of attention.
In large-format 3D printing, Raise3D introduced a new Hyper FFF technology for its Pro 3 series 3D printers, achieving a speed 3.8 times faster than the average professional printer available in the market.
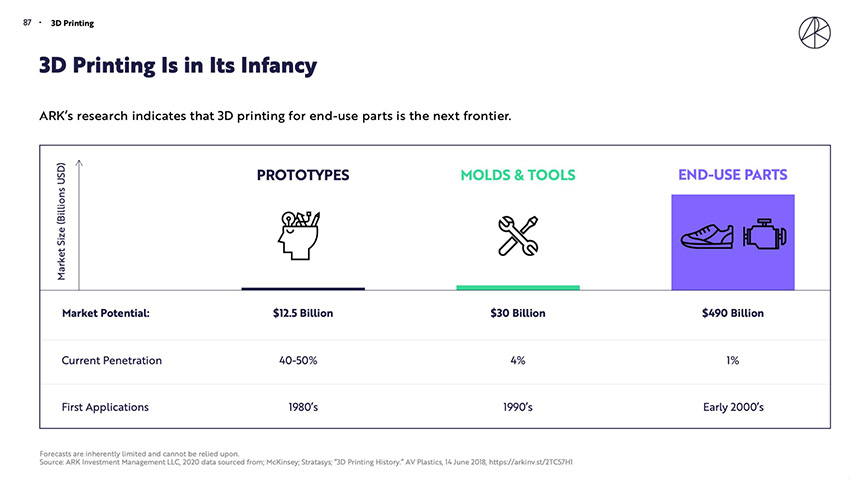
The challenge was never to just instruct an FFF printer to print at a higher speed. Telling an FFF 3D printer to print at high speed is quite simple, and most manufacturers and users have tried it at some point. The challenge was to be able to do so while keeping the same quality of layer adhesion and surface finish, in addition to the structural stability of the whole printer. Raise3D can proudly announce that its R&D team has achieved this goal, initially for its Pro3 series dual extrusion 3D printer, for which the whole Raise3D’s ecosystem – hardware, software, and filament – had to be adapted.
As for 3D scanning, one of the latest products is the Freescan UE Pro. It’s the first laser 3D scanner which has built-in photogrammetry (which allows scanning objects up to 10 m in size) that caters not only to large enterprises, but also small-to-medium business.
The price of the Freescan UE Pro is 2-3 times lower than the market alternatives, but based on the current tests, the quality of the scans and the scanning experience itself is on par with the leading competitors.
E.E: What are the ranges of products?
E.D: Top 3D shop offers a wide range of 3D Printers, 3D Scanners, CNC Laser Cutters and Engravers, Robotic Equipment, and also such supplements as filament and resins. Among brands presented at Top3DShop’s website you can find Modix, Shining 3D, Raise 3D, Phrozen and many others. The full list of products is presented at the website.
E.E: At what stage is the market where you are currently active?
E.D: The additive manufacturing market was evaluated at $12 billion USD in 2020 (ARK, 2020). Market analysts estimate that by 2025 that the market may grow to $20 billion USD on the lowest range (a 2017 estimate by Lux Research) to $120 billion USD on the highest range (a 2020 estimate by ARK Invest, a 2013 estimate by McKinsey).
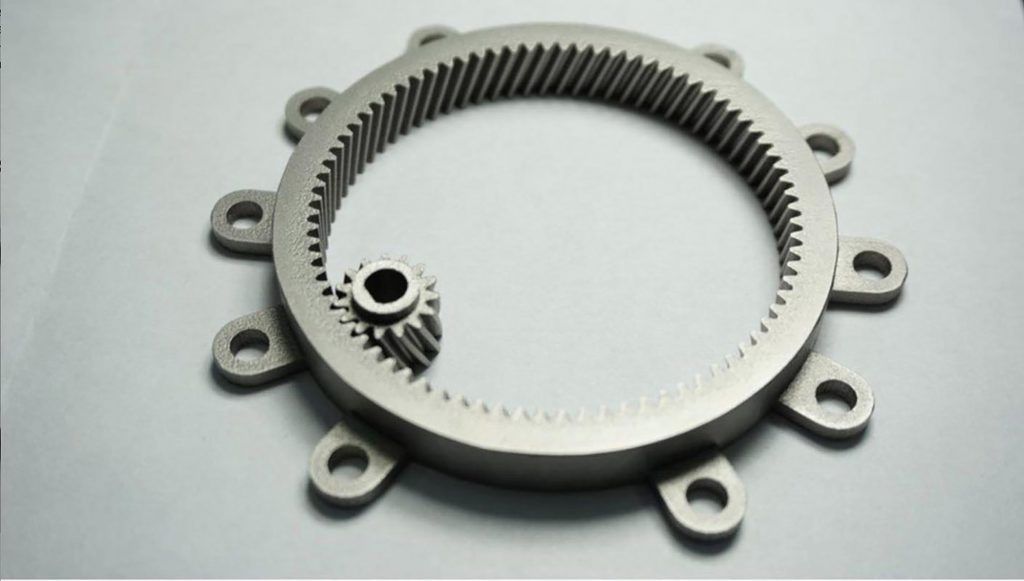
E.E: What can you tell us about market trends?
E.D: Research by ARK Invest suggests the aforementioned growth will be driven by the shift in the use of 3D printing, where 3D printing serves the role of a prototyping tool (current penetration: 40-50%) to the use of printed parts for Molds and Tools (4% Penetration) and the End-Use Parts (1% Penetration).
For example, the use of 3D printing for the end-use parts is driven by developments in such technologies as SLM 3D Printing. Everything from the hardware to the software to the diversity of metal powders and post-processing equipment has been advancing, allowing more companies to adopt this tech as part of their production workflows.
For example, Bugatti has leveraged SLM 3D printing to produce a range of functional parts for its sports cars, including a brake caliper that is recognized as the largest functional component 3D printed from titanium. Frank Götzke, Head of New Technologies at Bugatti, commented on the brake caliper being capable of coping with “extreme strength, stiffness and temperature requirements at speeds of over 375 km/h with a braking force of 1.35g and brake disc temperatures up to 1,100 °C”.