Interview with Marcel Pfeiffer, Head of Design and Brand at Zimmer Group.
The Zimmer Group focused on the topic of digitization at an early stage, what were the reasons for this?
Marcel Pfeiffer: The Zimmer Group had already foreseen the upheaval in automation and mechanical engineering from about a decade ago and recognized the enormous potential of digitalization. Since 2013, each of our mechatronic products has been equipped with an in-house control system, integrated sensor technology and is Industrie 4.0-ready. Since 2018, Zimmer Group has been offering “Digital Services”, and has been expanding their functionalities and the number of supported products ever since.
Digitization affects all industries and technology sectors worldwide. What is the Zimmer Group’s self-image and focus?
M.P: As a partner to the mechanical and plant engineering industry, the Zimmer Group is close to the pulse of the market. To this end, however, we see the topic of “Digital Services” not only as an additional service for the customer, but also quite consciously as the digital and technological further development of our products and the company in order to meet the increasing demands of the global market. We are implementing the digital transformation strategy at all levels, in all functions and at all locations. Our goal is to significantly increase the digital share of our offerings. The Zimmer Group sees itself as a nucleus for digital innovation and new, digital business models. We are shaping and driving the transformation and are a partner for all topics relating to digitization in the market.
What success factors do you see in the topic of digitization?
M.P: Approaches to solutions for mechanical and plant engineering must be viewed in a differentiated manner. First of all, the motivation and objective of a digitization project must be clarified. The validation of the initial situation is the second basis, because companies are often already much further along in this topic than they themselves assess. Companies with a very consistent production structure equipped with standard machines will certainly have a different target focus than, for example, an operator of special machines, a food processing company or an automotive OEM. The topic of acceptance and training also play a major role – in our experience – in driving the topic of digitization forward. As soon as companies have recognized the possibilities and opportunities offered by digitization, the topic takes on a momentum of its own. Success factors are certainly the process structure, as well as the technical and IT infrastructure. Last but not least, a company’s strategic growth planning is also an important influencing factor in the approach and gradual scaling of digital solutions.
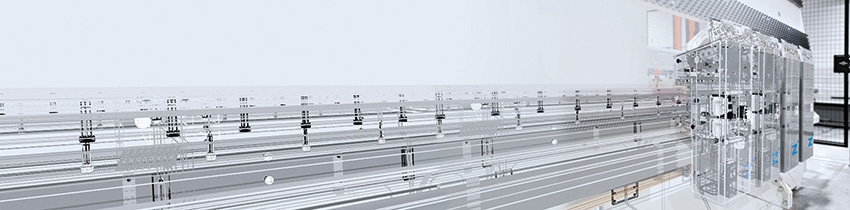
Why does the Zimmer Group offer software functionalities as a classic component manufacturer? Does that really make sense?
M.P: This question is justified, and yes the approach of offering “digital services” as a manufacturer of components, systems and plants is not only sensible, but also absolutely logical. If only for the fact that automation is about the production, assembly and movement of physical goods. This means that every data record has a relationship to a workpiece, a tool, a plant area or a storage location. Another perspective would be against the background of analytics/ statistics and a cumulation/averaging of events and the interpretation of this data. Experience shows that “Digital Services” significantly help to reduce error rates, increase availability, productivity and quality and thus to use the full capabilities of available hardware – no matter at which level. But who knows the features and capabilities of a component better than the manufacturer who developed it, supports tens of thousands of units worldwide over a long period of use in a wide range of industries, and ensures service and availability? “Digital services are not only an excellent instrument for upgrading existing infrastructure, but also for meeting the future challenges of the global market with confidence and strengthening and expanding one’s own position with new business models.
In which areas do you see the greatest benefits of digitization?
M.P: In my view, the greatest benefits of digitization are not only the familiar factors such as quality, time, productivity, efficiency and value creation, but also the ability to make more complex processes manageable and transparency in control and tracking. What I mean to say is that digitization moves companies forward at both the operational and strategic levels.
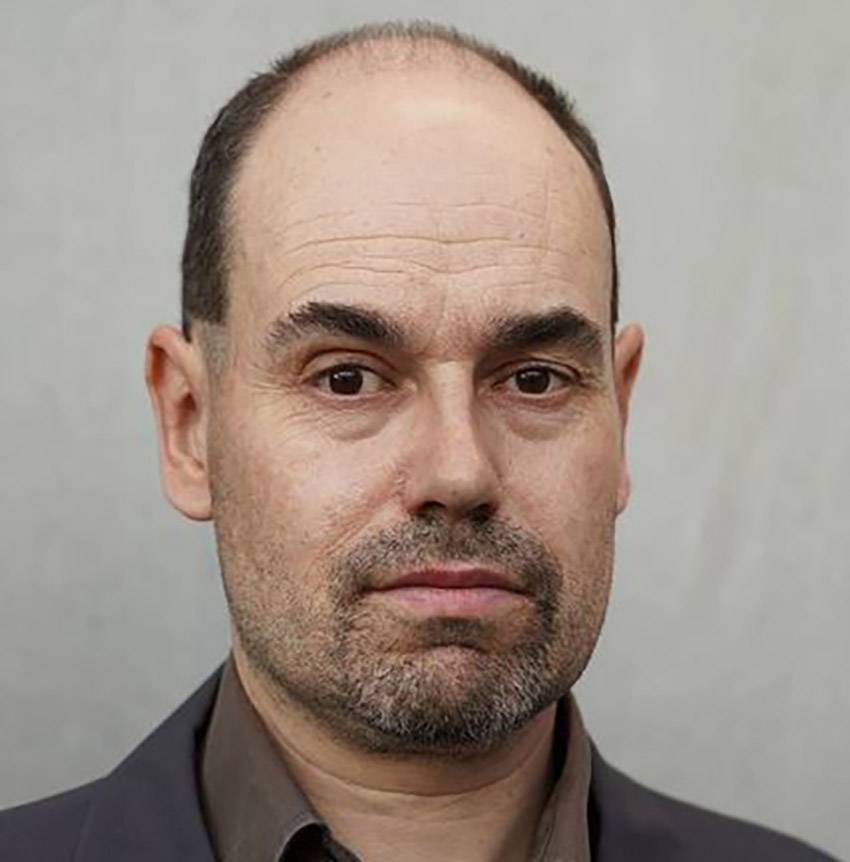
How is the Zimmer Group positioning itself in the age of digitalization?
M.P: As with any business, the question of added value is paramount in the age of digitization. The great advantage of the Zimmer Group, as a global supplier of components, systems and machining cells, is its extensive know-how for industrial production processes and for the needs of production companies. Because even in digitalization, hardware and a deep understanding of its behavior is the basis for new data-based solutions. We attach great importance to ensuring that our applications for the Industrial Internet of Things (IIoT) meet the specific requirements of customers, that the respective product is accompanied throughout the entire life cycle, and that implementation in the existing or projected application environment can be completed quickly and easily. All this is the basis for economically successful digital solutions.
IIoT applications can require enormous investments. Can and should any company afford that?
M.P: IIoT applications can be expensive, but they don’t have to be! Cooperation with our customers is very important to us and we see the topic of digitalization as an opportunity to develop together and achieve joint market success. That is why Zimmer Group’s “Digital Services” are scalable. Companies entering the topic can benefit from our CAD downloads e.g. for collision considerations, space allocations etc. worldwide, at any time and free of charge. A next step would be, for example, the consideration of a product as a digital twin in a low expansion stage. Condition monitoring is also a fast, cost-effective entry into digitization, which in most cases creates a lot of benefit for little effort. Since our digital services build on each other and complement each other, customers can decide for themselves when, at what scale and at what cost they want to take the step that best suits their company structure and situation.
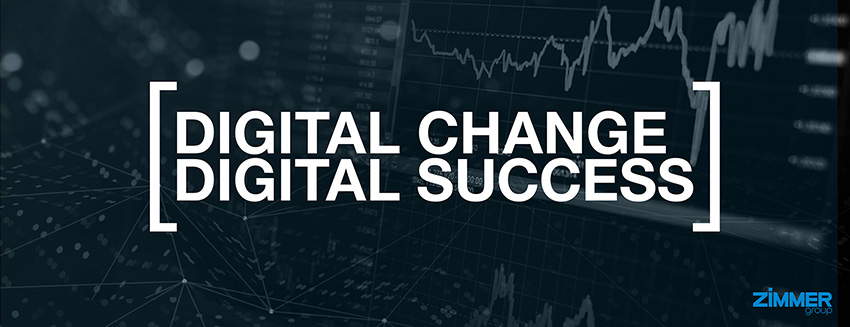
What trends will shape the digital transformation in mechanical and plant engineering in the near future?
M.P: For mechanical and plant engineering, the central keyword is Industry 4.0, i.e. the interlinking of industrial production with intelligent digital systems such as ERP, order and warehouse management, but also the networking of machines or different locations worldwide. In the near future, hardware and software will no longer be able to be considered separately from one another. The complexity of processes and their interdependency is increasing more and more in an increasingly dynamic and ever more volatile market environment. Digital services and their networking make these challenges more manageable and easier to plan for. Indicators point in the direction that after initial reticence, acceptance of cloud-based; AI and blockchain solutions is now increasing. Customers see the advantages of networking in daily operations but also in topics such as OEE maximization. Based on the current state of knowledge, it can be assumed that by the end of the decade, no major production plant worldwide will be able to do without cloud-linked services and AI functionalities in organization, process management and production.