Originally a division for industrial supplies within the parent company Adolf Würth GmbH & Co. KG, Würth Industrie Service GmbH & Co. KG was established as an independent subsidiary at Würth Industrial Park in Bad Mergentheim on 13th January 1999. With currently 1,700 employees, Würth Industrie Service focuses on supplying C-Parts to industrial customers in the manufacturing industry and provides holistic services to a total of 20,000 customers.
Easy Engineering: What are the main areas of activity of the company?
Würth Industrie: With our service brand “CPS® C-Parts Solutions”, Würth Industrie Service offers customers in the manufacturing industry made-to-measure logistics supply and service concepts such as scanner-supported storage rack systems, automated electronic ordering systems or just-in-time supplies in Kanban bin systems. The goals are geared clearly towards lowering purchasing costs, optimizing processes, reducing costs and maximizing time savings while at the same time maximizing supply security and minimizing capital commitment.
E.E: What’s the news for 2020 about new products? / 7. What are the most innovative products marketed?
Würth Industrie: Digitisation is finding its way into the world of industry. As a result, products are becoming available faster, process efficiency is improving, communication is becoming more intensive and data transparency is increasing – irrespective of time or place. Digital solutions are now also gaining importance in C-Parts management. This is why Würth Industrie Service has been working on intelligent, forward-looking solutions and making C-Parts management more reliable. The new iPLACER® is the latest development in our RFID portfolio and ensures maximum flexibility. The small, handy, battery-operated module with integrated reader and transmitter unit can be mounted anywhere and provides an automated reordering of C-Parts at the workplace or at the flow rack for more transparency in the material flow. The RFID technology is thus not only used as an ordering system, but now also functions as a stock management system. In addition to our system solutions for production material, Würth offers a holistic, modular concept for auxiliary and operating materials. The current study of the ORSY®mat CBL cable vending machine is about an automated supply concept for the specific product group of cables, wires, strands and installation material. Like all ORSY®mat models, the ORSY®mat CBL handles the entire procurement and logistics process. Another innovation is our virtual showroom „WIS Virtual Experiences”. Due to virtual rooms are highly relevant in this digital age, we have created innovative possibilities for interactively networking with our customers and colleagues. Now we are able to present the system solutions and our product range for an efficient C-Parts management. In general Würth is at the forefront of innovation as a business and we are always looking at new opportunities. For instance, we already have a 3D printer farm, where we can do a variety of samples for our customers. We have experienced engineers who can design the drawings for these printers and this helps us work alongside customers on any of their special needs.
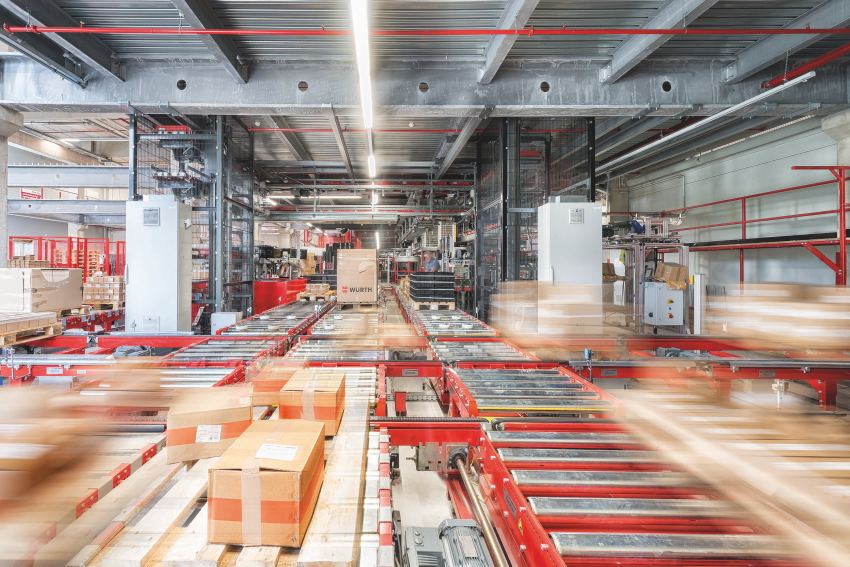
E.E: What are the ranges of traded products?
Würth Industrie: We are the truly holistic partner for our customers − in the area of production material and MRO, in Germany and Europe, but also all over the world! With a wide range of more than 1,100,000 items, we offer the best conditions for this. No matter whether it’s fastening and fixing technology, dowels, special parts or personal protective equipment and chemical products, right through to tools, batteries, bits and machines, we combine product and system competence. Security of supply is our top priority. The “6+R rule” describes the six overriding goals that our brand “C-Parts. With Certainty.” justifies: We provide our customers with the right product, at the right time, in the right place, in the right quantity, at the right price and in the right quality. We promise maximum product and process quality through innovative technologies. Our test laboratory specialised in connection technology is accredited for more than 50 test methods conforming to DIN EN ISO/IEC 17025 and serves as official and independent test station. With an area of 800 square metres, it is equipped with latest test devices, which together with qualified employees and end-to-end quality management offer optimum conditions for reliable test results.
E.E: What can you tell us about market trends?
Würth Industrie: A large and dynamically developing range of articles, a wide variety of article designs, a multitude of storage locations and suppliers as well as unforeseeable fluctuations in demand: This is precisely why robust processes, secure systems and digital technologies are extremely important. The turbulent times have shown us how important crisis-proof C-parts management is and that various aspects and competencies are more important than ever. These include the megatrends of individualisation, i.e. a C-parts supply to the immediate point of need and place of consumption that is precisely tailored to requirements – regardless of whether direct or indirect materials are involved, and the megatrend of connectivity, which necessitates decentralised solutions and global coverage across several locations and countries.
Another area of innovation for the future will be that more products will be handled electronically, with the systems of our customers connected to our systems. We already have Kanban and RFID technology in our customers’ sites and we can see vending machines becoming the next step – especially in the MRO sector. With the current situation regarding Covid-19, handing out parts will become a thing of the past. Instead these types of parts will be stored in vending machines with employees having to enter codes to access their correct products. Another demand in the future will be the need for us to carry out data handling for our customers. The European Union is always developing new rules and laws that impact a wide variety of parts. We will have all of this special data on file and will be able to provide all the answers to customers.
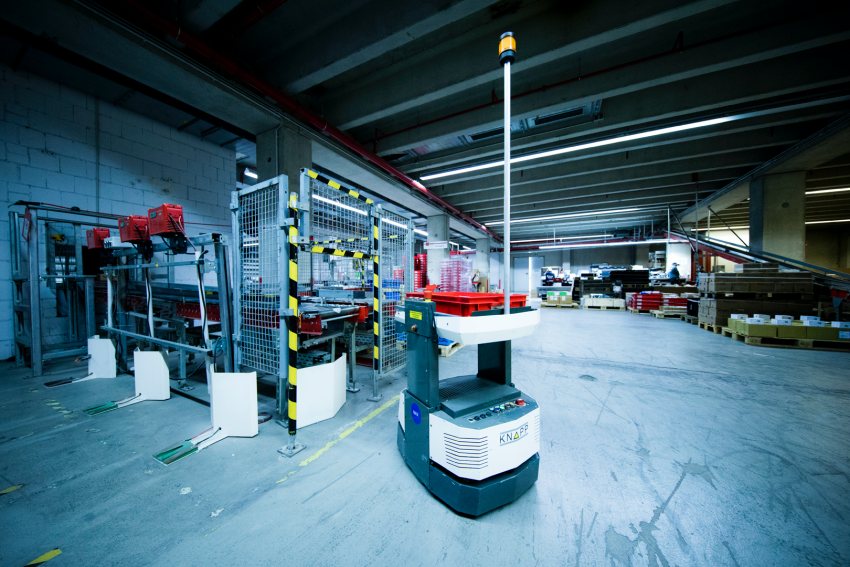
E.E: What estimations do you have for 2020?
Würth Industrie: The global consequences of the pandemic are challenging us all in an unexpected way. As a global retailer, we have immediately felt the worldwide and country-specific restrictions and have faced a number of challenges, such as restrictions due to lockdowns in many countries of our main suppliers, early plant closures and shutdowns at customers and manufacturers, delays due to border controls and customs clearance. The economic consequences resulting from the pandemic cannot yet be finally assessed.
As a company of the Würth Group and part of the Würth Industrial Network, we have a strong, broad and technological industrial network consisting of more than 60 companies in over 40 countries and have a solid financial basis. Due to this decentralized structure and the great internationality, we are independent of individual economic areas and market segments, which gives us greater stability. In addition, we are following a multi-channel strategy in almost all business areas, with the aim of enabling our customers to interact with us via a wide variety of channels – personal, stationary, but also contactless, digital and electronic. It is particularly pleasing that we have noticed in recent weeks that our contactless supply systems such as RFID Kanban or vending machines and automated procurement using e-business solutions are being accepted by customers due to the lockdown, also in terms of the new requirements. The Corona crisis is indeed proving to be an accelerator for digitization. That’s why we are looking to the future with caution, but also quite positively.