VI-grade is a leading provider of real-time simulation and professional driving simulator solutions that accelerate product development across the transportation industry. The company’s driving simulators range from static deskside solutions to full-scale driver-in-the-loop dynamic simulators, allowing OEMs, suppliers, research centers, motorsport teams and universities to reduce physical prototypes and accelerate innovation.
With a worldwide network of trusted partners, VI-grade delivers turnkey simulator solutions including proprietary software, hardware, services, and an open framework for customization. With over 30 years’ experience in simulation, VI-grade is headquartered in Darmstadt, Germany with technology centers in Italy, UK, Japan, China, and the USA.
Interview with Gabriele Ferrarotti, Marketing Director at VI-grade.
Easy Engineering: What are the main areas of activity of the company?
Gabriele Ferrarotti: VI-grade provides solutions that increase innovation in the product development process, changing the paradigm where you dream of a new product concept, but then you must build a hardware prototype to experience it. Instead, thanks to VI-grade’s solutions, customers can go directly from a concept to trying out that conceived product virtually, before anything is physically built.
This process is quicker, simpler, and safer. And customers not only realize the expected financial return-on-investment but have access to a collaboration platform that unites their teams and enables design breakthroughs.
VI-grade started by delivering real-time simulation software and then focused on an immersive Driving Simulators line-up that allows to feel the performance of the conceived product. Finally, Hardware-in-the-Loop solutions were added, enabling to test and optimize physical vehicle components with virtual vehicle models and human drivers.
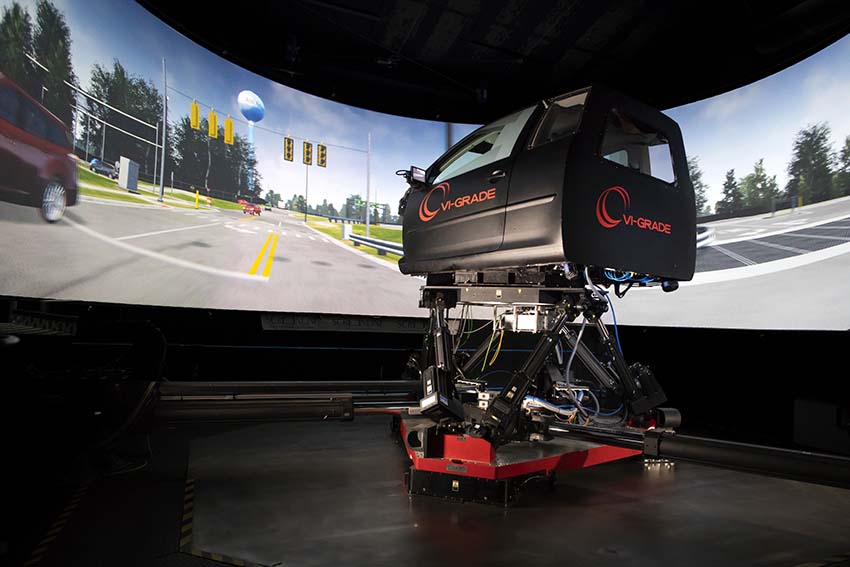
E.E: What’s the news about new products?
G.F: The most recent solution launched by VI-grade in collaboration with its sister company Concurrent Real-Time is called AutoHawk and is defined as the new HiL solution for automotive applications. AutoHawk consists of real-time hardware, real-time OS, real-time software and I/O cards and is highly configurable, since both VI-grade real-time software and/or software from 3rd party can be installed on it. In the same configuration, AutoHawk can work as a stand-alone Linux based high-power computer, as a HiL system or in combination with a driving simulator or on a real vehicle. AutoHawk is a flexible HiL platform that can be used across the entire product development cycle, from concept to sign-off.
E.E: What are the ranges of products?
G.F: The company develops a wide range of software products dedicated to offline simulations; these products are then also used to finetune real-time vehicle models and other components needed for the driver-in-the-loop applications on the driving simulator.
The driving simulator product line is highly configurable and scalable and ranges from static deskside solutions up to full-scale dynamic simulators, allows OEMs, suppliers, research centers, racing teams and universities to reduce physical prototypes and accelerate innovation, in all main automotive engineering disciplines: ride & handling, ADAS and autonomous vehicles, NVH, HMI and motorsports.
E.E: At what stage is the market where you are currently active?
G.F: Driver-in-the-loop market has been getting more and more mature in the last 10 to 15 years, this also strongly depends on the particular application.
Ride&handling optimization is nowadays strongly approached with the help of simulation and driving simulators.
NVH and acoustics prediction and optimization is also addressed with the help of specific driving simulators.
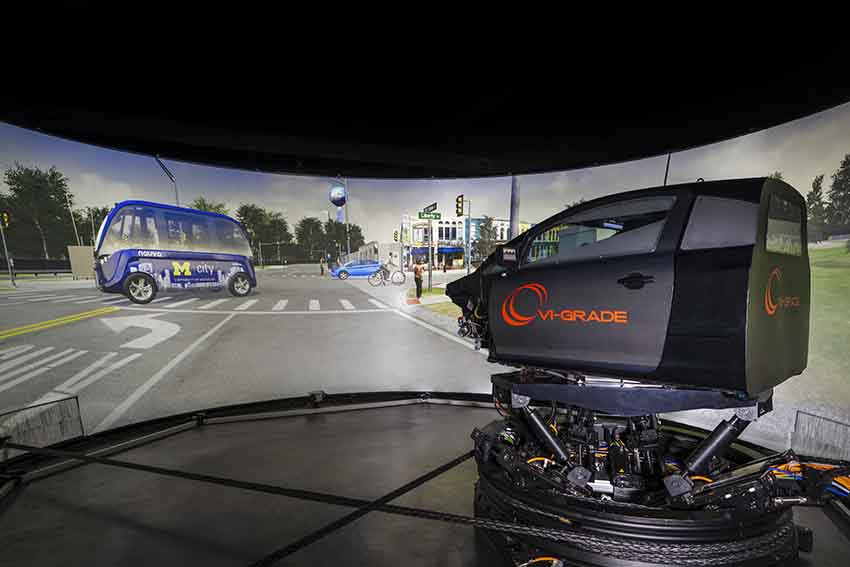
Autonomous vehicles and ADAS systems must be tested with the help of driving simulator solutions, to be able to run the billions of miles of tests required to certify and authorize the circulation of such vehicles, and to enable such testing in full safety.
Motorsports teams, who due to recent regulations can access racetracks only for a very limited period of time, use driving simulators to train their drivers on endless vehicle configurations and virtually every environmental condition (i.e. weather). Lap-times can be predicted with an extremely high level of precision.
HMI testing is today still not so mature and is typically addressed later in the development cycle, but also this is due to change due to the growing acceptance of simulation also in this field.