Zapp Precision Metals is a market leading manufacturer of precision steel products. With over three hundred years of history and based on German roots, Zapp has built up a network of production locations and service centers on three continents. Operating across 15 sites globally, with approximately 1,350 employees, their semi-finished product portfolio is the feedstock for many demanding applications and products in industrial sectors such as automotive, aerospace, medical, energy generation, oil and gas.
Easy Engineering: What are the main areas of activity of the company?
Zapp: Zapp operates three divisions; Precision Strip, Precision Wire and Materials Engineering, which is a distributor of specialist tooling alloys, powder metallurgical products and other exotic metals in various forms. Our production sites are supported by a global network of service centers to ensure reliable delivery with short leadtimes.
E.E: What’s the news for 2021 about new products?
Zapp: Across all three divisions we continue to invest in our production technology and infrastructure.
In the strip division we are developing our capabilities in the area of thin foils down to 0.025mm in thickness, and have recently commissioned a new „clean room” finishing hall, including a unique foil slitting line.
In addition, we have recently developed two special heat treated products, for use within precision etching and laser cutting applications; Zapp Micro-Etch® and Zapp Super-Etch®. Due to the removal of internal stresses within these strip products, the material etching performance and thermal stability is vastly increased. This enables our customers to achieve improved process yields, hold tighter tolerances and ultimately offers greater design freedom.
Finally, we are also starting to develop a non-magnetic austenitic stainless steel product, in 2021, for use within electromobility applications called Zapp ZeroMAG®.
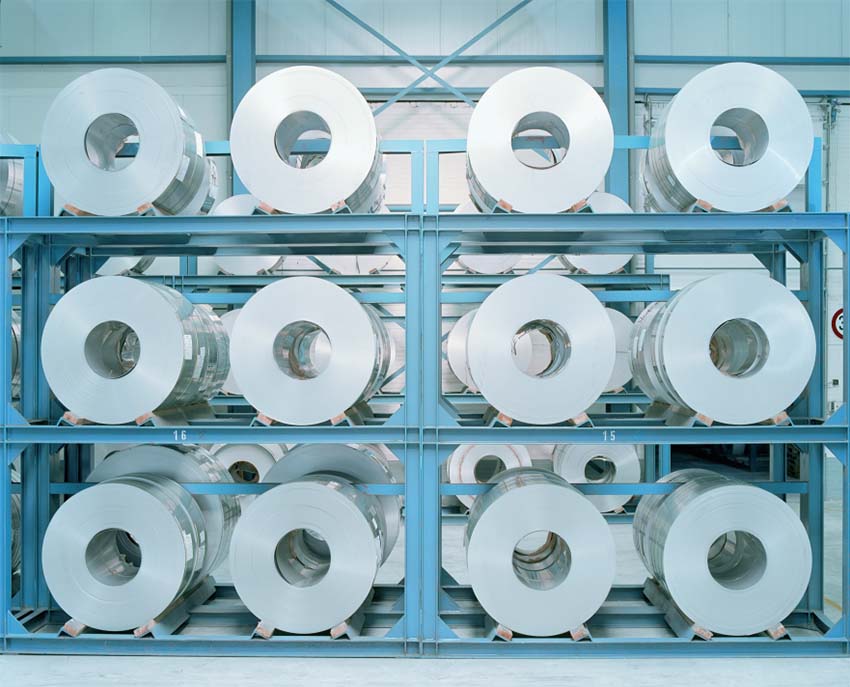
E.E: What are the ranges of products?
Zapp: Precision strip and foil, manufactured from various stainless steels, nickel alloys and titanium. Supplied in a variety of material conditions, from soft annealed to extra hard rolled as well as hardened and tempered martensitic stainless steels. Material thicknesses from 0.025 – 2.0mm and widths from 2 – approx. 1,000mm. Our strip material can be supplied in coil, sheet, spool or multicoil condition. Our cold rolling production facilities are accredited to IATF 16949 and AS 9100.
Our long products portfolio includes precision drawn wire 0.15-20mm in diameter, flat wire and rolled profiles from 0.3mm x 0.3mm in cross section and round bar 0.70 – 25mm diameter. Our long products can be supplied in a variety of stainless steels, nickel, cobalt and titanium alloys. All products can be finished to the tightest tolerances.
Our High Performance Materials facility stocks plate and sheet from 0.10 – 3.4mm in thickness, titanium up to 50mm in thickness and can also offer semi-finished water and laser cut blanks. In addition, we supply seamless and welded tubes made of nickel alloys and titanium, as well as tube accessories and welding consumables.
In medical technology, additive manufacturing processes offer application-specific advantages in terms of osseointegration, flexibility in production and freedom in product design. Our metallic powders for your additive manufacturing of medical implants or instruments are available in various materials and designs. The area of application is powder fed processing technology such as SLS, SLM, DMLS, etc.
Finally, Zapp Tooling Alloys offers engineered solutions to manufacturers that reduce downtime, increase productivity and, therefore, reduce part costs. Our combined team possesses hundreds of years of experience in the distribution of high performance tooling materials. Zapp has developed the premier global supply chain to offer our customers the best value proposition, Zapp’s Z-Series PM tool steels, which are manufactured to strict quality specifications. Our quality, when combined with renewed service levels, make Zapp the first choice for high performance tooling applications.
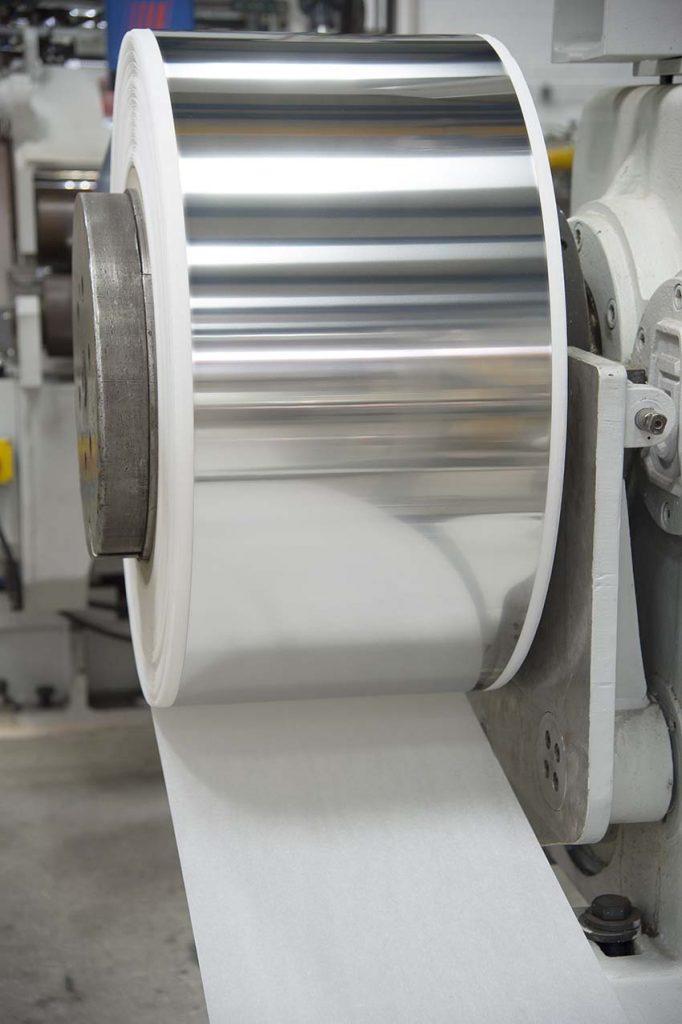
E.E: At what stage is the market where you are currently active?
Zapp: Zapp sources raw material from leading global suppliers, according to our own high quality material specifications. Utilising this network of global suppliers, we select the best raw material for each specific end product that our customers ask us to produce.
We specialise in the manufacture of high precision, cold formed, semi-finished products and normally operate as a tier 2 or 3 supplier in our supply chains. However, we often have direct contact with tier 1 or OEM companies, in order to design and co-develop new products together.
Supporting our customers with the development of their products is an important focus for our team and we have many R&D engineers and metallurgists who work in this area. In addition, we can also offer our customers material testing services via a number of accredited laboratories, including a corrosion testing centre.
E.E: What can you tell us about market trends?
Zapp: Across all of our divisions we see emerging macro-trends that will drive our business strategy for the coming years. These include the rapid transformation to electrical mobility, connectivity, sensor technology, miniaturisation and the ever increasing performance requirements of our customer’s products. All of these market trends place increasing demands on the steel feedstock material and require tailor made solutions from companies like Zapp.
Perhaps most importantly is the fundamental requirement to manufacture our products efficiently, whilst maximising the use of our natural resources and ensuring environmental sustainability in everything that we do.
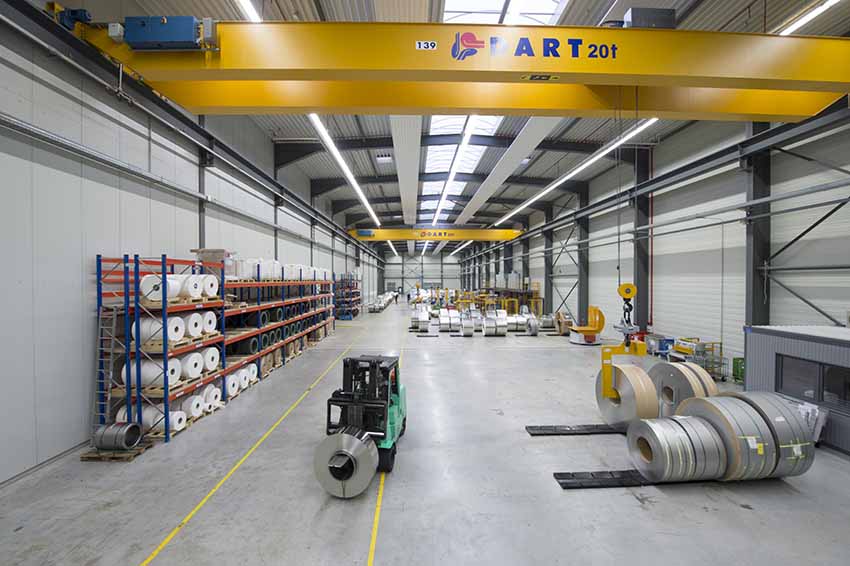
E.E: What are the most innovative products marketed?
Zapp: Over the past few year the Zapp Precision Strip division has developed its capabilities for the manufacture of thin foil products (down to 0.025mm) with extremely tight tolerances and shape requirements. One specific product is Zapp SuperClean Invar 36®*, which is used within the production of OLED displays. The quality demands for this application are extremely high due to the precise nature of the end product, which possesses etched apertures of approximately 30 microns in diameter.
In addition, we also offer precision strip with special functional or visual surfaces for a variety of automotive and consumer goods applications.
Finally, our extensive hardened and tempered martensitic stainless steel portfolio contains performance grades such as Zapp SF® (Super Fatigue) for demanding flapper valve applications, as well as other high-end engineering applications.
The production of such products in made possible by our modern production facilities, located in Germany, where we operate state-of-the-art cold rolling and heat treatment equipment.
E.E: What estimations do you have for 2021?
Zapp: The steel industry experienced an extremely high level of demand in the first quarter of 2021. The general demand for Zapp products has, in turn, increased significantly over the past few months. We expect this trend to continue throughout the remainder of the year. Availability of steel products in Europe will remain restricted in the short term, due to shortages on the raw material side. Despite this general backdrop, were are continuing to grow strongly in new market sectors and geographical regions, via new product development and end customer qualifications. The pace of transformation to new forms of mobility and cleaner energy will continue unabated and will require technical solutions from leading companies like Zapp Precision Metals.